
Titanium 3d printed part
Exploring the Revolution of Titanium 3D Printed Parts
Titanium 3D printing is at the forefront of transforming industries by offering new capabilities in manufacturing that traditional methods cannot match. This exploration delves into what makes titanium 3D printed parts a pivotal innovation in modern manufacturing, examining the technology, processes, and broad applications that make it indispensable for industries aiming to advance their operational efficiencies and product capabilities.
Titanium 3D printed parts are components produced through additive manufacturing processes like Direct Metal Laser Sintering (DMLS) or Selective Laser Melting (SLM), using titanium alloy powders, typically Ti6Al4V.

Introduction to Titanium 3D Printing
Definition and Overview
3D printing, or additive manufacturing, stands as a revolutionary technology, changing how industries conceive and produce complex parts. Titanium, known for its robustness and lightweight properties, has become increasingly significant in this field, offering new avenues for designing parts that are not only durable but also extremely precise and efficient.
Key Properties of Titanium 3D Printed Parts
Titanium offers exceptional benefits as a material for 3D printing, including its high strength-to-weight ratio, superior corrosion resistance, and the ability to withstand extreme temperatures. These properties make it ideally suited for demanding environments found in aerospace, automotive, and medical industries, providing the performance needed without sacrificing quality or safety.
- High strength-to-weight ratio: Titanium is lightweight yet extremely strong, making it ideal for applications where weight is a critical factor, such as aerospace and medical implants.
- Excellent corrosion resistance: Titanium is highly resistant to corrosion, making it suitable for harsh environments and biomedical applications.
- Biocompatibility: Titanium is biocompatible, meaning it can be safely used for medical implants and surgical instruments without causing adverse reactions in the human body.
- Complex geometries: 3D printing allows for the production of intricate shapes, internal channels, and lattice structures that would be difficult or impossible to manufacture using traditional methods.

The 3D Printing Process for Titanium
Key Technologies Involved
In DMLS or SLM, a high-powered laser selectively melts and fuses layers of titanium alloy powder according to a 3D CAD model. Support structures are often required for overhanging geometries. Post-processing like heat treatment, surface finishing, and machining may be performed.
Step-by-Step Process
The process begins with a digital blueprint of the object to be printed. Titanium powder is then precisely layered and melted by a focused laser or electron beam, which fuses the powder into a solid structure following the design parameters. This allows for the creation of complex geometries that traditional methods would find challenging or impossible to fabricate.
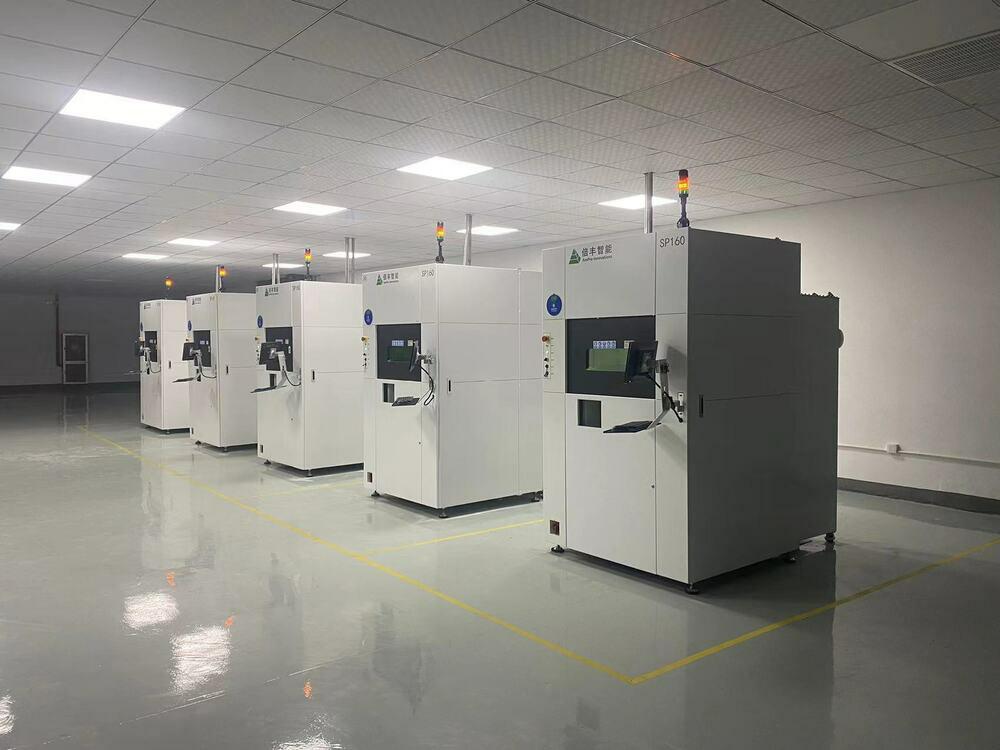
Properties of Titanium 3D Printed Parts
Material Characteristics
Titanium 3D printed parts exhibit excellent mechanical properties such as high tensile strength and density, essential for applications that demand durability and lightweight solutions. The technology also allows for customization in the microstructure of the parts, which can be tailored according to specific functional requirements.
Comparative Advantages
Compared to traditional manufacturing, titanium 3D printing offers unparalleled advantages in terms of waste reduction, customization, and the ability to produce complex designs without the need for multiple processes or assemblies. This results in a faster production cycle and significant cost savings in material and labor.
Applications of Titanium 3D Printed Parts
Aerospace Industry
In aerospace, titanium 3D printed parts are used to create components that contribute to the lightweight and robustness of aircraft. Examples include critical engine components, airframe structures, and intricate brackets—all benefiting from the weight-saving and performance-enhancing characteristics of titanium.
Medical Sector
The medical field utilizes titanium 3D printing for producing customized implants and prosthetic devices. These applications take advantage of titanium’s biocompatibility, allowing for personalized healthcare solutions that significantly improve patient outcomes.
More Applications
- Aerospace components (turbine blades, engine parts, airframe structures)
- Medical implants (orthopedic, dental, cardiovascular)
- Surgical instruments and tools
- Automotive and motorsports parts
- Industrial machinery components
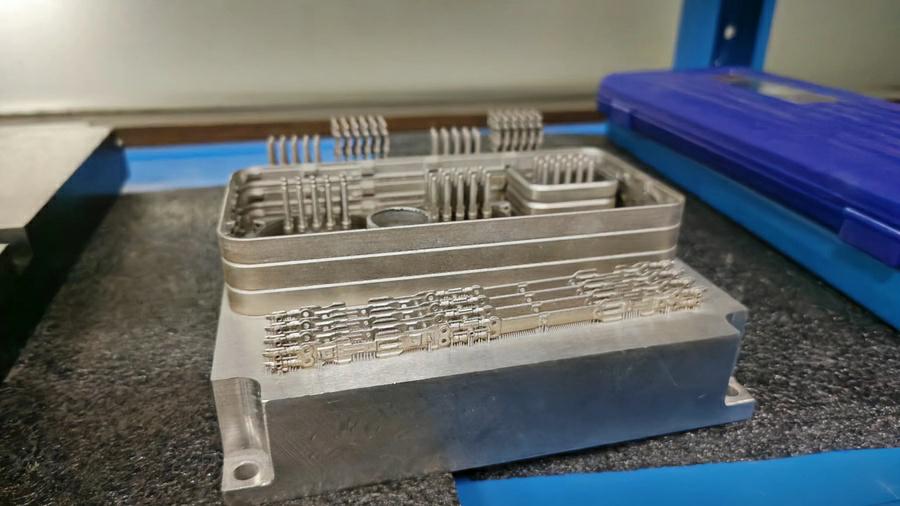
Challenges and Future Perspectives
Current Limitations
While promising, titanium 3D printing faces challenges such as high costs and technical complexities. The initial investment in machinery and material can be significant, and mastering the technology requires specialized skills and knowledge.
Future Trends
Future advancements are likely to focus on reducing costs, improving the speed and efficiency of printing processes, and expanding the range of titanium alloys available for printing. As these developments unfold, titanium 3D printing will become more accessible and widely used across various industries.
Conclusion
Titanium 3D printed parts represent a significant leap forward in manufacturing technology. By embracing these advancements, industries can enhance their product capabilities and operational efficiencies. The integration of titanium 3D printing into your production line is not just an upgrade—it’s a step toward future-proofing your manufacturing capabilities and embracing innovation that offers substantial competitive advantages. Let’s collaborate to unlock the potential of titanium in your projects, enhancing your product offerings and operational prowess.
