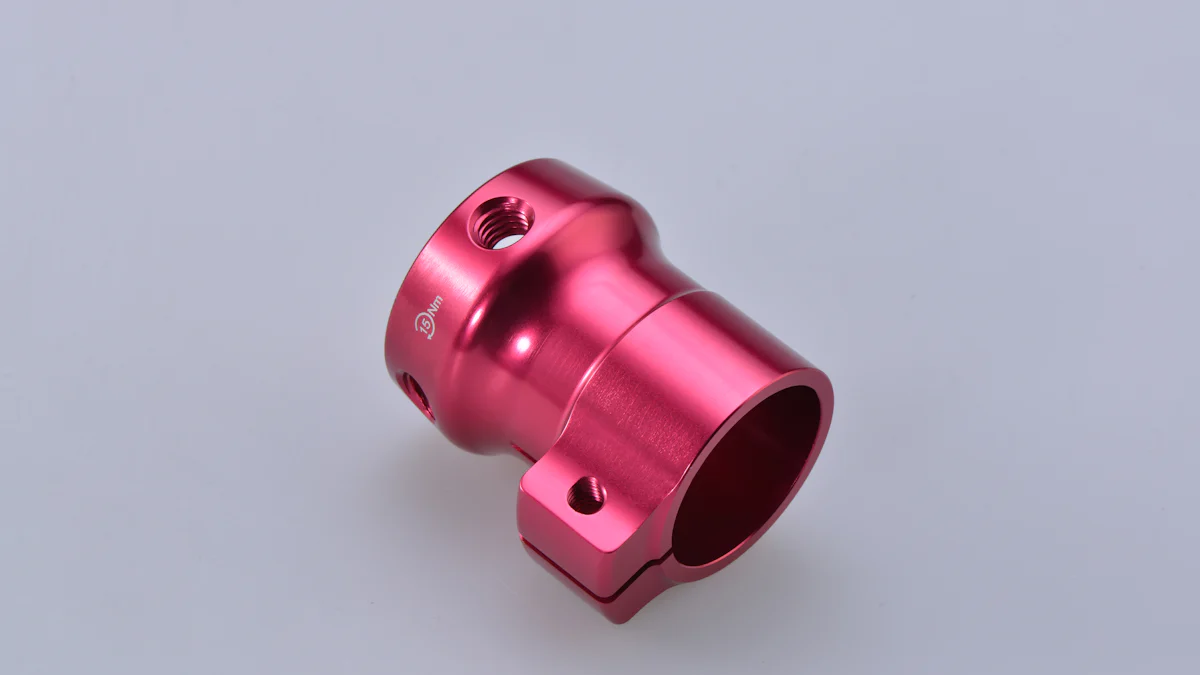
You might wonder how strong 3D printed titanium really is. This remarkable material often surpasses traditional titanium in specific applications. It achieves tensile strengths of over 1600 megapascals, making it one of the strongest 3D-printed metals available. The unique microstructure of 3D printed titanium contributes to its high strength-to-weight ratio, which is ideal for lightweight applications. For instance, 3D-printed Ti6Al4V shows higher strength and yield points compared to its metallurgically produced counterpart. This makes it a preferred choice in industries where reducing weight without compromising strength is crucial.
Understanding 3D Printing of Titanium
The 3D Printing Process
3D printing, also known as additive manufacturing, revolutionizes how you can create titanium parts. This process builds objects layer by layer, offering precision and flexibility that traditional methods cannot match.
Overview of Additive Manufacturing Techniques
Additive manufacturing encompasses several techniques. Each technique has its own strengths and applications. For titanium, the most common methods include Selective Laser Melting (SLM) and Electron Beam Melting (EBM). These techniques use high-energy sources to fuse titanium powder into solid structures. The ability to create complex geometries with minimal waste makes these methods highly efficient.
Materials Used in 3D Printing Titanium
In 3D printing, titanium powders play a crucial role. Manufacturers engineer these powders to ensure optimal performance. Various titanium alloys, such as Ti-6Al-4V, are popular due to their excellent mechanical properties. These alloys provide a high strength-to-weight ratio, making them ideal for demanding applications. Ongoing research focuses on improving the surface quality and reducing porosity of these materials, enhancing their overall performance.
Common 3D Printing Techniques for Titanium
Understanding the techniques used in 3D printing titanium helps you appreciate the material’s versatility and strength.
Selective Laser Melting (SLM)
SLM uses a high-powered laser to selectively melt titanium powder. This technique allows you to create intricate designs with high precision. The laser fuses the powder layer by layer, resulting in a dense and robust structure. SLM is particularly useful in industries like aerospace and medical, where precision and strength are paramount.
Electron Beam Melting (EBM)
EBM employs an electron beam to melt titanium powder. This method operates in a vacuum, reducing the risk of contamination. EBM is well-suited for producing large, complex parts with excellent mechanical properties. The process offers advantages such as reduced residual stress and improved material integrity. Industries benefit from EBM’s ability to produce bespoke parts efficiently.
By understanding these processes and techniques, you gain insight into why 3D printed titanium is a game-changer in modern manufacturing. Its ability to produce strong, lightweight, and complex parts opens new possibilities across various fields.
Factors Affecting the Strength of 3d printed titanium
Material Selection
Choosing the right material is crucial for achieving the desired strength in 3D printed titanium. Different titanium alloys offer unique properties that cater to various applications. For instance, Ti6Al4V (Grade 5) is a popular choice due to its high strength, lightweight characteristics, and corrosion resistance. This alloy is widely used in industries like aerospace and medical, where durability and biocompatibility are essential. Other alloys, such as Titanium Beta 21S and Cp-Ti (pure titanium), provide specific advantages like resistance to oxidation and high temperatures. Understanding these properties helps you select the most suitable alloy for your project.
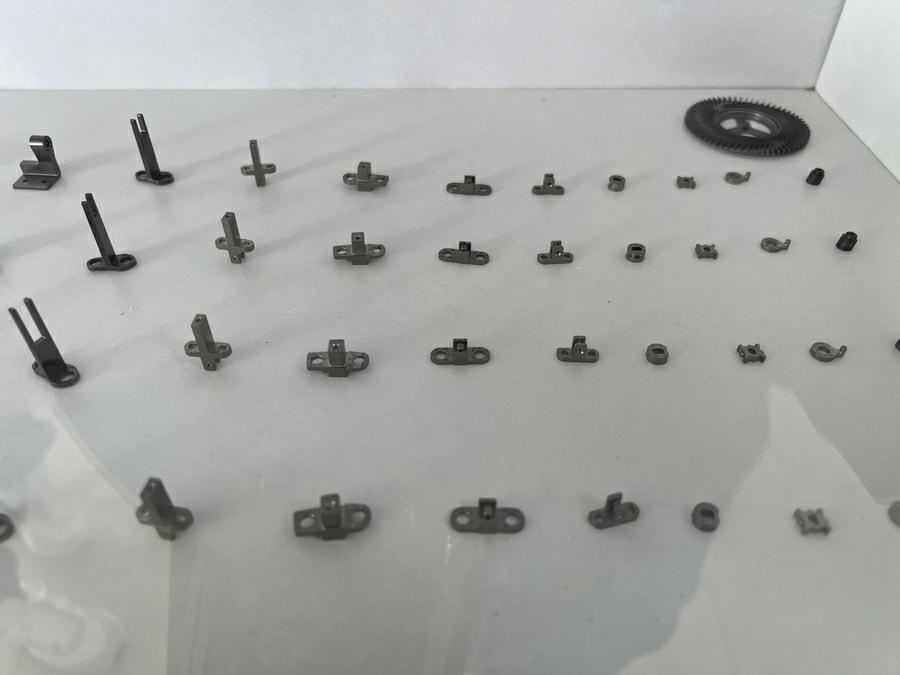
Printing Parameters
The parameters set during the 3D printing process significantly impact the final product’s strength. Two critical factors are layer thickness and build orientation.
Layer Thickness and Build Orientation
Layer thickness determines the resolution and surface finish of the printed part. Thinner layers result in smoother surfaces and finer details, enhancing the mechanical properties. However, they also increase printing time. Build orientation affects how the layers are stacked, influencing the part’s strength and load-bearing capacity. For example, printing with layers aligned along the direction of applied stress can improve tensile strength. By optimizing these parameters, you can achieve a balance between strength, precision, and efficiency.
Post-Processing Techniques
Post-processing plays a vital role in enhancing the strength and quality of 3D printed titanium parts. Techniques like heat treatment and surface finishing are commonly employed to improve mechanical properties and aesthetics.
Heat Treatment and Surface Finishing
Heat treatment involves heating the printed part to a specific temperature and then cooling it under controlled conditions. This process alters the microstructure of the material, increasing its strength and toughness. Surface finishing techniques, such as polishing and coating, enhance the part’s appearance and protect it from wear and corrosion. These post-processing steps ensure that the final product meets the required standards for performance and durability.
By understanding and optimizing these factors, you can harness the full potential of 3D printed titanium. This knowledge empowers you to create parts that are not only strong and durable but also tailored to meet specific application needs.
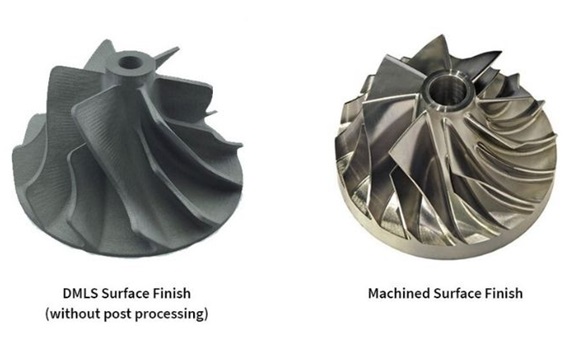
Comparing 3d printed titanium with Traditional Titanium
Mechanical Properties
When you compare the mechanical properties of 3D printed titanium to traditional titanium, you’ll notice some intriguing differences. Tensile strength is a key factor. 3D-printed titanium, especially the Ti6Al4V alloy, often exhibits higher tensile strength and yield points than its conventionally produced counterparts. This makes it a strong contender in applications where high strength is crucial. However, traditional titanium manufacturing techniques tend to outperform in terms of compressive strength, with values reaching up to 1070 MPa, compared to 659 MPa for 3D printed titanium.
Tensile Strength and Hardness
The tensile strength of 3D printed titanium can exceed 1600 megapascals, making it one of the strongest 3D-printed metals available. This strength is due to the unique microstructure formed during the additive manufacturing process. However, the surface roughness and porosity inherent in 3D printing can affect the hardness and overall mechanical performance. Traditional titanium, on the other hand, often has a smoother finish and fewer imperfections, which can enhance its hardness and durability.
Durability and Longevity
Durability and longevity are critical when choosing materials for demanding applications. 3D printed titanium offers several advantages in this regard. Its ability to produce complex geometries with minimal waste makes it ideal for industries like aerospace, medical, and automotive. Despite this, the surface roughness and porosity of 3D printed parts can sometimes lead to reduced durability compared to traditionally manufactured titanium.
Resistance to Wear and Corrosion
3D printed titanium parts generally exhibit excellent resistance to wear and corrosion, similar to traditional titanium. This resistance is crucial in environments where exposure to harsh conditions is common. However, the porosity in 3D printed parts can sometimes compromise their resistance to wear and corrosion. Traditional titanium, with its denser structure, often provides superior protection against these factors. Despite these challenges, the low thermal conductivity of titanium makes it difficult to machine traditionally, positioning 3D printing as an ideal solution for creating intricate designs without compromising material integrity.
Testing Methods for 3D Printed Titanium
Standard Testing Procedures
To ensure the reliability of 3D printed titanium, you must conduct rigorous testing. Tensile testing is a fundamental procedure. It measures how much force a material can withstand before breaking. You apply a pulling force to the titanium sample until it fractures. This test helps determine the tensile strength and elasticity of the material.
Fatigue testing is another crucial method. It assesses how the material behaves under repeated stress cycles. You subject the titanium to fluctuating loads to simulate real-world conditions. This test reveals the endurance limit of the material, indicating how long it can last before failure occurs. Both tests provide valuable insights into the mechanical properties of 3D printed titanium.
Results and Findings
The results from these tests often lead to fascinating discoveries. Case studies highlight the effectiveness of 3D-printed titanium in various applications. For instance, a study on titanium implants showed promising outcomes. The implants supported bone growth in facial reconstruction cases where traditional methods failed, demonstrating the potential of 3D-printed titanium in medical applications.
Industry reports also illuminate the performance of 3D-printed titanium. They often reveal that this material surpasses traditional titanium in specific scenarios. Reports indicate that 3D-printed titanium parts exhibit excellent strength-to-weight ratios. This makes them ideal for the aerospace and automotive industries, where reducing weight without compromising strength is essential.
By understanding these testing methods and their findings, you gain a deeper appreciation for the capabilities of 3D printed titanium. This knowledge empowers you to make informed decisions when selecting materials for your projects.
Applications of 3D Printed Titanium
Aerospace Industry
In the aerospace industry, 3D printed titanium plays a crucial role. You can create lightweight components and structural parts that significantly reduce aircraft weight. This reduction leads to improved fuel efficiency and lower operational costs. The ability to produce complex geometries with minimal waste makes 3D printing an ideal choice for aerospace applications. Titanium powder used in 3D printing provides the high strength-to-weight ratio necessary for these demanding environments. As a result, you can achieve designs that were previously impossible with traditional manufacturing methods.
Medical Field
The medical field benefits immensely from 3D printed titanium. You can produce custom implants and prosthetics tailored to individual patient needs. This customization enhances patient outcomes and reduces recovery times. 3D printed titanium implants offer excellent biocompatibility, ensuring they integrate well with the human body. The precision of 3D printing allows for the creation of intricate structures that match the patient’s anatomy perfectly. This technology revolutionizes how you approach medical treatments, providing solutions that improve quality of life.
Automotive and Other Industries
In the automotive industry, 3D printed titanium enables the production of high-performance parts and prototyping. You can design lightweight yet durable components that enhance vehicle performance. The ability to quickly prototype and test new designs accelerates innovation and reduces time to market. Beyond automotive, other industries also benefit from 3D printed titanium. For example, you can construct custom replacement parts for older equipment, extending their operational life. These parts often outperform original steel components, reducing maintenance costs and improving efficiency.
3D printed titanium continues to transform various industries by offering unprecedented design freedom and cost-effective production. As technology advances, you can expect even more innovative applications and improvements in quality control. This evolution opens up new possibilities for customization and efficiency across multiple sectors.
Future Implications and Developments
Advancements in 3D Printing Technology
The future of 3D printing technology looks promising, especially in the realm of titanium. You will witness significant advancements that enhance the strength and versatility of 3D printed parts. Innovations in Material Science play a crucial role in this evolution. Researchers are exploring new titanium alloys that offer superior mechanical properties. These alloys can be tailored to meet specific needs, providing increased strength, flexibility, and resistance to corrosion.
“Understanding the strength of 3D printed parts is critical to harnessing the full potential of this technology.”
This quote highlights the importance of ongoing research and development in the field. By adjusting the microstructure of metal alloys, you can achieve unprecedented levels of performance. This capability opens up new possibilities for creating parts that are not only strong but also lightweight and durable.
Potential Impact on Manufacturing Industries
The impact of 3D printing on manufacturing industries is transformative. You will find that this technology offers several advantages over traditional methods. Cost-Effectiveness and Customization are two key benefits that stand out. 3D printing allows you to produce parts with minimal waste, reducing material costs. The ability to create complex geometries without the need for expensive tooling further enhances cost savings.
Customization is another significant advantage. You can design and produce parts tailored to specific requirements, offering a level of personalization that traditional manufacturing cannot match. This flexibility is particularly valuable in industries like aerospace and medical, where bespoke solutions are often necessary.
“3D printing promises to be a key player in the manufacturing landscape, characterized by its innovative potential, commitment to sustainability, and transformative impact across industries.”
This statement underscores the potential of 3D printing to revolutionize how you approach manufacturing. As technology continues to advance, you can expect even greater improvements in efficiency and quality control. The future of 3D printed titanium is bright, with endless possibilities for innovation and growth.
3D printed titanium offers remarkable strength and versatility, making it a valuable material in various industries. You can see its potential to revolutionize manufacturing processes as significant, with ongoing advancements in technology and material science. As the cost of titanium lowers and more applications are discovered, titanium 3D printing will become a great manufacturing alternative for a much wider range of industries. This technology holds the potential to transform the manufacturing landscape, offering design freedom, lightweight structures, and cost-effective production. You are encouraged to explore further research into the capabilities of titanium 3D printing.