Titanium 3D printing is profoundly transforming product design with its unique capabilities. This method offers numerous advantages, particularly where the properties of titanium are essential. Here’s an enriched discussion on the benefits of titanium 3D printing, complete with supporting data and examples:
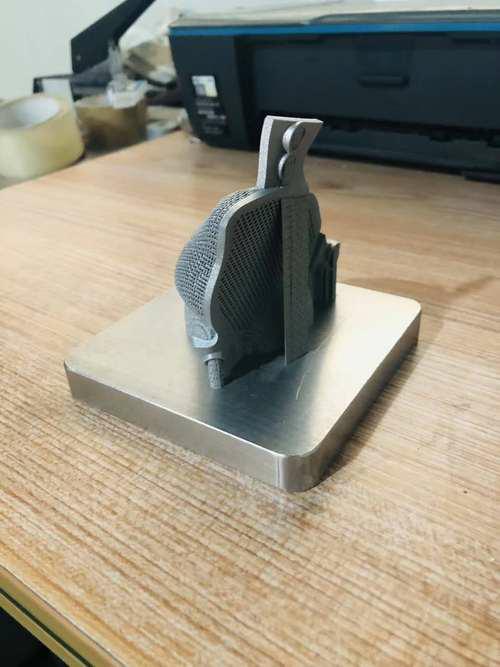
1. Customization and Complexity
The direct fabrication of complex geometric forms, typical in sectors such as medical implants, aerospace, and motorsports, is a hallmark of titanium 3D printing. For instance, in the medical sector, the production of customized orthopedic implants through traditional methods can be costly and time-consuming. Titanium 3D printing, however, allows for the creation of implants tailored to the patient’s anatomy, potentially improving recovery times and surgical outcomes. Studies have shown that customized implants can reduce the duration of surgery by approximately 25%, as they fit better and require less intraoperative adjustments.
2. Reduced Weight and Enhanced Performance
The aerospace industry greatly benefits from the weight reduction capabilities of titanium 3D printing. For example, GE Aviation reported a 25% weight reduction in parts produced for its LEAP jet engines, directly translating into improved fuel efficiency and reduced emissions. The specific use of lattice structures unique to 3D printing can decrease material usage by up to 60% while retaining structural integrity.
3. Material Efficiency and Sustainability
Material utilization in traditional titanium machining can be as low as 10%, with the rest becoming scrap. In contrast, titanium 3D printing can achieve material utilization rates of over 90%. This efficiency not only reduces the cost of materials but also minimizes the environmental impact associated with the extraction and processing of titanium.
4. Rapid Prototyping to Production
The transition from prototype to production is significantly expedited with titanium 3D printing. Prototypes that once took months to produce can now be printed in days, drastically reducing development cycles. In sectors like aerospace, where prototyping typically incurs high costs and lengthy timelines, the ability to rapidly produce prototypes can significantly accelerate innovation cycles.
5. Enhanced Mechanical Properties
Titanium printed parts often exhibit superior mechanical properties due to the precise control over microstructural characteristics achievable with 3D printing. For instance, the selective laser melting (SLM) process can be optimized to enhance the hardness and fatigue resistance of titanium alloys. Research indicates that titanium parts manufactured via SLM can achieve up to a 15% increase in tensile strength compared to those produced through traditional forging.
6. Integration of Functionality
3D printing allows for the integration of additional functionalities within a single print cycle, such as embedded sensors or internal channels for fluids. This integration is crucial for applications in high-performance sectors. For example, in aerospace, integrating cooling channels directly into turbine blades can lead to improved engine efficiency and reduced maintenance needs.
By harnessing the capabilities of titanium 3D printing, industries are able to push the boundaries of what’s achievable in terms of design, efficiency, and functionality. The data and examples provided highlight the transformative impact of this technology, making it a pivotal tool in modern manufacturing and product development.
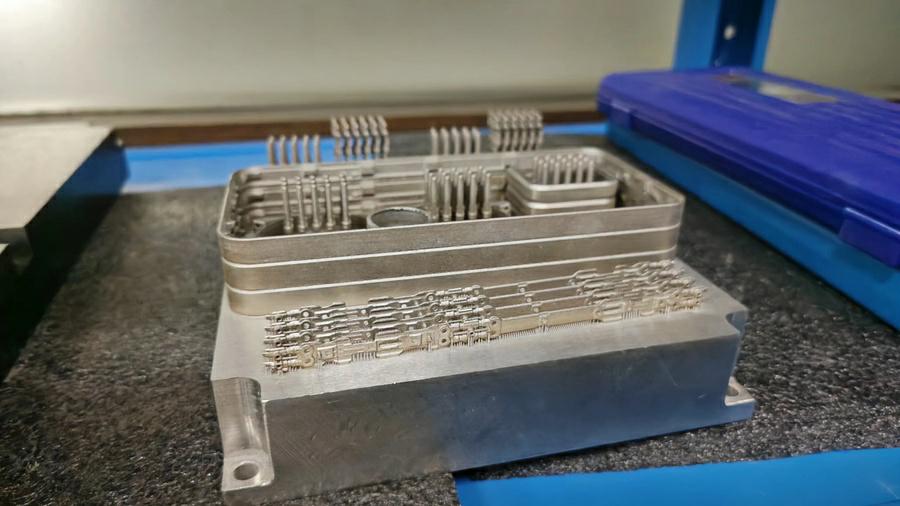