When comparing materials, I find that carbon fiber stands out for its lightweight properties. Its density of 1.6 g/cm³ makes it 2.8 times lighter than titanium, which has a density of 4.5 g/cm³. This leads to the question: is titanium lighter than carbon fiber? The answer is no, as shown in the quick comparison below:
Material | Density (g/cm³) | Comparison |
---|---|---|
Carbon Fiber | 1.6 | 2.8 times lighter |
Titanium | 4.5 | Heavier |
This weight advantage makes carbon fiber ideal for applications where reducing weight is critical, such as aerospace and automotive industries.
Key Takeaways
- Carbon fiber is much lighter than titanium. Its density is 1.6 g/cm³, while titanium’s is 4.5 g/cm³. This makes carbon fiber great for reducing weight in designs.
- Titanium is very strong and resists rust well. It works well in tough environments like airplanes and medical tools. Its strength makes it last a long time.
- Carbon fiber costs more at first but is very strong for its weight. It is perfect for lightweight uses. Titanium is cheaper and good for projects needing strength and durability.
Weight Comparison
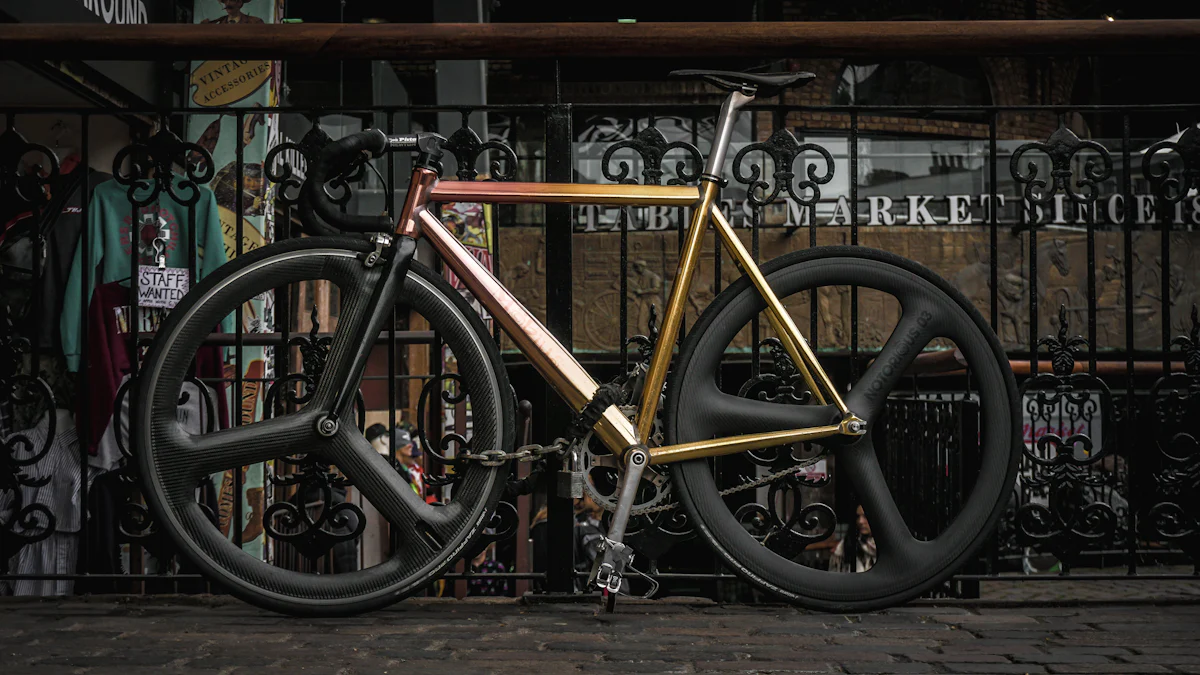
Density of Titanium vs. Carbon Fiber
When I compare the densities of titanium and carbon fiber, the difference becomes immediately clear. Titanium has a density of 4.5 g/cm³, while carbon fiber measures only 1.6 g/cm³. This means carbon fiber is approximately 2.8 times lighter than titanium. To illustrate this contrast, I’ve summarized the data in the table below:
Material | Density (g/cm³) | Comparison |
---|---|---|
Carbon Fiber | 1.6 | 2.8 times lighter |
Titanium | 4.5 | Heavier |
The significant disparity in density explains why carbon fiber is often the preferred choice for applications where weight reduction is critical. Titanium, while heavier, offers other advantages that I’ll explore later in the blog.
Why Carbon Fiber is Lighter
The lightweight nature of carbon fiber stems from its unique composition and structure. Carbon fiber consists of thin strands of carbon atoms bonded together in a crystalline formation. This structure provides exceptional strength while maintaining a low density. In contrast, titanium’s higher density results from its atomic structure and the complex manufacturing process required to produce it. Titanium is extracted from minerals like rutile and ilmenite, then processed through chemical treatments and reduction reactions. These steps contribute to its heavier weight.
For applications where weight is a priority, carbon fiber’s lower density makes it the superior option. Whether in aerospace, automotive, or sports equipment, I’ve found that carbon fiber consistently outperforms titanium in weight-sensitive scenarios. This is why the answer to the question “is titanium lighter than carbon fiber” is a definitive no.
Strength-to-Weight Ratio
Performance of Titanium
Titanium offers an impressive strength-to-weight ratio, making it a standout material in high-stress environments. Its alloys can achieve yield strengths of up to 1,400 MPa, which allows components to handle significant loads without adding excessive weight. This property is why titanium is widely used in industries like aerospace and automotive. For example, aircraft frames, jet engines, and landing gear benefit from titanium’s ability to reduce weight while maintaining structural integrity. In the automotive sector, high-performance vehicles use titanium for exhaust systems and suspension components to enhance fuel efficiency and performance.
Titanium also excels in durability. It resists corrosion, even in harsh environments like marine or chemical processing applications. Its thermal stability ensures that it retains strength at temperatures as high as 600°C, making it suitable for jet engines and other high-performance settings. These characteristics highlight titanium’s versatility, especially in applications where both strength and weight are critical.
Characteristic | Technical Parameters | Justification |
---|---|---|
Strength-to-Weight Ratio | Up to 1,400 MPa for yield strength | Enables lightweight components that withstand heavy loads. |
Corrosion Resistance | Resistance to oxidation and pitting | Ideal for long-term use in marine and chemical environments. |
Thermal Stability | Maintains strength up to 600°C | Suitable for high-temperature applications like jet engines. |
Impact Resistance | High impact toughness values | Prevents cracking, essential for protective equipment and high-stress scenarios. |
Performance of Carbon Fiber
Carbon fiber surpasses titanium in strength-to-weight ratio, making it a preferred choice for weight-sensitive applications. It is approximately 2.8 times lighter than titanium, yet it can achieve tensile strengths of up to 6,000 MPa. This combination of lightweight and exceptional strength is why carbon fiber dominates industries like aerospace and automotive. For instance, aircraft components and high-performance car parts rely on carbon fiber to reduce weight while maintaining structural rigidity.
The material’s stiffness further enhances its performance. Its high modulus of elasticity ensures rigidity, which is crucial for applications like bicycle frames and wind turbine blades. Additionally, carbon fiber resists corrosion and maintains its integrity across a wide temperature range. These properties make it suitable for outdoor and marine environments, as well as high-temperature applications like exhaust systems.
Property | Description |
---|---|
High Strength-to-Weight Ratio | Stronger than steel, yet lighter than aluminum, ideal for aerospace and automotive. |
Stiffness | High rigidity, perfect for applications requiring structural stability. |
Corrosion Resistance | Does not rust or corrode, suitable for harsh environments. |
Thermal Stability | Performs well across a wide temperature range. |
Fatigue Resistance | Durable under repeated stress, ensuring reliability in demanding industries. |
When comparing the two materials, carbon fiber’s superior strength-to-weight ratio makes it the better option for lightweight applications. However, titanium’s unique properties, such as its biocompatibility and thermal stability, make it indispensable in specific scenarios. This balance of strengths explains why the question “is titanium lighter than carbon fiber” often arises in material selection discussions.
Durability and Longevity
Wear and Tear Resistance
When I evaluate the durability of titanium and carbon fiber, both materials demonstrate exceptional resistance to wear and fatigue. Carbon fiber excels in handling repeated stress, making it ideal for applications like aerospace and automotive components. Its lightweight structure ensures minimal strain on connected parts, reducing the risk of mechanical failure over time. However, carbon fiber can be prone to surface scratches, which may compromise its appearance and, in some cases, its structural integrity.
Titanium, on the other hand, offers superior resistance to wear and tear. Its robust nature allows it to withstand significant impacts without cracking or breaking. This makes it a preferred choice for high-stress environments, such as medical implants and industrial machinery. Unlike carbon fiber, titanium can endure surface damage, as scratches can be polished out to restore its finish. I find this feature particularly valuable for long-term use in demanding conditions.
Material | Durability | Maintenance Requirements |
---|---|---|
Carbon Fiber | Excellent resistance to wear and fatigue | Regular cleaning with mild detergent; avoid harsh chemicals |
Titanium | Resistant to wear, corrosion, and fatigue | Minimal maintenance; polish scratches to prevent damage |
Environmental Factors and Corrosion
Environmental conditions significantly impact the longevity of both materials. Carbon fiber resists corrosion effectively, making it suitable for outdoor and marine applications. However, prolonged exposure to UV light can degrade its surface, leading to discoloration and reduced strength. To mitigate this, I recommend keeping carbon fiber components out of direct sunlight and applying protective coatings when necessary.
Titanium stands out for its remarkable resistance to corrosion. It remains unaffected by moisture, saltwater, and most chemicals, making it ideal for marine and chemical processing environments. Additionally, titanium retains its strength and integrity under extreme temperatures, which is why it is widely used in jet engines and space exploration. While titanium requires minimal maintenance, I suggest cleaning it with mild detergent and water to preserve its appearance and functionality.
Material | Maintenance Requirements |
---|---|
Carbon Fiber | Regular cleaning with mild detergent and water; avoid harsh chemicals; keep out of direct sunlight and extreme temperatures. |
Titanium | Minimal maintenance; polish scratches; clean with mild detergent and warm water; avoid chlorine and harsh chemicals. |
Both materials offer impressive durability, but their performance varies depending on environmental factors. Carbon fiber thrives in controlled conditions, while titanium excels in harsh and unpredictable environments. This distinction highlights the importance of selecting the right material based on specific application needs.
Cost Comparison
Initial Costs
When I compare the initial costs of titanium and carbon fiber, the price difference becomes evident. Carbon fiber is significantly more expensive due to its labor-intensive manufacturing process and the high cost of raw materials. On average, carbon fiber costs between 60and60 and 60and120 per kilogram, while titanium (Grade 5) ranges from 30to30 to 30to50 per kilogram. This disparity makes titanium the more affordable option for many industries.
Material | Cost (USD per kg) | Comparison |
---|---|---|
Carbon Fiber | 60–60 – 60–120 | Much higher cost |
Titanium (Grade 5) | 30–30 – 30–50 | Lower cost compared to carbon fiber |
Additionally, the price per pound further highlights this difference. Carbon fiber costs between 10and10 and 10and30 per pound, whereas titanium ranges from 5to5 to 5to20 per pound. These figures demonstrate that titanium offers a cost advantage during the initial stages of production, especially for large-scale projects.
- Carbon Fiber: Costs 60–60–60–120 per kg due to expensive raw materials and labor-intensive processes.
- Titanium (Grade 5): Costs 30–30–30–50 per kg, making it less expensive than carbon fiber.
For budget-conscious applications, titanium provides a more economical solution without compromising on performance.
Long-Term Value
While carbon fiber has a higher upfront cost, its long-term value depends on the application. Titanium stands out for its durability and minimal maintenance requirements. It resists wear, corrosion, and fatigue, making it ideal for environments where longevity is critical. Maintenance involves occasional polishing to remove scratches, which ensures titanium retains its functionality and appearance over time.
Carbon Fiber | Titanium | |
---|---|---|
Durability | Excellent resistance to wear and fatigue | Resistant to wear, corrosion, and fatigue |
Maintenance | Regular cleaning; avoid harsh conditions | Minimal upkeep; polish scratches |
Carbon fiber, on the other hand, requires more care. It resists corrosion effectively but is prone to surface scratches and UV degradation. Regular cleaning and protective coatings are necessary to maintain its integrity. Despite these challenges, carbon fiber excels in weight-sensitive applications, offering unmatched strength-to-weight performance.
In my experience, titanium offers better long-term value for projects requiring durability and low maintenance. However, carbon fiber remains the superior choice for applications prioritizing lightweight properties. The decision ultimately depends on the specific needs of the project.
Applications of Titanium and Carbon Fiber
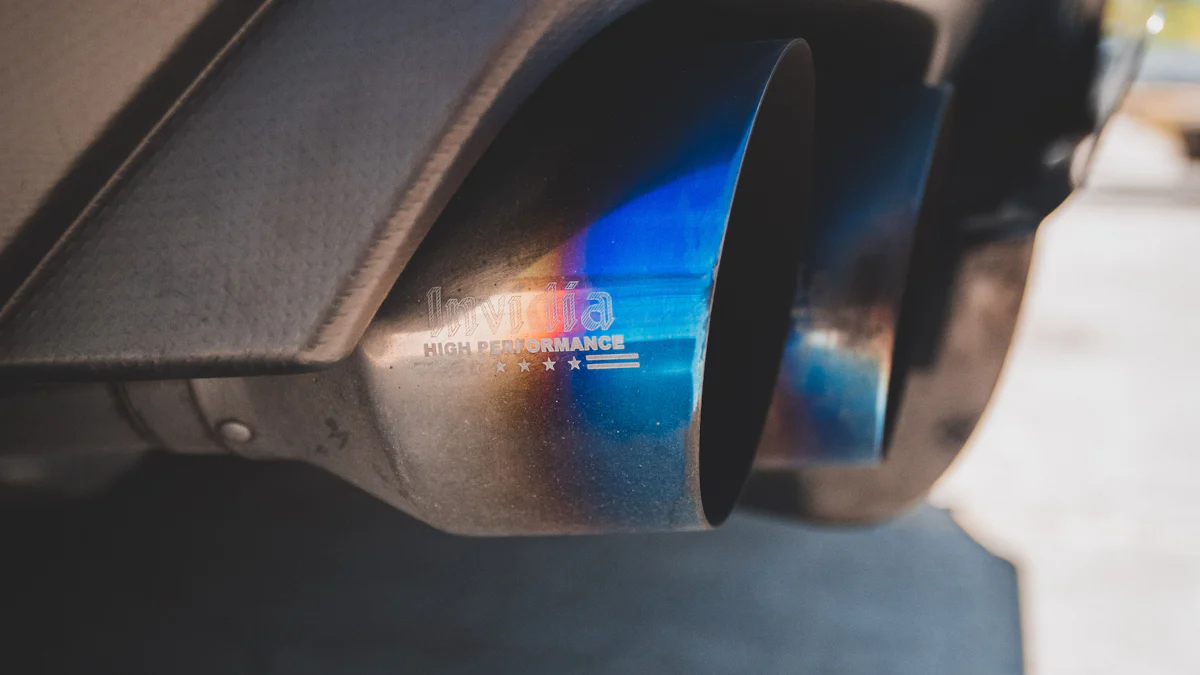
Aerospace and Automotive
Titanium and carbon fiber play crucial roles in aerospace and automotive industries due to their unique properties. In aerospace, carbon fiber is widely used for components like aircraft fuselage and engine parts. Its high strength-to-weight ratio improves fuel efficiency and performance. Titanium, on the other hand, is essential for high-temperature and corrosion-resistant applications. I’ve seen it used in landing gear and turbine engine blades, where durability is critical.
In the automotive sector, carbon fiber enhances the performance of sports cars by reducing weight while maintaining strength. It also adds a sleek, modern aesthetic to vehicle designs. Titanium finds its place in exhaust systems and internal components, offering lightness and resistance to high temperatures. These materials, when combined, create advanced alloys for chassis and body structures, further improving stiffness and reducing weight.
Sports Equipment
The sports industry benefits significantly from titanium and carbon fiber. Carbon fiber is a favorite for bicycle frames, tennis rackets, and hockey sticks. Its lightweight nature and high strength-to-weight ratio allow athletes to perform better with less fatigue. For example, carbon fiber rods in tennis rackets enable faster swing speeds and more powerful strokes.
Titanium is often used in golf clubs and bicycle parts. Its lightness and durability make it ideal for high-performance equipment. Racing bicycles, for instance, incorporate both materials to achieve a balance of strength and weight, enhancing speed and maneuverability. These advancements have revolutionized sports equipment design, providing athletes with tools that maximize their potential.
Medical Devices
In the medical field, titanium and carbon fiber offer distinct advantages. Titanium is a go-to material for orthopedic implants, pacemakers, and dental implants. Its exceptional corrosion resistance and biocompatibility ensure long-term reliability inside the human body. Carbon fiber, however, excels in external support devices like prosthetics and braces. Its high strength-to-weight ratio and design flexibility make it ideal for creating lightweight yet durable medical aids.
For example, carbon fiber prosthetics are easier to maneuver and reduce strain on the user. Titanium implants, on the other hand, provide unmatched durability and resistance to wear. These materials have transformed medical device design, improving patient outcomes and quality of life.
Carbon fiber, with its density of 1.6 g/cm³, is significantly lighter than titanium’s 4.5 g/cm³. Its superior strength-to-weight ratio makes it ideal for aerospace and automotive applications. Titanium, however, excels in durability, resisting corrosion and extreme conditions. Choosing between them depends on priorities like weight, cost, and durability, as shown below:
Material | Specific Weight (g/cm³) | Average Price ($/lb) | Key Strengths |
---|---|---|---|
Carbon Fiber | 1.6 | 10–10–10–30 | Lightweight, high strength-to-weight |
Titanium | 4.5 | 5–5–5–20 | Durable, corrosion-resistant |
Both materials offer unique advantages, ensuring their relevance across industries.
FAQ
What makes carbon fiber lighter than titanium?
Carbon fiber’s crystalline structure and low-density composition make it lighter. Titanium’s higher atomic mass and denser structure contribute to its heavier weight.
Can titanium replace carbon fiber in all applications?
No, titanium cannot replace carbon fiber in weight-sensitive applications. Carbon fiber’s superior strength-to-weight ratio makes it indispensable for aerospace, automotive, and sports equipment.
Why is titanium more durable than carbon fiber?
Titanium resists corrosion, wear, and extreme temperatures better than carbon fiber. Its robust nature ensures long-term performance in harsh environments, unlike carbon fiber’s susceptibility to surface damage.