Introduction: Pain, Agitate, Solution
Have you ever felt the frustration of needing a lightweight, durable part that traditional manufacturing just can’t deliver? The aerospace and medical industries are constantly pushing the boundaries, demanding components that are not only strong and lightweight but also capable of withstanding extreme conditions. Traditional methods often fall short, leaving you with heavy, cumbersome parts that don’t meet your needs. But what if there was a way to create these intricate, high-performance components with precision and efficiency? Enter titanium 3D printing – a revolutionary solution that promises to change the game.
How to 3D Print Titanium?
3D printing titanium involves using a powder bed fusion process, typically Direct Metal Laser Sintering (DMLS) or Selective Laser Melting (SLM). Here’s a step-by-step guide to how it’s done:
- Powder Preparation: A thin layer of titanium powder, usually the Ti6Al4V alloy, is spread across the build platform. This alloy is chosen for its excellent balance of strength, weight, and corrosion resistance.
- Laser Melting: A high-powered laser beam selectively melts and fuses the powder particles together in the desired areas, forming a single layer of the 3D model. This process is incredibly precise, allowing for the creation of complex geometries.
- Layer Building: After each layer is formed, the build platform is lowered, and a new layer of powder is spread over the previous one. The laser then melts and fuses the new layer to the existing structure. This layer-by-layer approach continues until the entire 3D model is built.
- Post-Processing: Once the printing is complete, any support structures used during the build are carefully removed. The part may also undergo additional heat treatment to enhance its mechanical properties and ensure it meets the required specifications.
- Finishing Touches: Depending on the application, the printed part might require further finishing processes such as machining, polishing, or coating to achieve the desired surface quality and dimensional accuracy.
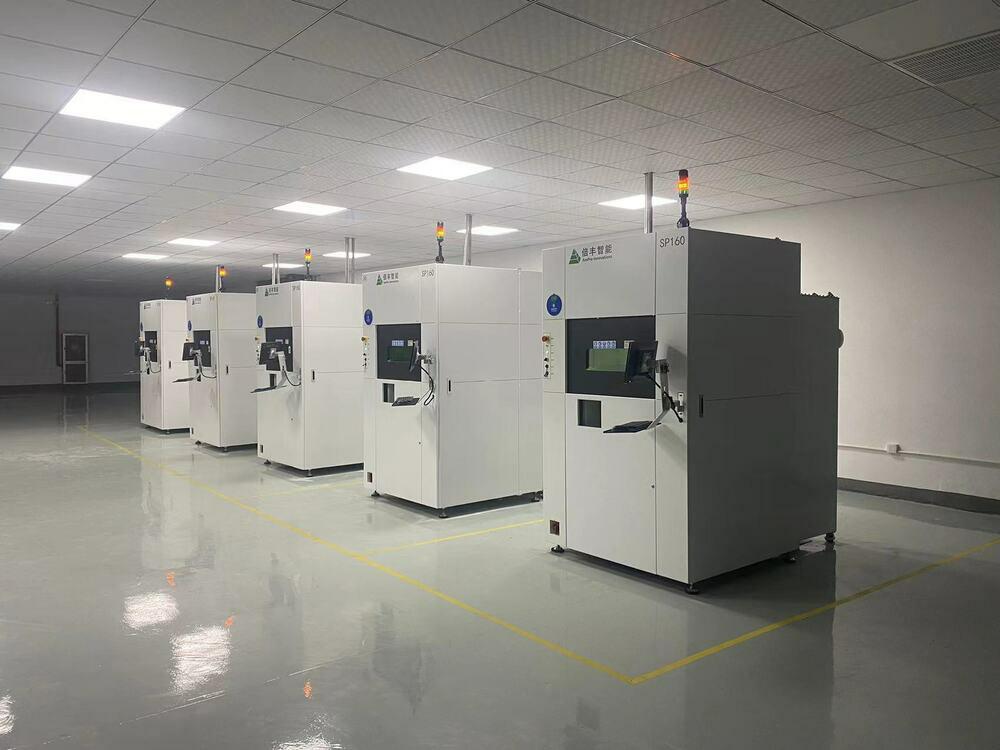
Key Considerations
When 3D printing titanium, several critical factors need to be taken into account to ensure optimal results:
- Minimum Wall Thickness: For structural components, a minimum wall thickness of 1-2 mm is recommended to ensure durability and strength.
- Minimum Detail Size: Fine details, such as embossed or engraved features, should be at least 0.5 mm in size to be effectively reproduced.
- Surface Quality: Overhanging areas with less than a 45° angle tend to have a poorer surface finish. Design parts with minimal overhangs or use support structures to improve the surface quality.
- Hollow Parts: An exit hole of at least 3 mm in diameter is required to remove any unsintered powder from hollow parts.
- Edge Design: Edges should be rounded or filleted with at least a 3 mm radius to reduce thermal stresses and improve structural integrity.
- Tolerances: Typical tolerances for well-designed parts are ±0.076 mm plus ±0.0254 mm/mm, ensuring high precision and accuracy.
How much does it cost to 3D printed titanium?
At this point, you might be wondering about the practical implications and performance characteristics of 3D printed titanium. Is it strong enough for demanding applications? What temperatures are involved in the printing process? And what makes titanium 3D printing particularly valuable in the medical field? These are crucial questions to explore as we delve deeper into the capabilities and benefits of this advanced manufacturing technique.
Is 3D Printed Titanium Strong?
Yes, 3D printed titanium is incredibly strong. In fact, titanium is known for its high strength-to-weight ratio, which means it offers exceptional strength without adding excessive weight. This makes it ideal for applications where both durability and lightweight properties are critical. The 3D printing process further enhances its utility by allowing for the creation of complex, robust structures that would be difficult or impossible to achieve with traditional methods.
What Temperature Is Titanium 3D Printing?
The process of 3D printing titanium typically involves temperatures around 1,600 to 1,700 degrees Celsius (2,912 to 3,092 degrees Fahrenheit). These high temperatures are necessary to melt the titanium powder and fuse it layer by layer. The precise control of temperature during the process ensures the integrity and performance of the final product.

Typical Applications for 3D Printed Titanium in the Medical Field
In the medical field, 3D printed titanium is revolutionizing how we approach patient care. Some typical applications include:
- Implants: Titanium’s biocompatibility makes it an excellent material for medical implants such as joint replacements and dental implants. The ability to 3D print custom implants tailored to a patient’s specific anatomy enhances the fit and function of these critical devices.
- Surgical Instruments: Custom-designed surgical tools that are lightweight yet strong can be produced through titanium 3D printing, improving surgical precision and reducing fatigue for surgeons.
- Prosthetics: Titanium’s strength and lightweight properties make it ideal for creating durable, comfortable prosthetic limbs that can be customized to meet the unique needs of each patient.

Conclusion
Titanium 3D printing represents a significant advancement in manufacturing technology, offering unparalleled opportunities to create lightweight, strong, and complex components for a variety of applications. Whether it’s in aerospace, medical, or automotive fields, the precision and efficiency of this process open up new possibilities for innovation and performance.