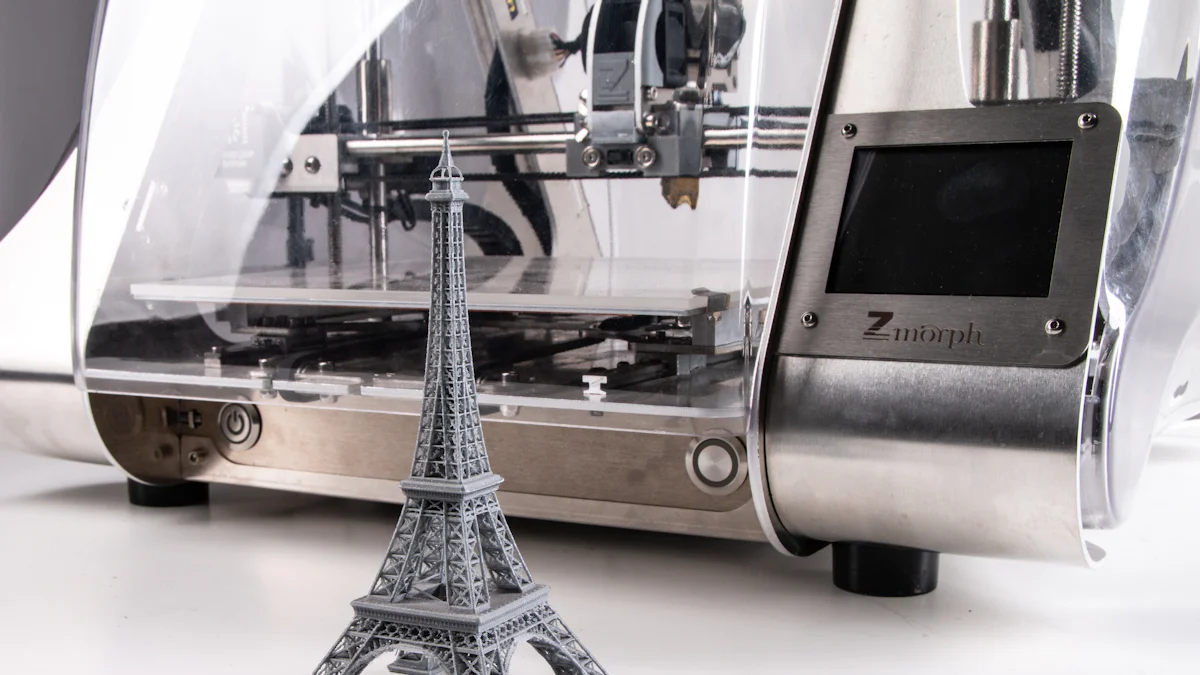
3D printing has revolutionized how you create objects, offering endless possibilities in design and manufacturing. Among the materials available, titanium stands out due to its exceptional properties. You might wonder why titanium is so special. Well, it boasts a high strength-to-weight ratio, corrosion resistance, and biocompatibility, making it ideal for various applications. Choosing the right material is crucial in 3D printing, as it directly impacts the quality and functionality of your printed parts. Metal forming & 3D Printing with Titanium opens up new avenues for innovation and efficiency across industries like aerospace, medical, and automotive.
Properties of Titanium
Strength and Durability
Titanium shines when it comes to strength and durability. You might wonder why this metal is so special. Well, it has a high strength-to-weight ratio. This means titanium is incredibly strong without being heavy. Imagine having the power of steel but with much less weight. This makes it perfect for industries like aerospace, where every ounce counts.
Titanium also offers resistance to wear and tear. It can handle tough conditions without breaking down. Whether you’re printing parts for a car or a plane, you want them to last. Titanium ensures that your creations stand the test of time.
Corrosion Resistance
Another standout feature of titanium is its corrosion resistance. You might think of rust when you hear corrosion, but titanium doesn’t have that problem. It thrives in harsh environments. Whether it’s salty sea air or acidic conditions, titanium holds up. This makes it ideal for marine and chemical applications.
The longevity of printed parts is another benefit. When you use titanium, you know your parts won’t degrade quickly. This means fewer replacements and repairs, saving you time and money in the long run.
Biocompatibility
Titanium’s biocompatibility is a game-changer in the medical field. It’s non-toxic and safe for the human body. This makes it perfect for applications in medical implants. From hip replacements to dental implants, titanium is the go-to material. It integrates well with bone, reducing the risk of rejection.
Moreover, titanium ensures safety for human use. You can trust it in your body without worrying about adverse reactions. This peace of mind is invaluable for both patients and healthcare providers.
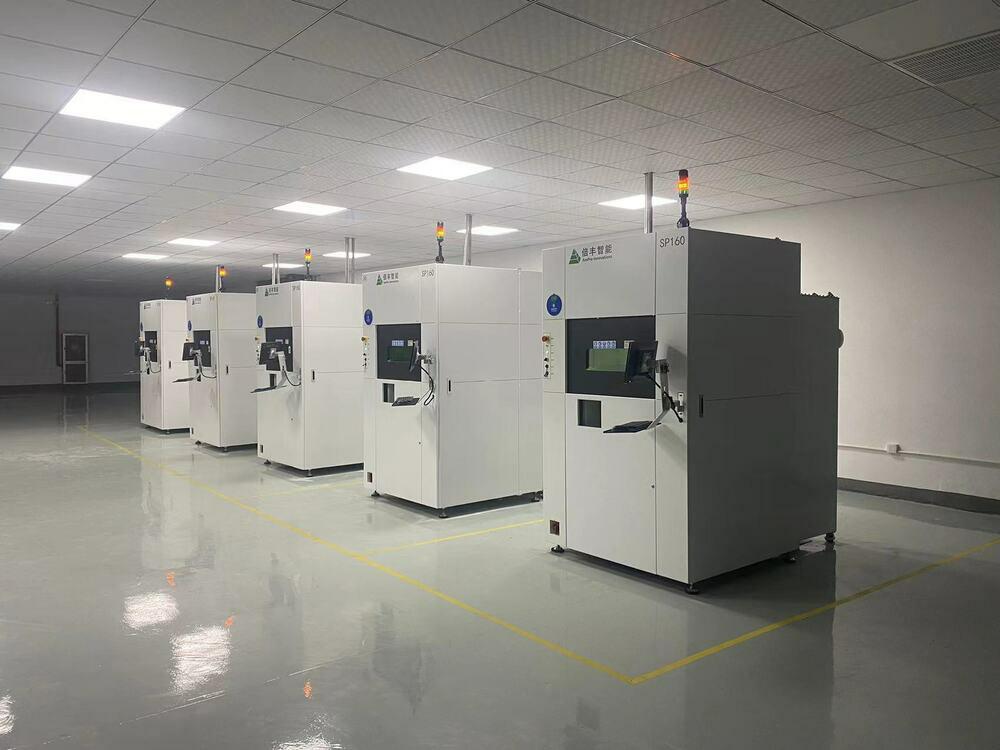
Metal forming & 3D Printing with Titanium
Metal forming & 3D Printing with Titanium
When you think about creating intricate designs, traditional manufacturing methods might limit your creativity. However, Metal forming & 3D Printing with titanium 3D printing opens up a world of possibilities. You can craft complex, bespoke parts that were once unimaginable. This technology leverages titanium’s desirable properties, such as biocompatibility and high strength, to produce components with unworkable geometries. Imagine the freedom to design without constraints—this is what titanium 3D printing offers.
Advantages over traditional manufacturing
- Material Efficiency: Traditional manufacturing often results in material waste. You cut away excess material, which isn’t very efficient. In contrast, titanium 3D printing uses only the exact amount needed. This reduces waste and enhances sustainability. You contribute to a greener planet while enjoying cost-effective production.
- Design Freedom: With titanium 3D printing, you can create lightweight structures with channels and lattice infills. These designs are not possible with traditional methods. You gain the ability to fabricate parts that improve performance and fuel efficiency, especially in the automotive industry. This design freedom allows you to innovate like never before.
- High-Performance Components: Titanium’s high strength-to-weight ratio and corrosion resistance make it ideal for high-stakes industries. Whether you’re in aerospace, medical, or automotive sectors, you need components that perform under pressure. Titanium 3D printing delivers lightweight, high-strength parts that meet these demands.
Complex geometries and design flexibility
Titanium 3D printing excels in producing complex geometries. You can design intricate parts with ease. This flexibility is transformative for industries like aerospace and healthcare. You can create components that traditional methods can’t achieve. For example, in the medical field, you can design custom implants tailored to individual patients. This level of personalization enhances patient outcomes and sets new standards in healthcare.

Applications of Titanium in 3D Printing
Aerospace Industry
In the aerospace industry, titanium’s unique properties make it a game-changer. You can create lightweight components that are crucial for aircraft. Every pound saved means better fuel efficiency and performance. Imagine the impact on long-haul flights where weight reduction translates to significant cost savings. Titanium’s high strength-to-weight ratio ensures that these components remain robust and reliable.
Moreover, titanium contributes to fuel efficiency improvements. By reducing the overall weight of the aircraft, you enhance its aerodynamics. This leads to less fuel consumption and lower emissions. It’s a win-win for both the environment and the airline industry. You get to enjoy more sustainable travel without compromising on safety or performance.
Medical Field
The medical field benefits immensely from titanium’s biocompatibility. You can design custom implants and prosthetics tailored to individual patients. This personalization improves patient outcomes and comfort. Titanium integrates seamlessly with human tissue, reducing the risk of rejection. Whether it’s a hip replacement or a dental implant, titanium ensures durability and safety.
Additionally, titanium is ideal for crafting surgical tools. Its corrosion resistance means these tools maintain their integrity even after repeated sterilization. You can rely on them for precision and reliability during critical procedures. The use of titanium in medical applications underscores its versatility and importance in advancing healthcare.
Automotive Sector
In the automotive sector, titanium plays a pivotal role in enhancing vehicle performance. You can produce performance parts that withstand high stress and temperatures. This is particularly beneficial for sports cars and high-performance vehicles. Titanium’s strength ensures these parts deliver optimal performance without adding unnecessary weight.
Furthermore, titanium aids in weight reduction strategies. By replacing heavier materials, you improve the vehicle’s fuel efficiency and handling. This not only benefits the driver but also contributes to a greener planet. The automotive industry continues to explore new ways to leverage titanium’s properties for innovation and sustainability.
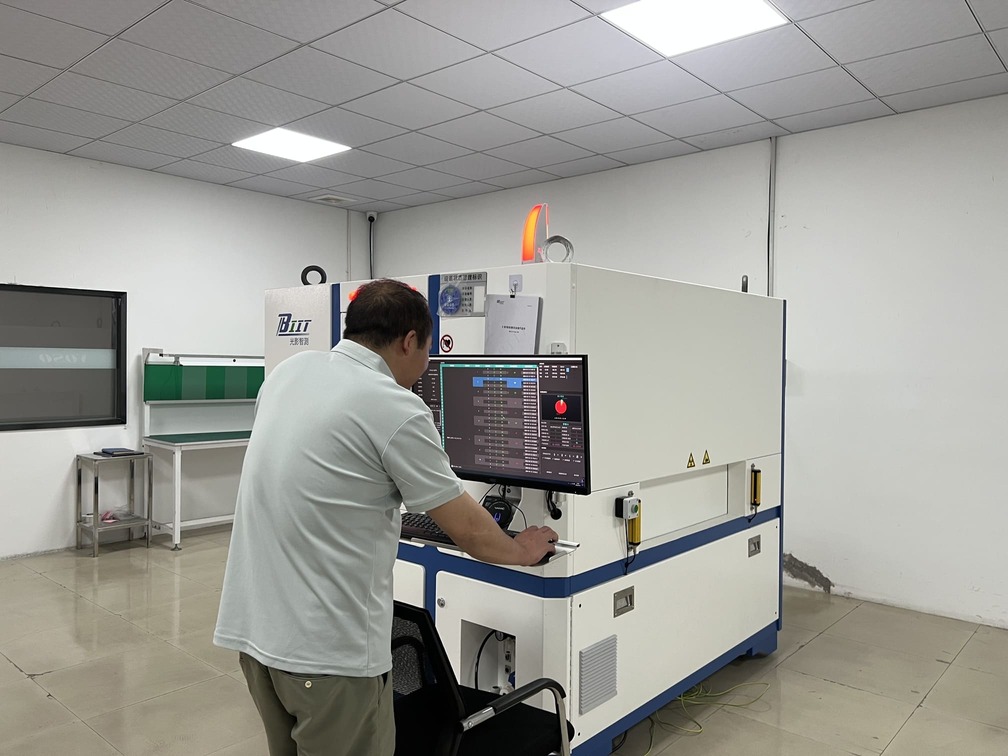
Challenges of Using Titanium in 3D Printing
Cost Considerations
High material costs
When you dive into 3D printing with titanium, one of the first hurdles you’ll encounter is the high cost of materials. Titanium powders, essential for the printing process, can range from 300to300 to 300to600 per kilogram. This price tag makes titanium a premium choice, often limiting its use to industries where its unique properties are indispensable, like aerospace and medical fields. For some applications, these costs might make titanium 3D printing nonviable. You need to weigh the benefits against the expenses to determine if it’s the right fit for your project.
Economic implications
You might find that the upfront costs pay off in the long run, especially if you’re producing high-value, complex parts.
Technical Challenges
Printing process complexities
Temperature control is crucial, as titanium requires precise conditions to prevent defects and ensure quality.
Equipment requirements
The equipment needed for titanium 3D printing is another significant consideration. Specialized printers capable of handling titanium powders are necessary, and they don’t come cheap. You also need to ensure that your setup includes proper ventilation and safety measures, as titanium powder can be hazardous if not handled correctly. Investing in the right equipment is crucial for success, but it can be a substantial financial commitment. You must assess whether your current resources align with the demands of titanium 3D printing before diving in.
Future Trends in Titanium 3D Printing
Technological Advancements
Innovations in printing techniques
You might wonder how titanium 3D printing will evolve. Well, the future looks promising with ongoing innovations in printing techniques. Researchers are constantly exploring new methods to enhance the precision and efficiency of titanium 3D printing. These advancements aim to reduce production time and improve the quality of printed parts. Imagine being able to print complex structures faster and with even greater accuracy. This is the direction in which the technology is heading.
Improved material formulations
The quest for better materials never stops. Scientists are working on developing improved titanium formulations that offer enhanced properties. These new materials could lead to stronger, lighter, and more durable printed parts. You can expect to see titanium alloys that push the boundaries of what’s possible in 3D printing. This means more opportunities for innovation across various industries, from aerospace to healthcare.
Market Growth
Increasing demand in various industries
The demand for titanium 3D printing is on the rise. Industries are recognizing the benefits of using titanium for their applications. In aerospace, the need for lightweight and strong components is driving the adoption of titanium 3D printing. The medical field also sees the value in creating custom implants and prosthetics. As more sectors discover the advantages of titanium, you can expect the market to grow significantly.
Expansion of applications
With technological advancements and improved materials, the applications of titanium 3D printing are expanding. You might see its use in areas previously thought impossible. From automotive parts to consumer electronics, the possibilities are endless. This expansion opens up new opportunities for businesses to innovate and stay ahead of the competition. By embracing titanium 3D printing, you can be part of this exciting future.
Case Studies and Real-World Examples
Successful Implementations
Notable projects in aerospace
In the aerospace industry, titanium 3D printing has made significant strides. You might be interested to know about the Airbus A350 XWB project. Airbus used titanium 3D printing to create over 1,000 parts for this aircraft. The result? A lighter, more fuel-efficient plane that meets stringent safety standards. This project showcases how titanium’s strength and lightweight properties can revolutionize aircraft design.
Another exciting development is the GE Aviation’s LEAP engine. GE Aviation utilized titanium 3D printing to produce fuel nozzles for this engine. These nozzles are 25% lighter and five times more durable than those made with traditional methods. This advancement not only improves engine performance but also reduces fuel consumption, benefiting both airlines and the environment.
Breakthroughs in medical applications
The medical field has also seen remarkable breakthroughs with titanium 3D printing. Consider the case of customized cranial implants. Surgeons can now design implants tailored to a patient’s unique anatomy. This personalization enhances the fit and integration of the implant, leading to better patient outcomes.
Another noteworthy example is the use of titanium 3D printing in dental implants. Dentists can create precise, patient-specific implants that improve comfort and functionality. The biocompatibility of titanium ensures that these implants integrate seamlessly with the jawbone, reducing the risk of complications.
Lessons Learned
Challenges faced and solutions
Despite its successes, titanium 3D printing has faced challenges. One major hurdle is the high cost of titanium powder. This expense can limit its use to high-value applications. However, advancements in recycling and powder reuse are helping to mitigate these costs. By reusing leftover powder, you can reduce waste and lower production expenses.
Another challenge is the complexity of the printing process. Maintaining precise temperature and environmental conditions is crucial for quality results. To address this, companies are investing in advanced monitoring systems and training programs. These initiatives ensure that operators have the skills and tools needed to manage the intricacies of titanium 3D printing.
Impact on industry practices
The lessons learned from titanium 3D printing have had a profound impact on industry practices. In aerospace, the ability to produce lightweight, durable components has led to more efficient aircraft designs. This shift not only improves performance but also reduces environmental impact through lower fuel consumption.
In the medical field, the success of titanium 3D printing has paved the way for more personalized healthcare solutions. Custom implants and prosthetics are becoming the norm, offering patients better outcomes and improved quality of life. As industries continue to embrace titanium 3D printing, you can expect to see even more innovative applications and practices emerge.
Titanium’s advantages in 3D printing are undeniable. Its high strength-to-weight ratio, corrosion resistance, and biocompatibility make it a top choice for industries like aerospace, medicine, and automotive. As technology advances, you can expect even more innovative applications. Imagine the possibilities with improved printing techniques and material formulations. Choosing the right material is crucial in 3D printing. Titanium not only enhances performance but also opens doors to new design possibilities. By embracing titanium, you position yourself at the forefront of innovation and efficiency.