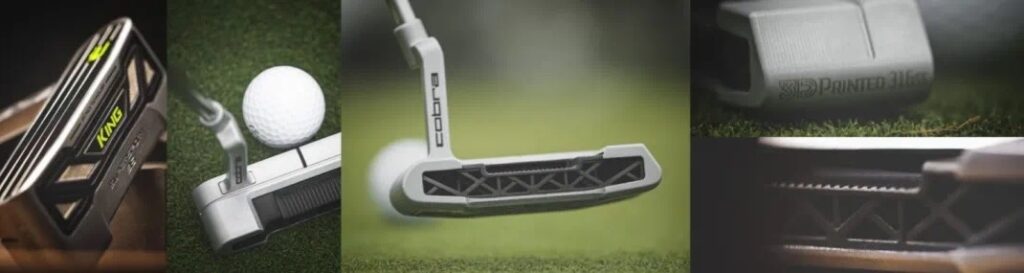
Introduction
In recent years, technology has played a pivotal role in transforming various sports, and golf is no exception. The integration of titanium 3D printing into golf equipment manufacturing is not just an evolution but a revolution. This article delves into how titanium 3D printing is reshaping the golf industry, particularly in the production of golf clubs, highlighting its numerous advantages, groundbreaking case studies, and the promising future of this technology.
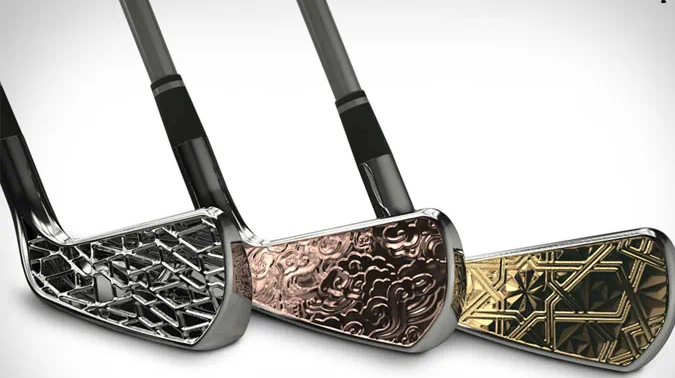
The Advantages of Titanium in Golf Clubs
Lightweight and High Strength
Enhanced Swing Speed and Control
Titanium’s lightweight nature significantly enhances a golfer’s swing speed. Traditional materials often add unnecessary weight, hindering the player’s ability to generate maximum clubhead speed. Titanium, being lighter, allows for faster swings without compromising control. This increased speed translates into greater distance and precision, providing golfers with a competitive edge.
Durability and Longevity
One of titanium’s most celebrated properties is its high strength-to-weight ratio. This means that while the material is light, it is also incredibly durable. Golf clubs made from titanium can withstand the rigors of frequent use, maintaining their structural integrity and performance over time. This durability reduces the need for frequent replacements, making titanium clubs a cost-effective choice in the long run.
Customization and Precision Engineering
Tailored Designs for Optimal Performance
Titanium 3D printing enables the creation of highly customized golf clubs tailored to individual players’ needs. Unlike traditional manufacturing methods, 3D printing can produce unique designs that optimize performance. Whether adjusting the club’s weight distribution or fine-tuning its aerodynamics, this level of customization ensures that each club is perfectly suited to its user.
Complex Geometries and Fine-Tuning
The precision of 3D printing allows for the creation of complex internal geometries that were previously impossible with conventional methods. These intricate designs can be fine-tuned to enhance the club’s performance, improving factors like swing stability and impact force distribution. This technological capability means that every aspect of the club can be optimized for peak performance.
Case Studies of Titanium 3D Printed Golf Clubs
COBRA Golf and HP Collaboration
The KING Supersport-35
In November 2020, COBRA Golf, in collaboration with HP and Parmatech, launched the KING Supersport-35, the first commercially available golf club produced using 3D printing technology. This club features a lattice structure that optimizes weight distribution and increases the moment of inertia (MOI), enhancing stability and forgiveness. The precise engineering behind the KING Supersport-35 demonstrates the potential of 3D printing to revolutionize golf equipment design.
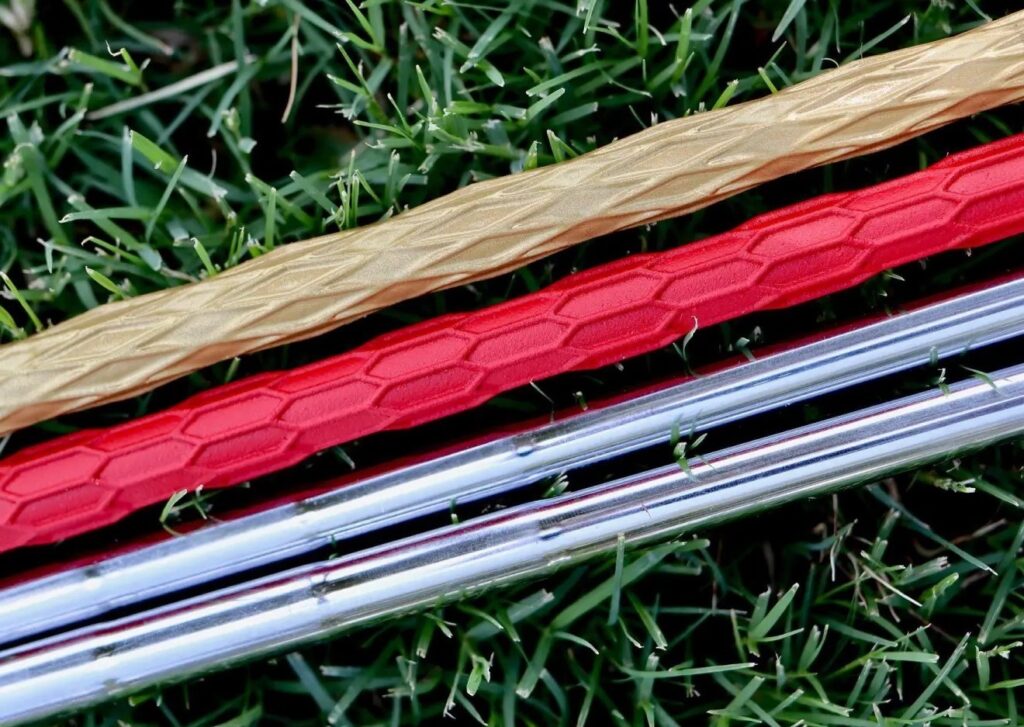
Market Impact and Player Feedback
The KING Supersport-35 received widespread acclaim from both the market and players. Golfers reported improved accuracy and consistency in their putting, attributing these enhancements to the club’s innovative design. The successful launch of this product has positioned COBRA Golf at the forefront of technological innovation in the industry.
Snarr3D’s Innovative Approach
3D Printed Golf Club Shafts
In March 2023, Snarr3D announced the introduction of 3D printed golf club shafts. This innovation allows for precise weight redistribution during the printing process, enhancing the feel and performance of the putter. Traditional methods required post-production weight adjustments, but Snarr3D’s approach integrates this step into the printing process, streamlining production and improving the final product.
Aesthetic and Functional Customizations
Snarr3D’s 3D printing capabilities also allow for extensive aesthetic and functional customizations. From unique textures to personalized designs, golfers can now own clubs that not only perform exceptionally but also reflect their personal style. This blend of form and function sets Snarr3D’s products apart in the competitive golf equipment market.
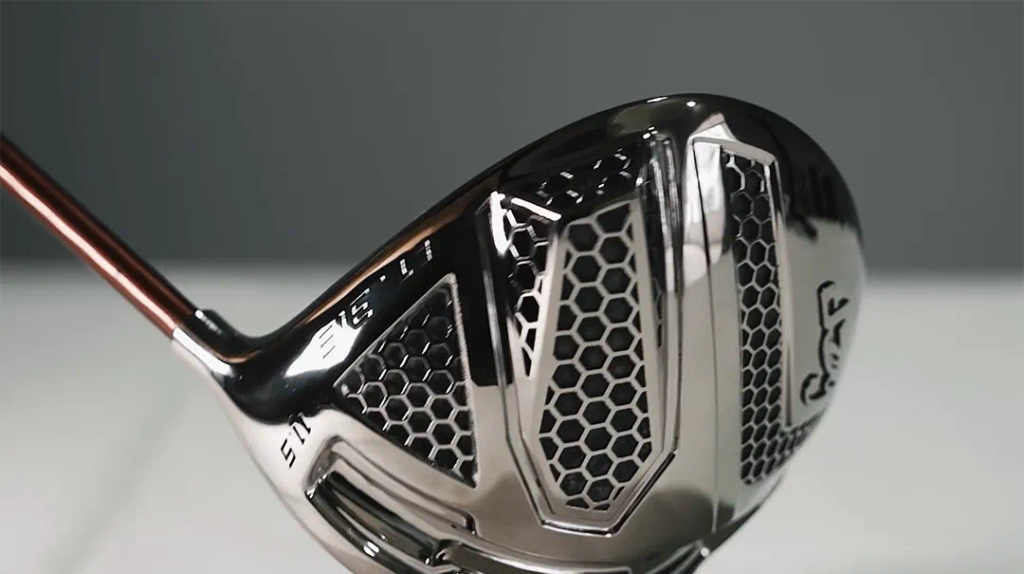
Other Notable Applications and Innovations
Fukai Technology and Farsoon High-Tech
In March 2023, Fukai Technology, a pioneer in the application of 3D printing in the golf industry, partnered with Farsoon High-Tech to produce titanium golf club heads. Utilizing Farsoon’s advanced metal 3D printing machines, Fukai Technology can produce over 15,000 golf club heads annually. These heads feature complex structures that enhance both the aesthetic appeal and functional performance of the clubs.
Designer and Avoda Golf
In January 2024, the Japanese company Designer released a new line of titanium golf club heads produced using Farsoon’s metal 3D printing technology. After over 1,600 days of research and more than 1,000 tests, Designer’s clubs achieved unprecedented levels of precision and forgiveness. Meanwhile, Avoda Golf’s custom clubs for professional golfer Bryson DeChambeau incorporate advanced features like surface curvature and weight distribution based on scientific principles, resulting in improved performance on the course.
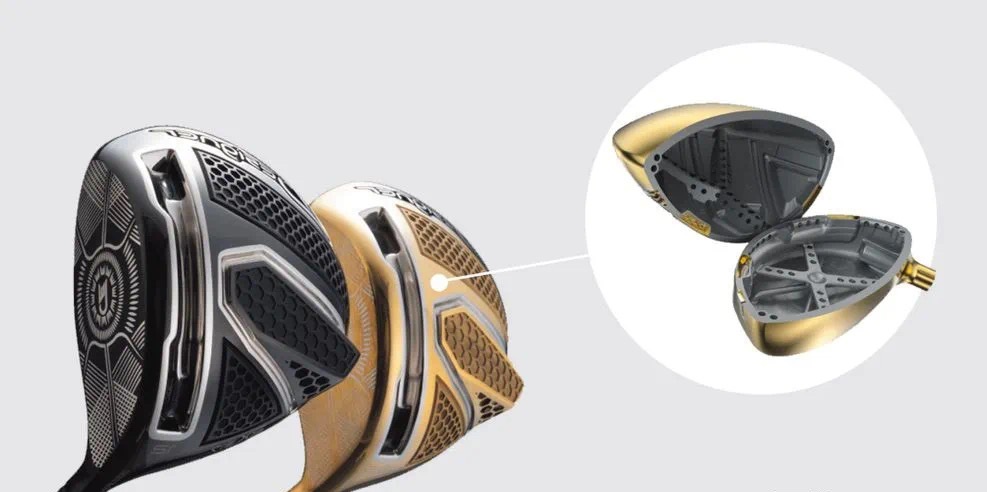
The Future of Titanium 3D Printing in Golf
Technological Advancements and Material Innovations
Emerging Printing Techniques
As 3D printing technology continues to evolve, new techniques are emerging that promise to further enhance the capabilities of titanium golf club manufacturing. Techniques such as direct metal laser sintering (DMLS) and electron beam melting (EBM) allow for even greater precision and efficiency. These advancements will likely lead to more innovative and high-performance golf equipment.
New Titanium Alloys and Composites
Researchers are continually developing new titanium alloys and composites that offer enhanced properties, such as increased strength, flexibility, and corrosion resistance. These materials will open up new possibilities for golf club design, enabling manufacturers to push the boundaries of what is possible in terms of performance and durability.
Market Trends and Consumer Adoption
Growing Demand for Customization
The demand for customized golf equipment is on the rise, driven by players’ desire for clubs that perfectly match their playing style and preferences. Titanium 3D printing meets this demand by offering unparalleled customization options, from personalized weight distribution to unique aesthetic designs. As more golfers experience the benefits of customized clubs, the market for 3D printed equipment is expected to grow significantly.
Competitive Landscape and Brand Strategies
Major brands in the golf industry are increasingly adopting titanium 3D printing to stay competitive. Companies like COBRA Golf, Snarr3D, and Designer are leading the way, using innovative strategies to differentiate their products. These strategies include leveraging the latest technological advancements, offering extensive customization options, and emphasizing the performance benefits of 3D printed clubs.
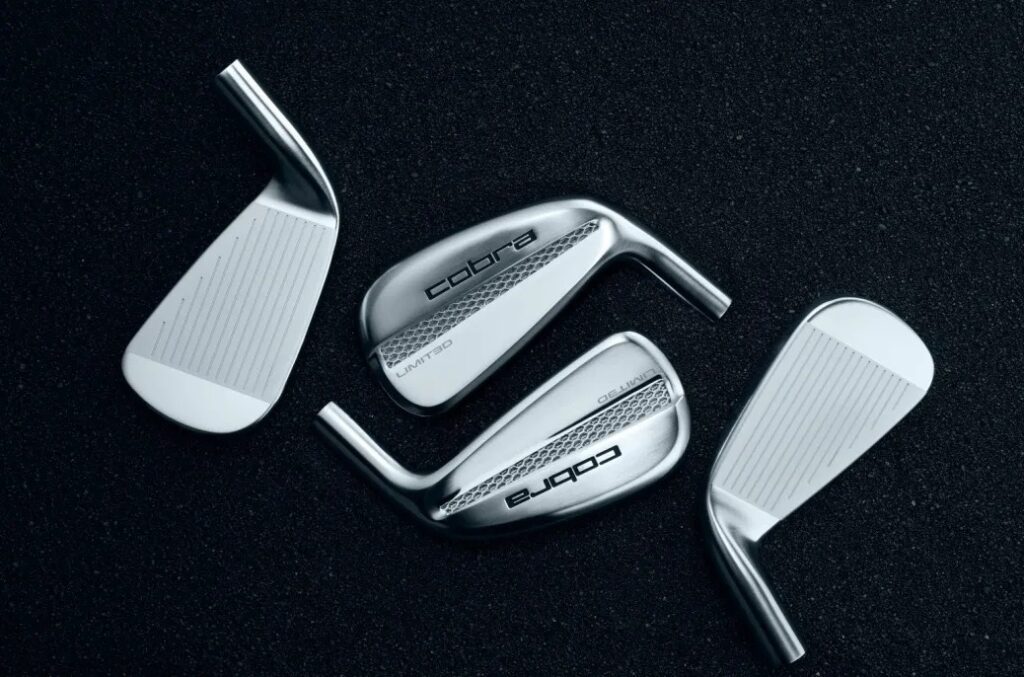
Conclusion
The integration of titanium 3D printing into golf club manufacturing is transforming the industry, offering significant advantages in terms of performance, customization, and cost-effectiveness. Through various case studies, we see how this technology is being adopted by leading brands to create innovative products that enhance the game for golfers of all levels. As technology continues to advance, titanium 3D printing will undoubtedly play an increasingly important role in the future of golf equipment, driving further innovations and setting new standards for quality and performance.
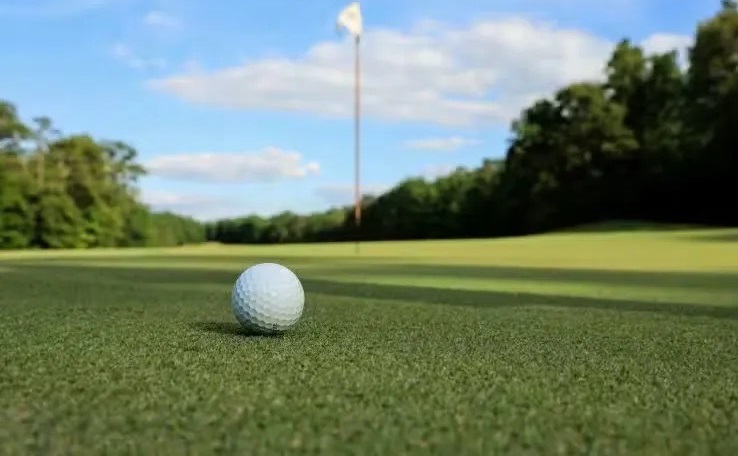