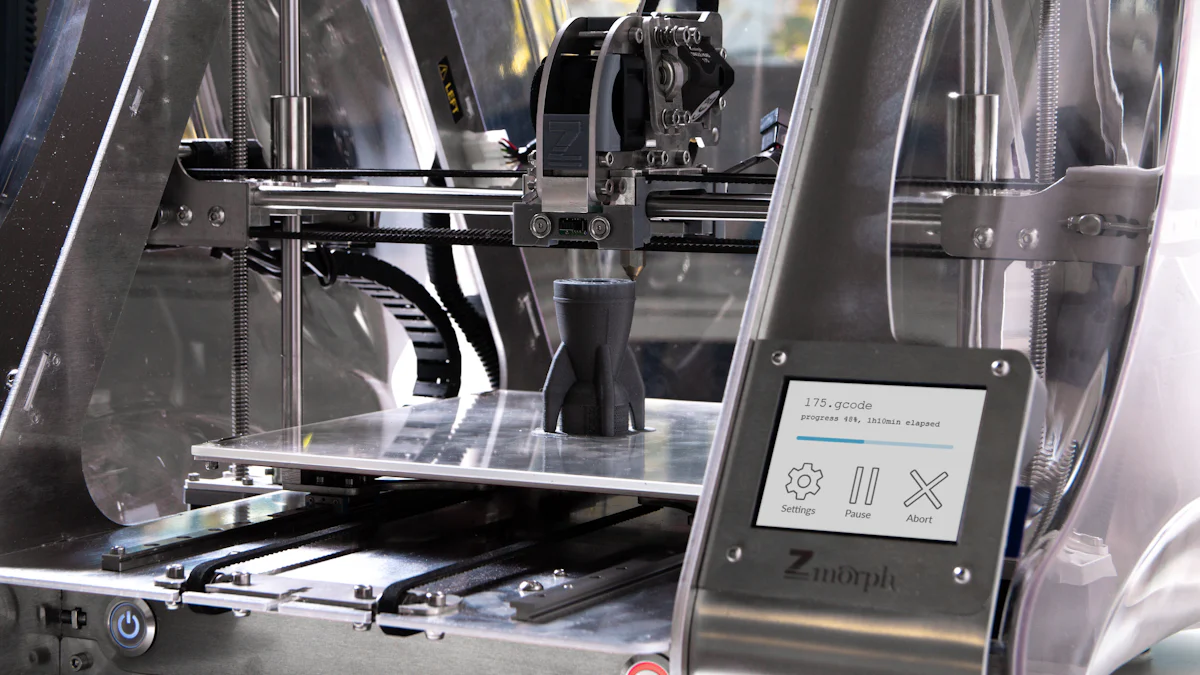
In the world of modern manufacturing, the Additive Manufacturing of Titanium Parts stands out as a game-changer, especially in industries like aerospace and medical. I see titanium as a vital material due to its exceptional properties. Its lightweight nature and high strength make it indispensable in aerospace, where about half of the global demand for titanium originates. The medical sector also benefits from titanium’s biocompatibility and corrosion resistance, ensuring safe and durable implants. These unique characteristics not only enhance manufacturing processes but also meet the stringent standards of these critical industries.
Key Takeaways
- Additive manufacturing, or 3D printing, revolutionizes titanium part production by building components layer by layer, allowing for complex designs and reduced material waste.
- Titanium’s unique properties, including strength, lightweight nature, and corrosion resistance, make it an ideal choice for critical applications in aerospace, medical, and automotive industries.
- Selective Laser Melting (SLM) and Electron Beam Melting (EBM) are the two primary techniques for additive manufacturing of titanium, each offering distinct advantages for different applications.
- Despite high initial costs, additive manufacturing can lead to long-term savings through reduced waste and shorter lead times, making it a cost-effective solution for small batch production.
- Customization and precision in additive manufacturing enhance the production of patient-specific medical implants, improving surgical outcomes and patient satisfaction.
- The sustainability aspect of additive manufacturing aligns with eco-friendly practices by minimizing energy consumption and material waste, supporting the growing demand for sustainable manufacturing.
- Overcoming technical challenges in additive manufacturing, such as equipment maintenance and quality control, is essential for achieving high-quality titanium parts and maximizing the technology’s potential.
Overview of Additive Manufacturing
Definition and Explanation
Additive manufacturing, often referred to as 3D printing, represents a transformative approach in the production of titanium parts. Unlike traditional methods that typically involve cutting away material from a solid block, additive manufacturing builds components layer by layer. This process begins with a digital 3D model, which guides the precise deposition of material. I find this method particularly advantageous for creating complex geometries that would be challenging or impossible to achieve with conventional techniques. The Additive Manufacturing of Titanium Parts not only enhances design flexibility but also reduces material waste, aligning with sustainable manufacturing practices.
Comparison with Traditional Manufacturing Methods
When I compare additive manufacturing to traditional manufacturing methods, several key differences stand out:
- Material Efficiency: Additive manufacturing significantly reduces waste. Traditional methods often involve subtractive processes, where excess material is removed and discarded. In contrast, additive manufacturing uses only the material necessary for the part, minimizing waste and lowering costs.
- Design Flexibility: The ability to create intricate designs is unparalleled in additive manufacturing. Traditional methods impose limitations on design complexity due to the constraints of machining tools. Additive manufacturing allows for the production of complex, lightweight structures that maintain strength and durability.
- Customization and Precision: Additive manufacturing excels in producing customized parts with high precision. This capability is particularly beneficial in industries like aerospace and medical, where specific requirements and exact specifications are crucial.
- Lead Time and Cost: While the initial setup for additive manufacturing can be costly, it offers long-term cost advantages. The elimination of specialized tooling and reduced lead times make it a cost-effective solution for small batch production.
- Sustainability: Additive manufacturing aligns with environmental sustainability goals by minimizing energy consumption and material waste. This approach supports the growing demand for eco-friendly manufacturing practices.
Benefits of Using Titanium
Strength and Durability
I find titanium’s strength and durability remarkable. This metal boasts an exceptional strength-to-weight ratio, making it ideal for demanding applications. Industries like aerospace and automotive rely on titanium for its ability to withstand high stress and extreme conditions. Titanium’s durability ensures that components maintain their integrity over time, reducing the need for frequent replacements. This reliability translates into cost savings and enhanced safety in critical applications.
Lightweight Properties
Titanium’s lightweight nature is another significant advantage. It offers the strength of steel at a fraction of the weight. This characteristic proves invaluable in sectors where weight reduction is crucial. In aerospace, for instance, lighter components contribute to fuel efficiency and improved performance. The automotive industry also benefits from titanium’s lightweight properties, as it helps in achieving better fuel economy and reduced emissions. I see this as a key factor in the growing adoption of titanium in these fields.
Corrosion Resistance
Corrosion resistance is one of titanium’s standout features. This metal forms a protective oxide layer that shields it from environmental factors. As a result, titanium components exhibit excellent corrosion resistance, even in harsh environments. This property makes titanium a preferred choice for marine applications and chemical processing industries. In the medical field, titanium’s corrosion resistance ensures the longevity and safety of implants, providing peace of mind to patients and healthcare professionals alike.
Additive Manufacturing Processes for Titanium
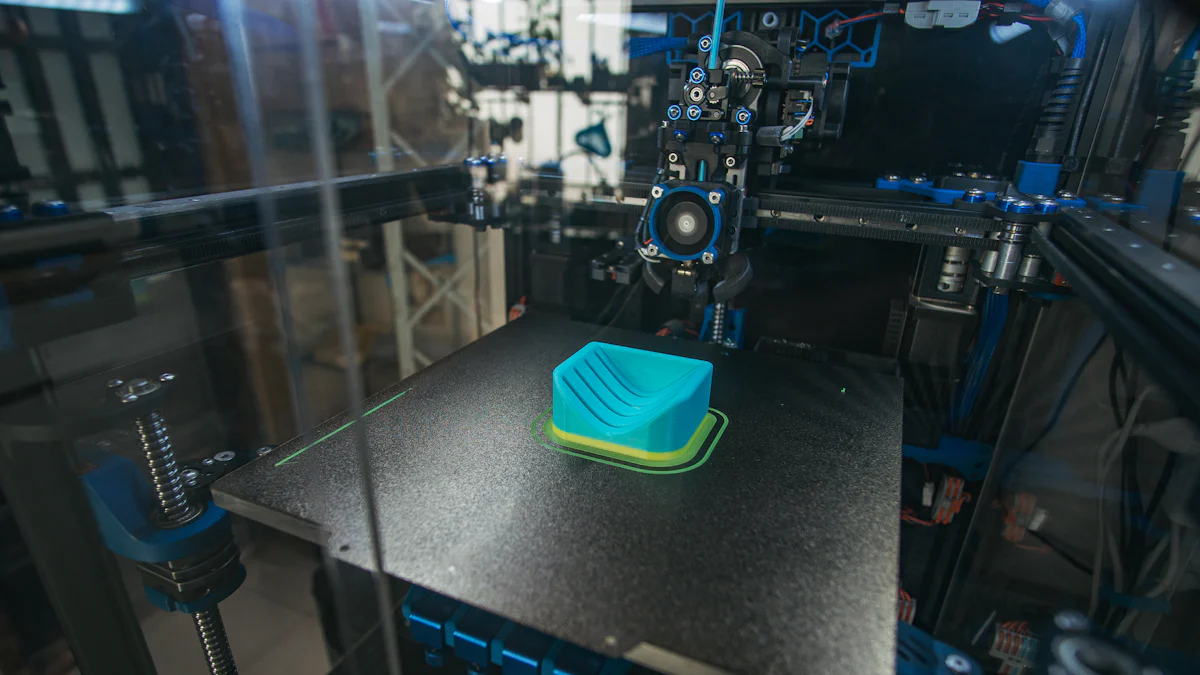
In the realm of additive manufacturing, two prominent techniques stand out for producing titanium parts: Selective Laser Melting (SLM) and Electron Beam Melting (EBM). Each method offers unique advantages and challenges, making them suitable for different applications within industries like aerospace and medical.
Selective Laser Melting (SLM)
Selective Laser Melting (SLM) utilizes a high-powered laser to fuse titanium powder into solid structures. I appreciate this method for its precision and ability to create intricate geometries. The laser selectively melts the powder layer by layer, guided by a digital 3D model. This process allows for the production of complex shapes that traditional methods cannot achieve.
- Precision and Detail: SLM excels in producing parts with fine details and smooth surfaces. The laser’s precision ensures that even the most intricate designs are accurately reproduced.
- Material Properties: The resulting parts often exhibit excellent mechanical properties, including high strength and durability. However, surface defects can occur, which may affect fatigue life. Researchers have noted that these defects, even after processes like Hot Isostatic Pressuring (HIPing), can influence stress concentration during fatigue tests.
- Applications: I find SLM particularly useful in the aerospace industry, where lightweight and complex components are essential. The medical field also benefits from SLM’s ability to produce patient-specific implants with high precision.
Electron Beam Melting (EBM)
Electron Beam Melting (EBM) employs an electron beam to melt titanium powder, layer by layer, in a vacuum environment. This technique offers distinct advantages, especially in terms of material properties and production speed.
- Vacuum Environment: The vacuum setting in EBM reduces the risk of oxidation, enhancing the quality of the titanium parts. This environment also contributes to the superior mechanical properties of the finished product.
- Production Speed: EBM generally operates at higher build rates compared to SLM, making it suitable for larger components. The electron beam’s efficiency allows for faster production without compromising quality.
- Surface Finish: While EBM parts may have a rougher surface finish compared to SLM, post-processing techniques can improve this aspect. The choice between SLM and EBM often depends on the specific requirements of the application.
Both SLM and EBM play crucial roles in the Additive Manufacturing of Titanium Parts. Each method offers unique benefits, allowing manufacturers to choose the most appropriate technique based on the desired properties and application of the titanium component.
Challenges and Considerations
Cost Implications
In the realm of additive manufacturing, cost implications present a significant challenge. I often find that the initial investment in equipment and technology can be substantial. High-quality 3D printers and the necessary software require a considerable financial outlay. Additionally, the cost of titanium powder, a primary material in this process, remains high. This expense can impact the overall budget, especially for small-scale operations.
Despite these costs, I believe the long-term benefits often outweigh the initial expenses. Additive manufacturing reduces material waste and shortens lead times, which can lead to cost savings over time. However, businesses must carefully evaluate their financial capacity and potential return on investment before committing to this technology.
Material Properties and Limitations
Titanium’s unique properties make it an excellent choice for additive manufacturing, but it also presents certain limitations. I have observed that while titanium offers exceptional strength and corrosion resistance, it can be challenging to work with due to its reactivity and high melting point. These characteristics require specialized equipment and expertise to ensure successful production.
Moreover, the quality of the titanium powder used in additive manufacturing plays a crucial role in the final product’s performance. Impurities or inconsistencies in the powder can lead to defects in the manufactured parts. Therefore, maintaining strict quality control measures is essential to achieve the desired material properties and ensure the reliability of the components.
Technical Challenges
Technical challenges in additive manufacturing of titanium parts are not uncommon. I have encountered issues related to the precision and accuracy of the printing process. Achieving the desired level of detail and surface finish requires careful calibration and maintenance of the equipment. Proper tool maintenance is crucial to avoid poor results, slow processes, tearing, bad surface finish, and heat buildup. This practice ensures efficient machining and cost control in titanium processing.
Additionally, the complexity of the designs often necessitates advanced software and skilled operators. Training personnel to handle these sophisticated systems can be time-consuming and costly. Despite these challenges, I believe that overcoming them is essential for harnessing the full potential of additive manufacturing in producing high-quality titanium parts.
Applications
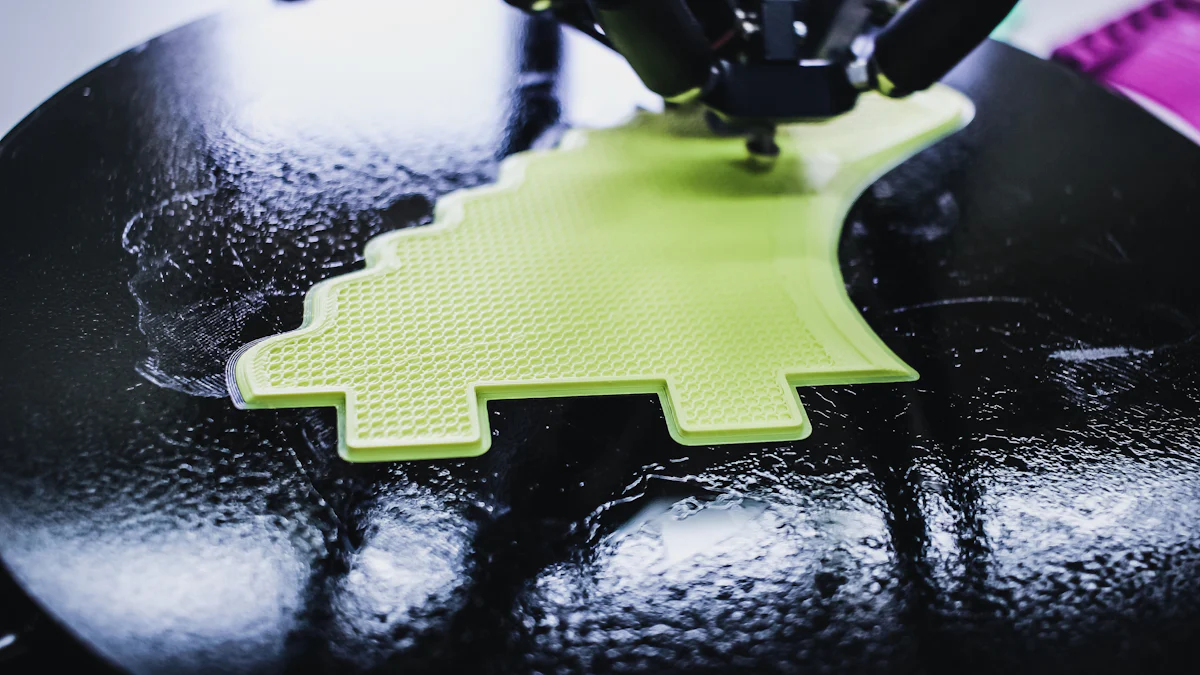
Aerospace Industry
In the aerospace industry, titanium has become indispensable. I have seen its use grow since the 1950s, when it was first utilized for its high tensile strength and excellent fatigue resistance. Titanium alloys, such as Ti-6Al-4V, have proven their worth in aircraft frames and engine components. These materials offer a remarkable strength-to-weight ratio, which is crucial for reducing the overall weight of aircraft. This reduction leads to improved fuel efficiency and performance.
Titanium’s corrosion resistance also plays a vital role in aerospace applications. It ensures long-term reliability and durability in harsh environments. Common uses include rotors, compression blades, and hydraulic system components. The metal’s ability to withstand extreme conditions makes it the material of choice for military and commercial aircraft alike. I believe that the Additive Manufacturing of Titanium Parts further enhances these applications by allowing for the creation of complex geometries that traditional methods cannot achieve.
Medical Implants
The medical field has long relied on titanium for implants due to its superior biocompatibility and strength. I have observed that titanium’s ability to integrate with human bone makes it ideal for orthopedic and dental implants. Its corrosion resistance ensures that implants remain safe and effective over time, providing peace of mind to both patients and healthcare professionals.
Additive manufacturing has revolutionized the production of medical implants. This technology allows for the creation of patient-specific implants tailored to individual anatomical needs. The precision and customization offered by additive manufacturing improve surgical outcomes and patient satisfaction. I see this as a significant advancement in medical technology, as it enhances the quality of life for many individuals.
Automotive Sector
In the automotive sector, titanium’s lightweight properties contribute to better fuel economy and reduced emissions. I have noticed an increasing trend towards using titanium in high-performance vehicles. Its strength and durability make it suitable for critical components such as exhaust systems and suspension parts.
The Additive Manufacturing of Titanium Parts offers additional benefits in the automotive industry. It enables the production of complex, lightweight structures that maintain strength and integrity. This capability supports the development of innovative designs and technologies that enhance vehicle performance. As the demand for eco-friendly and efficient vehicles grows, I expect titanium’s role in the automotive sector to expand further.
In my exploration of the Additive Manufacturing of Titanium Parts, I have highlighted its numerous benefits and challenges. This innovative approach offers remarkable advantages, such as reduced material waste, enhanced design flexibility, and the ability to produce complex geometries. However, it also presents challenges, including high initial costs and technical complexities. I see immense potential in this field, with future developments likely to enhance efficiency and broaden applications. As technology advances, I anticipate that additive manufacturing will continue to revolutionize industries, driving innovation and sustainability.
FAQ
What is additive manufacturing of titanium parts?
Additive manufacturing, often called 3D printing, involves creating titanium parts layer by layer from a digital model. This method allows for complex designs and reduces material waste compared to traditional manufacturing.
Why is titanium preferred in additive manufacturing?
I find titanium ideal for additive manufacturing due to its exceptional strength, lightweight properties, and corrosion resistance. These characteristics make it suitable for demanding applications in aerospace, medical, and automotive industries.
Is titanium additive manufacturing expensive?
The initial setup costs can be high, but titanium additive manufacturing offers long-term cost advantages. It reduces waste, utilizes materials efficiently, and eliminates the need for specialized tooling, which can lead to significant savings over time.
Can titanium additive manufacturing produce large-scale parts?
Producing large-scale titanium parts through additive manufacturing presents challenges due to production speed and build volume limitations. However, advancements in printing technologies are gradually enabling larger-scale applications.
What are the main techniques used in titanium additive manufacturing?
The two primary techniques are Selective Laser Melting (SLM) and Electron Beam Melting (EBM). SLM uses a laser to fuse titanium powder, while EBM employs an electron beam in a vacuum environment. Each method has unique advantages and is chosen based on specific application needs.
How does additive manufacturing benefit the aerospace industry?
In aerospace, additive manufacturing allows for the creation of lightweight, complex components that improve fuel efficiency and performance. Titanium’s strength and corrosion resistance ensure reliability in harsh environments, making it indispensable for aircraft parts.
What role does titanium play in medical implants?
Titanium’s biocompatibility and strength make it ideal for medical implants. Additive manufacturing enables the production of patient-specific implants, improving surgical outcomes and patient satisfaction by tailoring implants to individual anatomical needs.
How does additive manufacturing contribute to sustainability?
Additive manufacturing aligns with sustainability goals by minimizing energy consumption and material waste. It uses only the necessary material for each part, reducing environmental impact and supporting eco-friendly manufacturing practices.
What challenges exist in the additive manufacturing of titanium parts?
Challenges include high initial costs, technical complexities, and the need for specialized equipment and expertise. Maintaining strict quality control is essential to ensure the reliability and performance of the manufactured parts.
How does additive manufacturing impact the automotive sector?
In the automotive sector, titanium’s lightweight properties contribute to better fuel economy and reduced emissions. Additive manufacturing allows for the production of complex, lightweight structures that enhance vehicle performance and support innovative designs.