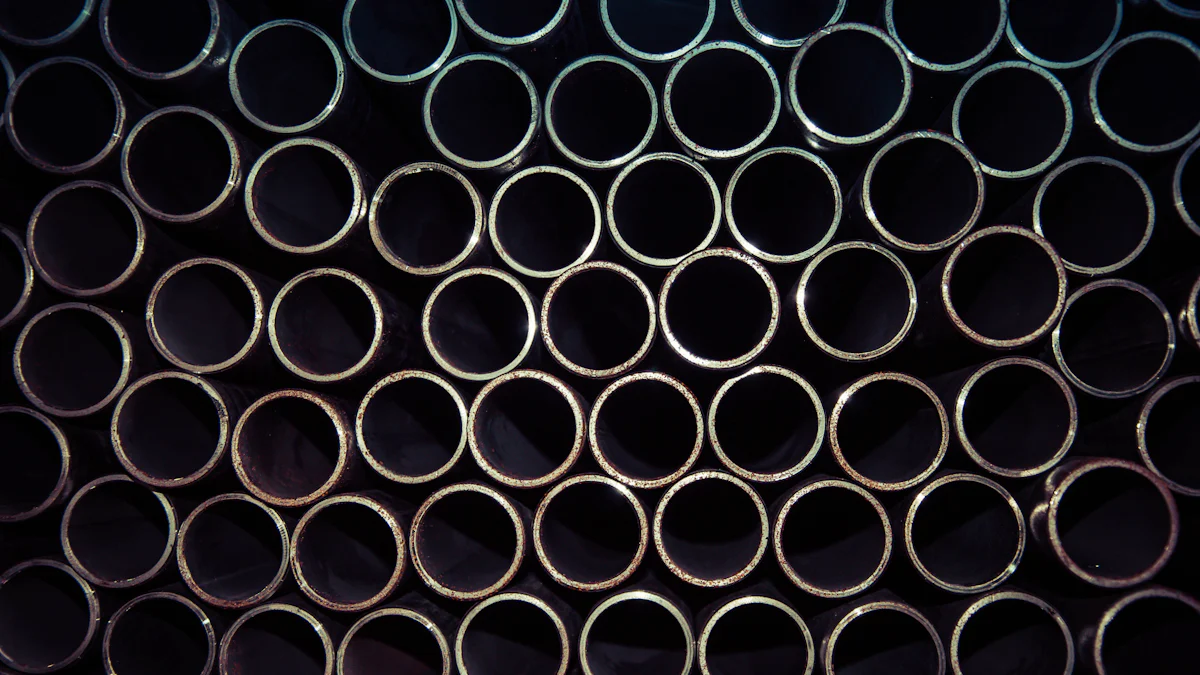
When I think about materials that revolutionize industries, I often wonder why titanium stands out. Its strength-to-weight ratio surpasses most metals, making it indispensable in aerospace and defense. Industries like medical and luxury goods also rely on titanium for its biocompatibility and corrosion resistance. Rapid industrialization in Asia continues to drive its global demand.
Key Takeaways
- Titanium is strong but light, perfect for making aircraft fuel-efficient.
- It resists rust, so it works well in oceans and medicine.
- Titanium is safe for the body, helping implants work better for patients.
Why Titanium is Unique
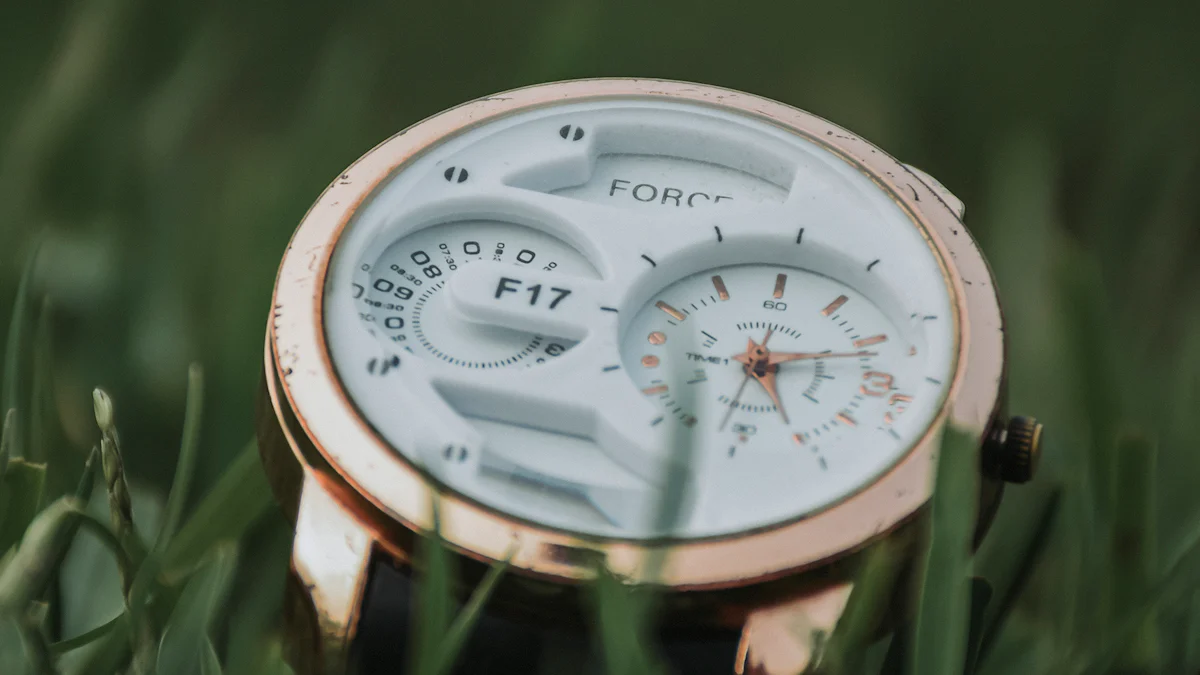
Strength-to-Weight Ratio
When I think about why titanium is so widely used, its strength-to-weight ratio immediately comes to mind. Titanium offers exceptional strength while remaining lightweight, making it ideal for applications where weight reduction is critical. For example, in aerospace engineering, titanium enables the construction of fuel-efficient aircraft that can carry heavier payloads without compromising performance. Engineers often choose titanium because its lightweight nature reduces operational costs and enhances safety under high-stress conditions.
- Fuel efficiency improves due to reduced vehicle weight.
- Structures can support heavier loads without significant weight penalties.
- Maintenance requirements decrease, extending the service life of components.
This balance of strength and weight allows for innovative designs that push the boundaries of technology.
Corrosion Resistance
Titanium’s corrosion resistance is another reason why titanium remains indispensable in many industries. Its surface forms a stable oxide film when exposed to oxygen, acting as a protective barrier against corrosive agents. This film is self-healing, meaning it regenerates quickly if damaged.
- Titanium resists pitting and stress corrosion cracking in chloride-rich environments, such as seawater.
- It performs exceptionally well in aggressive chemical environments, including acidic and saline conditions.
Evidence | Description |
---|---|
Passive Film Formation | Titanium alloys form a dense passive film in oxygen-rich environments. |
Self-Healing Properties | The oxide layer regenerates quickly, maintaining corrosion resistance. |
This unique property makes titanium a preferred material for marine, chemical, and medical applications.
Biocompatibility
Titanium’s biocompatibility sets it apart in the medical field. Since the 1950s, it has been used in dental and orthopedic implants due to its ability to integrate with human bone, a process called osseointegration. This property enhances patient outcomes and quality of life. Recent advancements, such as hydroxyapatite coatings, further improve titanium’s bioactivity and integration with bone tissue.
- Titanium promotes bone adhesion without causing inflammation.
- Coatings enhance bioactivity and bacteriostatic properties, ensuring better implant integration.
Its compatibility with living tissues explains why titanium is a cornerstone material in healthcare.
High Temperature Tolerance
Titanium’s ability to withstand high temperatures is another reason why titanium excels in demanding environments. Titanium alloys maintain their mechanical properties at temperatures exceeding 500°C (932°F), outperforming conventional steels. This makes titanium indispensable in aerospace and power generation industries.
Application | Operating Temperatures | Component Examples |
---|---|---|
Aerospace | Up to 1100°F (593°C) | Turbine blades, compressor discs |
Power Generation | 800°F to 1100°F (427°C to 593°C) | Steam turbine blades, heat exchangers |
Chemical Processing | Up to 1000°F (538°C) | Reactors, heat exchangers, piping systems |
Its high-temperature tolerance ensures reliability and performance in extreme conditions, solidifying its role in modern engineering.
Applications of Titanium
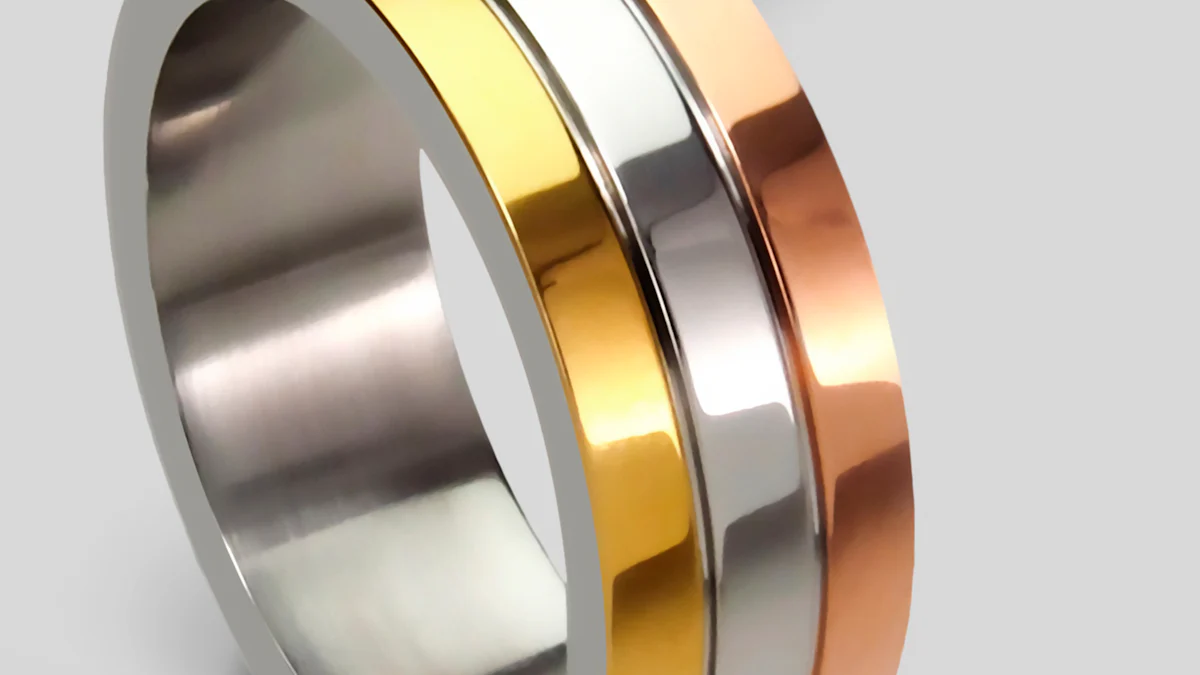
Aerospace and Defense
I find titanium indispensable in aerospace and defense due to its unique properties. It constitutes about 20% of the weight of advanced commercial aircraft, and the aerospace industry consumes nearly 40% of global titanium production. Its strength-to-weight ratio allows engineers to design lightweight yet durable components, improving fuel efficiency and payload capacity.
In defense, titanium plays a critical role in:
- Military fighter aircraft and engines
- Naval platforms
- Military ground vehicles
- Armoring military vehicles and naval ships
Advantage | Description |
---|---|
Strength-to-weight ratio | Enables lightweight armor, enhancing maneuverability and safety. |
Corrosion resistance | Reduces maintenance needs, extending equipment lifespan. |
Durability | Ensures resilience in harsh environments, improving operational efficiency. |
Recent advancements, such as additive manufacturing, have revolutionized titanium’s use in aerospace. Engineers now create intricate components with minimal waste, pushing the boundaries of innovation.
Medical and Healthcare
Titanium’s biocompatibility makes it a cornerstone in healthcare. I’ve seen it used in implants like hip prostheses and dental screws. Ti-6Al-4V, a popular alloy, offers excellent mechanical strength for orthopedic applications. Pure titanium grades are ideal for surgical plates and screws due to their compatibility with human tissue.
Type of Implant | Description |
---|---|
Ti-6Al-4V | Used for hip and knee prostheses, offering high strength. |
Pure Titanium | Ideal for reconstructive surgery, known for biocompatibility. |
Ti-6Al-7Nb | Provides superior corrosion resistance for specific surgeries. |
Nitinol-55 | Exhibits shape memory, used in cardiac and dental applications. |
These implants integrate seamlessly with bone, ensuring long-term success and improving patient outcomes.
Automotive and Transportation
Titanium enhances vehicle performance and safety. Its strength-to-weight ratio reduces overall vehicle weight, improving fuel efficiency. I’ve noticed its corrosion resistance extends the lifespan of automotive components, while its durability ensures safety under high-stress conditions.
- Lightweight nature boosts fuel efficiency.
- High strength improves durability and safety.
- Corrosion resistance enhances component longevity.
This combination allows manufacturers to create innovative designs without compromising strength or reliability.
Luxury Goods and Consumer Products
Titanium’s appeal extends to luxury goods. I’ve seen it used in high-end watches and sporting equipment. For example, 3D-printed titanium watches made from recycled materials offer durability and sustainability. Titanium bike frames, with their superior strength-to-weight ratio, improve performance and longevity.
Luxury Good Type | Example | Value Enhancement |
---|---|---|
Watches | 3D-printed titanium watches | Durable and sustainable, made from recycled titanium. |
Sporting Equipment | Titanium bike frames | Lightweight and strong, enhancing performance. |
Its unique properties elevate the value and functionality of these products, making titanium a preferred choice in the luxury market.
Challenges of Using Titanium
High Cost of Production
I’ve observed that titanium’s high production cost stems from several factors. Its rarity plays a significant role, as titanium doesn’t occur in pure form and requires complex extraction processes. The refining process demands substantial energy and specialized equipment, which further drives up costs. Additionally, strict quality control standards are essential for critical applications like aerospace and medical, adding to the overall expense.
- Titanium’s chemical extraction from ore is expensive and wasteful.
- Processing titanium ingots generates significant material waste.
- Its reactivity at high temperatures complicates production, increasing costs.
Innovations like the Joule Form™ process and FAST-forge technology are helping to address these challenges. For instance, FAST-forge reduces the manufacturing steps from 40 to just 2, potentially cutting costs by up to 50%. These advancements make titanium more accessible for industries that rely on it.
Difficulty in Machining and Fabrication
Working with titanium presents unique challenges. I’ve noticed that its properties, while advantageous in applications, complicate machining and fabrication. Titanium’s poor thermal conductivity causes heat to concentrate at the cutting edge, leading to rapid tool wear. Additionally, its tendency to harden during machining can result in poor surface finishes and tool chipping.
Challenge | Description | Mitigation Strategy |
---|---|---|
Heat Buildup | Heat concentrates at the tool edge | Use high-pressure coolant, reduce speeds |
Rapid Tool Wear | Tools degrade quickly | Use coated carbide or PCD tools |
Work Hardening | Material hardens after initial passes | Optimize cutting parameters |
Poor Surface Finish | Chatter and deformation affect quality | Increase machine rigidity, adjust feeds |
Tool Chipping | Brittle tools crack under high stress | Use tougher tool materials, optimize depth |
Innovations like additive manufacturing (3D printing) are transforming titanium fabrication. This technique reduces waste and allows for the creation of complex geometries, making it a game-changer for industries like aerospace.
Limited Availability and Resource Constraints
Titanium’s availability directly impacts its cost and usage. Global reserves include approximately 690 million metric tons of ilmenite and 55 million metric tons of rutile. However, mining challenges, strict environmental regulations, and geopolitical tensions, such as the Ukraine-Russia conflict, have disrupted supply chains.
- Aerospace and automotive industries face price volatility due to supply shortages.
- Increased demand has intensified competition for limited resources.
To mitigate these issues, industries are exploring resource diversification, recycling initiatives, and alternative materials. Sustainable mining practices and energy-efficient production methods are also gaining traction to address environmental concerns. Despite these efforts, titanium’s limited availability remains a significant challenge, underscoring why titanium continues to command a premium in global markets.
Titanium’s unmatched properties make it a cornerstone of modern innovation. Its strength-to-weight ratio, corrosion resistance, and biocompatibility have transformed industries like aerospace, medical, and automotive. Recent advancements in alloys and manufacturing processes are expanding its applications, including green technology and smart implants. As production technologies evolve, titanium’s role in shaping the future will only grow.
FAQ
What makes titanium different from other metals?
Titanium combines high strength, low weight, and excellent corrosion resistance. Unlike steel or aluminum, it withstands extreme conditions while remaining biocompatible, making it ideal for aerospace, medical, and luxury applications.
Why is titanium so expensive?
Titanium’s cost stems from its complex extraction and refining processes. Mining challenges, energy-intensive production, and strict quality standards for aerospace and medical use further drive up its price.
Can titanium be recycled?
Yes, titanium is 100% recyclable. Recycling reduces waste and energy consumption, making it a sustainable option for industries like aerospace and automotive that rely heavily on this valuable material.
💡 Tip: Recycling titanium not only conserves resources but also lowers production costs, making it more accessible for future innovations.