Titanium 3D printing powder
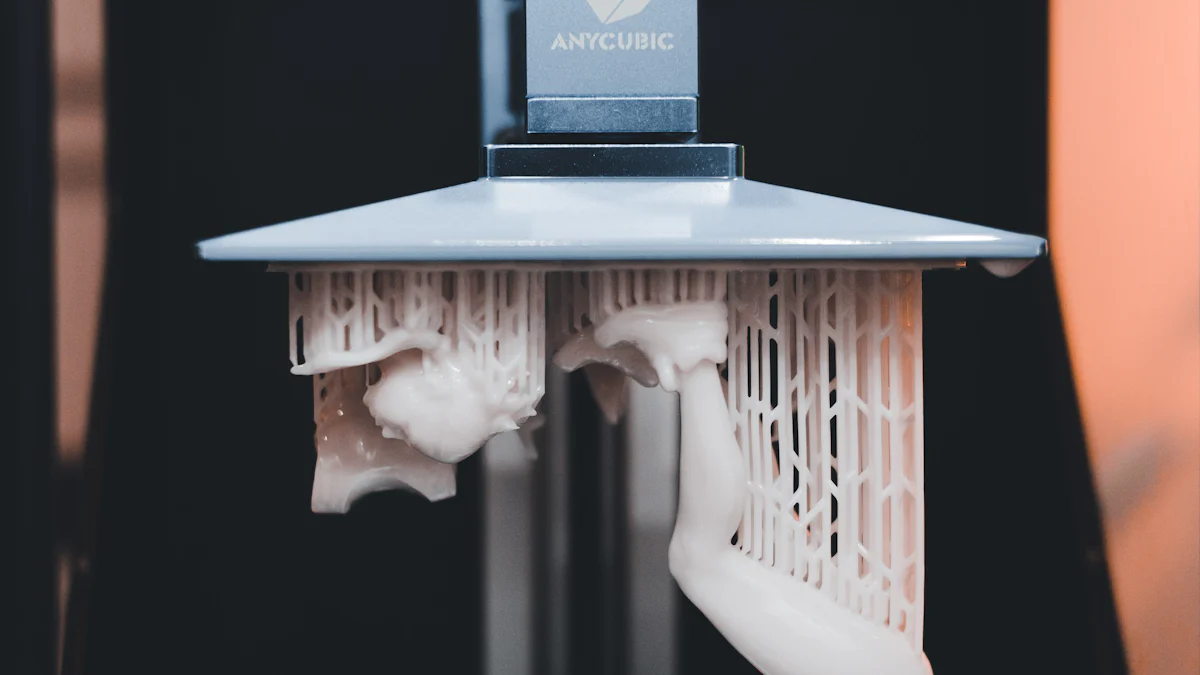
Titanium 3D printing powder stands as a cornerstone in additive manufacturing. This fine metallic powder transforms into robust, lightweight, and corrosion-resistant components. Its unique properties make it indispensable in industries like aerospace, automotive, and healthcare. The market for titanium powders is booming, with projections showing growth from 214millionin2023to214 million in 2023 to 214millionin2023to1.4 billion by 2032. This surge underscores the material’s value in high-performance applications. As I delve into this topic, I find the blend of strength and versatility in titanium truly remarkable.
Benefits of Titanium 3D Printing Powder
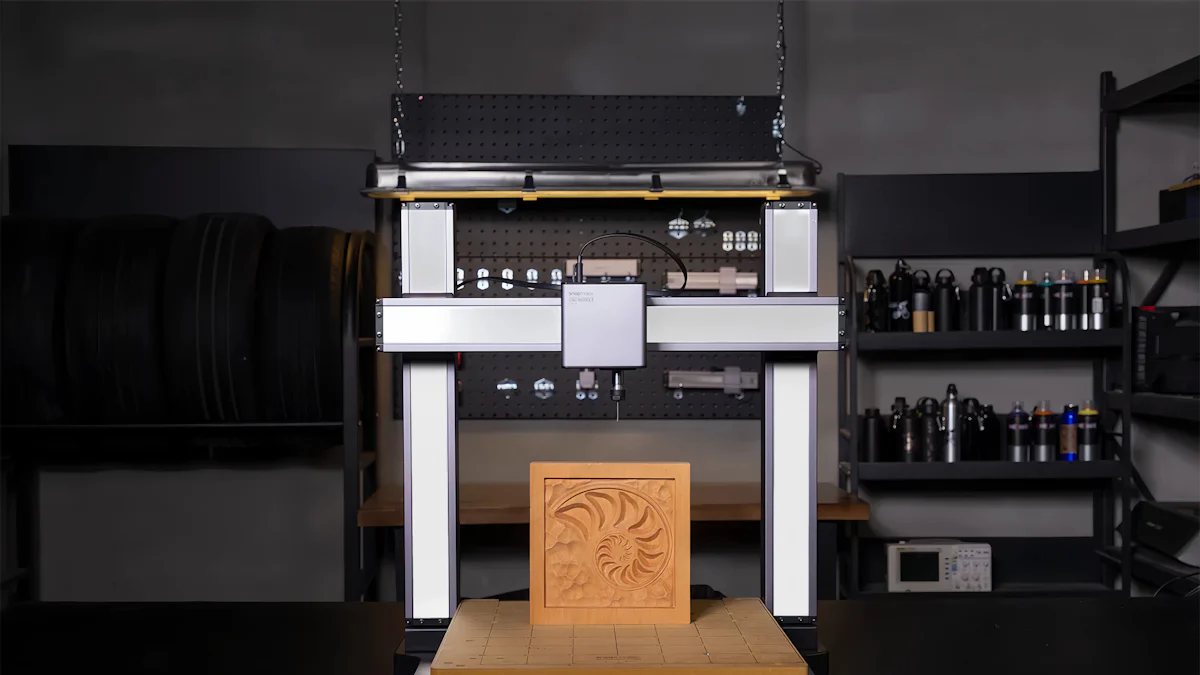
Titanium 3D printing powder offers remarkable advantages that make it a preferred choice in various industries. Its unique properties contribute to the creation of components that are not only strong but also lightweight and resistant to corrosion. Let me delve into these benefits in more detail.
Strength and Durability
Titanium 3D printing powder provides exceptional strength and durability. I find it fascinating how this material can withstand high stress and pressure, making it ideal for demanding applications. The aerospace industry, for instance, has approved 3D printed titanium parts for use in aircraft airframes and other critical components. This approval highlights the material’s ability to meet stringent performance standards. Moreover, new titanium alloys, such as titanium aluminides, enhance strength and ductility, allowing for the production of complex parts with superior performance.
Lightweight Properties
One of the standout features of titanium 3D printing powder is its lightweight nature. Despite its strength, titanium remains incredibly light, which is a significant advantage in industries where weight reduction is crucial. In aerospace and automotive sectors, reducing weight can lead to improved fuel efficiency and performance. I appreciate how this property allows engineers to design parts that are both strong and light, optimizing the overall functionality of the final product.
Corrosion Resistance
Corrosion resistance is another key benefit of titanium 3D printing powder. This property ensures that parts made from titanium can withstand harsh environments without degrading over time. In the medical industry, for example, titanium’s biocompatibility and resistance to corrosion make it an excellent choice for implants and prosthetics. The material’s ability to maintain its integrity in the human body underscores its suitability for medical applications. Additionally, the aerospace industry values titanium’s corrosion resistance for components exposed to extreme conditions.
Applications of Titanium 3D Printing Powder
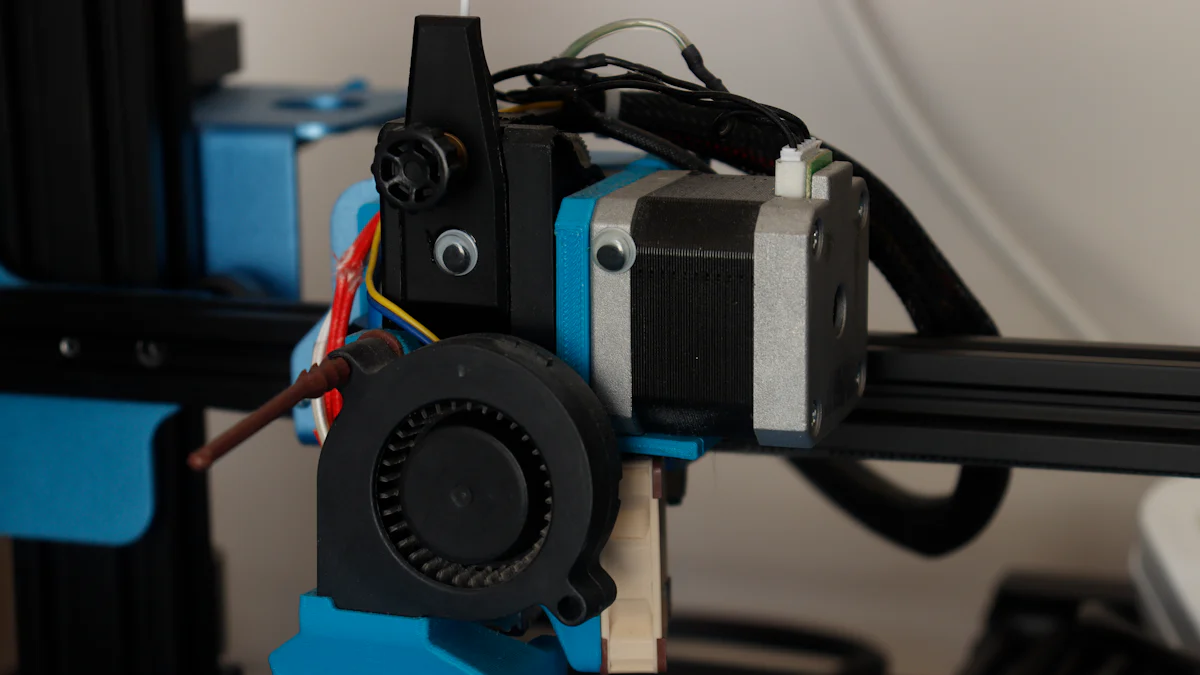
Titanium 3D printing powder has revolutionized several industries by enabling the creation of components that are both lightweight and strong. Its unique properties make it an ideal choice for high-performance applications. Let me explore how this technology is transforming the aerospace, medical, and automotive sectors.
Aerospace Industry
In the aerospace industry, the demand for materials that offer a high strength-to-weight ratio is paramount. Titanium 3D printing powder meets this need by allowing manufacturers to produce complex components that are lighter and more durable. I find it fascinating how this technology contributes to the development of fuel-efficient aircraft. By reducing the weight of jet engines and airframe components, aerospace companies can achieve significant improvements in fuel efficiency. This not only reduces operational costs but also minimizes the environmental impact of air travel.
Medical Industry
The medical industry benefits immensely from the versatility of titanium 3D printing powder. This technology has transformed the fabrication of custom-made implants and prosthetics. I am particularly impressed by its ability to create biocompatible components that integrate seamlessly with the human body. Titanium’s corrosion resistance ensures that these medical devices maintain their integrity over time, providing patients with reliable and long-lasting solutions. The precision of 3D printing also allows for the customization of implants to fit individual patients, enhancing the effectiveness of medical treatments.
Automotive Industry
Although the automotive industry has been slower to adopt titanium 3D printing due to cost considerations, its potential is undeniable. The ability to produce lightweight, high-strength components can significantly enhance vehicle performance and fuel efficiency. I see a growing interest in using titanium 3D printing powder to create parts that reduce the overall weight of vehicles. This reduction leads to improved acceleration, handling, and fuel economy. As the technology becomes more cost-effective, I anticipate a broader adoption within the automotive sector, driving innovation and sustainability.
How It Works
Understanding the process of 3D printing with titanium powder is crucial for appreciating its transformative impact on manufacturing. I find the intricacies of this technology fascinating, as it combines precision and innovation to create high-performance components.
3D Printing Process
The 3D printing process using titanium powder involves several key steps. Initially, a digital model of the desired component is created using computer-aided design (CAD) software. This model serves as the blueprint for the printing process. Once the design is finalized, the printer spreads a thin layer of titanium powder across the build platform. A high-powered laser then fuses the powder particles together, layer by layer, to form the solid object. This method, known as selective laser melting (SLM), ensures that each layer adheres perfectly to the previous one, resulting in a strong and cohesive structure.
I appreciate how this process allows for the creation of complex geometries that would be impossible to achieve with traditional manufacturing methods. The precision of the laser ensures that even the most intricate designs can be realized with exceptional accuracy. Additionally, the ability to control the density and porosity of the printed parts offers further customization options, enhancing the versatility of titanium 3D printing powder.
Types of Printers
Various types of printers are available for titanium 3D printing, each offering unique capabilities. Eplus3D’s precision metal additive manufacturing printers, such as the EP-M260 and EP-M150, are specifically designed to work with advanced titanium powders like Titanium Ti6Al4V / 3.7165. These printers provide exceptional strength, corrosion resistance, and biocompatibility, making them ideal for demanding applications in aerospace, medical, and other high-performance industries.
I find it intriguing how different printers cater to specific needs. Some models focus on speed, using coarse titanium powders to accelerate the printing process. Others prioritize precision, ensuring that every detail of the design is captured accurately. The choice of printer depends on the requirements of the project, whether it be the need for rapid prototyping or the production of highly detailed components.
Challenges and Considerations
Cost Implications
Titanium 3D printing presents significant cost challenges. The initial investment in industrial-grade Direct Metal Laser Sintering (DMLS) systems can reach six or seven figures. I find the production of titanium powder particularly costly due to the need for high purity and fine particle consistency. These processes demand substantial energy and advanced technology. Additionally, the environmental impact of titanium extraction and processing involves extensive safety and regulatory compliance, further increasing costs. Smaller businesses often face financial barriers, as the high price of titanium alloy powder and specialized equipment can deter adoption. While the long-term benefits of additive manufacturing are compelling, addressing these cost challenges is crucial for broader implementation.
Safety Concerns
Safety remains a critical consideration in titanium 3D printing. The high melting point of titanium poses challenges in managing uniform material sintering. I recognize the importance of ensuring safe handling and processing of titanium powder, as exposure can lead to respiratory issues. The production environment must adhere to strict safety protocols to protect workers from potential hazards. Additionally, the risk of fire and explosion due to the fine nature of titanium powder necessitates careful monitoring and control measures. Implementing comprehensive safety guidelines and training programs is essential to mitigate these risks and ensure a secure working environment.
Technical Challenges
Technical challenges in titanium 3D printing are multifaceted. The high melting point of titanium requires specialized equipment capable of achieving and maintaining the necessary temperatures for effective sintering. I find the need for skilled personnel to operate and maintain this equipment crucial, as the technology demands precision and expertise. Ensuring uniform material sintering and achieving consistent quality across printed components can be complex. The intricacies of the process require continuous monitoring and adjustments to optimize outcomes. Overcoming these technical hurdles is vital to fully harness the potential of titanium 3D printing and drive innovation in high-performance industries.
Titanium 3D printing powder revolutionizes manufacturing with its unique benefits and applications. It enables the creation of lightweight, strong, and corrosion-resistant components, transforming industries like aerospace, medical, and automotive. Understanding the challenges, such as cost and safety, remains crucial for successful implementation. The future holds immense potential for advancements in this technology. As it evolves, I anticipate even greater innovations and efficiencies, solidifying its role as a game-changer in engineering and beyond.
FAQ
What is Titanium 3D Printing Powder?
Titanium 3D printing powder consists of fine metallic particles used in additive manufacturing. It transforms into strong, lightweight, and corrosion-resistant components. This powder is essential for industries like aerospace, automotive, and healthcare due to its unique properties.
How much does titanium powder for 3D printing cost?
The cost of titanium powder for 3D printing varies based on factors like purity and particle size. Generally, it is more expensive than other metal powders due to its high-quality requirements. For a comprehensive guide on costs and other aspects, I recommend exploring resources that cover composition, properties, and applications in detail.
What is the best titanium alloy for 3D printing?
Titanium Ti6Al4V, also known as Grade 5, is the most commonly used alloy for 3D printing. It offers an excellent balance of strength, weight, and corrosion resistance. This alloy is ideal for creating complex geometries in demanding applications such as aerospace and medical industries.
How does the 3D printing process work with titanium powder?
The process begins with a digital model created using CAD software. A printer spreads a thin layer of titanium powder on the build platform. A high-powered laser or electron beam fuses the particles layer by layer, forming a solid object. This method, known as selective laser melting (SLM) or electron beam melting (EBM), ensures precision and strength.
What are the safety concerns associated with titanium 3D printing?
Handling titanium powder requires strict safety protocols. The fine particles pose respiratory risks if inhaled. Additionally, the powder’s flammable nature necessitates careful monitoring to prevent fire hazards. Implementing comprehensive safety guidelines is crucial to ensure a secure working environment.
Can titanium 3D printing be used for medical implants?
Yes, titanium 3D printing is widely used for medical implants. Its biocompatibility and corrosion resistance make it suitable for creating custom-made implants and prosthetics. The precision of 3D printing allows for tailored solutions that integrate seamlessly with the human body.
What are the technical challenges in titanium 3D printing?
Technical challenges include achieving uniform material sintering and maintaining consistent quality across printed components. The high melting point of titanium requires specialized equipment and skilled personnel. Continuous monitoring and adjustments are necessary to optimize outcomes.
How does titanium 3D printing benefit the aerospace industry?
Titanium 3D printing allows for the production of lightweight, durable components with complex geometries. In the aerospace industry, this technology contributes to fuel-efficient aircraft by reducing the weight of jet engines and airframe components, leading to improved performance and reduced operational costs.
Is titanium 3D printing cost-effective for the automotive industry?
While initially costly, titanium 3D printing holds potential for the automotive industry. The ability to produce lightweight, high-strength components can enhance vehicle performance and fuel efficiency. As technology becomes more cost-effective, broader adoption is anticipated, driving innovation and sustainability.
What future advancements can we expect in titanium 3D printing?
I foresee significant advancements in titanium 3D printing, including improved cost-effectiveness and enhanced material properties. As technology evolves, I anticipate greater innovations and efficiencies, solidifying its role as a game-changer in engineering and beyond.