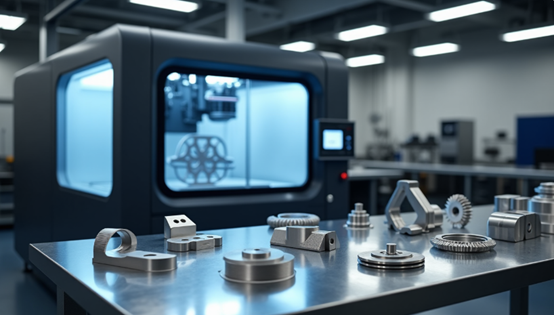
Aluminum 6061 reaches 290 MPa tensile strength through 3D printing. This breakthrough has revolutionized metal additive manufacturing. Ford Motor Company’s qualification of binder jet technology showed that 3D printed aluminum components now deliver 99% density. These components match properties of traditional manufacturing methods.
The aluminum alloy stands out with its excellent mechanical properties. It offers good thermal conductivity and resists corrosion well. These features make it perfect for aerospace, automotive, and medical uses. 3D printed aluminum parts weigh very little at 2.8 g/cm³ density. They still maintain a strong 240 MPa yield strength, especially when you have aerospace or automotive applications in mind.
This piece guides you through everything in 3D printing Aluminum 6061. You’ll learn about material preparation, optimal print settings, and post-processing needs to achieve perfect results.
Essential Properties of 3D Printable Aluminum 6061
“It is an alloy that combines aluminum with magnesium and silicon, providing a good balance of strength, corrosion resistance and machinability.” — Dr. Slade Gardner, Former Advanced Manufacturing Fellow at Lockheed Martin Space Systems Company
The success of 3D printing with Aluminum 6061 powder depends on its exact chemical makeup. The mix contains aluminum (97.9%), magnesium (1.0%), and silicon (0.6%) as its key elements. Copper (0.28%) and chromium (0.2%) are also part of the alloy, along with trace amounts of other elements.
Chemical Composition Requirements
You need to follow composition standards carefully to get consistent material properties. The powder must meet ASTM International’s ASTM B216 specifications. Keeping oxygen levels under 500 ppm is crucial to stop too much oxide from forming during printing.
Mechanical Property Specifications
3D printed Aluminum 6061’s mechanical properties match those from traditional manufacturing methods. The material has a density range of 2.5-2.9 g/cm³ and reaches a Vickers hardness of 107. Its thermal conductivity hits 167 W/m-K, which means printed parts can dissipate heat well.
The temper grade plays a big role in determining strength characteristics. T6 heat-treated components show these properties:
Property | Value |
Ultimate Tensile Strength | <citation index=”26″ link=”https://www.americanelements.com/aluminum-6061-alloy-powder” similar_text=”Tensile Strength |
Thermal Expansion | <citation index=”26″ link=”https://www.americanelements.com/aluminum-6061-alloy-powder” similar_text=”Thermal Expansion |
Electrical Resistivity | <citation index=”26″ link=”https://www.americanelements.com/aluminum-6061-alloy-powder” similar_text=”Electrical Resistivity |
Specific Heat | <citation index=”26″ link=”https://www.americanelements.com/aluminum-6061-alloy-powder” similar_text=”Specific Heat |
Powder Characteristics for Optimal Results
Particle size distribution has a huge impact on print quality and final part properties. The best range lies between 15 and 100 micrometers. Finer powders (15-45 micrometers) give you a better surface finish but might not flow as well. Coarser powders (45-100 micrometers) flow better but leave rougher surfaces.
The powder’s apparent density and flow properties must meet ASTM B854 and ASTM B212 standards. These standards help ensure steady material feed during printing. Your powder should be free from clumps and have very low oxygen content to keep its quality intact.
Pre-Processing Steps for Aluminum 6061
The quality of 3D prints and workplace safety depend on how you store and handle Aluminum 6061 powder. These microscopic metal particles smaller than 100 µm need strict protocols to prevent hazards.
Powder Storage Guidelines
Aluminum 6061 powder just needs controlled environments to stay in good condition. You should keep the powder in vacuum-sealed containers with silica gel pouches to minimize oxidation and moisture absorption. Stainless steel jars under atmospheric pressure work best for long-term storage.
Storage containers should be:
- Away from heat sources and spark-generating equipment
- Protected with inert gas or vacuum sealing
- Equipped with moisture indicators
- Labeled with appropriate hazard warnings
Material Handling Safety Protocols
Aluminum 6061 powder’s fine nature creates specific risks. We need to watch out for dust clouds and potential fire hazards. A Class D fire extinguisher should always be within reach during handling operations.
Personal Protective Equipment (PPE) requirements include:
- Long pants and closed-toe shoes
- Laboratory coat
- Nitrile, butyl, or neoprene gloves covering coat cuffs
- Safety goggles or full-face respirator
- Half-face or full-face respirator with P100 filters
Good ventilation and properly grounded equipment are essential for handling operations. All powder transfers should happen in designated areas with proper containment systems. Workers need to handle materials carefully to avoid creating dust clouds.
Aluminum powder’s reactivity means you need specialized vacuum systems. Only vacuums designed for metal powders are safe to use, as regular units can cause fires or explosions. These systems must stay electrically grounded during operation.
Bulk quantities work well in palletized plastic containers of 25 kg capacity or steel drums up to 1-ton super sacks. Research quantities typically need special packaging under argon or vacuum conditions.
Optimizing Print Parameters
The success of Aluminum 6061 3D printing depends on precise control of print parameters. Line laser energy density, calculated as P/(vhd) where P is laser power, v is scanning speed, h is hatch spacing, and d is layer thickness, directly influences part density.
Layer Height vs Surface Quality
Your choice of layer height affects both print time and surface finish. Finer layers between 15-45 micrometers create better surface finish compared to thicker layers. A layer height of 0.3mm combined with a print speed of 50mm/s delivers better mechanical properties.
Temperature Control Requirements
Proper temperature management plays a vital role in successful prints. Close-loop control systems must maintain minimum deposition temperature to reduce thermal gradients. Al 6061 shows improved results with a continuous furnace approach compared to batch sintering. Pyrometers monitor the maximum deposition temperature of 417°C to maintain optimal material flow.
Power Settings for Different Features
Laser power substantially affects part density and mechanical properties. The optimal processing window needs:
Parameter | Range |
Laser Power | 200-250 W |
Scanning Speed | 1000 mm/s |
Hatch Spacing | 140 µm |
Energy Density | 44-50 J/mm³ |
These settings achieve relative densities of 99.8%. Part’s nanohardness increases with laser power initially but declines at higher values.
Speed vs Quality Trade-offs
Part quality and mechanical properties depend directly on print speed. Higher scanning frequencies above 150 Hz show reduced crack sensitivity compared to slower speeds. You can achieve the best balance between speed and quality with an energy density range of 44-50 J/mm³. Porosity drops from 5% to below 1% when energy density increases from 25.51 to 44.64 J/mm³.
The build process needs active control of oxygen and humidity levels. Low oxygen content and consistent humidity control in the powder bed prevent build-killing powder-bed defects.
Post-Processing Requirements
Raw 3D printed Aluminum 6061 components become high-performance parts through controlled thermal and mechanical treatments. Hot Isostatic Pressing (HIP) emerges as the main method that applies high temperature and pressure to reach density levels of 99.99%.
Heat Treatment Specifications
Stress relief starts the thermal post-processing sequence before solution treatment and aging. The components undergo HIP treatment at 1250°C with 145 MPa pressure to reduce porosity and texture anisotropy. This process improves mechanical properties and boosts tensile strength to 90% while raising fatigue strength to 75% of wrought material values.
The optimal heat treatment sequence involves:
Process Stage | Parameters | Duration |
Stress Relief | 250°C | 12-14 hours |
Solution Treatment | 1000°C | 40 minutes |
Aging | 325°C | 18 hours |
HIP treatment changes the grain structure from elongated columnar to equiaxed, which eliminates anisotropy. The process reduces internal voids, minimizes blowholes, and closes microcracks through plastic deformation under high pressure.
Surface Finishing Options
We improved specific roughness and performance requirements through surface enhancement techniques. Laser polishing reduces surface roughness by up to 95% compared to as-built specimens. The surface peaks melt selectively to increase surface reflectivity.
Alternative finishing methods include:
- Bead blasting for uniform surface texture
- Chemical treatments for enhanced corrosion resistance
- Conventional machining for dimensional accuracy
- Shot peening for improved fatigue resistance
Application requirements determine the finishing method selection. Laser shock peening improves surface hardness through local grain refinement. The final surface quality depends on the overlap percentage between laser scans.
Surface treatments improve both esthetics and functional properties. Post-processed components show better flow rates in internal channels and higher dimensional accuracy. These finishing operations help transform raw 3D printed parts into fully functional, refined products.
Quality Control Measures
“AlSi10Mg is an aluminum alloy that is typically used in casting applications and aluminum metal 3D printing. It has excellent temperature and corrosion resistance which makes it ideal for gearboxes, housings, or brackets that get exposed to high loads.” — David Iacovelli, Regional Director at EOS North America
Quality control plays a vital role in aluminum 6061 3D printing. The manufacturing process needs constant monitoring to prevent defects and confirm part integrity.
Density Testing Methods
Print quality and structural integrity depend on precise density measurements. X-ray imaging inspections can detect internal pores and defects with 2 µm spatial resolution. Parts that are printed correctly reach 99.9% relative density at an energy density of 50 J/mm³. Polished samples show 0.1–1% less porosity than as-built parts.
Mechanical Property Validation
Testing confirms how well parts perform and their reliability. Tensile tests show that properly printed Al6061 components achieve:
- Ultimate tensile strength of 310 MPa
- Yield strength of 240 MPa
- Elongation at break of 16.7%
Microhardness values show small variations of 8.8% along the build direction. All the same, specimens from top sections show higher ultimate stress levels than lower regions. The tensile properties stay consistent across the part’s width.
Dimensional Accuracy Checks
Part functionality depends on precise dimensional control. 3D printed aluminum typically maintains ±200µ tolerance, though optimal settings can achieve 0.2% accuracy. These dimensional variations depend on:
Parameter | Impact Range |
Energy Density | 76.8 J/mm³ for lowest tolerance |
Surface Flatness | Improves with higher hatch spacing |
Hole Diameter | Minimum 1mm for powder removal |
Complex and irregular holes need extra inspection to remove powder completely. Small adjustments through traditional mechanical methods work well enough unless perfectly straight holes are needed.
Common Defect Prevention
Understanding why defects occur helps prevent them. Fusion-based processes can lead to anisotropy and solidification-related defects. Large spatters pose a big challenge and can cause:
- Recoater blockage
- Powder bed non-uniformity
- Surface pits
- Lack of fusion porosity
Surface roughness measurements show that proper parameter control reduces Ra from 20 ± 3 µm to 2.1 ± 0.2 µm. The maximum height difference (Rm) drops by 89% with optimal processing conditions. Adding nanoparticles to the powder bed helps control laser-powder interaction, which eliminates large spatters and improves consistency.
The build process requires constant monitoring of oxygen levels and humidity. The powder bed needs very low oxygen content to prevent powder-bed defects that could ruin the build and ensure consistent part quality.
Conclusion
Aluminum 6061 delivers remarkable results in metal 3D printing. Manufacturers can achieve parts with 99.9% density and mechanical properties that match traditional manufacturing components. This happens through careful attention to powder characteristics, precise parameter control, and full post-processing.
Several critical factors determine your success with this versatile alloy:
- You must strictly follow powder storage and handling safety protocols
- Your print parameters need precise control, especially in the 44-50 J/mm³ energy density range
- A complete post-processing routine includes HIP treatment at 1250°C
- Quality control requires density testing and mechanical validation
3D printed Aluminum 6061’s combination of 310 MPa tensile strength, excellent thermal conductivity, and superior corrosion resistance makes it perfect for aerospace, automotive, and medical applications. This piece shows that optimal results come from careful attention to each printing stage. The process starts with material preparation and ends with final quality validation.
This all-encompassing approach will give a consistent output of high-quality aluminum components. These parts meet or exceed industry standards while keeping additive manufacturing’s flexibility. Metal 3D printing’s future looks promising as manufacturers keep refining these processes. They continue to find new applications for this versatile alloy.
FAQs
Q1. Is it possible to 3D print Aluminum 6061? Yes, Aluminum 6061 can be 3D printed using advanced metal additive manufacturing techniques like laser powder bed fusion (LPBF) or binder jetting. However, it requires specialized industrial equipment and expertise to achieve high-quality results.
Q2. What are the key properties of 3D printed Aluminum 6061? 3D printed Aluminum 6061 exhibits excellent mechanical properties, including a tensile strength of 310 MPa, yield strength of 240 MPa, and elongation at break of 16.7%. It also offers good thermal conductivity and corrosion resistance, making it suitable for aerospace, automotive, and medical applications.
Q3. How does the cost of 3D printing Aluminum 6061 compare to traditional manufacturing methods? 3D printing Aluminum 6061 can be more expensive than traditional manufacturing methods for simple geometries. However, it becomes cost-effective for complex parts or low-volume production runs where tooling costs for traditional methods would be prohibitive.
Q4. What post-processing steps are required for 3D printed Aluminum 6061 parts? Post-processing typically involves stress relief, solution treatment, and aging. Hot Isostatic Pressing (HIP) is often used to achieve near-perfect density. Surface finishing techniques like laser polishing or bead blasting may be applied to improve surface quality and dimensional accuracy.
Q5. How does the quality of 3D printed Aluminum 6061 parts compare to traditionally manufactured ones? When properly processed, 3D printed Aluminum 6061 parts can achieve 99.9% density and mechanical properties comparable to traditionally manufactured components. However, careful attention to print parameters, post-processing, and quality control is essential to ensure consistent results.