In the rapidly evolving landscape of manufacturing, understanding the cost implications of different production methods is crucial for making informed decisions. Two prominent methods are 3D printing and injection molding. 3D printing is known for its versatility and rapid prototyping capabilities, while injection molding remains a staple for high-volume production due to its efficiency and cost-effectiveness at scale. This article aims to provide B2B purchasers with a comprehensive comparison of these two methods, helping them align their production needs with budget constraints.
Key Cost Drivers in 3D Printing and Injection Molding
3D Printing
Build Time
Build time is a significant cost factor in 3D printing. The time required to produce a part depends on its complexity, size, and the layer height used. Complex designs with intricate details and larger dimensions naturally take longer to print, thus increasing costs. To mitigate this, optimizing the design for quicker printing can substantially reduce expenses. Techniques such as reducing the infill density, using larger layer heights for less critical sections, and orienting the part to minimize support structures can help optimize build time.
Material Cost
The material cost in 3D printing can vary significantly depending on the type of material used. Common materials include PLA, ABS, and various metals such as titanium. Each material has its cost implications. For instance, Direct Metal Laser Sintering (DMLS) allows for the recycling of unused powder, potentially lowering material costs. In contrast, methods like Selective Laser Sintering (SLS) do not recycle unused powder, increasing material waste and costs. Choosing the appropriate material for the specific application is essential while considering cost and performance.
Post-processing
Post-processing is an often overlooked cost driver in 3D printing. Almost all 3D-printed parts require some level of post-processing to achieve the desired finish and functionality. This can include sanding, polishing, painting, or additional machining. The complexity and finish required will dictate the extent of post-processing needed and consequently, the cost. For high-precision or aesthetically critical parts, post-processing can become a significant expense.
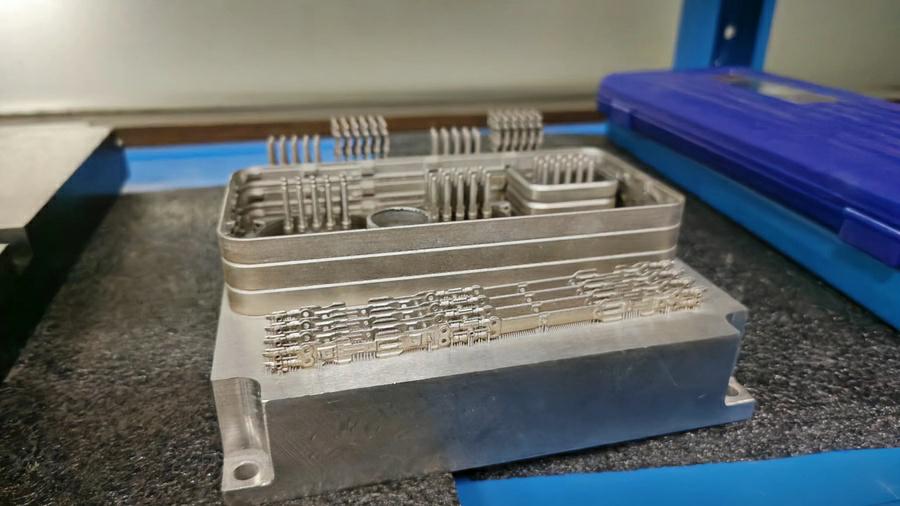
Injection Molding
Part Complexity
The complexity of the part being produced is a major cost factor in injection molding. Complex parts may require intricate molds with features like undercuts or side actions, significantly increasing mold costs. Design for Manufacturability (DFM) analysis is essential to optimize the part design, reducing complexity, and consequently, the cost. By simplifying the design and eliminating unnecessary features, manufacturers can reduce the overall cost of the mold.
Tooling and Setup Costs
Injection molding involves substantial initial costs for mold creation and setup. However, these costs can be amortized over large production volumes, making injection molding economically viable for mass production. The high upfront costs of durable steel molds are justified when producing thousands or millions of parts, as the cost per part decreases significantly with volume. This makes injection molding ideal for high-volume production runs.
Piece-Part Price
At high volumes, the piece-part price for injection molding is generally lower than for 3D printing. Factors that affect the piece-part price include the cycle time, material cost, and the efficiency of the mold design. Injection molding’s efficiency in producing large quantities of parts quickly and consistently results in a lower cost per part, making it the preferred choice for large-scale production.
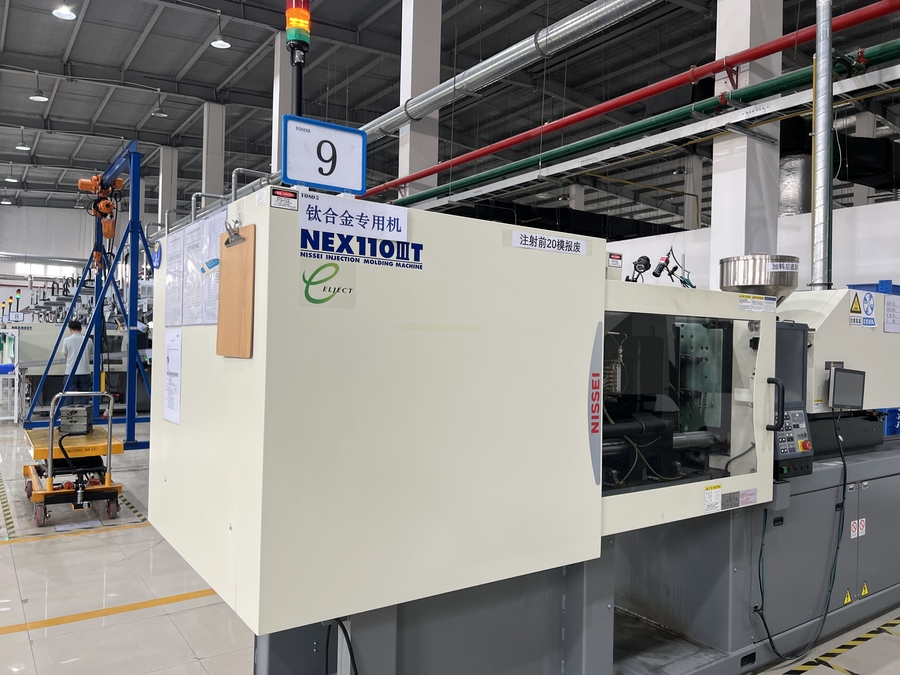
Decision Factors: Prototyping vs. Production
Prototyping
3D Printing for Prototyping
3D printing is ideal for rapid prototyping due to its low setup costs and fast turnaround times. Design changes can be quickly implemented by tweaking CAD files and reprinting, which is considerably cheaper and faster than modifying molds in injection molding. This flexibility allows for rapid iteration and refinement of designs, making 3D printing an excellent choice for early-stage product development.
Injection Molding for Prototyping
While traditionally more expensive for prototyping, injection molding can be viable for prototypes requiring the exact material properties as the final product. Using a single-cavity aluminum mold can produce hundreds of parts quickly and at a lower cost than traditional steel molds. This method is suitable for prototypes that need to closely mimic the final production parts in terms of material properties and structural integrity.
Production
3D Printing for Production
3D printing is increasingly viable for low to mid-volume production runs. Its ability to produce complex, custom parts without the need for expensive molds makes it ideal for small-batch production. Industries such as aerospace, medical, and custom consumer goods have successfully utilized 3D printing for production, leveraging its flexibility and speed for specialized applications.
Injection Molding for Production
Injection molding remains the gold standard for high-volume production due to its cost-effectiveness and speed. Once the design is finalized, durable steel molds can produce virtually unlimited quantities of parts with consistent quality. This method is advantageous for managing large orders and minimizing per-unit costs, making it the preferred choice for large-scale manufacturing.
Strategic Integration of Both Technologies
Hybrid Approaches
The future of manufacturing likely involves a strategic integration of both 3D printing and injection molding. By leveraging the rapid prototyping capabilities of 3D printing for initial design and small-batch production, manufacturers can maintain flexibility and speed. Once the design is finalized and production volumes increase, transitioning to injection molding ensures cost-efficiency and scalability. This hybrid approach allows manufacturers to optimize production cycles, reduce time to market, and achieve cost savings.
Conclusion and Next Steps
Choosing between 3D printing and injection molding—or integrating both—depends on several factors including production volume, part complexity, material requirements, and budget constraints. At JhTi, we specialize in optimizing your manufacturing processes by providing expert guidance and state-of-the-art solutions in both 3D printing and injection molding. For more detailed analysis and consultation on how to efficiently integrate these technologies into your production line, contact us.
Explore the potential of modern manufacturing techniques with JhTi and ensure your production capabilities are as innovative as they are efficient.
Subscribe to Our Newsletter!
Stay updated with the latest advancements in 3D printing and injection molding. Subscribe to our newsletter at titanium-supplier.com and never miss out on industry insights and technological breakthroughs.