In the field of materials science, titanium and aluminum are two of the most widely used metals, each possessing unique characteristics that make them suitable for various applications. This article delves into the differences, advantages, and specific uses of titanium and aluminum, providing a comprehensive comparison to help you determine which metal best suits your needs.
1. Introduction to Titanium and Aluminum
Overview
Titanium and aluminum are two of the most commonly used metals in various industries today. Titanium is renowned for its high strength-to-weight ratio and excellent corrosion resistance, while aluminum is known for its lightweight and high conductivity.
Historical Background
Titanium was first discovered by William Gregor in 1791 and was later named by Martin Heinrich Klaproth. Its commercial production began in the 1950s. Aluminum was discovered in the early 19th century, with its commercial production starting in the late 19th century.
Common Uses
Titanium is widely used in aerospace, medical devices, and high-performance sports equipment. Aluminum, due to its versatility and low cost, is used in automotive parts, consumer electronics, and construction.
2.A comparison of the physical properties of titanium and aluminum
2.1 Melting Point
Property | Titanium | Aluminum |
Melting Point | 1,668°C (3,034°F) | 660°C (1,220°F) |
Titanium has a high melting point of 1,668°C (3,034°F), making it suitable for high-temperature applications such as aerospace and components in industrial furnaces. The high melting point of titanium ensures that it maintains structural integrity at extreme temperatures. In contrast, aluminum has a lower melting point of around 660°C (1,220°F), which makes it easier to cast and form. The low melting point of aluminum not only reduces production costs but also makes it an ideal choice for mass production of complex parts.
2.2 Density
Property | Titanium | Aluminum |
Density | 4.5 g/cm³ | 2.7 g/cm³ |
Titanium has a density of approximately 4.5 grams per cubic centimeter, which is higher than aluminum’s density of 2.7 grams per cubic centimeter. This makes titanium excellent for applications requiring high strength without significantly increasing weight, such as aerospace and biomedical implants. Aluminum, due to its lower density, is a lighter choice for applications where weight is a critical factor, such as in transportation and packaging. The low density of aluminum helps reduce the overall weight of products, improving energy efficiency and maneuverability.
2.3 Corrosion Resistance
Property | Titanium | Aluminum |
Corrosion Resistance | Excellent | Good |
Titanium can form a passive oxide layer, giving it excellent corrosion resistance, especially in harsh environments such as marine and chemical industries. This corrosion resistance makes titanium an ideal material for equipment and structures that need to be exposed to corrosive environments for extended periods. Aluminum also forms a protective oxide layer, but its corrosion resistance is inferior to that of titanium, especially in saline environments and other extreme conditions. While aluminum has good corrosion resistance in general environments, it requires additional protective measures in marine environments.
2.4 Conductivity
Property | Titanium | Aluminum |
Electrical Conductivity | 0.038 MS/m | 37.8 MS/m |
Thermal Conductivity | 21.9 W/m·K | 235 W/m·K |
Aluminum is an excellent conductor of electricity and heat, with an electrical conductivity of 37.8 MS/m and a thermal conductivity of 235 W/m·K, making it an ideal choice for electrical and thermal applications such as wires, cables, and heat sinks. Titanium, on the other hand, has an electrical conductivity of 0.038 MS/m and a thermal conductivity of 21.9 W/m·K, much lower than that of aluminum. This limits its use in electrical and thermal conduction applications. The lower electrical and thermal conductivity of titanium make it more suitable as a structural material rather than a conductor of electricity or heat.
2.5 Ductility
Property | Titanium | Aluminum |
Ductility | Moderate | High |
Aluminum is more ductile than titanium, making it easier to shape through processes like extrusion and rolling. Its high ductility makes it highly efficient in manufacturing thin sheets, pipes, and complex-shaped parts. While titanium still possesses ductility, its high strength and lower ductility require more specialized processing techniques and equipment. Titanium’s forming processes are typically more complex and costly, suitable for applications that demand high strength and durability.
In conclusion, titanium and aluminum exhibit significant differences in their physical properties. Titanium, with its high melting point, high density, and excellent corrosion resistance, is suitable for high-performance and high-temperature applications. Aluminum, with its low density, excellent conductivity, and high ductility, is widely used in lightweight and high-conductivity applications. The choice between the two materials depends on specific application requirements and environmental conditions.
3. Comparison of mechanical properties of titanium and aluminum
3.1 Formability
Aluminum has excellent malleability, allowing it to be easily formed into various shapes, making it an ideal choice for complex designs. This characteristic makes aluminum widely used in industries such as automotive, aerospace, and construction, where complex geometries are required. In contrast, titanium has higher strength, so more effort and specialized equipment are required during forming. Although titanium is more difficult to form, its unique properties make it competitive in certain high-demand applications.
3.2 Strength
3.2.1 Yield Strength
The yield strength of titanium is generally higher than that of aluminum, meaning it can withstand greater stress before deformation. Specifically, pure aluminum has a yield strength of about 35-40 MPa, while aluminum alloys can reach 200-600 MPa. In comparison, pure titanium has a yield strength of approximately 170 MPa, and titanium alloys (such as Ti-6Al-4V) can reach 830-900 MPa.
3.2.2 Tensile Strength
Titanium also has higher tensile strength, meaning it can withstand greater forces without fracturing. The tensile strength of pure aluminum is about 90 MPa, while high-strength aluminum alloys (such as 7075 aluminum alloy) can reach 500-600 MPa. In contrast, the tensile strength of pure titanium is about 240 MPa, and titanium alloys can reach 900-950 MPa. This makes titanium an ideal choice for applications requiring high durability, such as aerospace and military applications.
3.3 Hardness
Titanium is typically harder than aluminum, thus offering excellent wear resistance. The hardness (Brinell hardness) of pure aluminum is approximately 15 HB, while common aluminum alloys (such as 6061 aluminum alloy) can reach 95 HB. In comparison, the hardness of pure titanium is about 70 HB, and titanium alloys can reach 300-400 HB. This makes titanium a better choice for applications where surface durability is critical, such as medical implants and high-performance sporting equipment.
In conclusion, there are significant differences in the mechanical properties of titanium and aluminum. Aluminum, with its excellent formability and lower cost, is commonly used in applications requiring complex shaping. Titanium, on the other hand, with its high strength and hardness, has advantages in applications requiring high durability and wear resistance. The choice of material depends on specific application requirements and cost considerations.
4. Cost and Availability
4.1 Market Prices of Titanium and Aluminum
- Aluminum: The market price of aluminum is generally lower than that of titanium because aluminum resources are abundant, and the cost of mining and processing is lower. Aluminum ore mainly exists in the form of bauxite, which is extracted into pure aluminum through the electrolysis process, a relatively simple and cost-effective process. Therefore, the market price of aluminum is relatively low, usually around $2-3 per kilogram.
- Titanium: The cost of titanium is higher because its extraction and processing processes are more complex. Titanium ore mainly exists in the form of ilmenite or rutile, which needs to be converted into metallic titanium through the Kroll or Hunter process, a process that requires a large amount of energy and high technical requirements. Therefore, the market price of titanium is significantly higher than that of aluminum, usually around $10-20 per kilogram, and sometimes even higher.
4.2 Availability of Raw Materials
- Aluminum: Aluminum is the third most abundant element in the Earth’s crust, accounting for about 8% of the crust’s mass, making it very easy to obtain. The abundance of aluminum resources ensures its stable supply and relatively low market price. The major aluminum-producing countries include China, India, Russia, and Canada, which have abundant resources and advanced production technologies, further reducing the cost of aluminum.
- Titanium: The reserves of titanium are relatively small, accounting for about 0.57% of the Earth’s crust mass, making it costly and in limited supply. Although titanium is not scarce in the Earth’s crust, its distribution is more scattered, and its extraction is more challenging, leading to a relatively tight supply of titanium. The major titanium-producing countries include Australia, South Africa, and China.
4.3 Economic Impact
- Aluminum: The low cost and large supply of aluminum make it an economically viable choice for large-scale production. Due to its low market price, aluminum is widely used in industries such as construction, automotive, and packaging. Aluminum’s excellent malleability and good conductivity give it a clear economic advantage in manufacturing and processing processes.
5. Common Processing Methods for Titanium and Aluminum
Both titanium and aluminum can be processed using a variety of techniques to meet different industrial requirements. Some of the most common methods include:
5.1 Casting
Casting involves pouring molten metal into molds to form the desired shapes. This method is more common in aluminum due to its lower melting point, around 660°C (1220°F), making melting and casting easier and more cost-effective. Aluminum casting is widely used in the automotive and aerospace industries for producing lightweight and complex components.
5.2 Forging
Forging is used for both metals to manufacture high-strength components. The process involves shaping the metal using localized compressive forces (typically using hammers or presses). Forged titanium parts are renowned for their excellent strength-to-weight ratio, making them an ideal choice for critical aerospace applications. On the other hand, aluminum forging is commonly used for manufacturing automotive parts, sporting equipment, and various industrial components.
5.3 Extrusion
Extrusion involves squeezing metal billets through a die to form long, continuous shapes with a fixed cross-sectional profile. Aluminum is extensively extruded to produce complex profiles used in construction, transportation, and consumer goods. This process leverages aluminum’s excellent ductility to produce complex and precise shapes.
5.4 3D Printing
Both metals are used in additive manufacturing, also known as 3D printing. Titanium is particularly suitable for high-performance parts due to its high strength, light weight, and excellent corrosion resistance, making it ideal for medical implants, aerospace components, and custom manufacturing. Aluminum, with its good mechanical properties and lightweight characteristics, is also used in 3D printing for automotive, aerospace, and consumer goods applications.
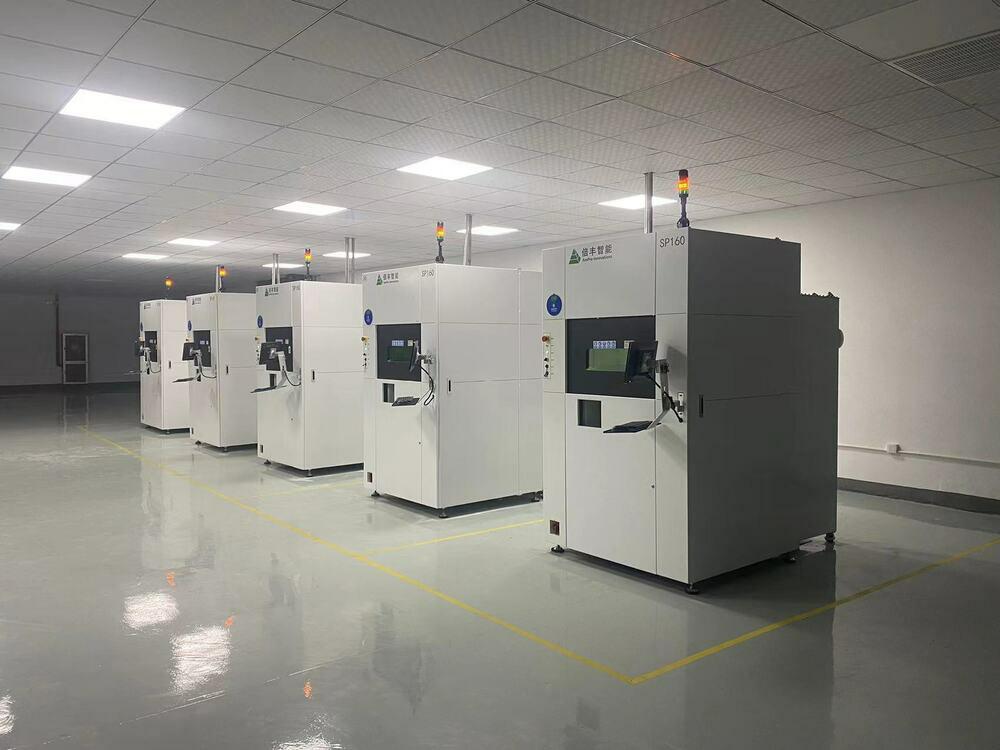
5.5 Metal Injection Molding (MIM)
Metal Injection Molding (MIM) is an advanced manufacturing technology that combines powder metallurgy with plastic injection molding to produce small metal parts with high precision and complex shapes. Both aluminum and titanium are used in the MIM process.
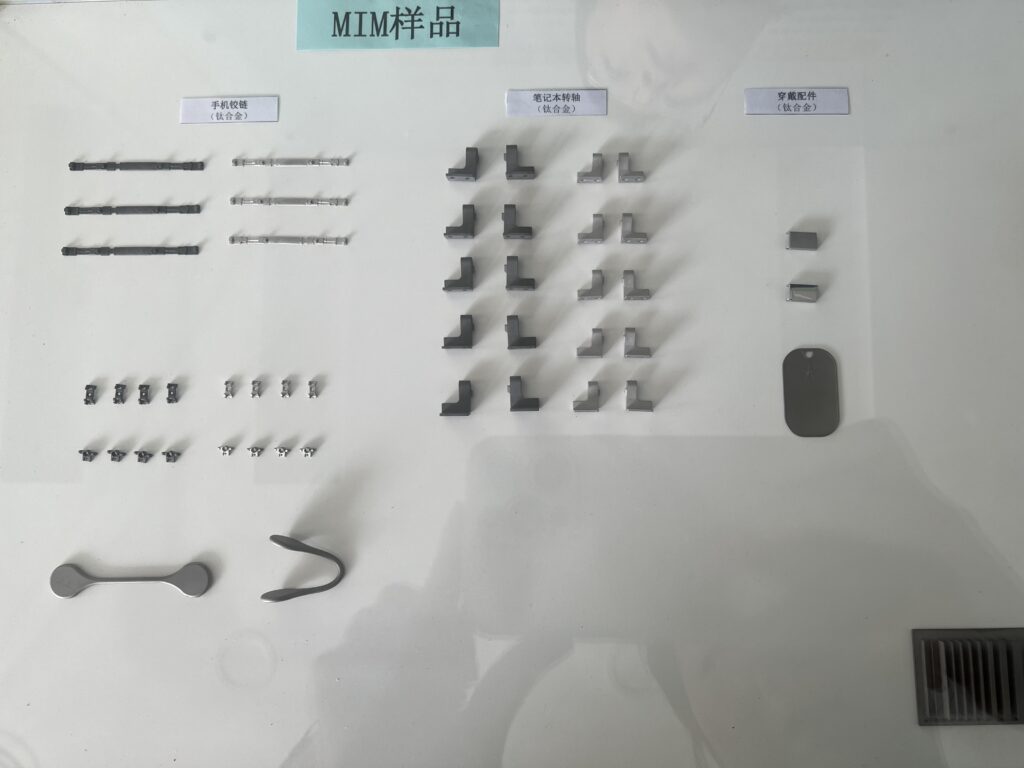
6. Surface Treatment
To enhance their performance and prolong their lifespan, titanium and aluminum undergo various surface treatments and coatings:
6.1 Anodizing
Both aluminum and titanium can be anodized to improve corrosion resistance and aesthetics. Anodizing is an electrochemical process that thickens the natural oxide layer on the metal surface. For aluminum, this process not only enhances corrosion resistance but also allows for a variety of colored finishes, making it popular in architectural and consumer applications. Titanium anodizing is used to enhance its biocompatibility in medical implants and to produce decorative colors for jewelry and high-end consumer goods.
6.2 Painting
Aluminum is often painted to enhance its appearance and provide additional protection against environmental factors. Painted aluminum is used in building facades, automotive exteriors, and household appliances. The paint layer adds a protective barrier, reducing the risk of corrosion and extending the material’s lifespan.
6.3 Plating
Titanium can be plated with other metals to enhance its surface properties for specific applications. For example, gold plating on titanium can improve its conductivity and is used in electronic components. Nickel plating on titanium is used in chemical processing equipment to enhance corrosion resistance. This flexibility allows titanium to be used for a wide range of specialized purposes.
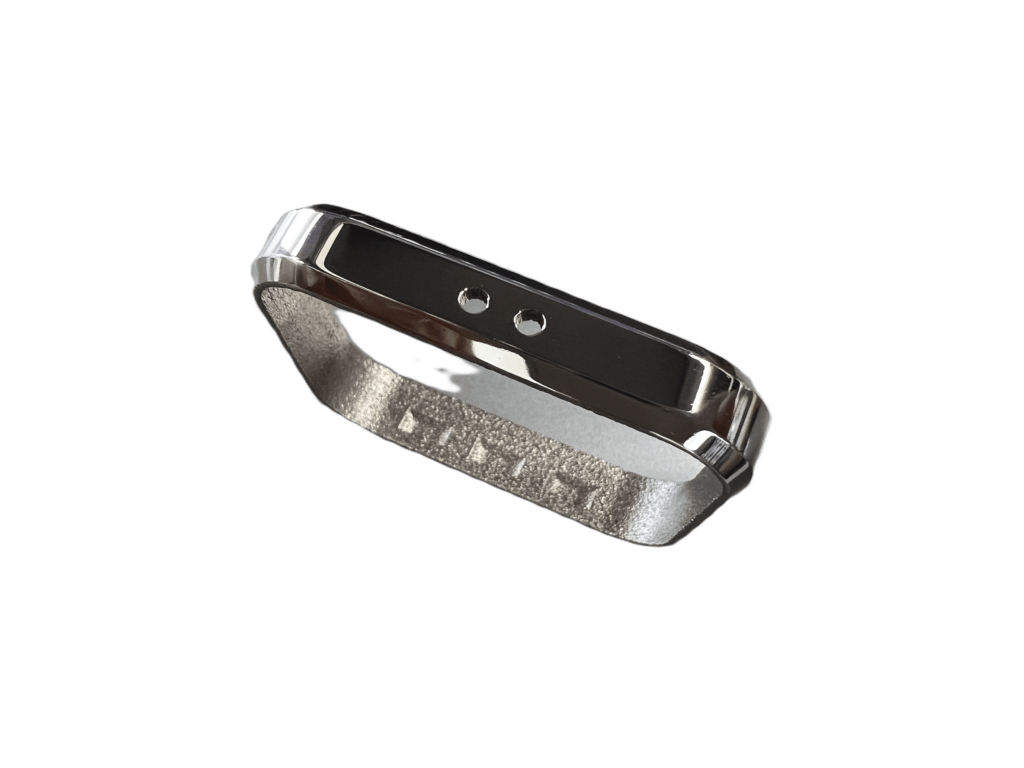
7. Advantages and disadvantages of titanium and aluminum
Properties | Titanium | Aluminum |
Advantages | High strength-to-weight ratio/Excellent corrosion resistance/Biocompatibility, suitable for medical use | Lightweight/Excellent conductivity/Easier to shape and form |
Disadvantages | Higher cost/Higher processing difficulty | Lower strength compared to titanium/Poorer corrosion resistance in harsh environments |
7.1 Advantages and Disadvantages of Titanium
Advantages:
- High strength-to-weight ratio: Titanium has a very high strength while being lightweight, making it ideal for aerospace and high-performance engineering applications.
- Excellent corrosion resistance: Titanium exhibits strong resistance to corrosion in various environments, especially in marine and chemical environments.
- Biocompatibility: Titanium is biologically inert and does not cause allergic reactions, so it is widely used in medical implants and surgical instruments.
Disadvantages:
- Higher cost: The mining and processing costs of titanium are high, making it uneconomical for certain applications.
- Higher processing difficulty: Titanium’s high strength and low thermal conductivity make it difficult to process, requiring special tools and techniques.
7.2 Advantages and Disadvantages of Aluminum
Advantages:
- Lightweight: Aluminum has a low density, only a fraction of titanium’s, making it an important material in the aerospace, automotive, and packaging industries.
- Excellent conductivity: Aluminum has good electrical conductivity and is widely used in the electrical and electronics industries.
- Easier to shape and form: Aluminum’s malleability and ductility make it easy to form complex shapes through various processing methods such as extrusion, rolling, and stamping.
Disadvantages:
- Lower strength compared to titanium: Aluminum has lower strength than titanium, limiting its use in certain high-strength applications.
Poorer corrosion resistance in harsh environments: While aluminum has some corrosion resistance, its performance in corrosive environments such as marine and chemical environments is not as good as titanium.
8. Comparison of Industry Applications
8.1 Aerospace
- Titanium: Widely used for aircraft frames, engine components, and spacecraft due to its high strength and corrosion resistance.
- Aluminum: Commonly used for fuselage structures, wings, and other key components requiring weight reduction.
8.2 Medical Industry
- Titanium: Preferred material for medical implants and surgical instruments due to its biocompatibility and durability.
- Aluminum: Used in medical devices and equipment requiring high demands on weight and conductivity.
8.3 Construction Industry
- Titanium: Used for high-end architectural components and structures due to its strength and corrosion resistance.
- Aluminum: Widely used for window frames, roofs, and exterior wall panels.
8.4 Consumer Electronics
- Titanium: Used in high-quality consumer electronics for durability and aesthetics.
- Aluminum: Commonly used in laptop bodies, smartphones, and other electronic devices for its lightweight and good thermal conductivity.
Industrial Manufacturing
- Titanium: Used for industrial applications requiring high strength and corrosion resistance.
- Aluminum: Widely used in industrial manufacturing for its versatility and lower manufacturing cost.
In summary, titanium and aluminum have their own advantages and applications in different industries. Titanium’s high strength, corrosion resistance, and biocompatibility make it essential for high-performance and critical applications, while aluminum’s lightweight, conductivity, and ease of processing make it widely used in various industrial and consumer applications.
9. Future Trends and Innovations
9.1 Research and Development
- Titanium
- New Alloy Development: Research focuses on improving the strength, corrosion resistance, and processability of titanium alloys. New titanium alloys, such as Ti-6Al-4V, demonstrate significant advantages in aerospace and medical applications.
- Process Technology Improvements: Research is optimizing titanium processing technologies, such as plasma arc welding and laser cutting, to increase production efficiency and reduce costs.
- Aluminum
- High-Strength Aluminum Alloys: Researchers are developing high-strength aluminum alloys, such as 7075 aluminum alloy, to enhance their competitiveness in high-performance applications. These alloys have excellent strength-to-weight ratios and are suitable for the aerospace and automotive industries.
- Nanostructured Aluminum: Adding nanomaterials to the aluminum matrix can significantly improve the mechanical properties and corrosion resistance of aluminum. This innovative technology is expected to bring breakthroughs in the electronics and construction industries.
9.2 Emerging Technologies
9.2.1 3D Printing
- Titanium: 3D printing technology is revolutionizing the way titanium is used. Additive manufacturing allows for the production of complex and lightweight titanium parts, particularly suitable for aerospace, medical, and high-performance automotive industries. For example, Boeing and Airbus have begun using 3D printing technology to manufacture aircraft components, significantly reducing production time and material waste.
- Aluminum: The application of aluminum in 3D printing is also expanding, especially in the production of prototypes and custom parts. Automakers like General Motors and Tesla are leveraging 3D printing technology to produce lightweight aluminum parts, enhancing vehicle performance and fuel efficiency.
9.2.2 Advanced Coatings
- Titanium: Advanced coating technologies, such as aluminum oxide coatings and titanium nitride coatings, are being used to further enhance the wear resistance and corrosion resistance of titanium. These coating technologies have wide application prospects in industrial machinery, medical implants, and sports equipment.
- Aluminum: Surface treatment technologies for aluminum are also advancing, such as anodizing and electrophoretic coating, to improve its corrosion resistance and aesthetics. Apple extensively uses anodized aluminum in its products, enhancing product durability and visual quality.
10. Common Questions
10.1 What are the main differences between titanium and aluminum?
- Titanium:
- Strength: Much stronger than aluminum, making it suitable for applications requiring high strength and durability.
- Corrosion Resistance: Excellent corrosion resistance, especially in harsh environments like marine or chemical industries.
- Weight: Heavier than aluminum, but with a better strength-to-weight ratio.
- Aluminum:
- Weight: Lighter than titanium, making it ideal for applications where weight reduction is important.
- Ductility: More ductile, making it easier to form complex shapes.
- Conductivity: Excellent electrical conductivity and thermal conductivity, making it the preferred choice in electrical and electronic applications.
10.2 Which metal is more cost-effective?
- Aluminum:
- Due to its more abundant reserves in the Earth’s crust and lower extraction and processing costs, it is generally more affordable.
- Lower production costs make aluminum an economical choice for mass-produced products.
- Titanium:
- Higher price due to complex extraction and refining processes.
- Initial costs are higher, but it can offer better long-term value in applications requiring high strength and durability.
10.3 Can aluminum replace titanium in aerospace applications?
High-strength aluminum alloys can replace titanium in some non-critical components where weight reduction is more important than strength and corrosion resistance. However, titanium remains the preferred choice for critical aerospace components (such as engine parts, landing gear, and structural elements) due to its excellent strength, fatigue resistance, and corrosion resistance.
10.4 Is titanium more suitable for medical implants?
Yes, titanium’s biocompatibility ensures it is non-toxic and well-tolerated by the human body. Its excellent corrosion resistance prevents degradation in the body, making it an ideal choice for long-term implants such as joint replacements, dental implants, and bone screws.
10.5 How does recycling affect the sustainability of these metals?
- Titanium: Recycling titanium can significantly reduce the need for raw material extraction, saving natural resources and reducing environmental impact. Recycled titanium retains its high quality and performance characteristics.
- Aluminum: Highly efficient aluminum recycling uses only about 5% of the energy needed to produce new aluminum from ores. This makes aluminum recycling a key factor in reducing energy consumption and environmental footprint.
10.6 What are some common applications of aluminum in consumer electronics?
- Laptop Cases: Aluminum’s lightweight and durability make it ideal for protecting and dissipating heat from laptops.
- Smartphone Bodies: Widely used for its stylish appearance, lightweight, and ability to conduct heat away from device components.
- Wearable Technology: Aluminum’s lightweight and corrosion resistance make it a popular choice for smartwatches and fitness trackers.
10.7 How do titanium and aluminum compare in terms of thermal conductivity?
- Titanium has lower thermal conductivity compared to aluminum, which limits its use in heat dissipation applications.
- Aluminum has excellent thermal conductivity, making it ideal for applications requiring efficient heat transfer, such as heat sinks, cooling systems, and others.
10.8 How does mining and processing these metals affect the environment?
- Titanium: Mining and processing titanium can have significant environmental impacts, including habitat destruction and water pollution. However, advances in sustainable mining practices are helping to mitigate these impacts.
- Aluminum: Bauxite mining (the primary source of aluminum) can lead to deforestation and soil erosion. However, the industry is increasingly adopting more sustainable practices and restoration work to reduce environmental damage.
10.9 Can titanium and aluminum be combined to make high-quality alloys?
Yes, titanium-aluminum alloys combine the advantages of both metals, providing enhanced performance for specific applications. These alloys are used in high-performance engineering, such as aerospace components and advanced manufacturing.
10.10 What are the maintenance requirements for products made from these metals?
- Titanium requires almost no maintenance due to its high corrosion resistance and durability, making it suitable for long-term, low-maintenance applications.
- Aluminum may require protective coatings or treatments to prevent corrosion in harsh environments. Regular maintenance may be needed to ensure longevity under such conditions.
10.11 Are there health risks associated with using these metals?
- Titanium is generally considered safe and biocompatible, making it suitable for medical implants and devices.
- Aluminum is generally safe for most applications, but research is ongoing into the potential health effects of long-term exposure to aluminum, especially in food and beverage containers.
Titanium and aluminum each have unique advantages that make them important players in different industries. Titanium has unparalleled strength and corrosion resistance, making it suitable for fields such as aerospace and medical industries that require high performance and durability. Aluminum, on the other hand, is widely used in fields such as aviation, automobiles and consumer electronics due to its light weight and versatility.
By taking advantage of the advantages of both metals while understanding their limitations, optimal performance, cost-effectiveness and sustainability can be achieved. Therefore, when selecting materials, the choice between titanium and aluminum needs to be weighed based on the specific needs and priorities of the project. Whether you are designing aerospace components, developing medical devices or creating consumer electronics, you need to consider these factors to ensure that you choose the most suitable material.