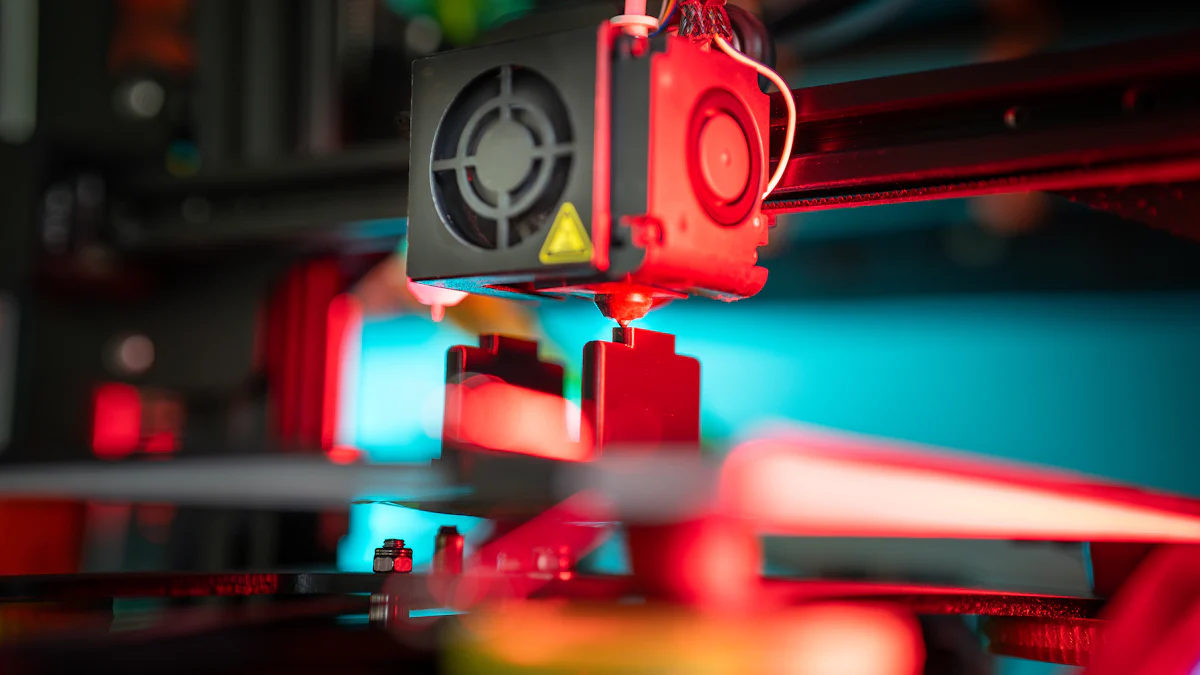
In the world of manufacturing, choosing between 3D Printing vs. CNC Machining can significantly impact the outcome of a project. These technologies differ fundamentally in their approach. 3D Printing builds objects layer by layer, offering flexibility and innovation, while CNC Machining removes material from a solid block, ensuring precision and durability. The global market for 3D Printing is projected to reach 22.14billion∗in2023,whereasCNCMachiningisexpectedtohit∗22.14 billion* in 2023, whereas CNC Machining is expected to hit *22.14billion∗in2023,whereasCNCMachiningisexpectedtohit∗25 billion by 2028. Selecting the right technology in the debate of 3D Printing vs. CNC Machining depends on specific needs, such as material requirements and precision levels.
Key Takeaways
- 3D Printing offers design flexibility and rapid prototyping, making it ideal for innovative projects and small production runs.
- CNC Machining excels in precision and material versatility, suitable for high-strength applications requiring tight tolerances.
- Choosing between 3D Printing and CNC Machining depends on specific project needs, including material type, precision requirements, and production volume.
- 3D Printing is cost-effective for projects needing intricate designs and quick turnaround, while CNC Machining is more economical for large-scale production.
- Both technologies can be combined to optimize costs and enhance production efficiency, leveraging the strengths of each method.
- Understanding the advantages and limitations of each technology is crucial for making informed manufacturing decisions.
- Industries such as aerospace, healthcare, and automotive benefit significantly from the unique capabilities of 3D Printing and CNC Machining.
Understanding the Processes
In the realm of manufacturing, understanding the processes of 3D Printing and CNC Machining is crucial. Each technology offers unique methods and advantages that cater to different project needs.
3D Printing Process
How 3D Printing Works
I find 3D Printing fascinating due to its additive nature. This process builds objects layer by layer from a digital model. It starts with a 3D design file, often in STL or OBJ format. The printer reads this file and deposits material, such as plastic or metal, in successive layers. This method allows for intricate designs with minimal geometric constraints. The flexibility in design makes 3D Printing ideal for rapid prototyping and creative projects.
Common 3D Printing Technologies
Several technologies dominate the 3D Printing landscape. Fused Deposition Modeling (FDM) uses thermoplastic filaments, which are heated and extruded through a nozzle. Stereolithography (SLA) employs a laser to cure liquid resin into solid parts. Selective Laser Sintering (SLS) fuses powdered material using a laser. Each technology has its strengths, with FDM being cost-effective, SLA offering high detail, and SLS providing robust mechanical properties.
CNC Machining Process
How CNC Machining Works
CNC Machining, in contrast, is a subtractive process. I appreciate its precision and reliability. It involves removing material from a solid block using computer-controlled tools. The process begins with a CAD model, which guides the machine’s movements. CNC machines cut, drill, and mill the material to achieve the desired shape. This method excels in producing high-strength, precision parts with tight tolerances.
Types of CNC Machines
Various CNC machines cater to different manufacturing needs. CNC Mills use rotating cutting tools to remove material, ideal for complex shapes. CNC Lathes rotate the workpiece against a stationary cutting tool, perfect for cylindrical parts. CNC Routers handle larger sheets of material, often used in woodworking. Each type offers specific advantages, making CNC Machining versatile across industries.
In the debate of 3D Printing vs. CNC Machining, understanding these processes helps in selecting the right technology for your project. Whether you prioritize design freedom or precision, both methods offer valuable solutions in modern manufacturing.
Materials and Precision
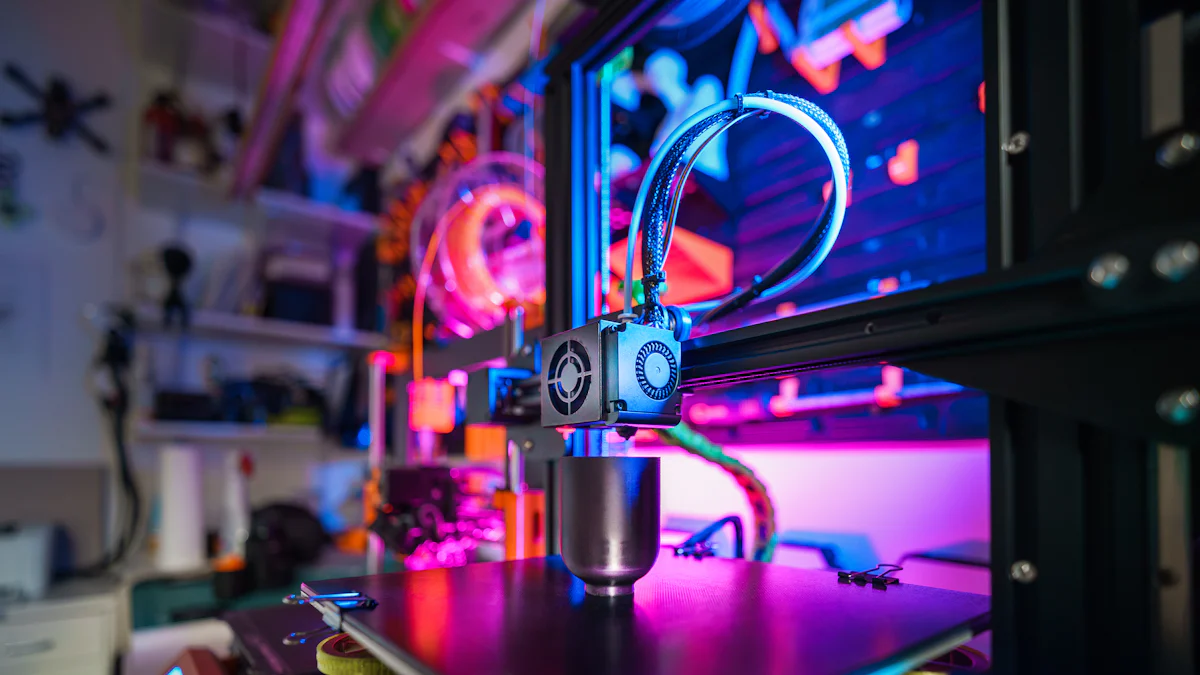
In the ongoing debate of 3D Printing vs. CNC Machining, understanding the materials and precision each technology offers is crucial. Both methods cater to different needs, providing unique advantages in terms of material usage and accuracy.
Materials Used in 3D Printing
Plastics, Metals, and Composites
I find 3D Printing remarkable for its versatility in material usage. It primarily employs plastics, such as PLA and ABS, which are popular for their ease of use and affordability. These materials suit a wide range of applications, from simple prototypes to complex models. Metals like stainless steel and titanium are also used, offering strength and durability for more demanding projects. Additionally, composites combine materials to enhance properties, providing options like carbon fiber-reinforced polymers for lightweight yet strong parts. This diversity allows 3D Printing to cater to various industries, from consumer goods to aerospace.
Materials Used in CNC Machining
Metals, Plastics, and Wood
CNC Machining stands out for its ability to work with a broad spectrum of materials. Metals such as aluminum, brass, and steel are commonly used, offering excellent mechanical properties and precision. These materials are ideal for high-strength applications requiring durability and reliability. Plastics like nylon and polycarbonate provide flexibility and are often used for parts needing specific chemical resistance or lightweight characteristics. Wood is another material CNC machines handle well, making it suitable for furniture and decorative items. The capability to machine real materials with origin traceability makes CNC Machining a preferred choice for industries demanding high-quality standards.
Precision and Tolerances
Comparing Accuracy in 3D Printing and CNC Machining
When it comes to precision, CNC Machining often takes the lead. It delivers superior dimensional accuracy and better mechanical properties across all three dimensions. This makes it the gold standard for applications requiring tight tolerances and high-strength parts. CNC Machining can achieve tolerances as low as ±0.005 mm, ensuring exceptional precision.
On the other hand, 3D Printing offers unparalleled design flexibility and rapid production capabilities. While it may not match CNC Machining’s precision, it excels in creating complex geometries with fewer geometric constraints. This makes it cost-effective and faster for prototyping and projects where design freedom is paramount.
Advantages and Disadvantages
In the ongoing debate of 3D Printing vs. CNC Machining, understanding the advantages and disadvantages of each technology is essential. Both methods offer unique benefits and limitations that cater to different manufacturing needs.
Advantages of 3D Printing
Design Flexibility and Rapid Prototyping
I admire 3D Printing for its unparalleled design flexibility. This technology allows me to create complex geometries with minimal constraints. The additive nature of 3D Printing enables the production of intricate designs that would be challenging or impossible with traditional methods. Rapid prototyping is another significant advantage. I can quickly transform digital models into physical objects, which accelerates the development process. This speed is particularly beneficial in industries where innovation and time-to-market are critical.
Disadvantages of 3D Printing
Limitations in Material Strength and Surface Finish
Despite its advantages, 3D Printing has limitations. I often encounter challenges with material strength. While 3D Printing offers a wide range of materials, the mechanical properties may not match those achieved through CNC Machining. Surface finish is another area where 3D Printing falls short. The layer-by-layer construction can result in a rough surface, requiring additional post-processing to achieve a smooth finish. These limitations make 3D Printing less suitable for applications demanding high strength and superior surface quality.
Advantages of CNC Machining
High Precision and Material Versatility
CNC Machining excels in precision and material versatility. I appreciate its ability to produce parts with exceptional dimensional accuracy. This precision is crucial for applications requiring tight tolerances and high-strength components. CNC Machining also offers a broad spectrum of materials, including metals, plastics, and wood. This versatility allows me to select the best material for each project, ensuring optimal performance and durability. The subtractive process of CNC Machining provides a superior surface finish, reducing the need for additional finishing work.
Disadvantages of CNC Machining
Material Waste and Setup Time
CNC Machining, while renowned for its precision, presents some notable challenges. One of the primary drawbacks I encounter is material waste. The subtractive nature of CNC Machining means that it removes material from a solid block to create the desired shape. This process often results in significant material wastage, especially when working with expensive materials like metals. Unlike 3D Printing, which adds material layer by layer, CNC Machining can lead to higher costs due to this inefficiency.
Another challenge is the setup time. CNC Machining requires meticulous preparation before production can begin. Setting up the machine involves configuring the tools, securing the workpiece, and programming the machine with precise instructions. This setup phase can be time-consuming, particularly for complex parts or small production batches. In contrast, 3D Printing typically requires less initial preparation, allowing for quicker turnaround times.
“CNC machining prototyping takes longer but offers superior final production quality and finish.”
This quote highlights the trade-off between time and quality. While CNC Machining may take longer to set up and execute, it often results in superior production quality and finish. However, for projects where speed is crucial, this extended setup time can be a disadvantage.
Additionally, CNC Machining’s efficiency diminishes with smaller production runs. The time and effort invested in setup may not justify the output for limited quantities. In such cases, 3D Printing emerges as a more cost-effective and faster alternative, especially for prototyping or small-scale production.
Applications and Industry Use
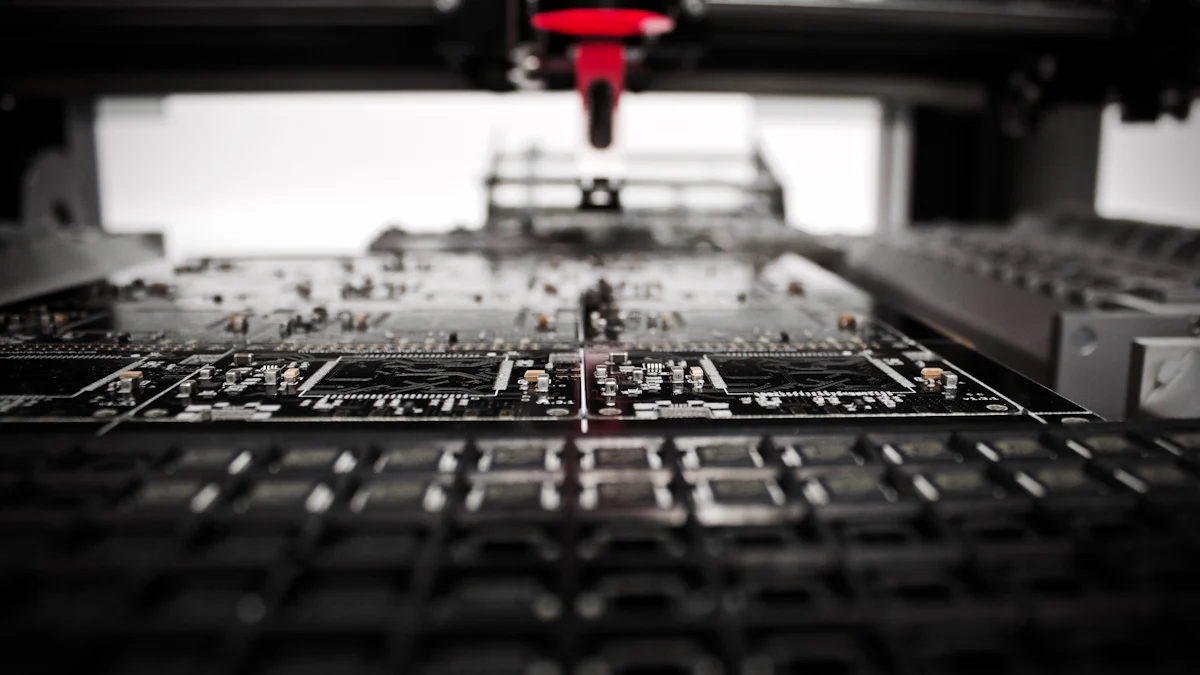
In the ongoing debate of 3D Printing vs. CNC Machining, understanding their applications across various industries highlights their unique strengths and capabilities. Each technology serves distinct sectors, offering tailored solutions to meet specific demands.
Industries Utilizing 3D Printing
Aerospace, Healthcare, and Consumer Goods
I find 3D Printing particularly transformative in the aerospace industry. It enables the creation of lightweight components, which are crucial for fuel efficiency and performance. The ability to produce complex geometries without traditional manufacturing constraints allows for innovative designs that enhance aerodynamics and reduce weight. This flexibility is invaluable in an industry where every gram counts.
In healthcare, 3D Printing revolutionizes the production of custom prosthetics and implants. The technology allows for personalized medical devices tailored to individual patients, improving comfort and functionality. I appreciate how this customization enhances patient outcomes and reduces recovery times. Additionally, 3D Printing facilitates the rapid prototyping of medical devices, accelerating the development of new treatments and technologies.
The consumer goods sector benefits from 3D Printing’s rapid prototyping capabilities. I can quickly iterate designs and bring new products to market faster than ever before. This speed fosters innovation and allows companies to respond swiftly to changing consumer demands. The ability to produce small batches of customized products also opens new opportunities for personalization, catering to niche markets and enhancing customer satisfaction.
Industries Utilizing CNC Machining
Automotive, Aerospace, and Industrial Manufacturing
CNC Machining plays a pivotal role in the automotive industry. Its precision and material versatility make it ideal for producing high-strength components like engine parts and transmission systems. I value the reliability and durability that CNC Machining brings to these critical applications, ensuring vehicles perform optimally under demanding conditions.
In aerospace, CNC Machining complements 3D Printing by providing the precision required for structural components. The tight tolerances achievable with CNC Machining ensure that parts fit perfectly and function reliably in extreme environments. I often rely on CNC Machining for parts that demand exceptional strength and accuracy, such as turbine blades and landing gear components.
Industrial manufacturing relies heavily on CNC Machining for its ability to produce complex parts with consistent quality. The technology’s efficiency and repeatability make it a cornerstone of mass production. I appreciate how CNC Machining minimizes downtime and maximizes output, even though occasional maintenance or programming errors can lead to delays. Regular updates and debugging of CNC programs help mitigate these issues, ensuring smooth and cost-effective operations.
Cost Implications
Understanding the cost implications of 3D Printing vs. CNC Machining is crucial for making informed decisions in manufacturing. Each technology presents unique cost factors that can significantly impact the overall budget of a project.
Cost Factors in 3D Printing
Material Costs and Machine Maintenance
In my experience, material costs in 3D Printing can vary widely depending on the type of material used. Plastics like PLA and ABS are generally affordable, making them popular choices for prototyping and small-scale production. However, when I work with metals or specialized composites, the costs can increase significantly. These materials offer enhanced properties but come at a higher price point.
Machine maintenance also plays a role in the cost structure of 3D Printing. Regular upkeep ensures optimal performance and longevity of the equipment. I find that maintaining a 3D printer involves tasks like cleaning nozzles, calibrating the build platform, and replacing worn-out parts. While these activities incur additional expenses, they are essential for preventing costly breakdowns and ensuring consistent print quality.
Cost Factors in CNC Machining
Material Waste and Labor Costs
CNC Machining often involves higher material costs due to waste. The subtractive nature of this process means that I remove material from a solid block, resulting in excess material that cannot be reused. This waste becomes particularly costly when working with expensive metals like titanium or stainless steel.
Labor costs also contribute to the overall expense of CNC Machining. Skilled operators are required to set up and run the machines, ensuring precision and accuracy. I have observed that the setup time can be lengthy, especially for complex parts, which increases labor costs. Additionally, programming the CNC machines demands expertise, further adding to the labor expenses.
Comparing Overall Costs
When Each Technology is More Cost-Effective
Deciding between 3D Printing vs. CNC Machining often comes down to evaluating when each technology is more cost-effective. For projects requiring rapid prototyping or small production runs, I find 3D Printing to be the more economical choice. Its ability to produce intricate designs with minimal setup time makes it ideal for innovation-driven industries like aerospace and healthcare.
On the other hand, CNC Machining proves more cost-effective for large-scale production or when high precision is paramount. Despite the initial setup costs, the efficiency and repeatability of CNC Machining make it suitable for mass production. Industries such as automotive and industrial manufacturing benefit from its ability to produce high-strength components with tight tolerances.
In some cases, combining both technologies can optimize costs and enhance production efficiency. For instance, I have seen metal 3D printing files optimized for CNC machining to achieve desired specifications at a lower cost. This synergy allows for the production of complex parts with low roughness and tight tolerances, maximizing the strengths of both methods.
In the debate of 3D Printing vs. CNC Machining, each technology presents distinct advantages. 3D Printing offers design freedom and rapid production, making it ideal for innovative projects. CNC Machining excels in precision and material versatility, is suitable for high-strength applications. When choosing between them, consider your project’s specific needs. For small volumes and complex designs, 3D Printing may be more cost-effective. For large-scale production and precision parts, CNC Machining often proves superior. Evaluate both short-term costs and long-term benefits to make an informed decision.
FAQ
What are the main differences between 3D Printing and CNC Machining?
3D Printing and CNC Machining differ fundamentally in their processes. 3D Printing is an additive process, building objects layer by layer from a digital model. CNC Machining, on the other hand, is subtractive, removing material from a solid block to create the desired shape. Each method offers unique advantages and limitations, making them suitable for different applications.
How do I decide which technology to use for my project?
Choosing between 3D Printing and CNC Machining depends on your project’s specific requirements. Consider factors like material type, precision needs, production volume, and budget. 3D Printing excels in design flexibility and rapid prototyping, while CNC Machining offers high precision and material versatility. Understanding these strengths helps you make an informed decision.
What materials can I use with 3D Printing and CNC Machining?
3D Printing primarily uses plastics, metals, and composites. Common materials include PLA, ABS, stainless steel, and carbon fiber-reinforced polymers. CNC Machining works with metals, plastics, and wood, such as aluminum, brass, nylon, and polycarbonate. Each technology’s material options cater to different industry needs and applications.
Which technology offers better precision?
CNC Machining generally provides superior precision, achieving tolerances as low as ±0.005 mm. This makes it ideal for applications requiring tight tolerances and high-strength parts. While 3D Printing offers design flexibility, its precision may not match CNC Machining, making it more suitable for projects where design freedom is paramount.
What are the cost implications of using 3D Printing vs. CNC Machining?
Cost factors vary between the two technologies. 3D Printing involves material costs and machine maintenance, with plastics being more affordable than metals or composites. CNC Machining incurs higher material costs due to waste and requires skilled labor for setup and operation. Evaluate your project’s needs to determine the most cost-effective option.
Can I combine both technologies in a single project?
Yes, combining 3D Printing and CNC Machining can optimize costs and enhance production efficiency. For instance, you can use 3D Printing for initial prototypes and CNC Machining for final production. This approach leverages the strengths of both methods, achieving desired specifications at a lower cost.
What industries benefit most from 3D Printing?
Industries like aerospace, healthcare, and consumer goods benefit significantly from 3D Printing. It enables the creation of lightweight components, custom prosthetics, and rapid prototyping of new products. The technology’s flexibility and speed foster innovation and allow companies to respond quickly to changing demands.
What industries rely heavily on CNC Machining?
CNC Machining is crucial in automotive, aerospace, and industrial manufacturing. Its precision and material versatility make it ideal for producing high-strength components like engine parts and structural elements. The technology’s efficiency and repeatability support mass production and ensure consistent quality.
How does each technology impact the product lifecycle?
Understanding the impact of 3D Printing and CNC Machining across the product lifecycle is essential. 3D Printing accelerates prototyping and innovation, reducing time-to-market. CNC Machining ensures precision and durability in final products, supporting long-term reliability. Identifying where each technology offers benefits helps optimize your manufacturing process.
What are the environmental considerations for each technology?
Environmental considerations vary between 3D Printing and CNC Machining. 3D Printing generates less waste due to its additive nature, making it more sustainable for small-scale production. CNC Machining, being subtractive, produces more waste, especially with expensive materials. Consider these factors when evaluating the environmental impact of your manufacturing choices.