Introduction to 3D Printed Titanium Implants
3D printing, also known as additive manufacturing, is revolutionizing the medical field by offering unprecedented customization and precision. Titanium, known for its exceptional strength, biocompatibility, and resistance to corrosion, is becoming the material of choice for medical implants. The combination of 3D printing technology and titanium material has led to the development of advanced implants that significantly enhance patient outcomes.
3D printed titanium implants provide several advantages over traditional manufacturing methods. These implants can be precisely tailored to fit individual patient anatomy, leading to better surgical outcomes. The process also allows for more complex designs that are not feasible with conventional techniques, enabling the creation of implants with improved functionality and longevity.
The Advantages of 3D Printed Titanium Implants
H3: Customization and Precision
One of the most significant advantages of 3D printed titanium implants is the ability to customize each implant to the patient’s specific needs. Traditional implants are often standardized, which can result in suboptimal fit and performance. With 3D printing, medical professionals can use patient-specific data, such as CT scans or MRI images, to create implants that perfectly match the patient’s anatomy. This customization leads to enhanced surgical outcomes, faster recovery times, and improved overall patient satisfaction.
The precision of 3D printing also allows for the creation of intricate geometries that are not possible with traditional manufacturing methods. For example, porous structures can be designed to mimic natural bone, promoting better integration with the patient’s tissue and reducing the risk of implant rejection.
Biocompatibility and Durability
Titanium is renowned for its biocompatibility, meaning it is well-tolerated by the human body and does not cause adverse reactions. This makes it an ideal material for implants that need to integrate seamlessly with the patient’s bone and tissue. Moreover, titanium’s high strength-to-weight ratio ensures that the implants are both strong and lightweight, contributing to patient comfort and mobility.
The durability of titanium means that implants can withstand the stresses and strains of daily activities, providing long-term reliability. This longevity is particularly important for patients undergoing procedures such as joint replacements, where the implants need to function effectively for many years.
Cost and Time Efficiency
The traditional manufacturing of medical implants can be time-consuming and expensive, involving multiple steps and significant material waste. In contrast, 3D printing streamlines the production process by building the implant layer by layer, directly from a digital model. This reduces the time required to produce the implant and minimizes material waste, potentially leading to cost savings.
Additionally, the rapid prototyping capability of 3D printing allows for faster iteration and refinement of implant designs. Surgeons can quickly test and adjust prototypes, ensuring the final product meets the patient’s needs precisely.
Applications of 3D Printed Titanium Implants
Orthopedic Implants
Orthopedic surgery has greatly benefited from the adoption of 3D printed titanium implants. These implants are used in various procedures, including hip and knee replacements, spinal surgeries, and bone fracture repairs. The ability to customize implants to the patient’s specific anatomy leads to better fit and function, reducing the risk of complications and improving patient outcomes.
Case studies have shown that patients with 3D printed orthopedic implants experience faster recovery times and increased mobility compared to those with traditional implants. The use of porous titanium structures also promotes better bone ingrowth, further enhancing the stability and longevity of the implants.
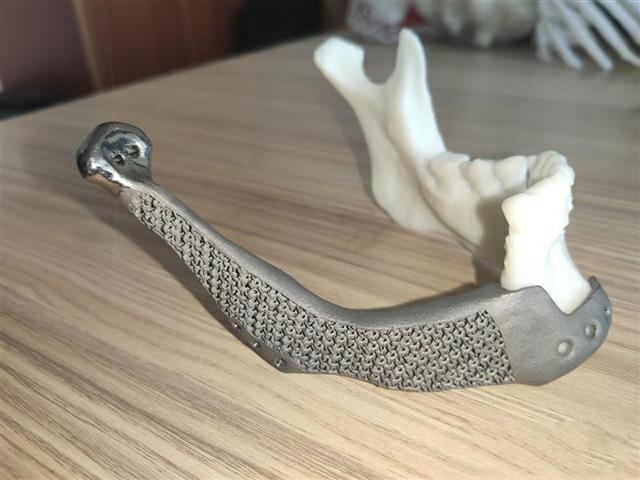
Dental Implants
In dentistry, 3D printed titanium implants are used for tooth replacement and jaw reconstruction. The precision of 3D printing allows for the creation of implants that perfectly match the patient’s dental structure, ensuring a natural look and feel. Custom dental implants provide a more comfortable fit, reducing the risk of implant failure and improving overall patient satisfaction.
Moreover, the use of 3D printed guides and models during dental surgery enhances the accuracy of implant placement, leading to better outcomes. Patients benefit from shorter surgery times, less discomfort, and faster healing.
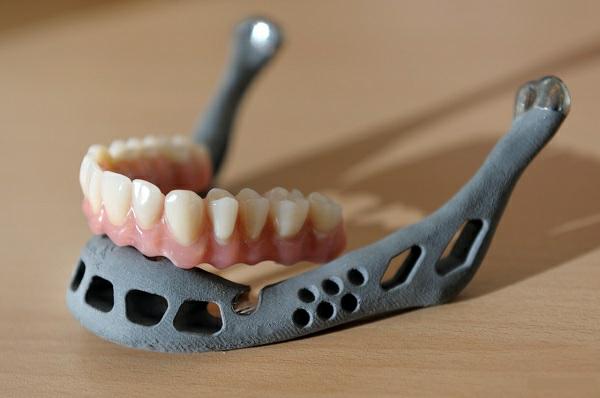
Craniofacial Implants
Craniofacial surgery, which involves the reconstruction of the skull and facial bones, has seen significant advancements with 3D printed titanium implants. These implants are used in procedures to repair congenital deformities, traumatic injuries, and tumor resections. The ability to customize implants to the patient’s unique anatomy is particularly crucial in craniofacial surgery, where precise fit and aesthetic considerations are paramount.
Examples of successful craniofacial surgeries with 3D printed implants demonstrate the life-changing impact of this technology. Patients not only benefit from improved functionality but also from enhanced appearance, contributing to their overall quality of life.

Challenges and Future Directions
Regulatory and Quality Control
Ensuring the safety and effectiveness of 3D printed titanium implants requires strict adherence to regulatory standards and rigorous quality control measures. Regulatory bodies such as the FDA in the United States and the European Medicines Agency (EMA) in Europe have established guidelines for the approval and monitoring of these implants. Manufacturers must demonstrate that their products meet stringent safety, efficacy, and quality requirements.
Current regulatory frameworks are evolving to keep pace with the rapid advancements in 3D printing technology. Ongoing collaboration between regulators, manufacturers, and healthcare providers is essential to ensure that patients receive safe and effective implants.
Technological Advancements
The field of 3D printing is continuously advancing, with ongoing research focused on improving the technology and materials used in implant production. Innovations such as multi-material printing, bioactive coatings, and advanced simulation techniques hold promise for further enhancing the performance of 3D printed titanium implants.
Researchers are also exploring the use of 3D bioprinting to create implants with living cells, potentially enabling the regeneration of damaged tissues and organs. These advancements could revolutionize the field of regenerative medicine and open new possibilities for patient care.
Market Growth and Adoption
The adoption of 3D printed titanium implants is steadily increasing as healthcare providers recognize their benefits. Market trends indicate growing demand for customized, high-performance implants, driven by an aging population and the rise in chronic conditions requiring surgical intervention.
The future market outlook for 3D printed titanium implants is promising, with significant opportunities for growth in both developed and developing regions. As technology continues to advance and regulatory frameworks evolve, the accessibility and affordability of these implants are expected to improve, further driving their adoption.
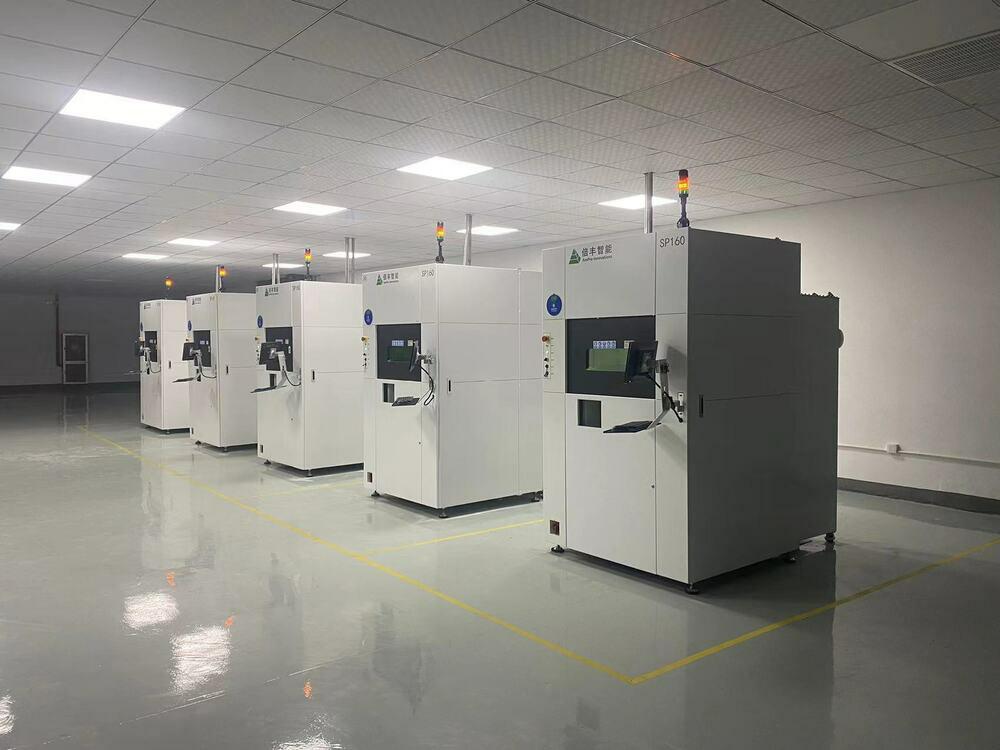
Conclusion
3D printed titanium implants represent a significant advancement in medical technology, offering unparalleled customization, precision, and biocompatibility. These implants have the potential to transform patient care across various medical fields, including orthopedics, dentistry, and craniofacial surgery.
While challenges such as regulatory compliance and technological advancements remain, the future of 3D printed titanium implants is bright. Ongoing research and collaboration will continue to drive innovation, ensuring that patients benefit from safer, more effective, and more personalized medical treatments.
Companies that can produce 3D printed titanium implants:
JHMIM 3D printed:https://titanium-supplier.com/titanium-3d-printing/
Introduction:JHMIM is a leading high-tech enterprise with a complete titanium alloy product processing plant in China. It uses advanced 3D printing technology to customize the production of titanium implants that meet customer specific needs. These implants have excellent biocompatibility and durability, which can effectively improve the healing speed and success rate of patients. JHMIM is committed to providing high-quality, customized medical solutions for the medical industry.
Tangible Solutions:https://tangiblesolutions3d.com/
Introduction: Tangible Solutions is a contract manufacturer based in Fairburn, Ohio, specializing in the production of 3D printed titanium orthopedic implants. Their manufacturing process includes discovery, prototyping, verification and validation, and alpha release.
Eplus3D:https://www.eplus3d.com/
Introduction: Eplus3D specializes in metal 3D printing technology, especially in the application of titanium alloys in the medical implant industry. Their technology can customize patient-specific implants, improving healing time and success rate.
DePuy Synthes (J&J MedTech):https://www.jnjmedtech.com/en-US/companies/depuy-synthes
Introduction: DePuy Synthes provides TRUMATCH® CMF titanium 3D printing equipment, mainly for orthognathic surgery and other medical applications, combined with virtual surgical planning.
Anatomics:https://www.anatomics.com/
About: Anatomics has partnered with Australia’s Commonwealth Scientific and Industrial Research Organisation (CSIRO) to develop the world’s first 3D printed titanium sternum and rib implants for patients with rare cancers.
Axial3D:https://axial3d.com/
About: Axial3D is a software company that simplifies the process from patient scan data to patient-specific 3D models, addressing the need for custom 3D printed implants.
The companies have significant expertise and technology in the field of 3D printed titanium implants, enabling them to deliver high-quality, customized medical solutions.