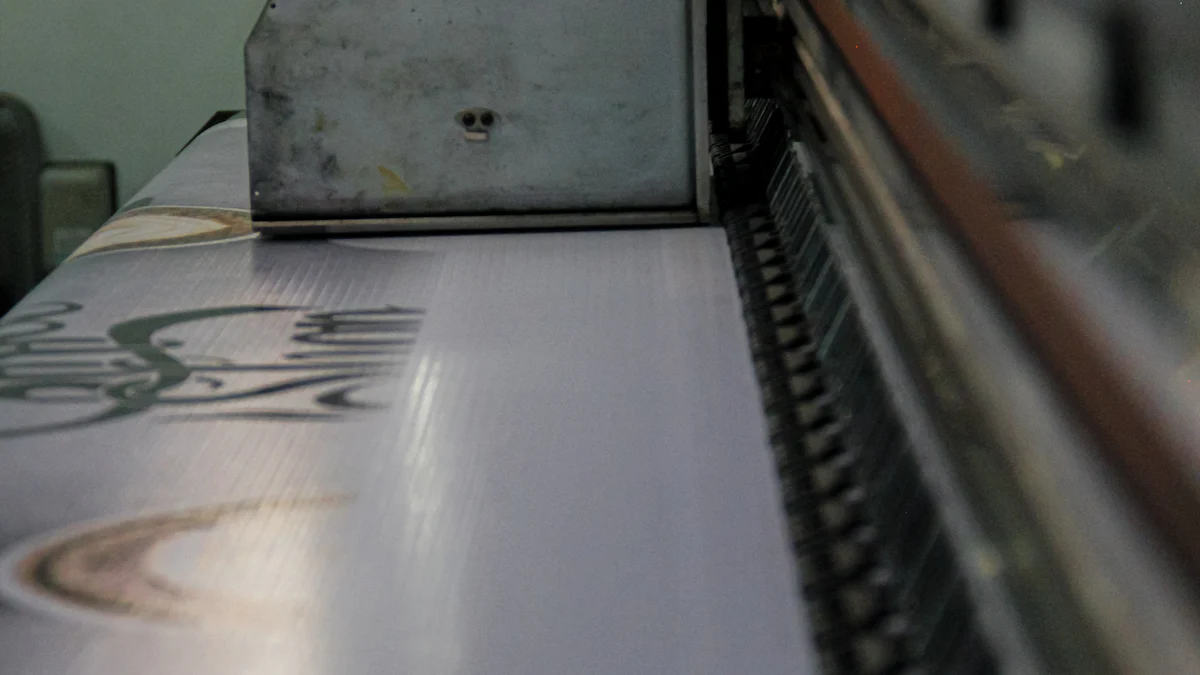
You play a crucial role in achieving 3D printing success by focusing on the importance of titanium powder quality in 3D printing. Titanium powder offers unique properties that make it ideal for creating complex and durable components. Manufacturers tailor these powders for 3D printing, ensuring uniform particle size and shape. This optimization enhances flowability and packing density in the print bed. By understanding and optimizing these factors, you can significantly improve the efficiency and quality of your 3D printing projects, making them more cost-effective in the long run.
Understanding Titanium Powder Properties
Composition and Particle Size
When you work with titanium powder for 3D printing, understanding its composition and particle size becomes crucial. Titanium powder typically consists of titanium alloys, such as Ti6Al4V (Grade 5) and Ti6Al4V ELI (Extra-Low Interstitial). These alloys offer unique properties that make them suitable for various applications. The composition of these powders ensures that they provide the strength and versatility needed for high-performance parts.
Particle size plays a significant role in the success of your 3D printing projects. Manufacturers engineer titanium powders to have uniform particle size and shape. This uniformity improves flowability and packing density in the print bed. When particles are consistent in size, they spread evenly, reducing the risk of defects in the final product. By focusing on these aspects, you can achieve optimal print results and enhance the quality of your 3D printed components.
Mechanical and Thermal Properties
Titanium powder’s mechanical and thermal properties make it an excellent choice for 3D printing. You benefit from its unparalleled strength and lightweight nature, which are essential for creating durable and complex parts. Titanium’s strength-to-weight ratio is one of the highest among metals, making it ideal for industries like aerospace and automotive, where weight reduction is critical.
In addition to its mechanical properties, titanium powder offers excellent thermal properties. It can withstand high temperatures without losing its structural integrity. This characteristic is particularly valuable in applications where components are exposed to extreme heat, such as in aircraft engines or medical implants. By leveraging these properties, you can produce parts that meet the demanding requirements of advanced applications.
Understanding these properties allows you to optimize the use of titanium powder in your 3D printing projects. By selecting the right composition and ensuring uniform particle size, you can achieve superior print quality and performance.
The Importance of Titanium Powder Quality in 3D Printing
Impact on Print Quality
When you engage in 3D printing with titanium powder, the quality of the powder directly influences the print quality. High-quality titanium powder ensures that your printed components exhibit unparalleled strength and lightweight properties. These attributes make titanium powder a transformative material across various industries, including aerospace and medical fields.
Surface roughness and porosity can pose challenges in 3D printing. However, by optimizing printing parameters and using high-quality titanium powder, you can mitigate these issues. Consistent powder quality leads to smoother surfaces and reduces the likelihood of defects. This optimization not only enhances the aesthetic appeal of your printed parts but also improves their functional performance.
Role in Achieving Desired Mechanical Properties
The mechanical properties of your 3D printed parts depend heavily on the quality of the titanium powder used. Titanium’s high strength-to-weight ratio, along with its fatigue and fracture resistance, makes it a desirable material for 3D printing. By ensuring the powder quality, you can achieve these desirable mechanical properties in your final products.
Biocompatibility is another critical factor, especially in the medical industry. High-quality titanium powder ensures that implants and prosthetics are safe and effective for patient use. The importance of titanium powder quality in 3D printing cannot be overstated, as it plays a crucial role in meeting the stringent requirements of advanced applications.
Advantages of Using Titanium Powder in 3D Printing
Lightweight and Strong
You will find that titanium powder offers a remarkable strength-to-weight ratio, making it an ideal choice for 3D printing applications where weight reduction is crucial. This property is particularly beneficial in industries like aerospace and automotive, where every ounce counts. By using titanium powder, you can create components that are not only lightweight but also incredibly strong. This combination allows for the production of parts that maintain structural integrity while reducing overall mass.
Designers often utilize intricate lattice structures and optimize material distribution to achieve this balance. These techniques enable the creation of parts that are both lightweight and robust. The ability to produce such components with titanium powder highlights its transformative potential in 3D printing. You can leverage these properties to enhance the performance and efficiency of your projects, ensuring that your printed parts meet the demanding requirements of high-performance applications.
Corrosion Resistance
Titanium powder’s excellent corrosion resistance makes it a preferred material for 3D printing in environments where durability is essential. This property ensures that components made from titanium can withstand harsh conditions without degrading over time. Industries such as aerospace, medical, and automotive benefit significantly from this characteristic, as it enhances the longevity and reliability of their products.
By choosing titanium powder for your 3D printing projects, you can produce parts that resist corrosion and maintain their functionality in challenging environments. This resistance not only extends the lifespan of the components but also reduces maintenance costs and downtime. The importance of titanium powder quality in 3D printing becomes evident when you consider the need for durable and reliable parts in critical applications. By understanding and utilizing titanium’s corrosion-resistant properties, you can ensure that your printed components perform optimally in any setting.
Challenges in 3D Printing with Titanium Powder
Cost Considerations
When you consider using titanium powder for 3D printing, cost becomes a significant factor. Titanium powder, known for its exceptional characteristics, often costs between $300 and $600 per kilogram. This price range makes it a vital technology in industries like aerospace, medical, and automotive, where the benefits outweigh the expenses. However, the high cost can be a barrier for smaller projects or companies with limited budgets.
Despite the expense, titanium powder offers unmatched strength-to-weight ratios. This makes it preferable for weight-critical applications compared to other materials like plastics or some aluminum alloys. While titanium alloys may not match the absolute strength of high-strength steel powders, their lighter weight provides an advantage in applications where reducing mass is crucial. You must weigh these benefits against the costs to determine if titanium powder is the right choice for your project.
Handling and Safety
Handling titanium powder requires careful attention to safety protocols. The fine particles can pose inhalation risks, so you should always use appropriate personal protective equipment (PPE) such as masks and gloves. Ensuring proper ventilation in your workspace is also essential to minimize exposure to airborne particles.
In addition to health concerns, titanium powder is highly flammable. You must store it in a controlled environment to prevent accidental ignition. Avoiding static electricity and open flames in the vicinity of titanium powder is crucial for maintaining a safe workspace. By adhering to these safety measures, you can mitigate the risks associated with handling titanium powder and focus on achieving successful 3D printing outcomes.
Understanding the importance of titanium powder quality in 3D printing extends beyond just the material’s properties. It involves recognizing the challenges and implementing strategies to overcome them. By addressing cost considerations and prioritizing safety, you can optimize the use of titanium powder in your projects, ensuring both efficiency and safety.
Technologies for 3D Printing with Titanium Powder
Direct Energy Deposition (DED)
Direct Energy Deposition (DED) stands out as a versatile technology in 3D printing with titanium. You use DED to build parts by melting titanium powder with a focused energy source, such as a laser or electron beam. This process allows you to add material precisely where needed, making it ideal for repairing existing components or creating complex geometries. DED offers you the flexibility to work with various titanium alloys, enhancing the strength and durability of your printed parts. By mastering DED, you can achieve high-quality results in industries like aerospace and automotive, where precision and performance are paramount.
Electron Beam Melting (EBM)
Electron Beam Melting (EBM) provides you with a powerful method for 3D printing titanium powder. In EBM, an electron beam melts the titanium powder layer by layer, creating parts with excellent mechanical properties. This technology operates in a vacuum, reducing the risk of contamination and ensuring high purity in your printed components. EBM is particularly beneficial for producing parts with complex internal structures, such as lattice designs, which are difficult to achieve with traditional manufacturing methods. By utilizing EBM, you can produce lightweight and strong components that meet the demanding requirements of industries like medical and aerospace, highlighting the benefits of using technologies like EBM and SLM.
Selective Laser Melting (SLM)
Selective Laser Melting (SLM) offers you a precise and efficient way to 3D print with titanium powder. In SLM, a high-powered laser selectively melts the titanium powder, fusing it into solid layers. This process allows you to create intricate and detailed parts with high accuracy. SLM is well-suited for applications requiring fine resolution and complex geometries, such as custom implants and high-performance aerospace components. By leveraging SLM, you can take advantage of titanium’s unique properties, including its strength, lightweight nature, and corrosion resistance, to produce parts that excel in both form and function.
“3D printing has revolutionized manufacturing, enabling the creation of complex structures and custom designs with precision.” This quote highlights the transformative impact of technologies like DED, EBM, and SLM in the field of titanium powder 3D printing. By understanding and utilizing these technologies, you can optimize your 3D printing projects and achieve success in various high-value applications.
Practical Tips for Optimizing Titanium Powder Use
Powder Storage and Handling
Proper storage and handling of titanium powder play a crucial role in maintaining its quality for 3D printing. You should store titanium powder in a dry, cool environment to prevent moisture absorption, which can lead to clumping and affect flowability. Use airtight containers to keep the powder free from contaminants and humidity. Regularly inspect the storage area for any signs of moisture or contamination.
When handling titanium powder, prioritize safety. Wear appropriate personal protective equipment (PPE) such as masks and gloves to protect yourself from inhaling fine particles. Ensure that your workspace has adequate ventilation to minimize exposure to airborne particles. Avoid static electricity and open flames near the powder, as titanium is highly flammable. By following these guidelines, you can maintain the integrity of the powder and ensure safe handling practices.
Calibration and Maintenance of Equipment
Calibration and maintenance of your 3D printing equipment are essential for achieving optimal results with titanium powder. Regularly calibrate your printer to ensure accurate layer deposition and alignment. This step helps prevent defects and ensures that your printed parts meet the desired specifications. Check the printer’s settings and adjust them according to the specific requirements of titanium powder.
Routine maintenance of your equipment is equally important. Clean the printer’s components, such as the build platform and nozzles, to prevent powder buildup and ensure smooth operation. Inspect the equipment for any signs of wear or damage, and address any issues promptly to avoid disruptions in your printing process. By keeping your equipment in top condition, you can enhance the quality and reliability of your 3D printed components.
“Titanium powder for 3D printing is a transformative material with unparalleled strength, lightweight properties, and versatility across industries.” This statement underscores the importance of optimizing every aspect of the 3D printing process, from powder storage to equipment maintenance, to fully leverage the benefits of titanium powder in your projects.
Future Trends in Titanium Powder 3D Printing
Innovations in Powder Production
You will witness exciting innovations in titanium powder production that promise to enhance 3D printing capabilities. Manufacturers are developing improved materials and alloys to meet the growing demands of various industries. These advancements aim to provide better mechanical properties, increased durability, and enhanced performance in printed components.
Key Innovations Include:
- Advanced Alloy Development: New titanium alloys are being engineered to offer superior strength and lightweight properties. These alloys cater to specific applications, such as aerospace and medical, where performance is critical.
- Refined Powder Production Techniques: Manufacturers are refining production techniques to achieve more uniform particle sizes and shapes. This refinement improves powder flowability and packing density, leading to higher-quality prints.
- Sustainability Initiatives: Efforts are underway to make titanium powder production more sustainable. This includes reducing energy consumption and minimizing waste during the manufacturing process.
By staying informed about these innovations, you can leverage the latest advancements in titanium powder production to optimize your 3D printing projects.
Emerging Applications
The future of titanium powder 3D printing holds exciting possibilities with emerging applications across various industries. As technology advances, you will find new opportunities to utilize titanium powder in innovative ways.
Emerging Applications Include:
- Aerospace and Defense: The aerospace industry continues to explore titanium powder for lightweight and durable components. You can expect to see more aircraft parts, such as engine components and structural elements, produced using 3D printing.
- Medical Implants and Prosthetics: Customization is key in the medical field. Titanium powder enables the creation of patient-specific implants and prosthetics, improving patient outcomes and comfort.
- Automotive Industry: High-performance automotive parts benefit from titanium’s strength and lightweight properties. You will see increased use of 3D-printed titanium components in vehicles to enhance performance and fuel efficiency.
- Consumer Goods: As 3D printing becomes more accessible, consumer goods manufacturers are exploring titanium powder for producing high-quality, durable products.
“Future trends in titanium powder 3D printing include the development of improved materials and alloys, enhanced printing technologies, integration of artificial intelligence and machine learning, and large-scale industrial adoption.” This quote highlights the transformative potential of titanium powder 3D printing in various sectors. By embracing these emerging applications, you can stay ahead in the ever-evolving landscape of additive manufacturing.
You have explored the essential aspects of optimizing titanium powder for 3D printing. By focusing on powder quality, understanding its properties, and implementing practical tips, you can enhance your 3D printing projects. The field of titanium powder 3D printing is evolving rapidly. Notable trends include advancements in materials and printing technologies. As costs decrease, expect more innovative applications to emerge. Embrace these strategies and stay informed about future developments. By doing so, you position yourself for success in this transformative manufacturing landscape.