The medical industry is continuously evolving, and recent advances in 3D printing technology have ushered in a new era of innovation, especially in the use of titanium alloys. Here’s a look at how titanium is revolutionizing medical device manufacturing through 3D printing:
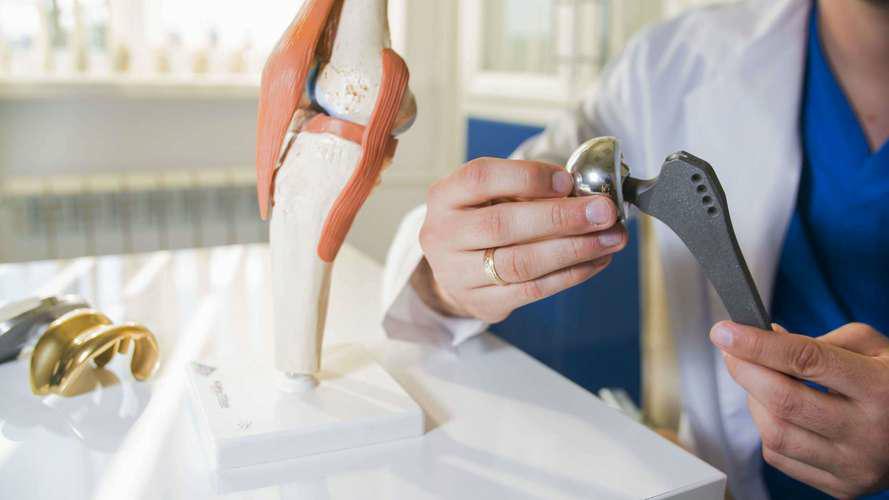
Enhanced Customization
3D printing, or additive manufacturing, allows for high precision in creating complex shapes and structures that are otherwise challenging to achieve with traditional methods. This is particularly beneficial in the medical field for the production of custom-made implants and prosthetics. Titanium is favored for these applications due to its biocompatibility, strength, and lightweight properties, ensuring that devices are comfortable and safe for long-term use.
Rapid Prototyping
Titanium’s compatibility with 3D printing technologies enables rapid prototyping, allowing designers and engineers to iterate and refine medical devices quickly. This agility speeds up the development process and helps in bringing critical medical products to market faster, a crucial factor in emergency medical scenarios or when bespoke solutions are needed urgently.
Cost-Effectiveness
While titanium materials are generally more expensive, the use of 3D printing helps in reducing waste. Traditional subtractive manufacturing methods typically produce a significant amount of scrap titanium, which is costly. 3D printing minimizes this waste by using only the material that is needed, which can significantly lower production costs in the long run.
Improved Implant Integration
One of the groundbreaking advancements in titanium 3D printing is the ability to create porous surfaces that facilitate better integration with human bone. Unlike traditional implants, which may require surface treatments to enhance bone integration, 3D-printed titanium implants can be designed with these features inherently. This not only speeds up the healing process but also improves the longevity and stability of the implant.
Strength and Durability
Titanium’s high strength-to-weight ratio makes it an excellent choice for many medical applications, from surgical instruments to orthopedic bone screws and joint replacements. 3D printing can further enhance these properties by optimizing the geometric design of the parts, which can lead to even better performance and durability.
Future Prospects
The future of 3D printing in the medical field looks promising, with ongoing research focused on improving the techniques and expanding the range of applications. Innovations such as multi-material printing, where titanium can be combined with other materials in a single print run, are on the horizon. This could lead to even more sophisticated medical devices that are custom-tailored to individual patients’ needs.
Conclusion
The synergy between titanium and 3D printing technology holds significant potential for the medical industry, offering a combination of customization, efficiency, and enhanced performance. As these technologies continue to develop, they are set to transform the landscape of medical manufacturing, leading to better patient outcomes and more effective treatments.