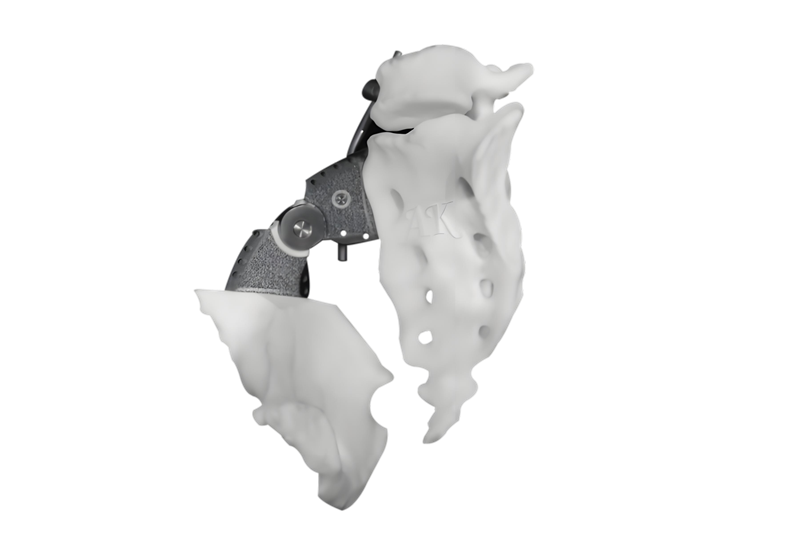
3D printed titanium bones represent a groundbreaking advancement in medical technology. They offer several advantages, such as enhanced biocompatibility and the ability to create patient-specific implants. Studies have shown that these implants can effectively integrate with human bone, reducing the need for additional materials like cement. However, challenges remain. The cost of production and limited availability pose significant hurdles. Additionally, long-term data on their effectiveness is still emerging. As this technology evolves, understanding its pros and cons becomes crucial for both medical professionals and patients.
Pros of 3D Printed Titanium Bones
Biocompatibility
3D printed titanium bones exhibit remarkable biocompatibility. This quality ensures that the human body readily accepts these implants, minimizing the risk of rejection. Scientific Research Findings: Studies highlight titanium’s non-toxic nature and resistance to corrosion, making it an ideal choice for medical implants. The Journal of Orthopaedic Surgery and Research emphasizes that titanium’s compatibility with bone tissue promotes rapid bone formation and reduces bone absorption. This compatibility is crucial for successful integration into the body, enhancing the overall effectiveness of the implant.
Strength and Durability
The strength and durability of 3D printed titanium bones stand out as significant advantages. Titanium’s high strength-to-weight ratio ensures that these implants can withstand the physical demands placed on them. Scientific Research Findings: According to AMFG, titanium’s mechanical properties make it a preferred material for orthopedic applications. Its resistance to wear and tear ensures longevity, reducing the need for frequent replacements. This durability provides patients with a reliable solution for bone repair and reconstruction.
Customization
Customization is a key benefit of 3D printed titanium bones. The technology allows for the creation of implants tailored to the specific anatomical needs of each patient. Scientific Research Findings: The MDPI journal notes that 3D printing technology enables precise control over the Young’s modulus of implants, matching them closely to natural bone tissues. This customization reduces the stress-shielding effect, promoting better integration with surrounding tissues. Patients receive implants that fit perfectly, enhancing comfort and functionality.
Reduced Recovery Time
3D printed titanium bones contribute to reduced recovery times for patients. The precise fit and biocompatibility of these implants facilitate quicker healing. Scientific Research Findings: The porous structures achievable through 3D printing enhance osseointegration, promoting better bone growth and stability around the implant. This improved integration leads to faster recovery, allowing patients to resume their daily activities sooner. The efficiency of this technology offers a promising outlook for those requiring bone implants.
Reduced Recovery Time
3D printed titanium bones significantly contribute to reduced recovery times for patients. The precise fit of these implants ensures that they align perfectly with the patient’s anatomy, promoting quicker healing. Scientific Research Findings: The Journal of Orthopaedic Surgery and Research highlights that titanium’s biocompatibility and mechanical properties make it an ideal choice for bone tissue repair. This compatibility allows for rapid bone formation and decreases bone absorption, which accelerates the healing process.
The porous structures achievable through 3D printing enhance osseointegration. This process involves the integration of the implant with the surrounding bone, leading to better stability and support. Scientific Research Findings: According to MDPI, 3D printing technology allows for precise control over the Young’s modulus of implants, matching them closely to natural bone tissues. This reduces the stress-shielding effect, promoting scaffold fixation into surrounding tissues.
Patients benefit from this advanced technology as it minimizes the time spent in recovery. They can resume their daily activities sooner, improving their quality of life. The ability to customize implants to fit individual needs further enhances the effectiveness of 3D printed titanium bones. This customization ensures that each implant provides optimal support and comfort, contributing to a smoother and faster recovery journey.
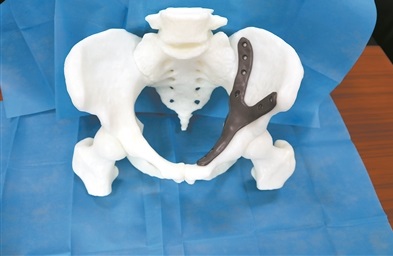
Cons of 3D Printed Titanium Bones
Cost
3D printed titanium bones come with a high price tag. The advanced technology and materials required for production contribute to this expense. Manufacturing these implants involves sophisticated equipment and skilled labor, which drive up costs. Additionally, the customization process, while beneficial, adds to the overall expense. Patients and healthcare providers often face financial challenges when considering these implants. Despite the potential for reduced recovery times and improved outcomes, the cost remains a significant barrier for widespread adoption.
Limited Availability
The availability of 3D printed titanium bones is limited. Not all medical facilities have access to the necessary technology and expertise. This limitation restricts the number of patients who can benefit from these innovative implants. In many regions, traditional implants remain the standard due to the lack of resources for 3D printing. The specialized equipment and trained personnel required for production are not universally available. As a result, patients in certain areas may not have the option to choose 3D printed titanium bones for their surgeries.
Technical Challenges
Technical challenges pose another hurdle for 3D printed titanium bones. The process of creating these implants requires precise control over various parameters. Any deviation can affect the quality and performance of the final product. Case Studies: Research on the structural design of porous titanium alloys highlights the importance of meticulous planning and execution. The complexity of designing implants that match the unique anatomical needs of each patient adds to the difficulty. Furthermore, limited data on the long-term performance of these implants raises concerns. Conflicting evidence suggests the need for more clinical trials to evaluate their effectiveness compared to traditional devices. These technical challenges necessitate ongoing research and development to ensure the reliability and safety of 3D printed titanium bones.
Long-term Data
The long-term performance of 3D printed titanium bones remains a topic of ongoing research. While these implants show promise in various applications, comprehensive data on their durability and effectiveness over extended periods is still emerging. Researchers have highlighted the need for more clinical trials to evaluate how these implants perform compared to traditional devices.
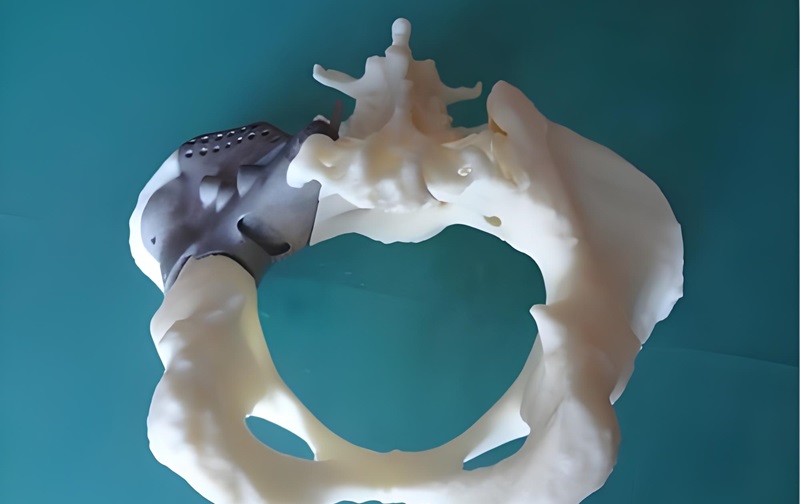
Case Studies:
- Titanium and its alloys for bone tissue repair: Studies on 3D-printed porous Ti6Al4V scaffolds demonstrate their potential in promoting rapid bone formation and decreasing bone absorption. These findings suggest that well-designed porous structures can enhance bone regeneration, yet long-term data is necessary to confirm these benefits.
- Performance of orthopedic implants produced by additive manufacturing: Conflicting evidence exists regarding the performance of 3D-printed implants versus conventionally manufactured devices. This inconsistency underscores the importance of further research to establish reliable conclusions about their long-term viability.
The structural design of porous titanium alloys plays a crucial role in bone regeneration. Researchers emphasize the significance of meticulous planning in creating implants that support long-term bone integration. The design criteria for titanium meshes, particularly in oral implant surgery, provide valuable insights into optimizing porosity for successful outcomes.
Despite the promising applications of titanium implants in surgeries involving the spine, hip, knee, and extremities, the lack of extensive long-term data presents challenges. Medical professionals and patients must consider these uncertainties when evaluating the suitability of 3D printed titanium bones for specific cases. As research progresses, a clearer understanding of their long-term performance will emerge, aiding in informed decision-making.
3D printed titanium bones offer a revolutionary approach to medical implants. They provide significant benefits, including biocompatibility, strength, and customization. These implants fit precisely, reducing recovery time and enhancing patient satisfaction. However, challenges such as high costs and limited availability persist. Technical hurdles and the need for long-term data also pose concerns. Despite these issues, the potential of 3D printed titanium bones remains promising. As technology advances, it is crucial for medical professionals and patients to weigh these pros and cons carefully, ensuring informed decisions about their use in healthcare.