
Can heart valves be 3D printed? 3D printing has revolutionized medicine, offering the potential to create heart valves tailored to individual patients using advanced materials. Despite this promise, challenges persist, including biocompatibility issues, durability concerns, and regulatory barriers that hinder widespread clinical use. Additionally, manufacturing processes require further refinement to ensure these valves are both cost-effective and accessible to all.
Key Takeaways
- 3D printing makes custom heart valves for each patient. This improves surgeries and lowers risks of problems.
- Picking the right materials is very important. Safe materials help the body accept the valve and last longer.
- 3D-printed heart valves show promise but face challenges. Issues like strength, safety, and approval need solving for common use.
How 3D Printing Works for Heart Valves
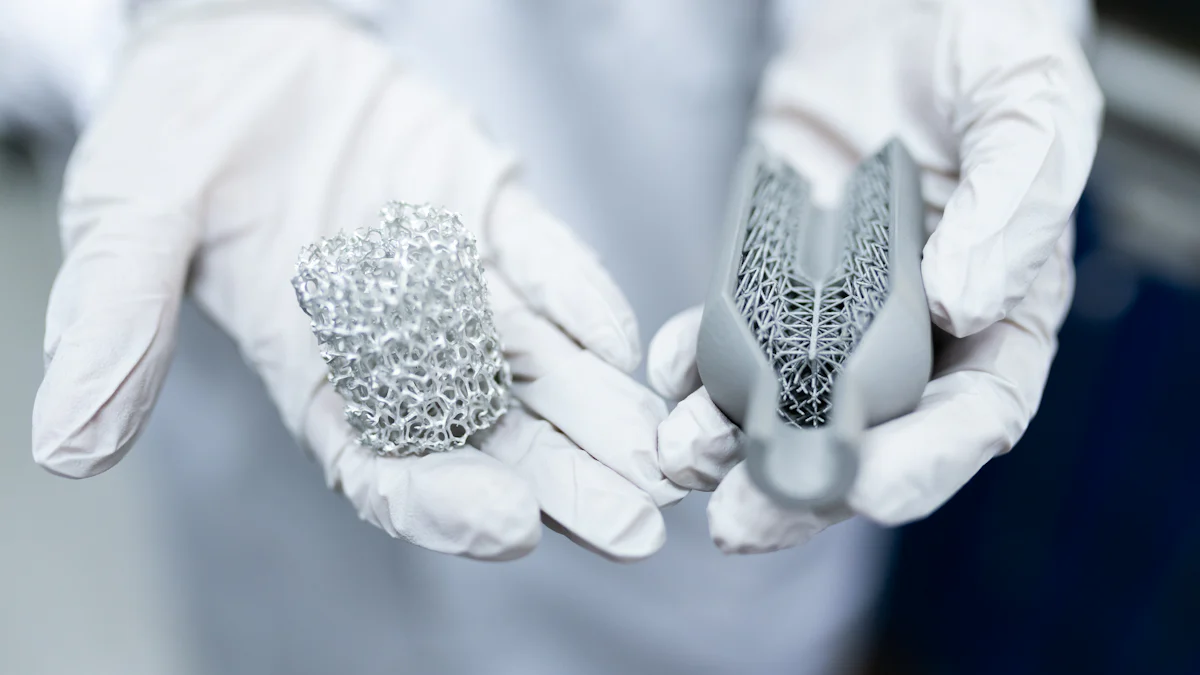
The process of 3D printing heart valves
Creating 3D-printed heart valves involves a meticulous, multi-step process. First, imaging data is acquired using advanced techniques like CT or MRI scans. This data helps capture the patient’s unique anatomy. Next, I segment the anatomical structures to isolate the heart valve. Afterward, I export the segmented structures into an STL file format, which serves as the blueprint for printing. Before printing, I repair and enhance the STL file to ensure accuracy. Then, I prepare the file for printing by defining support materials and slicing the model into layers. The actual printing process follows, using technologies like stereolithography (STL) or fused deposition modeling (FDM). Finally, post-printing steps, such as removing support materials and dipping the valve in silicone, complete the process. Each step ensures the final product meets the required precision and functionality.
Materials used in 3D-printed heart valves
The choice of material plays a critical role in the success of 3D-printed heart valves. I often rely on biocompatible materials that promote tissue regeneration and ensure durability. Natural polymers like collagen, fibrin, and chitosan are excellent for encouraging integration with the body. Synthetic polymers, such as polyglycolic acid (PGA), poly(L-lactic acid) (PLLA), and polyurethane (PU), offer mechanical strength and biodegradability. For instance, polyurethane is particularly valued for its flexibility and resilience. Additionally, materials like Acrylonitrile Butadiene Styrene (ABS) and TangoPlus FullCure 930 are frequently used, with usage rates of 29% and 36%, respectively. These materials ensure that the printed valves can withstand the demanding environment of the human heart.
Material | Usage Percentage |
---|---|
Acrylonitrile Butadiene Styrene (ABS) | 29% |
TangoPlus FullCure 930 | 36% |
Patient-specific designs and their importance
Patient-specific designs revolutionize how we approach heart valve replacement. By tailoring the valve to match an individual’s anatomy, I can reduce complications and improve surgical outcomes. For example, customized implants enhance hemodynamic function, leading to better postoperative results. Advanced imaging techniques allow me to create precise models that aid in understanding complex cardiovascular conditions. This precision improves surgical planning and execution, ultimately minimizing risks. Furthermore, these designs ensure the valve fits seamlessly, enhancing its performance and the patient’s recovery. In my experience, this personalized approach represents a significant leap forward in cardiovascular medicine.
Evidence Description | Impact on Functionality |
---|---|
Customized implants designed to match individual anatomy reduce complications. | Enhances surgical outcomes and minimizes risks during and after surgery. |
Accurate patient-specific models aid in understanding complex cardiovascular diseases. | Improves surgical planning and technique, leading to better procedural efficiency. |
Development relies on advanced imaging techniques for precise manufacturing. | Ensures implants are tailored to the patient’s unique anatomical needs. |
Patient-specific designs enhance hemodynamic function and overall postoperative results. | Leads to improved heart valve performance and patient recovery. |
Can heart valves be 3D printed? Yes, and patient-specific designs highlight the transformative potential of this technology.
Current Progress and Success Stories
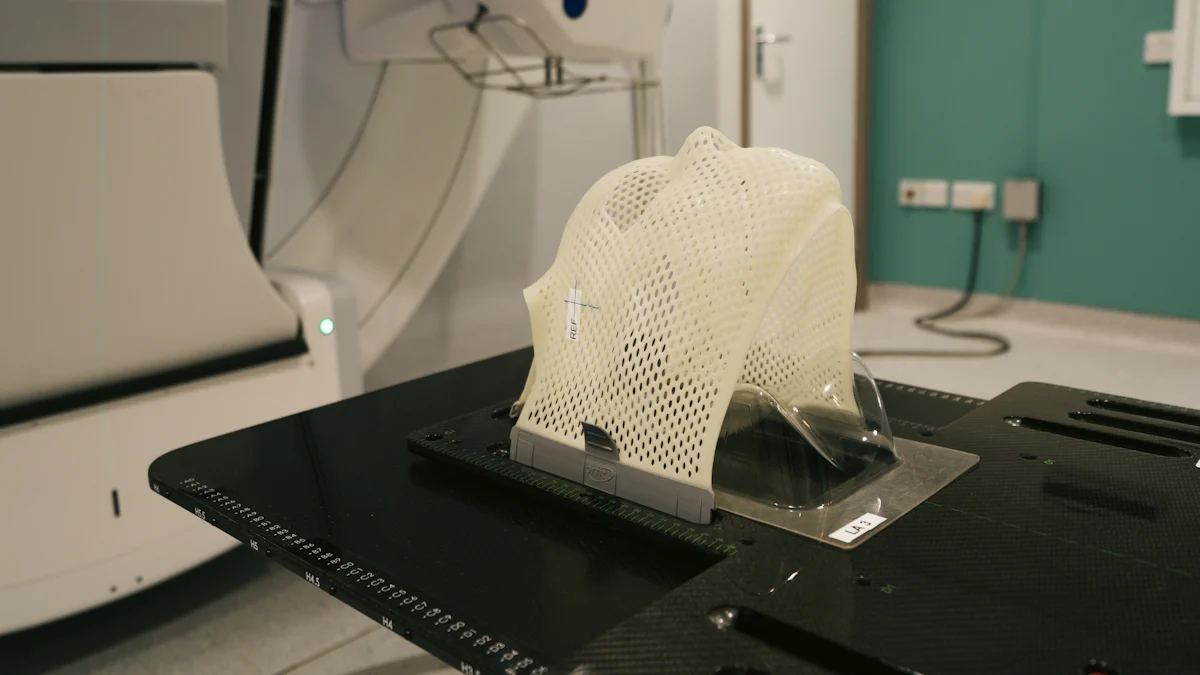
Research breakthroughs in 3D-printed heart valves
I have seen remarkable advancements in the development of 3D-printed heart valves. Researchers now use a combination of organic and synthetic polymers to create these valves. Each material offers unique benefits. For instance, synthetic polymers provide mechanical strength, while organic polymers promote tissue integration. Stem cells have also emerged as a game-changer in cardiac tissue engineering. They reduce the risk of immunological rejection and thrombosis, which are common complications in traditional valve replacements. Patient-specific designs have further revolutionized this field. These designs allow surgeons to visualize and assess implants before surgery, improving outcomes. Additionally, physiologically active cardiac implants, developed through 3D bioprinting, hold the potential to eliminate the need for artificial valves entirely.
Successful prototypes and testing examples
Several successful prototypes of 3D-printed heart valves have demonstrated promising results. For example, the TRISKELION valve prototype achieved a regurgitation fraction of 22.26% and a cardiac output of 3.80 L/min. In comparison, biological and mechanical valves showed slightly better performance metrics.
Prototype | Regurgitation Fraction (%) | Mean Systolic Pressure Gradient (mmHg) | Cardiac Output (L/min) |
---|---|---|---|
TRISKELION | 22.26 ± 4.34 | 9.93 ± 3.22 | 3.80 ± 0.21 |
Biological Valve | 8.55 ± 0.22 | 8.18 ± 0.65 | 4.46 ± 0.01 |
Mechanical Valve | 13.23 ± 0.79 | 10.15 ± 0.16 | 4.21 ± 0.05 |
Beyond these prototypes, I have observed other innovative applications. For instance, 3D-printed models of the descending aorta have been used for compliance tests. A right ventricular outflow tract model was created to simulate pulmonary valve replacement procedures. Additionally, life-size aortic root models and mitral valve models have been developed for testing valved stents and hemodynamic performance, respectively.
Insights from clinical and preclinical studies
Clinical and preclinical studies have provided valuable insights into the potential of 3D-printed heart valves. I have found that 3D printing is particularly useful for preoperative planning, training, and device testing. Accurate segmentation of anatomical structures is critical for successful printing. Advances in materials and printing techniques have significantly improved the accuracy of these structures. Flexible and transparent materials now allow for better representation of cardiac anatomy. However, the clinical benefits of 3D-printed heart valves remain unproven. Despite this, I believe this technology holds great promise for addressing specific clinical challenges in heart valve disease. Ongoing research continues to refine the materials and techniques required for these applications.
Can heart valves be 3D printed? The progress and success stories in this field suggest that they can, though further research is essential to bring this innovation into widespread clinical use.
Challenges and Limitations
Durability and long-term performance issues
Durability remains one of the most pressing challenges for 3D-printed heart valves. I have observed that these valves must endure the constant mechanical stress of the cardiovascular system. Factors such as biocompatibility, mechanical properties, wear resistance, degradation, and calcification significantly impact their long-term performance. For instance, calcification can lead to valve stiffening, reducing its functionality over time. Additionally, degradation of materials may release byproducts that could harm surrounding tissues. Addressing these issues is critical to ensuring that 3D-printed valves can reliably function within the body for years.
Biocompatibility and tissue integration challenges
Ensuring biocompatibility and proper tissue integration poses another significant hurdle. From my experience, selecting materials that do not provoke an immune response is essential. The materials must also integrate seamlessly with surrounding tissues to promote healing and stability. Furthermore, they need to withstand the dynamic environment of the cardiovascular system, which includes constant blood flow and pressure changes. Other considerations include durability, biodegradability, and the potential toxicity of degradation products. These factors must align to create a valve that is both safe and effective for patients.
- Materials must not trigger immunological reactions.
- They should integrate well with surrounding tissues.
- They must endure the cardiovascular system’s dynamic environment.
- Durability, biodegradability, and toxicity of byproducts require careful evaluation.
Regulatory and ethical considerations
Regulatory approval for 3D-printed heart valves involves a lengthy and rigorous process. I have seen that extensive preclinical research is required to validate the safety and functionality of these valves. Biocompatibility tests and mechanical evaluations are mandatory to ensure reliability. Additionally, clinical trials must demonstrate their effectiveness in real-world scenarios. Ethical considerations also come into play. For example, ensuring patient safety and addressing potential risks associated with new materials are paramount. These steps are necessary to build trust and pave the way for widespread clinical adoption.
- Preclinical research must validate safety and functionality.
- Biocompatibility and mechanical tests are essential.
- Clinical trials must prove safety and effectiveness.
- Ethical concerns include patient safety and material risks.
Can heart valves be 3D printed? Yes, but overcoming these challenges is crucial to making this technology a viable solution for patients worldwide.
Future Potential and Implications
Transforming heart valve replacement with 3D printing
I believe 3D printing has the potential to revolutionize heart valve replacement. Personalized heart valve solutions can significantly improve patient outcomes by tailoring implants to individual anatomies. Surgeons can use patient-specific models during preoperative planning to visualize and assess implant placement. This approach reduces complications and enhances surgical precision. Advances in bioprinting may even lead to physiologically active cardiac implants, eliminating the need for traditional artificial valves.
Additionally, 3D printing provides a wide range of training samples for medical professionals. These models simulate real-life conditions, helping surgeons refine their skills for procedures like transcatheter aortic valve replacement. By reducing reliance on animal models, this technology addresses ethical concerns while improving training efficiency.
Reducing costs and improving accessibility
3D printing offers a cost-effective alternative to traditional methods in heart valve replacement. I have seen how this technology reduces the need for expensive animal models in training, which are not only costly but also ethically challenging. Easily produced and replaced training samples lower overall training expenses for medical professionals. This cost reduction could make heart valve replacement procedures more affordable and accessible to patients worldwide.
Advancing personalized medicine and regenerative solutions
The integration of 3D printing into cardiac healthcare is advancing personalized medicine. Patient-specific cardiac implants, created using organic and synthetic polymers, improve surgical outcomes and reduce complications. Stem cell integration in tissue engineering minimizes immunological rejection, further enhancing the potential of personalized heart valve repair. Advances in imaging and printing technologies also enable precise representations of cardiac anatomy, aiding in surgical planning and candidate selection for heart therapies. These innovations align with the goals of regenerative medicine, paving the way for custom prostheses and improved patient care.
3D-printed heart valves represent a groundbreaking step forward in medical innovation. They offer the potential to transform heart valve replacement and repair by providing personalized solutions. However, the technology remains in its infancy and faces challenges like durability, biocompatibility, and regulatory hurdles. Advancing this field requires collaborative efforts among experts to optimize manufacturing processes, select affordable materials, ensure regulatory compliance, and integrate sensors into implants. Can heart valves be 3D printed? With continued research and teamwork, I believe this vision can become a clinical reality.
FAQ
What makes 3D-printed heart valves different from traditional ones?
I design 3D-printed valves to match a patient’s anatomy. This customization improves fit, reduces complications, and enhances surgical outcomes compared to traditional, one-size-fits-all valves.
Are 3D-printed heart valves safe for clinical use?
Not yet. While promising, 3D-printed valves require further testing to address durability, biocompatibility, and regulatory approval before they can be widely used in clinical settings.
How long does it take to create a 3D-printed heart valve?
The process varies. It typically takes several hours to days, depending on the complexity of the design and the materials used for printing.