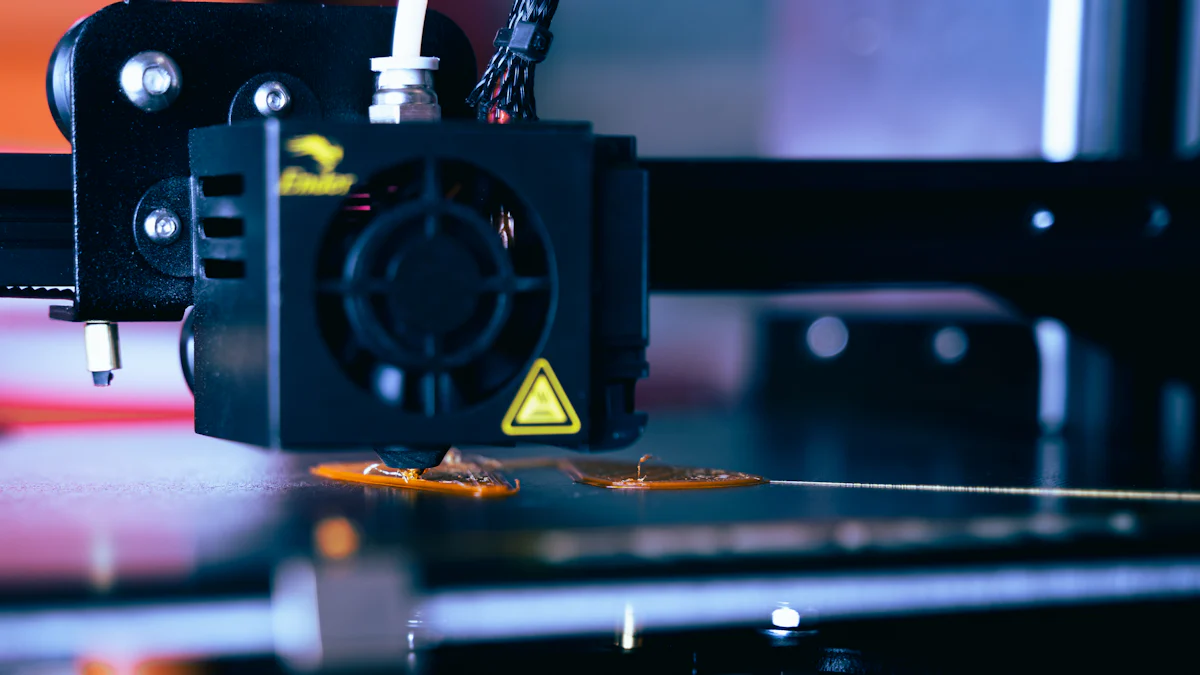
Titanium sternum 3D printing represents a groundbreaking advancement in medical technology. This innovative process involves using 3-D laser printing to create custom-made titanium implants for chest wall reconstruction. The precision of this technology allows for implants that perfectly match the patient’s anatomy, significantly improving surgical outcomes. Patients who have undergone this procedure often experience fewer complications and better recovery. In one study, three out of five patients remained free from implant-related issues over a 20-month follow-up period. This life-saving innovation offers hope and improved quality of life for many individuals.
The Need for Sternum Implants
The human sternum, or breastbone, plays a crucial role in protecting vital organs such as the heart and lungs. Damage to this area can result from trauma, congenital defects, or surgical procedures like open-heart surgery. In such cases, sternum implants become necessary to restore the chest wall’s integrity and function.
Traditional Methods and Their Limitations
Traditional methods for sternum reconstruction often involve using materials like metal plates or synthetic meshes. These materials, while functional, present several limitations:
- Lack of Customization: Traditional implants often come in standard sizes, which may not fit every patient’s unique anatomy. This can lead to discomfort or complications post-surgery.
- Increased Surgical Time: The process of fitting and securing these implants can be time-consuming, increasing the duration of surgery and the associated risks.
- Limited Durability: Over time, traditional materials may not withstand the body’s movements, leading to potential implant failure or the need for additional surgeries.
The Rise of 3D Printing in Medical Applications
The advent of titanium sternum 3d printing has revolutionized the field of medical implants. This technology offers several advantages over traditional methods:
- Precision and Customization: 3D printing allows for the creation of implants tailored to the patient’s specific anatomical features. Surgeons use 3-D laser printing to produce titanium implants that perfectly match the patient’s sternum, cartilages, and ribs. This precision reduces the risk of complications and enhances patient comfort.
- Reduced Surgical Time: The use of 3D printed implants simplifies the challenge of chest wall reconstruction. Surgeons can quickly secure these custom-made implants, reducing operating time and improving overall surgical outcomes.
- Material Benefits: Titanium, known for its high strength-to-weight ratio, is the material of choice for these implants. It integrates well with bone and does not flex with movement at joints, ensuring long-term durability and stability.
Titanium sternum 3d printing represents a significant leap forward in medical technology. By addressing the limitations of traditional methods, it offers patients a more effective and reliable solution for sternum reconstruction.

Understanding the 3D Printing Process
How 3D Printing Works
3D printing, also known, as additive manufacturing, builds objects layer by layer from a digital model. In the context of titanium sternum 3d printing, this process begins with a detailed CT scan of the patient’s chest. Surgeons use this scan to create a precise digital model of the sternum and surrounding structures. The 3D printer then uses this model to construct the implant, depositing layers of titanium powder and fusing them with a laser. This method allows for the creation of complex shapes that perfectly match the patient’s anatomy.
Scientific Research Findings:
- Evaluation of Long-Term Outcomes of Chest Wall Reconstruction with 3D-Printed Pure-Titanium Implant: This study highlighted the superior mechanical properties of 3D-printed titanium implants, which contribute to successful surgical outcomes.
The precision of titanium sternum 3d printing reduces the risk of complications during surgery. By creating implants that fit perfectly, surgeons can minimize the time spent adjusting the implant during the procedure. This efficiency not only shortens the operating time but also enhances the overall success of the surgery.
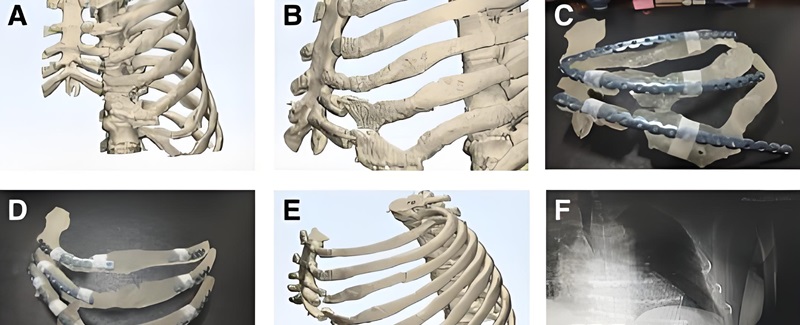
Why Titanium is the Material of Choice
Titanium stands out as the preferred material for sternum implants due to its unique properties. It boasts a high strength-to-weight ratio, making it both strong and lightweight. This characteristic is crucial for implants, as it ensures durability without adding unnecessary weight to the chest area.
Scientific Research Findings:
- Use of 3D Printing Technology for Titanium Implants in Chest Wall Reconstruction: This research underscores how 3D laser printing technology simplifies complex reconstructions and reduces surgical time.
Titanium’s biocompatibility further enhances its suitability for medical applications. The body readily accepts titanium, reducing the risk of rejection or adverse reactions. Additionally, titanium does not corrode, ensuring the implant remains stable over time. These properties make titanium sternum 3d printing a reliable choice for patients requiring chest wall reconstruction.
Advantages of 3D Printed Titanium Sternum Implants
Customization and Precision
Titanium sternum 3D printing offers unparalleled customization and precision in medical implants. Surgeons can create implants that fit the unique anatomical features of each patient. This level of customization ensures that the implant aligns perfectly with the patient’s sternum, cartilages, and ribs. Unlike traditional implants, which often come in standard sizes, 3D printed titanium implants are tailored to the individual. This precision reduces the risk of complications and enhances patient comfort.
The process begins with a detailed CT scan of the patient’s chest. Surgeons use this scan to design a digital model of the implant. The 3D printer then constructs the implant layer by layer, using titanium powder fused with a laser. This method allows for the creation of complex shapes that match the patient’s anatomy precisely. The result is an implant that integrates seamlessly with the body, providing a more natural and effective solution for chest wall reconstruction.
Durability and Biocompatibility
Titanium sternum 3D printing also excels in terms of durability and biocompatibility. Titanium, known for its high strength-to-weight ratio, provides a robust yet lightweight solution for sternum implants. This characteristic ensures that the implant can withstand the body’s movements without adding unnecessary weight to the chest area. The durability of titanium makes it a superior choice compared to traditional materials, which may not endure long-term use.
Biocompatibility is another critical advantage of titanium sternum 3D printing. The body readily accepts titanium, reducing the risk of rejection or adverse reactions. Titanium does not corrode, ensuring that the implant remains stable over time. These properties make titanium an ideal material for medical applications, offering patients a reliable and long-lasting solution for sternum reconstruction.
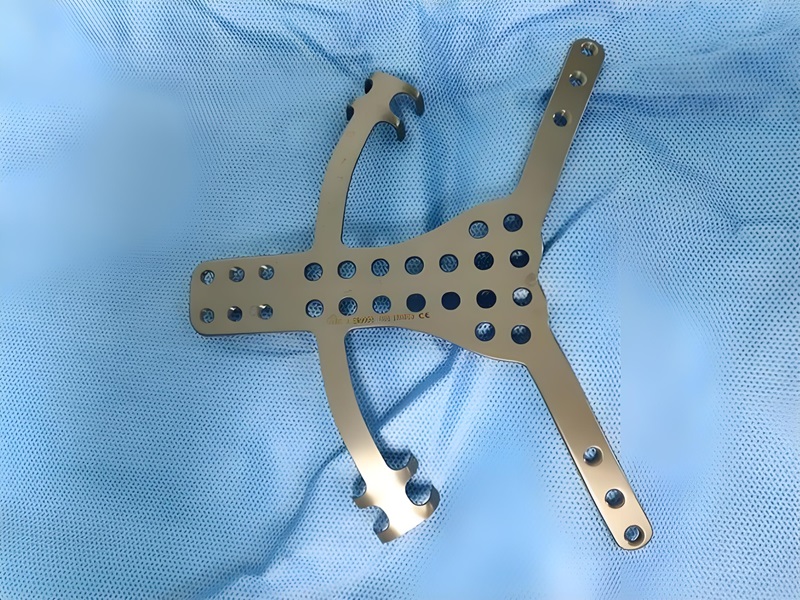
Real-Life Applications and Success Stories
Case Studies of Successful Implants
Reconstruction with a Patient-Specific Titanium Implant: Surgeons have successfully used customized titanium implants for patients undergoing wide anterior chest wall resection. They designed these implants based on the precise measurements of the chest wall defect obtained from computed tomography scans. This approach ensured that the implants fit perfectly, leading to uneventful recoveries without complications during the hospital stay. The precision of these implants highlights the transformative potential of 3D printing in medical applications.
Chest Wall Reconstruction with 3D Printed Titanium Ribs and Hemi-Sternum Implant: Another remarkable case involved the use of anatomically designed 3D printed titanium ribs and hemi-sternum implants. These implants not only preserved the anatomical shape and physiological function of the chest wall and thoracic spine but also had a positive psychological impact on the recipient. The success of this case underscores the importance of personalized medical solutions in enhancing both physical and mental well-being.
Patient Testimonials and Outcomes
Patients who have received 3D printed titanium sternum implants often express profound gratitude for the life-changing impact of these procedures. Many report significant improvements in their quality of life, with reduced pain and increased mobility. One patient shared how the implant allowed them to return to daily activities without discomfort, emphasizing the implant’s role in restoring normalcy.
Another patient highlighted the psychological benefits, noting a boost in confidence and self-esteem after the surgery. The implant’s seamless integration with their body provided not only physical stability but also emotional reassurance. These testimonials reflect the broader success of 3D printed titanium implants in delivering comprehensive care that addresses both the physical and emotional needs of patients.
Future Implications and Advancements
Potential for Broader Applications
3D printing technology holds immense potential for expanding its applications in the medical field. Currently, it plays a crucial role in creating patient-specific implants, surgical instruments, and anatomical models. This capability allows for more personalized and effective treatments. As the technology advances, its use could extend to other areas of medicine, such as prosthetics and dental applications.
Scientific Research Findings:
- 3D Printing in Medical Device Manufacturing: The technology is increasingly used to manufacture final-use, patient-specific medical devices, reducing costs and allowing for custom parts and complex designs. This adaptability suggests that 3D printing could soon become a standard practice in various medical procedures.
The potential for broader applications also includes the development of point-of-care (PoC) 3D printing centers. These centers could enable hospitals to produce necessary medical devices on-site, improving efficiency and patient outcomes. The FDA is already considering specific guidelines for PoC 3D printing, indicating a growing recognition of its importance in healthcare.
Innovations on the Horizon
The future of 3D printing in medicine promises exciting innovations. Researchers are exploring new materials and techniques to enhance the functionality and durability of implants. For instance, advancements in biocompatible materials could lead to implants that better integrate with the human body, reducing the risk of rejection or complications.
Scientific Research Findings:
- Advancements in 3D Printing Technology in Dentistry and Surgery: The technology has revolutionized these fields by allowing for the creation of patient-specific implants and surgical instruments. This progress hints at the possibility of even more sophisticated applications, such as bio-printing tissues or organs.
Another promising area of innovation is the development of highly accurate anatomical models. These models can aid in surgical planning and education, providing surgeons with a detailed understanding of a patient’s unique anatomy. The production of complex implants through 3D printing has already led to improved patient outcomes, and continued advancements could further enhance these results.
Addressing Safety and Regulatory Concerns
Ensuring Implant Safety
Ensuring the safety of 3D printed titanium sternum implants remains a top priority in medical applications. Manufacturers must adhere to stringent safety protocols to guarantee that these implants meet the highest standards. They conduct rigorous testing to assess the mechanical properties and biocompatibility of the titanium used. This testing ensures that the implants can withstand the physical demands of the human body without causing adverse reactions.
Medical professionals also play a crucial role in ensuring implant safety. Surgeons use detailed CT scans to create precise digital models of the patient’s anatomy. This precision allows for the creation of implants that fit perfectly, reducing the risk of complications during surgery. By minimizing the time spent adjusting the implant, surgeons can enhance the overall success of the procedure.
Navigating Regulatory Approvals
Navigating the regulatory landscape for 3D printed medical devices involves understanding the guidelines set by authorities like the FDA. The FDA classifies 3D printed medical devices based on their risk level and intended use. This classification determines the regulatory controls necessary to ensure the safety and effectiveness of the devices.
Manufacturers must comply with these regulatory guidelines to bring their products to market. They must demonstrate that their 3D printed implants meet the required safety and performance standards. This process often involves providing detailed documentation and evidence of the implant’s safety and efficacy.
The FDA also provides guidance on technical considerations specific to devices using additive manufacturing, including 3D printing. This guidance helps manufacturers understand the unique challenges and requirements associated with 3D printed medical devices. By following these guidelines, manufacturers can ensure that their products meet the necessary regulatory standards and provide safe and effective solutions for patients.
In conclusion, addressing safety and regulatory concerns is essential for the successful implementation of 3D printed titanium sternum implants. By adhering to strict safety protocols and navigating the regulatory landscape, manufacturers and medical professionals can ensure that these life-saving innovations continue to improve patient outcomes.
3D printed titanium sternum implants offer significant benefits in medical technology. They provide customized solutions that enhance patient outcomes and reduce complications. This innovation represents a leap forward in personalized medicine, ensuring implants fit precisely and function effectively. The potential for continued advancements in this field remains vast. Researchers and medical professionals must pursue ongoing research and development to unlock new possibilities. As technology evolves, it promises to further improve patient care and expand applications. Encouraging innovation while maintaining safety standards will ensure these life-saving solutions continue to benefit patients worldwide.