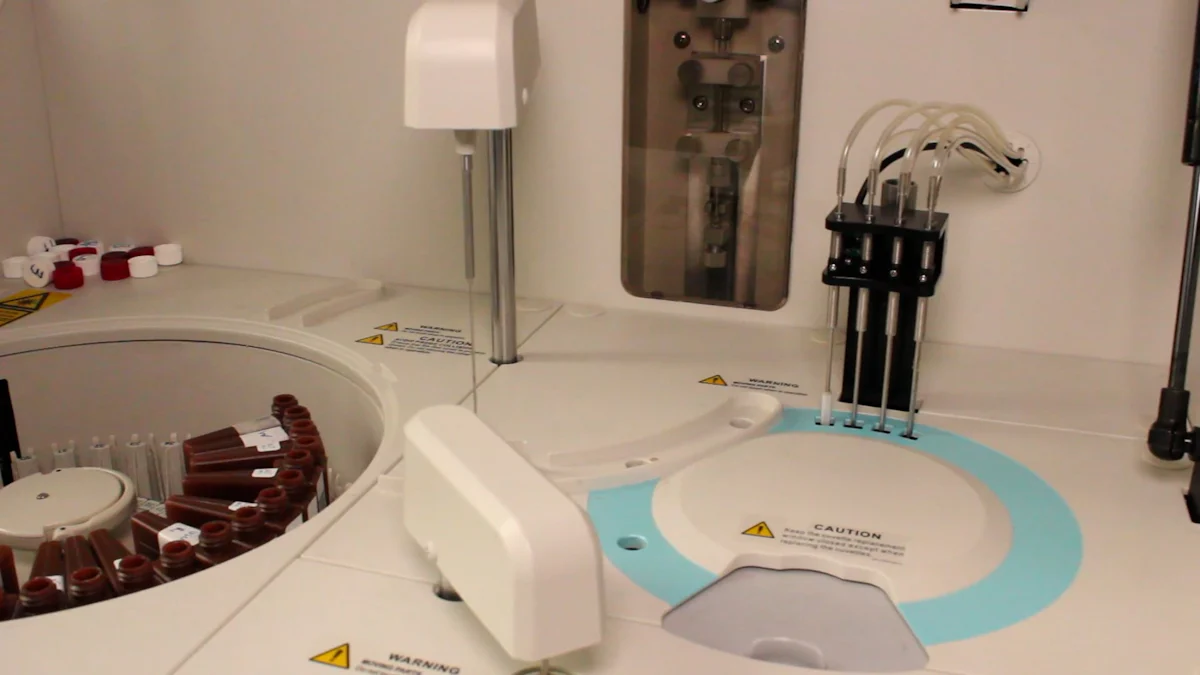
3D printed titanium implants are revolutionizing healthcare by offering transformative benefits. These implants provide exceptional biocompatibility, ensuring they integrate seamlessly with human tissue and reduce the risk of rejection. The customization capabilities of 3D printing allow for patient-specific designs, enhancing fit and comfort. Titanium’s inherent strength and durability make these implants a reliable choice for long-term use. Moreover, they significantly enhance osseointegration, improving surgical outcomes and patient recovery. The role of particulate analysis in 3D printed titanium implants ensures safety and performance, making them a groundbreaking advancement in medical technology.
Characteristics of Titanium Implants
Biocompatibility
Compatibility with human tissue
Titanium implants exhibit remarkable compatibility with human tissue. This compatibility stems from titanium’s ability to integrate seamlessly with bone, a process known as osseointegration. This integration ensures that the implant becomes a stable part of the body, reducing complications and promoting healing. Scientific Research Findings: Studies have shown that titanium alloys, such as commercially pure titanium (cpTi), are widely used in dental implants due to their excellent mechanical properties and biocompatibility.
Reduced risk of rejection
The risk of rejection significantly decreases with titanium implants. The body’s immune system often accepts titanium as a natural part of the body, minimizing adverse reactions. This acceptance leads to higher success rates in implant surgeries. Titanium’s inert nature plays a crucial role in its widespread use in medical applications, ensuring patient safety and comfort.
Customization
Tailored to individual patient needs
3D printing technology allows for the creation of implants tailored to individual patient needs. This customization ensures that each implant fits perfectly, addressing specific anatomical requirements. The ability to produce patient-specific designs enhances surgical precision and outcomes. Scientific Research Findings: 3D printing technology has been used to produce Ti6Al4V titanium alloy implants with adjustable porosity and roughness, which can enhance tissue integration.
Enhanced fit and comfort
Customized implants offer enhanced fit and comfort for patients. By matching the unique contours of a patient’s anatomy, these implants reduce discomfort and improve overall satisfaction. The precise fit also contributes to quicker recovery times and better long-term results, making them a preferred choice in modern healthcare.
Strength and Durability
Long-lasting performance
Titanium implants are renowned for their long-lasting performance. Their inherent strength ensures that they can withstand the stresses and strains of daily activities without compromising their structural integrity. This durability makes them suitable for various medical applications, including orthopedic and dental implants.
Resistance to wear and tear
The resistance of titanium to wear and tear further enhances its appeal as an implant material. Titanium’s robust nature ensures that it remains effective over time, reducing the need for frequent replacements. This resistance not only benefits patients by providing reliable solutions but also contributes to cost-effectiveness in healthcare.
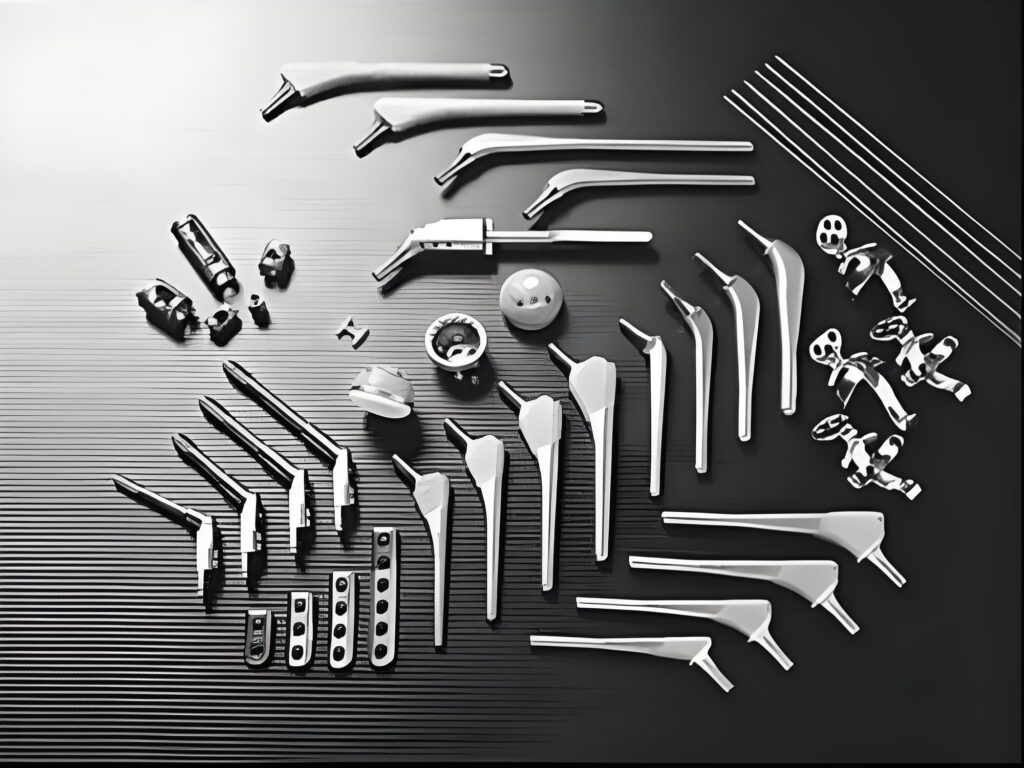
Current Applications in Healthcare
Orthopedic Implants
Joint replacements
3D printed titanium implants have revolutionized joint replacement surgeries. Surgeons now use these implants to replace damaged joints, such as hips and knees, with precision. The customization of these implants ensures a perfect fit for each patient, enhancing mobility and reducing recovery time. Case Studies: In foot and ankle surgeries, patient-specific 3D printed titanium implants have successfully treated complex bony defects and deformities, showcasing their efficacy in orthopedic applications.
Bone fracture repairs
Titanium implants play a crucial role in bone fracture repairs. They provide the necessary support to fractured bones, promoting healing and restoring function. The strength and durability of titanium make it an ideal choice for stabilizing fractures. Surgeons can rely on these implants to withstand the stresses of daily activities, ensuring long-term success in fracture management.
Dental Implants
Tooth replacements
Dental professionals increasingly use 3D printed titanium implants for tooth replacements. These implants offer a stable foundation for artificial teeth, mimicking the natural tooth root. The biocompatibility of titanium ensures seamless integration with the jawbone, reducing the risk of rejection. Patients benefit from improved oral function and aesthetics, making titanium implants a preferred choice in modern dentistry.
Jawbone reconstructions
In cases of severe jawbone loss, titanium implants provide a reliable solution for reconstruction. Surgeons utilize these implants to restore the structural integrity of the jaw, enabling patients to regain normal function. The customization capabilities of 3D printing allow for precise adaptation to the patient’s anatomy, enhancing surgical outcomes and patient satisfaction.
Cranial and Facial Implants
Skull reconstructions
3D printed titanium implants have transformed skull reconstruction procedures. Surgeons employ these implants to repair cranial defects resulting from trauma or surgery. The ability to create patient-specific designs ensures a perfect fit, promoting healing and reducing complications. The lightweight nature of titanium minimizes the load on the skeletal system, contributing to successful outcomes.
Facial prosthetics
Facial prosthetics benefit significantly from 3D printed titanium implants. These implants provide a stable framework for reconstructing facial features, improving both function and appearance. The customization of these implants allows for a natural look, enhancing the quality of life for patients. Surgeons can achieve remarkable results by leveraging the design freedom offered by 3D printing technology.
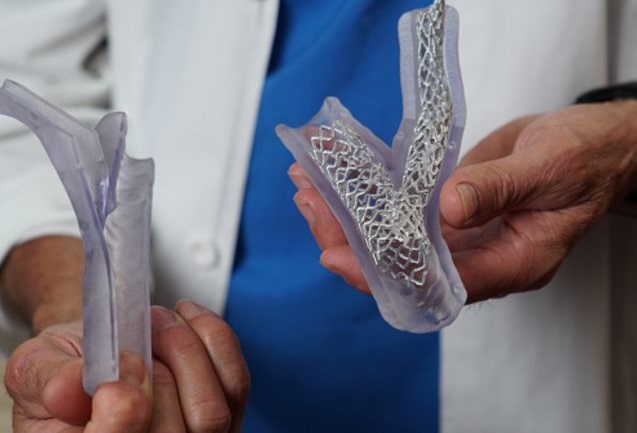
Challenges and Limitations
Cost Considerations
Initial investment in technology
3D printing technology requires a significant initial investment. Hospitals and clinics must purchase advanced 3D printers and related equipment. This investment can be a barrier for smaller healthcare facilities. They may struggle to justify the cost without immediate returns. However, larger institutions often find the investment worthwhile due to the long-term benefits.
Cost-effectiveness over time
Over time, 3D printed titanium implants can prove cost-effective. They reduce material waste and shorten production cycles. These factors lower overall manufacturing costs. Additionally, the durability of titanium implants minimizes the need for replacements. This longevity contributes to cost savings in the long run. Healthcare providers must weigh initial costs against these potential savings.
Technical Challenges
Precision in manufacturing
Manufacturing 3D printed titanium implants demands high precision. The process must ensure each implant meets exact specifications. Any deviation can affect the implant’s performance. Manufacturers face challenges in maintaining this precision consistently. Advanced technology and skilled technicians are essential to overcome these hurdles.
Quality control measures
Quality control is crucial in producing reliable implants. Each implant undergoes rigorous testing to ensure safety and effectiveness. Manufacturers implement strict quality control measures. These measures include detailed inspections and performance evaluations. Consistent quality control helps maintain high standards in implant production.
Regulatory Hurdles
Approval processes
3D printed medical devices, including titanium implants, must navigate complex approval processes. Regulatory bodies like the FDA provide guidelines for these devices. They ensure that 3D printed implants meet the same standards as traditional ones. Manufacturers must submit detailed documentation for approval. This process can be time-consuming and requires thorough preparation.
“Devices adhere to the same regulatory standards as conventional medical devices,” according to the FDA Guidance on 3D-printed medical devices.
Compliance with standards
Compliance with regulatory standards is mandatory for 3D printed implants. Manufacturers must adhere to guidelines for quality systems and manufacturing considerations. These standards ensure the safety and efficacy of medical devices. Non-compliance can result in delays or rejection of approval. Manufacturers must stay informed about evolving regulations to maintain compliance.
Future Trends
Advances in 3D Printing Technology
Improved printing techniques
3D printing technology continues to evolve, offering improved techniques that enhance precision and efficiency. Researchers focus on refining the printing process to produce implants with intricate designs and superior quality. These advancements allow for the creation of complex structures that were previously unattainable. The Journal of Personalized Medicine highlights the rapid progress in 3D printing, particularly in orthopedic surgery, where customization and osseointegration are significantly enhanced.
New materials development
The development of new materials plays a crucial role in advancing 3D printing technology. Scientists explore innovative materials that offer better biocompatibility and strength. These materials aim to improve the performance and longevity of implants. The potential for using novel materials in medical applications opens up exciting possibilities for future healthcare solutions. As technology progresses, the range of materials suitable for 3D printing will likely expand, providing more options for medical professionals.
Expanded Applications
Broader range of medical uses
The scope of 3D printed titanium implants extends beyond current applications. Researchers explore new medical uses, such as creating implants for cardiovascular and neurological conditions. The versatility of 3D printing allows for the adaptation of implants to various medical needs. The Journal of Medical Innovation suggests that 3D printing holds great promise for future medical applications, including the potential for printing organs for transplant.
Integration with other technologies
Integration with other technologies enhances the capabilities of 3D printed implants. Combining 3D printing with imaging technologies, such as MRI and CT scans, enables precise mapping of patient anatomy. This integration facilitates the creation of highly accurate implants tailored to individual patients. The synergy between 3D printing and other technologies paves the way for innovative solutions in personalized medicine.
Impact on Personalized Medicine
Customized treatment plans
3D printing technology revolutionizes personalized medicine by enabling customized treatment plans. Medical professionals can design implants that cater to the specific needs of each patient. This customization ensures that treatments align with individual anatomical and physiological requirements. The ability to tailor implants to patients enhances the effectiveness of medical interventions and improves overall patient care.
Enhanced patient outcomes
The impact of 3D printed titanium implants on patient outcomes is profound. Customized implants lead to better surgical results and faster recovery times. Patients experience improved comfort and satisfaction due to the precise fit of these implants. As 3D printing technology advances, the potential for enhancing patient outcomes continues to grow. The focus on personalized medicine promises a future where treatments are more effective and patient-centered.
Particulate Analysis in 3D Printed Titanium Implants
Importance of Particulate Analysis
Ensuring implant safety
Particulate analysis plays a crucial role in ensuring the safety of 3D printed titanium implants. This process involves examining the surface characteristics of implants, such as porosity and roughness, which directly impact their integration with human tissue. Researchers have found that implants with appropriate porosity enhance osseointegration, the process where bone integrates with the implant. This integration is vital for the stability and longevity of the implant.
Biocompatibility testing forms an essential part of particulate analysis. It ensures that the implants do not provoke adverse reactions in the body. Testing must be thorough, especially for devices representing the worst-case scenario, to guarantee patient safety. By conducting meticulous particulate analysis, manufacturers can identify and mitigate potential risks, ensuring that the implants meet stringent safety standards.
Enhancing implant performance
Particulate analysis not only ensures safety but also enhances the performance of 3D printed titanium implants. By analyzing the surface properties, researchers can optimize the design and manufacturing processes to improve implant functionality. For instance, implants with tailored roughness can promote better tissue integration, leading to improved surgical outcomes.
Advanced manufacturing techniques, such as Direct Metal Laser Sintering (DMLS) and Selective Laser Melting (SLM), allow for precise control over the implant’s surface characteristics. These techniques enable the creation of implants with complex structures that were previously unattainable. The ability to customize implants to meet specific patient needs further enhances their performance, providing reliable solutions for various medical applications.
In conclusion, particulate analysis in 3D printed titanium implants is indispensable for ensuring safety and enhancing performance. By focusing on surface characteristics and biocompatibility, researchers and manufacturers can produce implants that integrate seamlessly with human tissue, offering patients improved outcomes and a higher quality of life.
3D printed titanium implants are transforming healthcare with their remarkable potential. They offer patient-specific solutions that enhance comfort and surgical outcomes. Ongoing innovations in 3D printing technology promise even greater possibilities for personalized medicine. The implants’ biocompatibility, customization, and strength make them a preferred choice in medical applications. Particulate analysis plays a crucial role in ensuring the safety and performance of these implants, further solidifying their place in modern healthcare. As technology advances, 3D printed titanium implants will continue to revolutionize patient care and treatment options.