Are you seeking cutting-edge materials that redefine strength and durability? Imagine a world where the limitations of traditional manufacturing are shattered, where the strength of materials is no longer bound by conventional methods. Enter the realm of 3D-printed titanium, a technological marvel that is revolutionizing industries across the globe. But the burning question remains: Is 3D-printed titanium strong enough to meet the rigorous demands of modern applications?
The answer is a resounding yes. 3D-printed titanium has proven to be extraordinarily strong, with recent advancements significantly enhancing its strength capabilities. Engineers at Monash University have developed a new titanium alloy that boasts an impressive strength-to-weight ratio, achieving elongation and tensile strengths exceeding 1,600 MPa. This is a notable leap from most commercial titanium alloys, which typically max out around 1,000 MPa. Similarly, an international research team has created a 3D-printed titanium alloy with an ultimate tensile strength of over 1,600 MPa using laser-powder bed fusion and subsequent heat treatment. This process not only maintains but often surpasses the strength of traditionally manufactured titanium. Moreover, RMIT University researchers have developed a 3D-printed titanium lattice structure that is 50% stronger than the strongest cast magnesium alloy, WE54, used in aerospace applications. These advancements highlight that 3D-printed titanium can match or even exceed the strength of traditional titanium alloys, making it a game-changer for various high-demand industries.

So, how does the strength of 3D-printed titanium compare to its traditionally manufactured counterpart? The evidence suggests that 3D-printed titanium not only matches but in some cases surpasses the strength of conventional titanium alloys. The new titanium alloy from Monash University, for instance, exhibits strengths exceeding 1,600 MPa, far above the typical 1,000 MPa seen in commercial alloys. Additionally, the ability to create complex geometries through 3D printing allows for optimized designs that enhance strength-to-weight ratios. While some traditionally manufactured titanium alloys can reach ultimate tensile strengths around 2,000 MPa, the rapid advancements in 3D printing technology are closing the gap quickly. Studies have shown that 3D-printed metals can be significantly stronger than those produced by traditional methods, with 3D-printed stainless steel parts being 2 to 3 times stronger than their conventionally manufactured counterparts. This ability to combine high strength with design flexibility positions 3D-printed titanium as a superior choice for many applications.
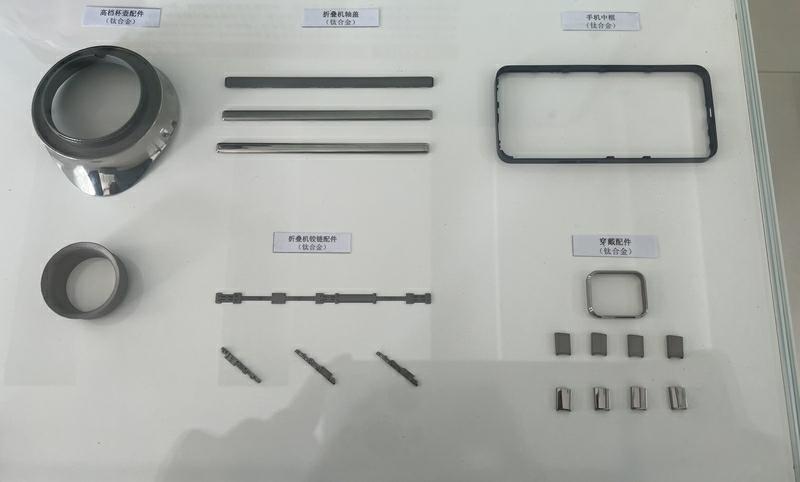
The durability of 3D-printed titanium alloys is also notably enhanced through the 3D printing process. This method can result in a unique microstructure with improved mechanical properties, thanks to the rapid cooling rates associated with processes like Selective Laser Melting (SLM). This leads to finer grain structures, contributing to the overall strength and durability. Advanced 3D printing techniques can achieve high relative density, crucial for durability, and allow for controlled porosity, beneficial for applications such as medical implants. Design optimization through 3D printing also enables the creation of complex geometries that further enhance durability. For instance, lattice structures can be integrated to improve strength-to-weight ratios. Post-processing treatments, such as heat treatment at 480°C, can significantly enhance the mechanical properties of 3D-printed titanium alloys. While challenges such as surface roughness and potential defects need to be managed, the overall potential for increased durability is substantial.
Industries poised to benefit from 3D-printed titanium are numerous. The aerospace industry, for example, can leverage titanium’s high strength-to-weight ratio to produce aircraft components that are both strong and lightweight, optimizing fuel efficiency and performance. The medical field is utilizing 3D-printed titanium for customized implants and prosthetics, taking advantage of its biocompatibility and the ability to tailor designs to individual patients. In the automotive sector, 3D-printed titanium parts can enhance vehicle performance and safety while reducing weight. Defense and high-performance products, including those for space exploration, also benefit from titanium’s excellent strength and corrosion resistance. Even in prototyping and tooling, 3D-printed titanium offers rapid production of complex designs, accelerating development cycles and reducing costs.
In conclusion, 3D-printed titanium not only matches but often exceeds the strength of traditionally manufactured titanium alloys. Its ability to create complex, optimized designs while maintaining superior strength and durability makes it an invaluable material for a wide range of industries. From aerospace to medical applications, 3D-printed titanium is proving to be a transformative technology, pushing the boundaries of what is possible in material science and engineering. As advancements continue, the potential for 3D-printed titanium will only grow, offering innovative solutions to meet the demands of the future.