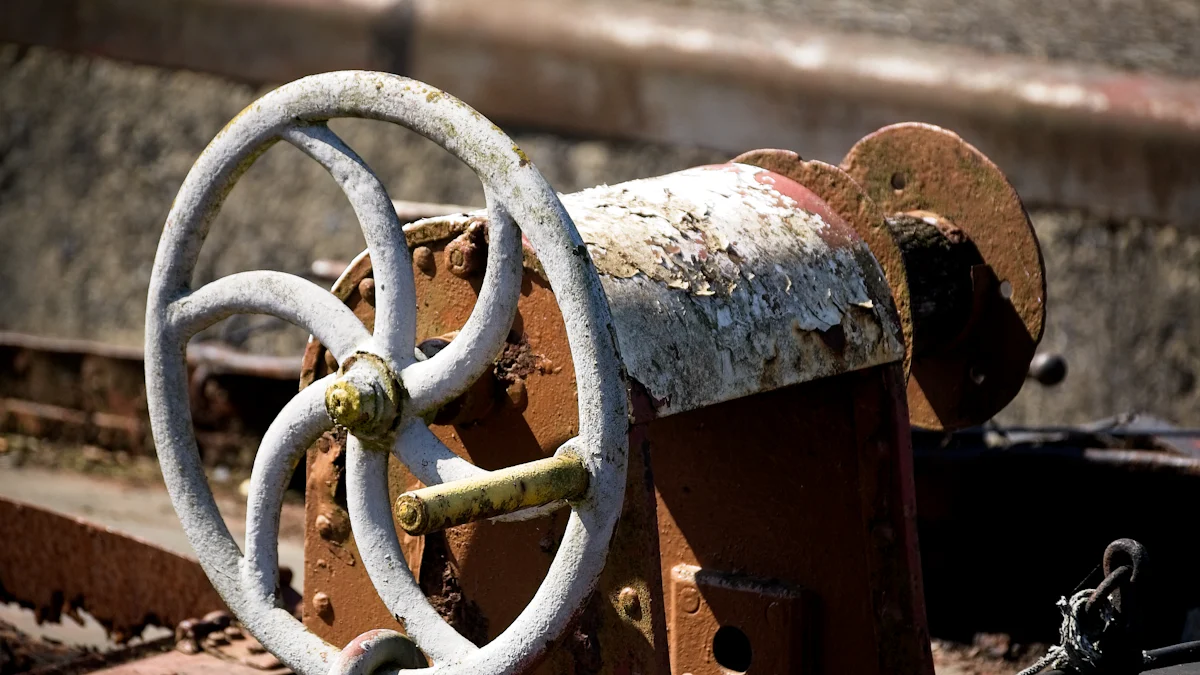
When I think about metals and their durability, titanium stands out as a remarkable material. A common question is, “Does Titanium Rust?” The answer is no; unlike iron or steel, titanium does not rust. Rust forms when iron reacts with oxygen and moisture, but titanium contains no iron. Instead, it develops a thin, protective oxide layer on its surface. This layer acts as a shield, preventing corrosion and ensuring the metal remains intact even in harsh environments. What amazes me most is how this oxide layer can repair itself if damaged, making titanium incredibly resilient and long-lasting.
Why Does Titanium Not Rust?
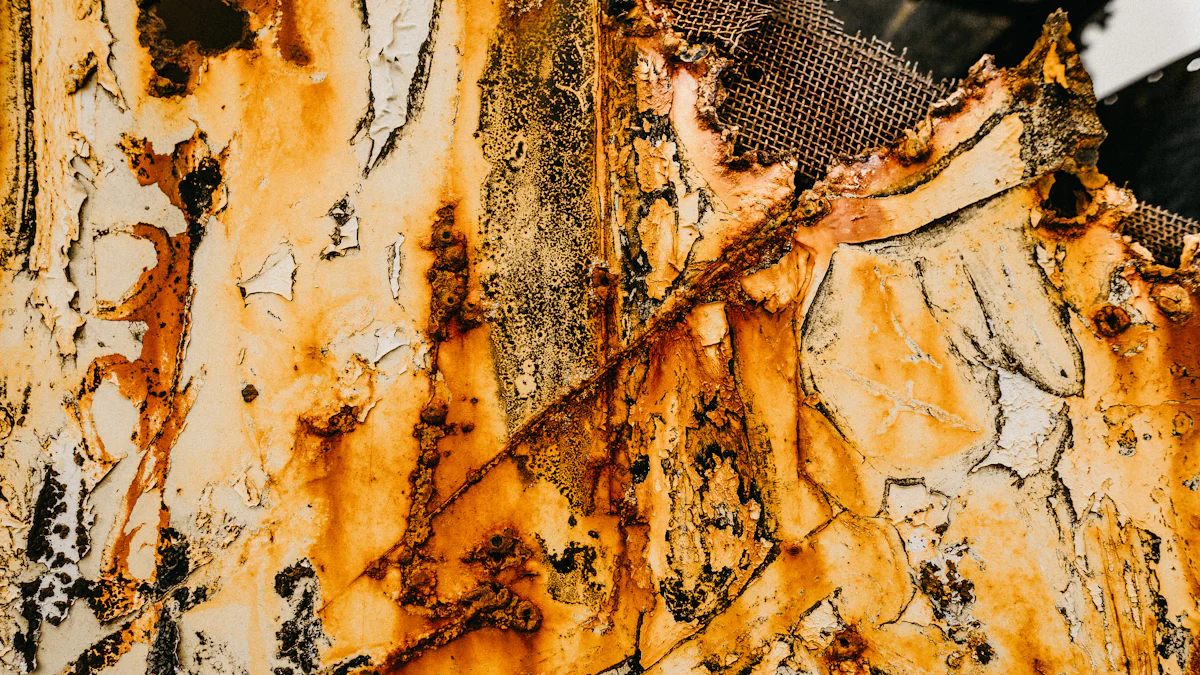
Understanding Rust and Corrosion
Rust: A process specific to iron and its alloys
Rust forms when iron reacts with oxygen and moisture in the environment. This process, known as oxidation, creates a reddish-brown flaky substance that weakens the metal over time. I find it fascinating that rust only occurs in metals containing iron, such as steel. Without iron, rust cannot form. This is why titanium, which contains no iron, does not rust. The absence of iron makes titanium immune to this specific type of degradation.
Corrosion: A broader term for metal degradation
Corrosion, on the other hand, refers to the gradual destruction of any metal due to chemical reactions with its surroundings. Unlike rust, corrosion affects a wide range of metals, including aluminum, copper, and even titanium. However, titanium stands out because it resists corrosion exceptionally well. Its unique properties allow it to endure harsh environments where other metals would deteriorate. For example, titanium is often used in naval ship hulls and boat components like propeller shafts because it withstands seawater corrosion far better than most materials.
Titanium’s Protective Oxide Layer
How the oxide layer forms naturally
Titanium owes its remarkable resistance to corrosion to a natural phenomenon. When exposed to air, titanium reacts with oxygen to form a thin, invisible oxide layer on its surface. This layer acts as a barrier, shielding the metal from further exposure to corrosive elements. I find it incredible how this process happens automatically, without any need for additional treatments or coatings. This self-forming layer explains why titanium remains durable in environments that would quickly degrade other metals.
Self-healing properties of the oxide layer
What truly sets titanium apart is the self-healing nature of its oxide layer. If the layer gets scratched or damaged, it regenerates almost instantly upon contact with oxygen. This feature ensures that titanium maintains its protective shield even in challenging conditions. For instance, titanium is widely used in chemical processing equipment like reactors and piping systems because it can withstand highly corrosive substances. Its ability to repair itself makes it a reliable choice for applications where durability is critical.
Does Titanium Corrode Under Certain Conditions?
Titanium stands out as one of the most corrosion-resistant metals, but even this remarkable material can face challenges in specific environments. I have always admired its resilience, yet understanding its limitations helps us appreciate its unique properties even more.
Environmental Factors That May Affect Titanium
High chloride concentrations (e.g., seawater)
Titanium performs exceptionally well in environments with high chloride levels, such as seawater. Its protective oxide layer shields it from corrosion, making it a preferred choice for marine applications. However, prolonged exposure to extremely high chloride concentrations can lead to localized corrosion, such as pitting or crevice corrosion. For example, in stagnant seawater or areas where oxygen levels drop, titanium may experience slight degradation. Despite this, I find it fascinating that titanium still outperforms most other metals, including stainless steel, in such conditions.
Exposure to strong acids or alkalis
Titanium resists many corrosive substances, including strong acids and alkalis. Its oxide layer acts as a barrier, preventing chemical reactions that would typically degrade other metals. However, certain environments, like those containing hydrofluoric acid or highly concentrated sulfuric acid, can challenge titanium’s durability. These substances can penetrate the oxide layer, causing corrosion. Even so, I have observed that titanium remains far more resilient than materials like aluminum or steel in similar conditions.
Comparing Titanium to Other Metals
Titanium vs. stainless steel
When comparing titanium to stainless steel, titanium emerges as the superior choice for corrosion resistance. Stainless steel relies on chromium to form its protective layer, but this layer can break down in harsh environments, such as seawater or chlorine-rich atmospheres. Titanium, on the other hand, maintains its integrity even in these challenging conditions. For instance, I have seen titanium used in desalination plants and chemical processing facilities where stainless steel would fail. Its ability to withstand such environments makes it invaluable for industries requiring long-term durability.
Titanium vs. aluminum
Aluminum, while lightweight and versatile, cannot match titanium’s corrosion resistance. In extreme chemical conditions, such as exposure to acidic or saline environments, aluminum corrodes more rapidly. Titanium’s oxide layer provides a level of protection that aluminum simply cannot achieve. For example, in aerospace applications, titanium components endure far better than aluminum when exposed to moisture and salt. I find it remarkable how titanium combines strength, corrosion resistance, and longevity, making it the preferred material for demanding applications.
Applications of Titanium’s Rust Resistance
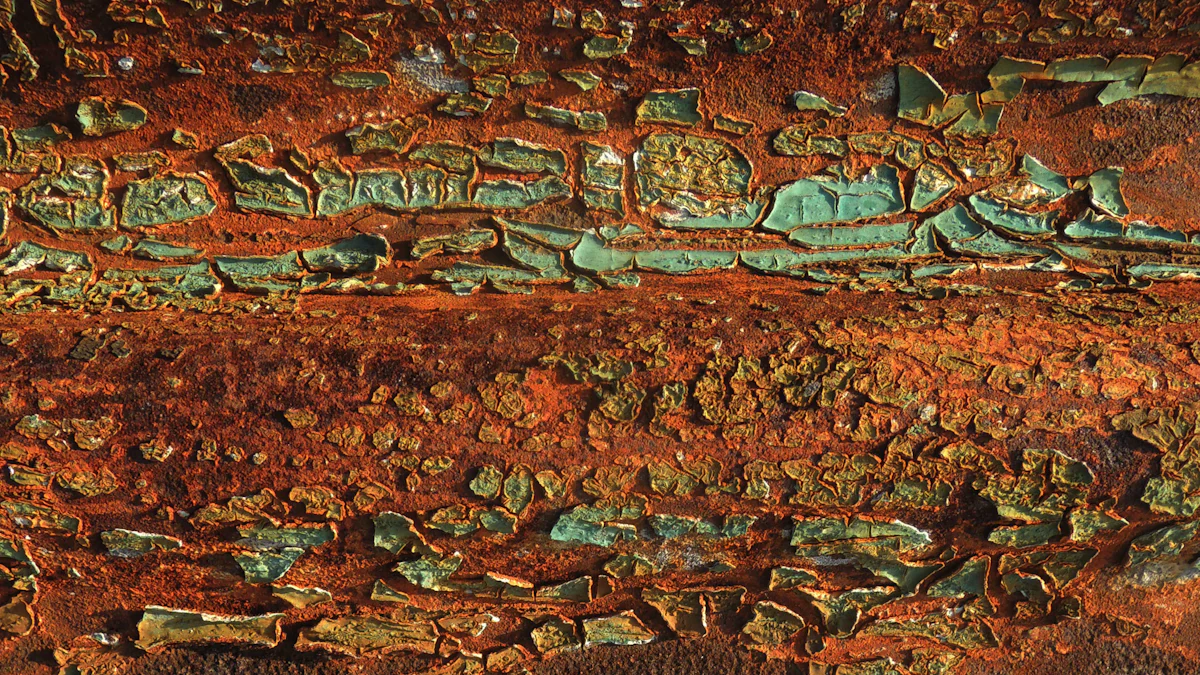
Titanium’s exceptional resistance to rust and corrosion makes it a vital material in several industries. Its unique properties, such as high strength-to-weight ratio, biocompatibility, and durability, allow it to excel in demanding environments.
Aerospace Industry
Use in aircraft and spacecraft components
In the aerospace industry, titanium plays a crucial role. Engineers rely on it for constructing aircraft and spacecraft components due to its lightweight nature and ability to withstand extreme conditions. For example, titanium is used in jet engines, airframes, and landing gear. Its corrosion resistance ensures that these components remain durable even when exposed to high altitudes and varying temperatures. I find it fascinating how titanium’s strength and resistance to fatigue contribute to safer and more efficient air travel. Additionally, its compatibility with advanced manufacturing techniques, like 3D printing, has revolutionized the production of aerospace parts.
Marine Industry
Applications in seawater environments
Titanium’s resistance to seawater corrosion makes it indispensable in the marine industry.
Medical Industry
Use in implants and surgical tools
In the medical field, titanium stands out for its biocompatibility and corrosion resistance. Surgeons often use titanium for implants, such as joint replacements, dental implants, and bone fixation devices. I find it remarkable how titanium integrates seamlessly with human tissue, reducing the risk of rejection. Its durability ensures that implants last for decades without degrading. Additionally, titanium’s lightweight nature makes it ideal for surgical tools, allowing for precision and ease of use during procedures. For example, orthopedic surgeons rely on titanium screws and plates to stabilize fractures effectively. Its role in advancing medical technology cannot be overstated.
Titanium does not rust, which I find remarkable given its unique ability to form a protective oxide layer. This natural barrier ensures exceptional resistance to corrosion, even in challenging environments. However, extreme conditions, such as high chloride concentrations or exposure to strong acids, can still affect its performance. Despite these limitations, titanium’s durability and resilience make it indispensable in industries like aerospace, marine, and medicine. Its strength, lightweight nature, and biocompatibility allow it to excel in high-stress and high-precision applications, proving its value as a versatile and reliable material.
FAQ
Does Titanium Rust?
Titanium does not rust. Rust forms when iron reacts with oxygen and moisture, but titanium contains no iron. Instead, it develops a protective oxide layer on its surface. This layer prevents corrosion and ensures titanium remains durable even in harsh environments. I find this property remarkable because it sets titanium apart from many other metals.
Why is Titanium Rust Resistant?
I admire how this natural characteristic makes titanium an excellent choice for applications requiring long-term durability.
Is Titanium Rust-Proof?
Yes, titanium is rust-proof. When titanium comes into contact with oxygen, it forms a tightly adhered oxide layer that prevents further oxidation. This feature ensures titanium remains highly resistant to rust and corrosion in most environments. I have seen this property make titanium invaluable in industries like aerospace and marine engineering.
What Are the Benefits and Limitations of Titanium’s Corrosion Resistance?
Titanium offers exceptional corrosion resistance, which I consider one of its greatest strengths.
Can Titanium Corrode in Seawater?
Titanium performs exceptionally well in seawater due to its protective oxide layer. This layer prevents most forms of corrosion, including pitting and crevice corrosion. However, in stagnant seawater or areas with low oxygen levels, titanium may experience slight degradation. Even so, I have observed that titanium outperforms materials like stainless steel in marine environments.
How Does Titanium Compare to Stainless Steel in Corrosion Resistance?
Titanium surpasses stainless steel in corrosion resistance. While stainless steel relies on chromium to form its protective layer, this layer can break down in harsh conditions like seawater. Titanium’s oxide layer remains intact even in challenging environments. I have seen titanium used in applications where stainless steel would fail, such as desalination plants and offshore platforms.
Why Is Titanium Used in Medical Implants?
Titanium’s biocompatibility and corrosion resistance make it ideal for medical implants. It integrates seamlessly with human tissue and resists degradation inside the body. I find it fascinating how titanium ensures implants, such as joint replacements and dental fixtures, remain functional for decades without causing adverse reactions.
Does Titanium Require Special Maintenance to Prevent Corrosion?
Titanium requires minimal maintenance to prevent corrosion. Its oxide layer forms naturally and regenerates if damaged. Unlike other metals, titanium does not need coatings or treatments to maintain its durability. I appreciate how this property reduces the effort and cost of upkeep in various applications.
Can Titanium Be Used in Extreme Environments?
Titanium excels in extreme environments. Its resistance to high temperatures, corrosive chemicals, and seawater makes it suitable for demanding applications. For example, I have seen titanium used in jet engines, chemical reactors, and deep-sea equipment. Its ability to endure such conditions highlights its versatility and reliability.
Is Titanium Environmentally Friendly?
Yes, titanium is environmentally friendly. It is non-toxic, recyclable, and has a long lifespan, reducing the need for frequent replacements. I believe these qualities make titanium a sustainable choice for industries aiming to minimize their environmental impact.