1. Basic Information about Titanium
Titanium, with the chemical symbol Ti and atomic number 22, is a lustrous transition metal known for its high strength, low density, and excellent corrosion resistance. These properties make titanium a highly valuable material in various industries such as aerospace, medical, and chemical processing.

Physical and Chemical Properties:
- Atomic Number: 22
- Atomic Weight: 47.87
- Density: 4.506 g/cm³
- Melting Point: 1,668°C (3,034°F)
- Boiling Point: 3,287°C (5,949°F)
- Modulus of Elasticity: 116 GPa
- Thermal Conductivity: 21.9 W/(m·K)
- Hardness: Mohs hardness 6
Titanium is abundant in the Earth’s crust, primarily found in minerals such as ilmenite and rutile. Its extraction involves complex processes like the Kroll process and the Hunter process, which convert titanium ore into usable metal.
Common Uses of Titanium:
- Aerospace: Aircraft frames, engines, and missiles
- Medical: Implants, prosthetics, and surgical instruments
- Industrial: Heat exchangers and chemical processing equipment
- Consumer Goods: Eyewear, jewelry, and sports equipment
2. What is the melting point of titanium?
The melting point of titanium is 1,668°C (3,034°F), making it a high melting point metal. This property allows it to withstand extreme temperatures without compromising structural integrity, making it highly versatile in various applications.
While titanium has a high melting point, some metals have even higher melting temperatures. A well-known example is tungsten, with a melting point of 3,422°C, almost twice that of titanium.
Other metals with melting points higher than titanium include:
- Rhodium – 1,963°C
- Tantalum – 3,020°C
- Iridium – 2,446°C
- Thorium – 1,755°C
- Vanadium – 1,910°C
Comparison with Other Metals:
Metal | Melting Point (°C) | Melting Point (°F) |
Aluminum | 660 | 1,220 |
Iron | 1,538 | 2,800 |
Titanium | 1,668 | 3,034 |
Stainless Steel | 1,375 – 1,530 | 2,507 – 2,786 |
Tungsten | 3,422 | 6,192 |
3. Three Main Factors Affecting the Melting Point of Titanium
3.1 Titanium Purity
The melting point of titanium can vary based on its purity. High-purity titanium has a higher melting temperature compared to titanium alloys. The presence of impurities and alloying elements can lower the melting point, affecting the metal’s performance in high-temperature applications.
3.2 Presence of Alloying Elements
Titanium alloys are created by adding elements such as aluminum, vanadium, and molybdenum. These additives significantly influence the melting point and other thermal properties. For example, the common titanium alloy Ti-6Al-4V has a melting range between 1,600°C and 1,650°C.
Example of Titanium Alloy | Titanium Alloy Melting Point (°C) |
Ti 6AL-4V | 1878 – 1933 |
Ti 6AL ELI | 1604 – 1660 |
Ti 3Al 2.5 | ≤ 1700 |
Ti 5Al-2.5S | ≤ 1590 |
3.3 Environmental Conditions
The melting point of titanium is also affected by environmental conditions, such as pressure and atmosphere. In a vacuum or inert gas environment, titanium maintains its high melting point. However, in an oxygen-rich atmosphere, titanium can react with oxygen at high temperatures, forming titanium oxide and effectively lowering its melting point.
4. Reasons for Titanium’s High Melting Point
Titanium’s high melting point can be attributed to several factors:
4.1 Atomic Structure
Titanium has a hexagonal close-packed (hcp) crystal structure at room temperature, which transforms into a body-centered cubic (bcc) structure at high temperatures. This stable atomic arrangement contributes to its high melting point.
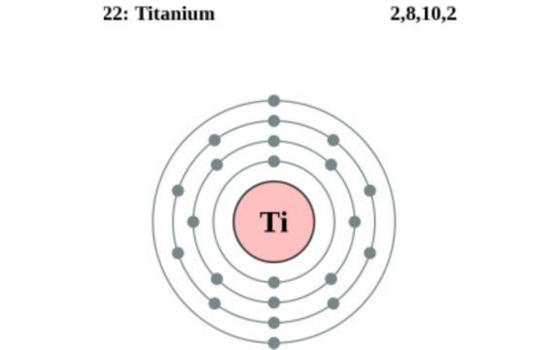
4.2 Bonding Characteristics
The strong metallic bonding in titanium involves the sharing of electrons between atoms, providing significant strength and stability. This bond strength means that the atoms do not easily dissociate from the matrix. Therefore, a considerable amount of thermal energy is required to break these bonds, leading to the transition from solid to liquid (melting titanium).
4.3 Comparison with Other High Melting Point Metals
Although titanium has a high melting point, it is lower than that of metals like tungsten and molybdenum. However, its advantageous properties, such as corrosion resistance and biocompatibility, make it more desirable for many applications that encounter extreme temperatures.
5. Thermal Properties and Applications of Titanium
Titanium’s thermal properties, including its high melting point, make it suitable for various high-temperature applications. Here are some key applications:
5.1 Material for Aircraft and Missile Manufacturing
In the aerospace sector, titanium’s high strength-to-weight ratio, combined with its ability to withstand extreme temperatures, makes it an ideal choice for aircraft frames, engines, and missile components. Additionally, titanium’s fatigue resistance and crack propagation resistance further enhance its application in this field.
5.2 Function as a Refractory Metal
With a melting point of 1,668°C, titanium is classified as a refractory metal, capable of maintaining its strength at high temperatures. Its heat and wear resistance make it suitable for industrial processes involving high-temperature environments, such as smelting and casting operations.
5.3 Titanium Heat Exchangers
Property | Titanium | Stainless Steel |
Melting Point (°C) | 1,668 | 1,375 – 1,530 |
Density (g/cm³) | 4.506 | 7.75 – 8.05 |
Thermal Conductivity | 21.9 W/(m·K) | 16.2 W/(m·K) |
Corrosion Resistance | Excellent | Very Good |
5.4 Turbine Engines
Titanium is widely used in turbine engines due to its high melting point and high-temperature strength. Components such as compressor blades, disks, and casings benefit from titanium alloys’ ability to withstand the harsh conditions inside turbine engines.
5.5 Titanium vs. Stainless Steel Melting Points
Compared to titanium, stainless steel has a lower melting point, making titanium advantageous in applications requiring high-temperature resistance. Stainless steel’s melting range is between 1,375°C and 1,530°C and, while it performs well, it cannot match titanium’s high-temperature capabilities.
Property | Titanium | Stainless Steel |
---|---|---|
Melting Point (°C) | 1,668 | 1,375 – 1,530 |
Density (g/cm³) | 4.506 | 7.75 – 8.05 |
Thermal Conductivity | 21.9 W/(m·K) | 16.2 W/(m·K) |
Corrosion Resistance | Excellent | Very Good |
6. Future Considerations and Advances in Titanium Use
The future of titanium applications is bright, with ongoing research and technological advancements aimed at improving its performance and expanding its uses. Innovations in titanium extraction, alloy development, and manufacturing processes continually enhance its performance and cost-effectiveness.
6.1 Advanced Titanium Alloys
Researchers are developing new titanium alloys with enhanced properties, such as increased strength, improved thermal conductivity, and better corrosion resistance. These advanced alloys are designed to meet specific needs in industries such as aerospace, automotive, and biomedical.
- Aerospace
In the aerospace industry, there is a continuous demand for materials that can withstand high temperatures and extreme stress. New titanium alloys with excellent creep resistance and fatigue strength, such as Ti-6Al-2Sn-4Zr-2Mo (Ti-6242), are being developed to improve the performance and lifespan of aircraft components. These alloys provide enhanced strength at high temperatures, making them suitable for turbine blades and other critical parts. - Automotive
The automotive industry is exploring titanium alloys to reduce vehicle weight and improve fuel efficiency. Alloys like Ti-5553 (Ti-5Al-5V-5Mo-3Cr) offer high strength and toughness, making them ideal for engine components, suspension systems, and exhaust systems. Using titanium in automotive applications not only reduces weight but also enhances vehicle durability and performance. - Biomedical
In the biomedical field, titanium alloys are designed to improve the biocompatibility and osseointegration of medical implants. Alloys such as Ti-6Al-7Nb and Ti-13Nb-13Zr are being developed to reduce the risk of allergic reactions and enhance the fusion of implants with bone tissue. These advancements lead to better outcomes for patients requiring orthopedic and dental implants.
6.2 Additive Manufacturing
Additive manufacturing, or 3D printing, is revolutionizing the production of titanium components. This technology enables the creation of complex geometries, reduces material waste, and shortens production times, making titanium parts more accessible and affordable.
- Complex Geometries
Additive manufacturing allows for the creation of intricate designs that are difficult or impossible to achieve with traditional manufacturing methods. This capability is particularly useful in the aerospace and medical industries, where custom, lightweight, and highly specialized components are often required. - Reduced Material Waste
Traditional manufacturing processes like machining and casting often result in significant material waste. In contrast, additive manufacturing uses only the necessary amount of material to build components layer by layer. Reducing waste not only lowers production costs but also minimizes the environmental impact of titanium manufacturing. - Shorter Production Times
The ability to rapidly produce titanium parts is a major advantage of additive manufacturing. Rapid prototyping and production enable manufacturers to shorten lead times, quickly respond to market demands, and innovate more effectively. This speed is crucial for industries such as aerospace and defense, where timely delivery of high-performance parts is essential.

6.3 Sustainable Use
Efforts are being made to reduce the environmental impact of titanium production. Recycling titanium scrap and developing more efficient extraction methods are key strategies for promoting sustainability in the titanium industry.
- Recycling Titanium Scrap
Recycling titanium scrap involves reprocessing waste titanium material into new products. This practice saves natural resources, reduces energy consumption, and lowers greenhouse gas emissions compared to primary titanium production. The aerospace industry, in particular, generates substantial titanium scrap that can be recycled to produce new aircraft components and other products. - Efficient Extraction Methods
Innovations in extraction methods aim to make titanium production more energy-efficient and environmentally friendly. For example, the FFC Cambridge process is a promising technology that reduces the energy required to extract titanium from its ores. This method not only lowers production costs but also reduces the carbon footprint of titanium manufacturing.
7. Conclusion
Titanium’s high melting point and exceptional properties make it a versatile and valuable material across industries. Understanding the factors affecting its melting temperature, the reasons for its high melting point, and its thermal properties helps optimize its use in high-temperature applications. As technology continues to advance, titanium’s role in modern engineering and industry is set to grow, offering new possibilities and solutions for future challenges.
By leveraging titanium’s advantages, industries can achieve greater efficiency, durability, and performance in their products and processes, ultimately driving innovation and progress. The future of titanium is bright, with ongoing research and development poised to unlock even more of its potential, making it an indispensable material for addressing the challenges and opportunities of the 21st century.