When comparing materials for strength, the debate of titanium vs aluminum strength reveals that titanium stands out as a superior choice. Titanium offers exceptional yield strength, tensile strength, and hardness, making it ideal for demanding applications. For instance, titanium can tolerate over 1100 MPa in tensional forces, while aluminum handles only 300 MPa. Despite being about 1.7 times denser, titanium’s strength-to-weight ratio surpasses aluminum, ensuring remarkable performance in high-stress environments. On the other hand, aluminum’s lightweight nature and cost-effectiveness make it a practical option for projects prioritizing affordability and reduced weight. Ultimately, the decision between these two materials hinges on the specific needs of the application, particularly when considering titanium vs aluminum strength.
Key Takeaways
- Titanium outperforms aluminum in yield strength, tensile strength, and hardness, making it the preferred choice for high-stress applications.
- Aluminum is lightweight and cost-effective, making it ideal for projects where affordability and reduced weight are priorities.
- The strength-to-weight ratio of titanium is superior, allowing it to maintain performance in demanding environments despite being denser than aluminum.
- Certain aluminum alloys can enhance strength, but they still fall short of titanium’s capabilities in high-stress situations.
- Durability is a key advantage of titanium, as it resists wear, impact, and corrosion better than aluminum, ensuring long-term reliability.
- In aerospace and automotive industries, the choice between titanium and aluminum depends on balancing performance needs with budget constraints.
- Understanding the specific requirements of your project is crucial in deciding whether to use titanium for strength or aluminum for cost-effectiveness.
Mechanical Properties of Titanium vs Aluminum
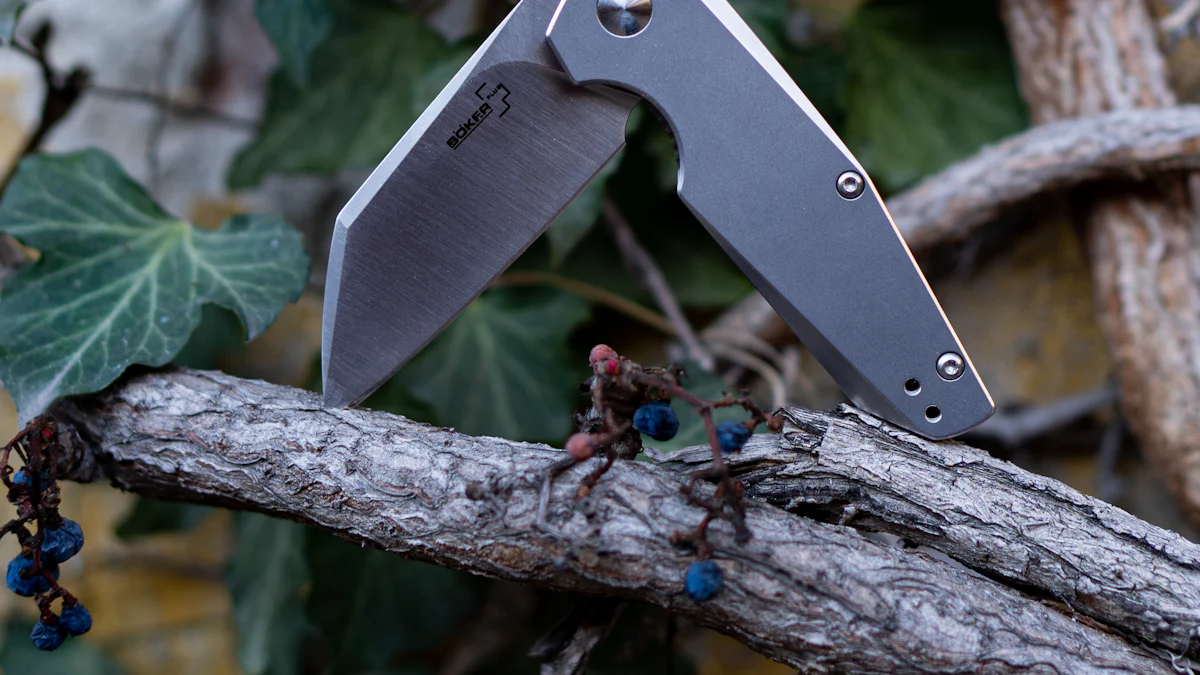
Yield Strength
Yield strength measures a material’s ability to resist deformation under stress. Titanium exhibits significantly higher yield strength compared to aluminum. Pure titanium offers yield strengths ranging from 170 MPa to 480 MPa, while aluminum typically falls between 7 MPa and 11 MPa. This disparity highlights titanium’s superior resistance to permanent deformation. For applications requiring materials to endure high stress without bending or breaking, titanium becomes the preferred choice.
Aluminum, however, compensates for its lower yield strength through alloying. Certain aluminum alloys, such as 7075 and 6061, achieve improved yield strength, making them suitable for structural applications. Despite these advancements, aluminum still cannot match titanium’s performance in high-stress environments. The comparison of titanium vs aluminum strength in terms of yield strength clearly favors titanium for demanding applications.
Tensile Strength
Tensile strength defines the maximum stress a material can withstand while being stretched or pulled before breaking. Titanium outperforms aluminum in this category as well. Titanium’s tensile strength ranges from 345 MPa to 1380 MPa, depending on the grade, whereas aluminum’s tensile strength varies between 140 MPa and 480 MPa. This vast difference underscores titanium’s ability to handle extreme forces without failure.
In industries like aerospace and medical devices, where materials must endure significant tension, titanium’s high tensile strength proves invaluable. Aluminum, while weaker, remains a viable option for less demanding applications due to its lightweight nature and cost-effectiveness. However, when strength is the primary concern, titanium consistently emerges as the superior material.
Hardness
Hardness measures a material’s resistance to surface deformation, such as scratching or denting. Titanium generally surpasses aluminum in hardness, making it more durable in harsh conditions. For example, titanium’s hardness allows it to maintain its structural integrity in environments where aluminum might suffer damage. This characteristic makes titanium ideal for applications requiring long-term durability and resistance to wear.
Some aluminum alloys, like AA7075 and AA6082 in specific tempers, exhibit higher hardness levels than pure titanium. These alloys are often used in industries where a balance between hardness and weight is essential. Nonetheless, titanium’s overall hardness advantage ensures its dominance in scenarios demanding exceptional surface resilience.
Physical Properties Influencing Strength
Density
Density plays a critical role in determining the strength-to-weight ratio of materials. Titanium, with a density of approximately 4.5 g/cm³, is denser than aluminum, which has a density of about 2.7 g/cm³. This difference means titanium weighs more than aluminum for the same volume. However, titanium compensates for its higher density with exceptional strength. Its strength-to-weight ratio surpasses aluminum, making it a preferred choice in industries like aerospace and automotive, where both strength and weight matter.
Aluminum’s lower density makes it ideal for applications requiring lightweight materials. For example, in aircraft manufacturing, aluminum reduces overall weight, improving fuel efficiency. Yet, titanium’s ability to withstand greater forces while maintaining a manageable weight often outweighs aluminum’s advantage in density. This balance between density and strength highlights why titanium dominates in high-performance applications.
Key Insight: Titanium’s higher density does not hinder its utility. Instead, its superior strength-to-weight ratio ensures its effectiveness in demanding environments.
Durability
Durability defines how well a material withstands wear, impact, and environmental factors over time. Titanium excels in this area, offering remarkable resistance to wear and tear. Components made from titanium can endure years of use without significant degradation. Its rigidity and toughness allow it to handle severe impacts, making it a reliable choice for long-term applications.
Aluminum, while durable in its own right, cannot match titanium’s resilience. Over time, aluminum components may show signs of fatigue or wear, especially in harsh conditions. Titanium’s durability extends to its corrosion resistance, which further enhances its longevity. For instance, titanium resists rust and chemical damage, even in marine or industrial environments.
Scientific Research Findings: Studies reveal that titanium’s durability stems from its inherent rigidity and resistance to environmental stressors. This makes it a superior option for projects requiring materials that last.
Practical Applications of Titanium and Aluminum
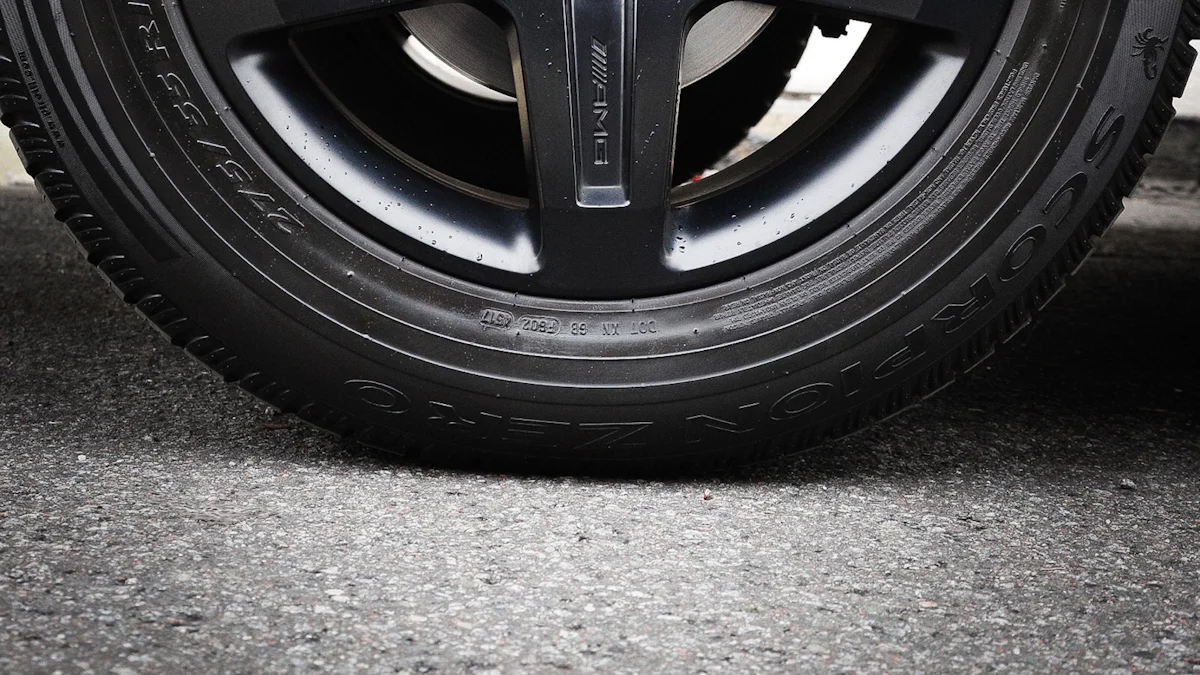
Aerospace Industry
In aerospace, material selection directly impacts performance and efficiency. Titanium plays a pivotal role due to its exceptional strength-to-weight ratio. Aircraft like the Boeing 747, introduced in 1969, incorporated titanium in engine components to handle high temperatures and thrust demands. This innovation established titanium as a cornerstone material in both military and commercial aviation. Military aircraft, such as the Lockheed A-12 and SR-71 Blackbird, relied heavily on titanium to endure extreme velocities and harsh conditions. These examples highlight titanium’s unmatched robustness under stress.
Aluminum, on the other hand, dominates in areas where weight reduction is critical. Its lightweight nature makes it ideal for constructing fuselages and wings, improving fuel efficiency. While aluminum cannot match titanium’s strength, its affordability and ease of fabrication make it indispensable in aerospace manufacturing. The balance between titanium and aluminum ensures optimal performance across various aerospace applications.
Key Insight: Titanium’s strength and durability excel in high-stress environments, while aluminum’s lightweight properties enhance fuel efficiency.
Automotive Industry
The automotive industry increasingly integrates titanium and aluminum to meet performance and sustainability goals. Titanium’s high strength and corrosion resistance make it suitable for critical components like exhaust systems and engine valves. These parts benefit from titanium’s ability to withstand extreme heat and wear, ensuring long-term reliability. High-performance vehicles often use titanium to reduce weight without compromising safety or durability.
Aluminum, however, remains the go-to material for mass-market vehicles. Its lightweight properties improve fuel economy and reduce emissions. Manufacturers use aluminum in body panels, frames, and wheels to achieve a balance between cost and performance. While titanium offers superior strength, its higher cost limits its widespread use in everyday vehicles. Together, these materials drive innovation in automotive design and engineering.
Construction and Architecture
In construction and architecture, material choice influences structural integrity and aesthetics. Titanium’s durability and corrosion resistance make it ideal for projects exposed to harsh environments. For instance, titanium cladding protects buildings from weathering while maintaining a sleek, modern appearance. Its strength allows architects to design bold, innovative structures that stand the test of time.
Aluminum, with its lightweight and versatile nature, finds extensive use in construction. Window frames, roofing, and curtain walls often feature aluminum due to its affordability and ease of installation. While aluminum lacks titanium’s strength, its adaptability makes it a practical choice for a wide range of architectural applications. The combination of titanium and aluminum enables engineers to create structures that are both functional and visually striking.
Professional Insight: The choice between titanium and aluminum in construction depends on project requirements. Titanium excels in durability and strength, while aluminum offers cost-effective versatility.
Cost Comparison: Strength vs Cost-Effectiveness
Titanium
Titanium stands out for its exceptional strength and durability, but these qualities come at a premium. The cost of titanium remains significantly higher than aluminum due to several factors. First, titanium is less abundant in nature, which makes its extraction more challenging. Second, the processing and machining of titanium require advanced techniques. These processes involve high energy consumption and specialized equipment, driving up production costs.
For industries prioritizing performance over budget, titanium justifies its price. Its superior strength-to-weight ratio and corrosion resistance make it indispensable in aerospace, medical, and high-performance automotive applications. For example, titanium components in jet engines or surgical implants offer unmatched reliability and longevity. However, the high cost limits its use in projects where affordability takes precedence.
Fact: Titanium’s price reflects its superior material properties. While expensive, it delivers unparalleled strength and durability, making it a worthwhile investment for critical applications.
Aluminum
Aluminum, on the other hand, offers a more economical solution. Its abundance in the Earth’s crust ensures a steady supply, keeping raw material costs low. Additionally, aluminum’s ease of machining and fabrication reduces manufacturing expenses. These factors make aluminum an attractive choice for industries with tight budgets or large-scale production needs.
Despite its lower cost, aluminum provides a balanced combination of strength and weight. This balance makes it ideal for applications like automotive frames, aircraft fuselages, and construction materials. For instance, aluminum’s affordability allows manufacturers to produce lightweight vehicles and structures without compromising functionality. While it cannot match titanium’s strength, its cost-effectiveness ensures widespread use across various sectors.
Key Insight: Aluminum’s affordability and versatility make it the go-to material for cost-sensitive projects. Its lightweight nature further enhances its appeal in industries like transportation and construction.
Titanium surpasses aluminum in yield strength, tensile strength, and hardness. Its superior performance makes it the go-to material for high-performance applications like aerospace and medical engineering. Aluminum, however, stands out for its lightweight nature and affordability, making it ideal for projects where cost and weight are critical. The decision between these two materials depends on the specific needs of the project. Balancing strength, weight, durability, and cost ensures the right choice for each application. The comparison of titanium vs aluminum strength highlights the trade-offs between performance and practicality.
FAQ
Is titanium stronger than aluminum?
Yes, titanium is stronger than aluminum. It offers a higher tensile strength and toughness, making it ideal for applications requiring durability and resilience. For example, titanium can withstand extreme forces without breaking, which is why industries like aerospace and medical devices rely on it. Its superior strength-to-weight ratio ensures that it delivers exceptional performance without adding unnecessary weight.
Is titanium lighter than aluminum?
No, titanium is not lighter than aluminum. Titanium has a higher density, making it heavier. However, its strength-to-weight ratio surpasses aluminum, meaning it provides more strength for its weight. This property makes titanium a preferred choice for components that need to endure severe impacts and wear, such as gears or aerospace parts, while maintaining manageable weight.
Why is titanium more expensive than aluminum?
Titanium costs more due to its scarcity and the complexity of its extraction and processing. Mining titanium requires advanced techniques, and its machining involves specialized equipment and high energy consumption. These factors drive up production costs. Despite the price, titanium’s unmatched strength and durability make it a worthwhile investment for critical applications like jet engines and surgical implants.
Can aluminum alloys match titanium’s strength?
Certain aluminum alloys, such as 7075 and 6061, achieve improved strength through alloying. These alloys perform well in structural applications and offer a balance between strength and weight. However, even the strongest aluminum alloys cannot match titanium’s performance in high-stress environments. Titanium remains the superior choice for applications demanding maximum strength and durability.
Which material is better for aerospace applications?
Both titanium and aluminum play vital roles in aerospace. Titanium excels in high-stress environments due to its strength and durability. It is often used in engine components and areas exposed to extreme conditions. Aluminum, being lightweight and cost-effective, is ideal for fuselages and wings, where reducing weight improves fuel efficiency. The choice depends on the specific requirements of the application.
Is titanium more durable than aluminum?
Yes, titanium is more durable than aluminum. It resists wear, impact, and environmental factors better, making it suitable for long-term use in harsh conditions. Titanium also offers superior corrosion resistance, even in marine or industrial environments. While aluminum is durable in its own right, it cannot match titanium’s resilience over time.
Why is aluminum preferred in cost-sensitive projects?
Aluminum is abundant and easier to process, which keeps its costs low. Its affordability makes it an attractive option for industries with tight budgets or large-scale production needs. Aluminum also offers a good balance of strength and weight, making it practical for applications like automotive frames and construction materials. This cost-effectiveness ensures its widespread use.
What are the main advantages of titanium?
Titanium stands out for its exceptional strength, durability, and corrosion resistance. It performs well in high-stress environments and maintains its integrity over time. Its strength-to-weight ratio makes it ideal for aerospace, medical, and high-performance automotive applications. Although more expensive, titanium delivers unmatched reliability and longevity.
What are the main advantages of aluminum?
Aluminum’s lightweight nature and affordability make it a versatile material. It is easy to machine and fabricate, which reduces manufacturing costs. Aluminum works well in applications where weight reduction and cost savings are priorities, such as automotive and construction projects. Its adaptability ensures its relevance across various industries.
How do I choose between titanium and aluminum?
The choice depends on your project’s specific needs. If strength, durability, and long-term performance are critical, titanium is the better option. For projects prioritizing weight reduction and cost-effectiveness, aluminum offers a practical solution. Consider factors like budget, application requirements, and environmental conditions to make the best decision.