Overview
3D printing technology has advanced, leading to the emergence of printing technologies on various materials. Due to its high strength, lightweight, resistance to corrosion, and non-oxidation properties, titanium alloy is one of the materials that is widely utilized in aviation, medical, automotive, and other areas. However, there are a lot of drawbacks to standard processing methods, including processing complex forms is difficult and there is a lot of waste (since titanium alloy ingredients are quite expensive). But titanium alloy-based 3D printing technology has surfaced, and it can effectively address these issues and increase the usage of titanium alloy. The present discourse aims to provide an overview of the current state of progress and future trends in this technology by delving deeply into the titanium alloy 3D printing method and its application research.
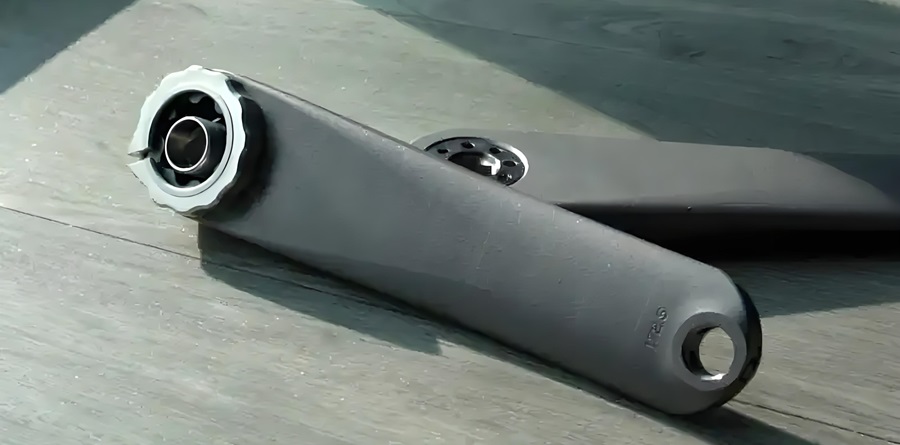
Features of alloys made of titanium
Typically, the following benefits come to mind when discussing titanium alloys:
High strength: Titanium alloys often possess 1.5 to 2 times the strength of ordinary steel.
Low weight: Titanium alloys typically weigh half as much as regular steel components.
Corrosion resistance: Titanium alloys exhibit remarkable corrosion resistance, exhibiting minimal deterioration in solutions containing ammonia and chloride.
Titanium alloys are good invisible metals because they are difficult to oxidize in the atmosphere.
Issues with the conventional titanium alloy manufacturing process
Mechanical processing, forging, or heat treatment are typically used in traditional titanium alloy processing. But these approaches have a lot of drawbacks, including the following:
Processing titanium alloys can be challenging because of their extreme hardness, which makes it challenging to form them into complex shapes. Boring, cutting, and other techniques are frequently needed.
Processing with electrochemistry is challenging: Traditional electrochemical processing procedures are challenging to execute with titanium alloys due to their high strength.
Elevated price: Titanium alloys can be quite expensive due to their scarcity and the limits of conventional processing techniques.
Titanium 3D printing process principle
Utilizing laser or electron beam welding equipment, titanium alloy powder is sprayed layer by layer onto the printing base plate in titanium 3D printing technology. At the same time, the powder layer is exposed to radiation from a laser or electron beam to melt and form the powder. This procedure is iterated until the required components are acquired. The primary processes in this technology’s process include base plate preparation, printing system setup, titanium alloy powder pretreatment, heating source setup, gas environment adjustment, and printing layer quality inspection.
In contrast to conventional processing techniques, the 3D printing process uses modeling software to automatically translate design drawings into physical models, saving a significant amount of time and effort. The following benefits of 3D printing technology are also present:
Complex manufacturing can be done: Materials can be added to, fused, and stacked to create complicated shapes using 3D printing technology.
Save materials: Waste may be prevented by carefully controlling the use of materials thanks to 3D printing technology.
Quick manufacturing speed: 3D printing is faster than traditional processing methods and can manufacture numerous items at once.
Research and development of titanium 3D printing technology
Many studies have been done by researchers in related sectors to try and tackle some of the issues that arise during the titanium 3D printing process. The primary issues consist of:
1. The burr issue
Burrs frequently arise during the 3D printing process used to generate titanium alloy parts. This adds extra surface roughness to the pieces, further impairing their accuracy and functionality. To address this issue, scientists optimize 3D printer parameters, printer head shape, and printing parameters to lower the frequency of burrs.
2. The deformation issue
Heat and stress during the production process will impact the material and cause deformation in titanium parts. Researchers investigated the mechanical and thermal characteristics of titanium alloy materials to address this issue, and they also offered several related solutions, such as the use of coolant spray during 3D printing.
3. Issue with material performance
components made of titanium alloy that are 3D printed operate very differently from components made using conventional manufacturing techniques. To address this issue, a great deal of research has been done on 3D printing materials and modeling, and these aspects have been consistently enhanced and refined. For instance, a technique based on multi-scale modeling has been proposed by worldwide academics to forecast the performance of 3D-printed titanium alloy parts.
Application research for 3D printing with titanium
The technique of 3D-printed titanium alloy has been effectively implemented in numerous industries, including shipbuilding, aircraft, automotive, and medicine. They will be introduced individually in the following.
1. The medical industry
Orthopedics and dentistry are the primary medical fields where titanium 3D printing technology is being used. Using orthopedics as an example, 3D printed technology using titanium alloy can quickly make different surgical equipment, such as screws and bone plates, based on the unique characteristics of patients, significantly increasing the surgical success rate. Furthermore, titanium alloy 3D printing technology can create a wide range of items, including prosthetic joints and formers, tailored to each patient’s specific requirements, greatly simplifying clinical treatment.
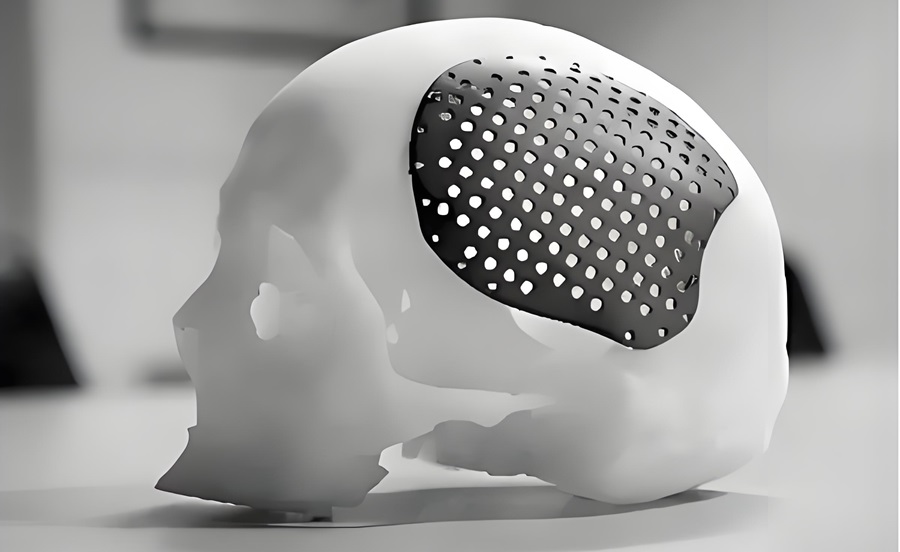
2. The aerospace industry
The aerospace industry uses titanium alloys extensively, and the titanium 3D printed process can increase the flexibility and efficiency of manufacturing a variety of complicated parts. For instance, producing intricate pieces and details is necessary for the optimum design of a jet aircraft’s engine and aerodynamic shape. These tasks are frequently challenging to do using conventional manufacturing techniques. Technology for 3D printing titanium alloys can effectively address this issue.
3. Automotive industry
The application of titanium alloy in the automotive industry is mainly to manufacture lightweight parts, thereby reducing the vehicle’s weight and improving the vehicle’s performance and fuel economy. Titanium alloy 3D printing technology is a very good way to solve the problem of automotive parts manufacturing.
4. Construction of ships
The shipbuilding industry has stricter guidelines for cost management and manufacturing processes than other industrial sectors. In addition to producing complex pieces flawlessly, titanium alloy 3D printing technology can print the entire hull in layers, resolving issues with production costs and quality control right at the source.
In brief
The future development trend of titanium alloy 3D printing technology has gradually become apparent due to its ongoing development and extensive application research. The use of 3D printing technology will grow in popularity in the future as costs are further lowered and equipment performance and quality are further improved. At the same time, 3D printing technology for titanium alloy will find more applications and turn into a vital component of the manufacturing sector.