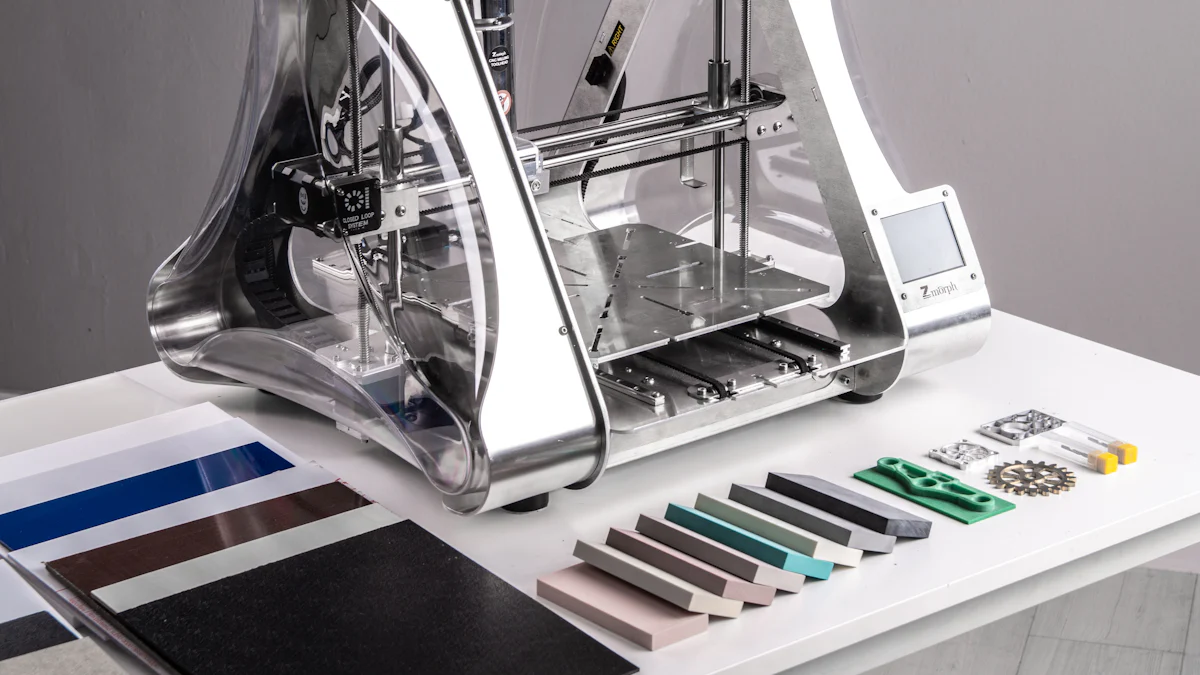
3D printed bikes represent a groundbreaking shift in cycling technology. If you’re wondering, “How much does a 3D printed bike cost?” you’ll find that prices range widely, starting at 1,499forentry−levelmodelsandclimbingbeyond1,499 for entry-level models and climbing beyond 1,499forentry−levelmodelsandclimbingbeyond20,000 for high-performance options. This variation stems from factors like material choice, production methods, and customization. For instance, titanium frames, known for their strength and lightweight properties, often push costs into the premium range. On the other hand, some models, such as those made with recycled aluminum or composite plastics, offer more affordable alternatives. The innovation behind these bikes, including tailored designs and advanced manufacturing techniques, justifies their price and sets them apart from traditional bicycles.
Key Takeaways
- 3D printed bikes range in price from 1,499toover1,499 to over 1,499toover20,000, influenced by materials, technology, and customization.
- Titanium and advanced composites offer high performance but come at a premium, while plastic options provide more budget-friendly alternatives.
- Customization is a key advantage of 3D printed bikes, allowing for tailored geometry and unique designs that enhance comfort and performance.
- Additive manufacturing reduces material waste and supports local production, making 3D printing a more sustainable option compared to traditional methods.
- The future of 3D printed bikes looks promising with advancements in technology that may lead to faster production and more affordable options.
- 3D printing enables innovative designs that improve bike performance, such as integrated features and optimized structures.
- As the cycling industry embraces 3D printing, expect a shift towards mass customization, allowing cyclists to own bikes tailored to their specific needs.
Factors Influencing the Cost of a 3D Printed Bike
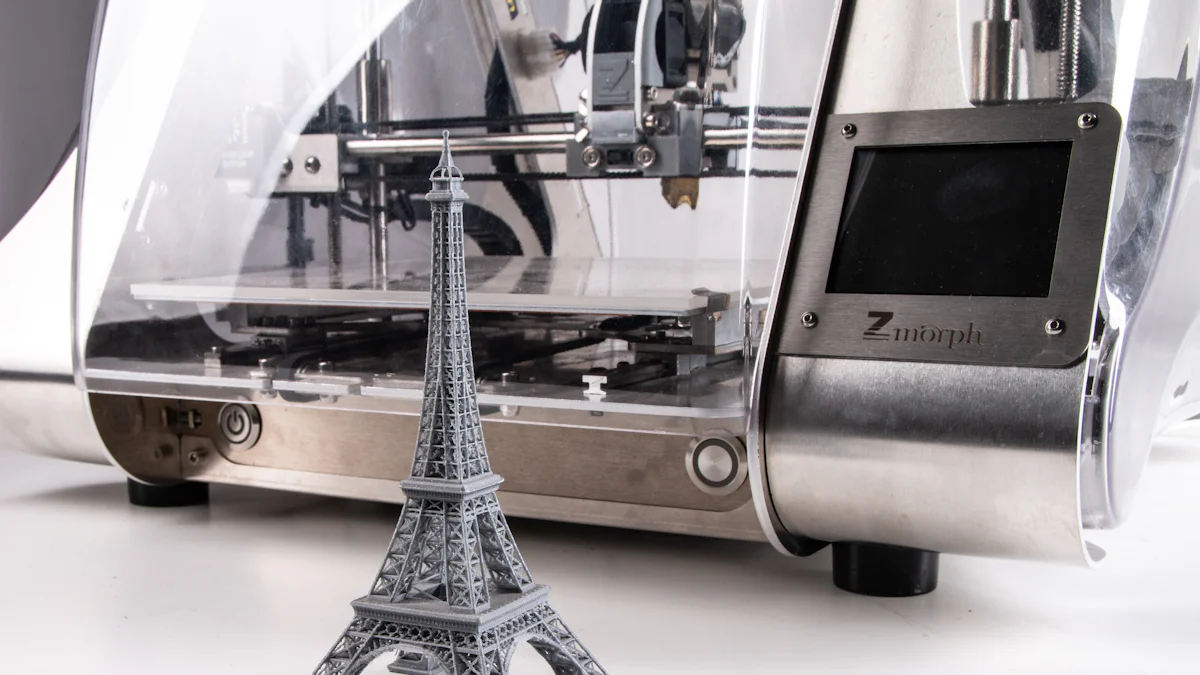
When exploring the question, “How much does a 3D printed bike cost?” it becomes clear that several factors contribute to the price. These factors include the materials used, the technology involved, and the level of customization. Each plays a significant role in determining the final cost.
Materials Used
Titanium and other premium metals
Titanium stands out as a popular choice for high-end 3D printed bikes. Its lightweight nature and exceptional strength make it ideal for performance-focused cyclists. However, titanium is expensive to source and process. The additive manufacturing process used in 3D printing allows for precise shaping of titanium, reducing material waste compared to traditional methods. Despite this efficiency, the cost of titanium remains high, which directly impacts the price of the bike.
Plastic and composite materials
For more budget-friendly options, manufacturers often turn to plastic and composite materials. These materials offer flexibility and durability at a lower cost. Composite materials, such as carbon fiber reinforced polymers, provide a balance between strength and affordability. Additionally, 3D printing enables the creation of complex designs with these materials, which would be challenging or impossible using traditional manufacturing techniques.
3D Printing Technology
Additive manufacturing processes
The core of 3D printed bike production lies in additive manufacturing. Unlike traditional methods that involve cutting or molding, additive manufacturing builds the bike layer by layer. This process minimizes waste and allows for intricate designs. However, the advanced machinery required for this technology adds to the overall cost. The precision of additive manufacturing ensures a high-quality product, but it also demands significant investment in equipment and expertise.
Precision and complexity of the design
3D printing excels in creating complex and precise designs. Manufacturers can produce bikes with unique geometries and integrated features that enhance performance. For example, internal cable routing or aerodynamic frames can be seamlessly incorporated into the design. These intricate details require advanced software and meticulous planning, which contribute to the bike’s price.
Customization Options
Tailored geometry and fit
One of the most appealing aspects of 3D printed bikes is the ability to customize the geometry and fit. Cyclists can have bikes tailored to their specific body measurements and riding preferences. This level of personalization ensures optimal comfort and performance. However, creating a custom design involves additional time and resources, which increases the cost.
Unique aesthetic designs
Beyond functionality, 3D printing allows for unparalleled creativity in aesthetics. Riders can choose unique patterns, colors, and finishes that reflect their personal style. This customization adds a premium touch to the bike, making it a one-of-a-kind product. While these aesthetic options elevate the bike’s appeal, they also contribute to its price.
Production Scale
Limited production runs
3D printed bikes often come from limited production runs. Manufacturers typically focus on creating small batches or even one-off designs. This approach allows them to maintain high quality and precision. However, producing fewer units increases the cost per bike. Unlike traditional manufacturing, which relies on mass production to lower costs, 3D printing thrives in low-volume scenarios. For smaller manufacturers, this technology eliminates the need for large-scale facilities or expensive molds. It empowers them to enter the market with minimal upfront investment.
“3D printing reduces entry barriers for smaller manufacturers by minimizing the need for large upfront investments.”
This flexibility benefits niche markets and custom bike enthusiasts. It also enables local production, which reduces dependency on global supply chains. While this method enhances exclusivity and customization, it limits the ability to achieve economies of scale, keeping prices higher.
Impact of economies of scale
Economies of scale play a significant role in traditional bike manufacturing. Large-scale production spreads fixed costs, such as machinery and labor, across thousands of units. This results in lower prices for consumers. In contrast, 3D printing operates differently. The technology excels in creating complex designs and prototypes quickly, but it struggles to match the cost efficiency of mass production.
For example, carbon fiber bikes benefit from well-established manufacturing methods and trained labor. These factors make them lighter and more aerodynamic at a competitive price. On the other hand, 3D printing remains more cost-effective for low-volume production. It reduces prototype delivery cycles by up to 50% and cuts labor hours significantly. This efficiency makes it ideal for producing functional prototypes or limited-edition models.
“3D printing has shown how complex consumer items can be produced cost-effectively, fast, and independently of supply chains.”
While 3D printing may not yet rival traditional methods in large-scale production, its potential lies in customization and innovation. As the technology advances, it could bridge the gap, making high-quality, personalized bikes more accessible to a broader audience.
How much does a 3D printed bike cost compared to traditional bikes?
When comparing 3D printed bikes to traditional bikes, the differences extend beyond just the price tag. These two categories of bicycles represent distinct approaches to manufacturing, performance, and design. Understanding these differences helps answer the question, “How much does a 3D printed bike cost?” while also highlighting the unique value they bring to the cycling world.
Price Comparison
Average cost of traditional bikes
Traditional bikes come in a wide range of prices, depending on their materials, brand, and purpose. Entry-level models typically start at 300to300 to 300to500, while mid-range bikes, often made with aluminum or basic carbon fiber, range from 1,000to1,000 to 1,000to3,000. High-performance road or mountain bikes, crafted with advanced carbon fiber and premium components, can cost anywhere from 4,000to4,000 to 4,000to12,000. Mass production and established manufacturing techniques help keep these prices relatively stable.
Why 3D printed bikes are more expensive
3D printed bikes, on the other hand, often exceed the cost of traditional bikes. The price reflects the cutting-edge technology, premium materials, and customization options involved. For example, titanium 3D printed frames can cost between 10,000and10,000 and 10,000and15,000, while complete high-performance models may reach $20,000 or more. Unlike traditional bikes, which benefit from economies of scale, 3D printed bikes are typically produced in limited quantities. This exclusivity, combined with the ability to create intricate designs and tailored geometries, justifies the higher price point.
“3D printing empowers manufacturers to create highly customized bikes that traditional methods cannot replicate.”
Performance and Durability
Strength and weight advantages of 3D printed bikes
3D printed bikes excel in performance due to their innovative use of materials and design. Titanium and carbon fiber composites, commonly used in 3D printing, offer exceptional strength-to-weight ratios. This means riders get a lightweight bike without compromising durability. The additive manufacturing process also allows for optimized frame structures, reducing unnecessary material while maintaining strength. Traditional bikes, while strong, often rely on standardized designs that lack this level of precision.
Longevity and maintenance considerations
The durability of 3D printed bikes often surpasses that of traditional bikes. The precise layering process ensures consistent material quality, reducing weak points that could lead to failure. Additionally, the ability to customize parts means replacements or upgrades can be tailored to the original design. Traditional bikes, while reliable, may require more frequent maintenance due to wear and tear on mass-produced components. However, the availability of replacement parts for traditional bikes remains an advantage.
Innovation and Design
Unique features enabled by 3D printing
3D printing opens the door to unparalleled innovation in bike design. Manufacturers can create frames with integrated features like internal cable routing, aerodynamic shapes, and even suspension systems. These designs enhance both performance and aesthetics. Customization extends to every detail, from geometry to color schemes, allowing riders to own a bike that fits their exact needs and preferences. Traditional manufacturing methods struggle to achieve this level of flexibility.
Limitations of traditional manufacturing
Traditional bike manufacturing relies on molds and standardized processes, which limit design possibilities. While these methods are efficient for mass production, they cannot match the complexity or personalization offered by 3D printing. For instance, creating a one-of-a-kind frame with unique geometry would be prohibitively expensive using traditional techniques. In contrast, 3D printing thrives in producing intricate, low-volume designs without the need for costly molds or tooling.
“The flexibility of 3D printing redefines what is possible in bike manufacturing, setting a new standard for innovation and customization.”
The Future of 3D Printed Bikes
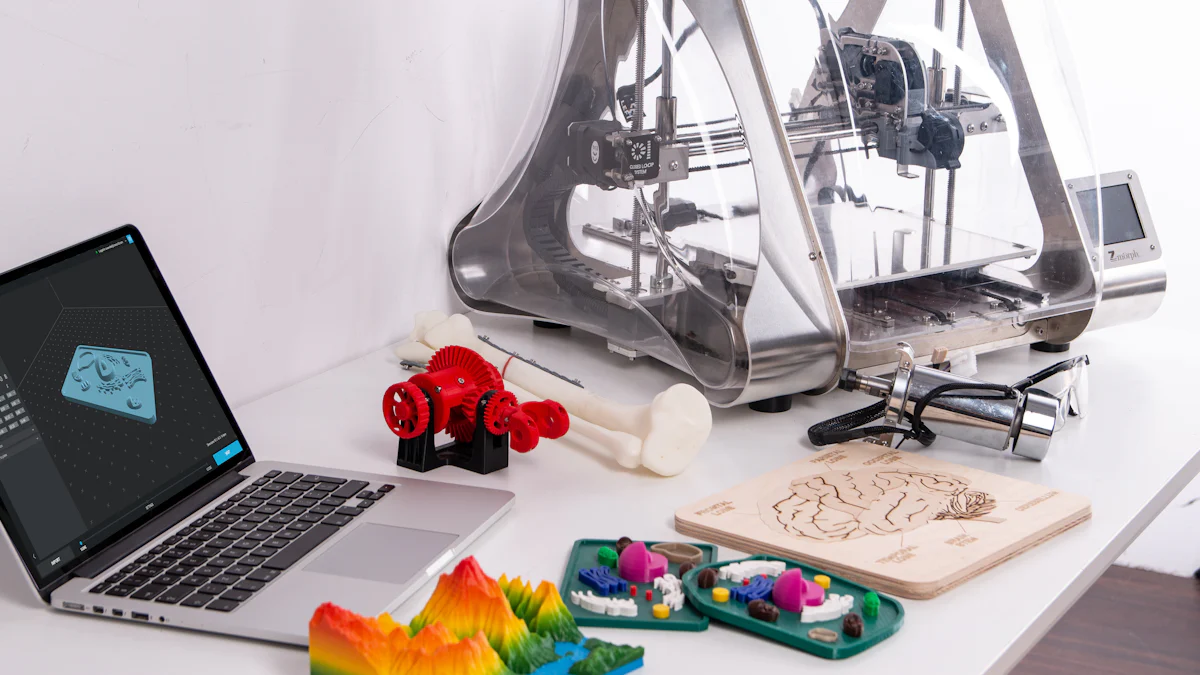
Advancements in 3D Printing Technology
Faster and more affordable production methods
The future of 3D printed bikes looks promising as advancements in technology continue to reshape the manufacturing landscape. Engineers are working on faster production methods that reduce the time required to create intricate bike components. For example, additive manufacturing allows manufacturers to produce parts layer by layer with minimal waste. This efficiency not only speeds up production but also lowers costs. As a result, cyclists may soon see more affordable 3D printed bikes entering the market.
Additionally, the development of high-speed printers and automated processes is expected to revolutionize the industry. These innovations will enable manufacturers to scale production without compromising quality. According to experts, 3D printing could cut prototype delivery cycles by up to 50%, making it easier to bring new designs to market quickly.
New materials and design possibilities
Material innovation plays a crucial role in the evolution of 3D printed bikes. Titanium, aluminum, and carbon fiber composites are already popular choices for their strength and lightweight properties. However, researchers are exploring new materials that could further enhance performance. For instance, advanced polymers and hybrid composites may offer improved durability and flexibility.
The design possibilities are equally exciting. 3D printing allows for the creation of complex geometries that traditional methods cannot achieve. Manufacturers can integrate features like internal cable routing, aerodynamic frames, and even suspension systems directly into the bike’s structure. This level of design freedom opens the door to bikes that are not only functional but also visually stunning.
“3D printing empowers manufacturers to push the boundaries of design, creating bikes that combine innovation with artistry.”
Market Trends
Growing adoption of 3D printing in the cycling industry
The cycling industry is embracing 3D printing at an unprecedented rate. From custom saddles to entire bike frames, manufacturers are leveraging this technology to meet the demands of modern cyclists. Small-scale producers, in particular, benefit from the flexibility and cost-effectiveness of 3D printing. They can create unique products without the need for expensive molds or large-scale facilities.
Larger companies are also recognizing the potential of 3D printing. Some are using it to produce prototypes, while others are incorporating it into their production lines for end-use parts. This trend indicates a shift toward more personalized and efficient manufacturing processes.
Potential for mass customization
Mass customization represents one of the most exciting opportunities for 3D printed bikes. Cyclists often seek bikes tailored to their specific needs, whether it’s a custom frame geometry or a unique aesthetic design. 3D printing makes this level of personalization feasible on a larger scale. Manufacturers can produce bikes that cater to individual preferences without significantly increasing costs.
This approach not only enhances the customer experience but also sets 3D printed bikes apart from their traditionally manufactured counterparts. As the technology matures, we may see a future where every cyclist can own a bike designed specifically for them.
Environmental Impact
Sustainability of 3D printing processes
Sustainability is a key advantage of 3D printing. Traditional bike manufacturing often involves significant material waste due to cutting and molding processes. In contrast, 3D printing builds components layer by layer, using only the material required. This efficiency reduces waste and minimizes the environmental footprint of production.
Moreover, 3D printing supports local manufacturing, which can reduce the carbon emissions associated with transportation. By producing bikes closer to their end users, manufacturers can further enhance sustainability.
Reduction in material waste
The reduction in material waste is one of the most compelling environmental benefits of 3D printing. For example, titanium frames produced through additive manufacturing use significantly less raw material compared to traditional methods. This not only conserves resources but also lowers production costs.
“3D printing demonstrates how innovation can align with sustainability, offering a greener alternative to traditional manufacturing.”
As the cycling industry continues to adopt 3D printing, these environmental benefits will likely become a major selling point. Cyclists who value eco-friendly practices may find 3D printed bikes an appealing choice. The combination of sustainability, customization, and cutting-edge technology positions 3D printed bikes as a transformative force in the world of cycling.
3D printed bikes redefine cycling with their unique blend of innovation, performance, and customization. Prices range from 1,500toover1,500 to over 1,500toover20,000, reflecting the advanced materials and technology involved. While they cost more than traditional bikes, their lightweight frames, tailored designs, and cutting-edge features justify the investment. The future looks bright as advancements in 3D printing promise greater accessibility and sustainability. For cyclists seeking a personalized experience and high-performance ride, these bikes represent a revolutionary choice that pushes the boundaries of what bicycles can achieve.
FAQ
What makes 3D printing unique in the cycling industry?
3D printing stands out for its ability to create highly customized products with unmatched precision. This technology allows manufacturers to tailor bike components to fit individual ergonomic and anatomical needs. For cyclists, this means a bike that feels like it was made just for them, enhancing both comfort and performance.
How does 3D printing improve bike components?
3D printing enables the design of components that handle complex, multi-directional loads better than traditional manufacturing methods. This results in stronger and more durable parts. For example, frames and handlebars can be optimized to withstand stress from various angles, ensuring reliability during intense rides.
Are 3D printed bikes more expensive than traditional bikes?
Yes, 3D printed bikes typically cost more due to the advanced technology, premium materials, and customization involved. While traditional bikes benefit from mass production, 3D printed bikes focus on precision and innovation. This exclusivity often justifies the higher price tag for those seeking cutting-edge performance and design.
Can 3D printing reduce waste in bike manufacturing?
Absolutely. Unlike traditional methods that involve cutting or molding, 3D printing builds components layer by layer. This process uses only the material needed, significantly reducing waste. Additionally, local production through 3D printing minimizes the environmental impact associated with transportation.
What materials are commonly used in 3D printed bikes?
Titanium, carbon fiber composites, and advanced polymers are popular choices. Titanium offers exceptional strength and lightweight properties, making it ideal for high-performance bikes. Carbon fiber composites provide a balance of durability and affordability, while advanced polymers open up new possibilities for innovative designs.
How does 3D printing impact the future of cycling?
3D printing is set to revolutionize cycling further. It’s not just about rapid prototyping anymore; manufacturers are now using it for both plastic and metal end products. As the technology advances, we can expect faster production, new materials, and even more affordable options for cyclists.
Can 3D printing enhance bike performance?
Yes, 3D printing allows for intricate designs that improve aerodynamics, reduce weight, and increase strength. Features like internal cable routing and aerodynamic frames can be seamlessly integrated into the bike’s structure. These innovations directly enhance performance, giving riders a competitive edge.
Is 3D printing suitable for mass production in the cycling industry?
Currently, 3D printing excels in low-volume production and customization. While it struggles to match the cost efficiency of traditional mass production, advancements in technology may bridge this gap. The potential for mass customization could redefine how bikes are manufactured in the future.
What challenges does 3D printing face in bike manufacturing?
The main challenges include high initial costs for equipment and slower production speeds compared to traditional methods. Additionally, the technology requires skilled expertise to design and produce complex components. However, ongoing advancements aim to address these limitations, making 3D printing more accessible.
What’s next for 3D printing in cycling?
The future looks bright. Engineers are exploring faster production methods, new materials, and innovative designs. 3D printing will likely become even more prominent, not just for prototypes but for end-use products. This evolution promises to bring more personalized, sustainable, high-performance bikes to the market.