Sintered titanium 3d printing cost
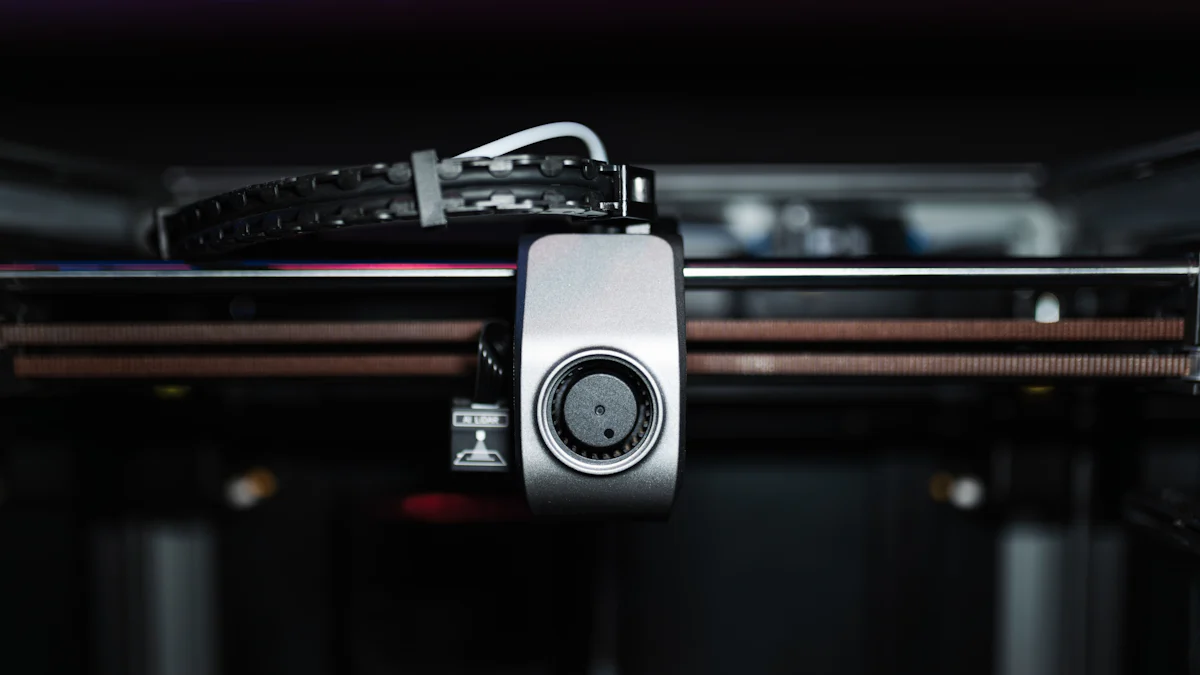
Understanding the sintered titanium 3D printing cost is essential for anyone considering this advanced manufacturing method. The high price of titanium materials and powders presents a significant challenge. Industrial-grade DMLS systems, crucial for this process, often come with six or seven-figure price tags. Despite these costs, the potential savings from a reduced buy-to-fly ratio can be substantial. This makes it crucial to weigh these factors carefully when deciding on using titanium 3D printing for component fabrication.
Key Takeaways
- Understanding the high costs of titanium materials is crucial, as they typically range from $350 to $550 per kilogram, impacting overall project budgets.
- Machine time is a significant cost factor; optimizing designs can reduce complexity and lower expenses, making budgeting more manageable.
- Post-processing is essential for achieving desired specifications, so plan for these additional costs early to avoid surprises.
- Sintered titanium 3D printing is ideal for low-volume production and custom parts, offering flexibility that traditional manufacturing cannot match.
- While initial costs are higher, the potential for savings through reduced material waste and faster production times makes 3D printing a valuable option.
- To optimize costs, focus on design efficiency by hollowing models and minimizing support structures, which can lead to significant savings.
- Comparing costs with traditional manufacturing reveals that 3D printing can be more cost-effective for small-scale projects, despite higher per-unit costs in mass production.
Understanding the DMLS Process
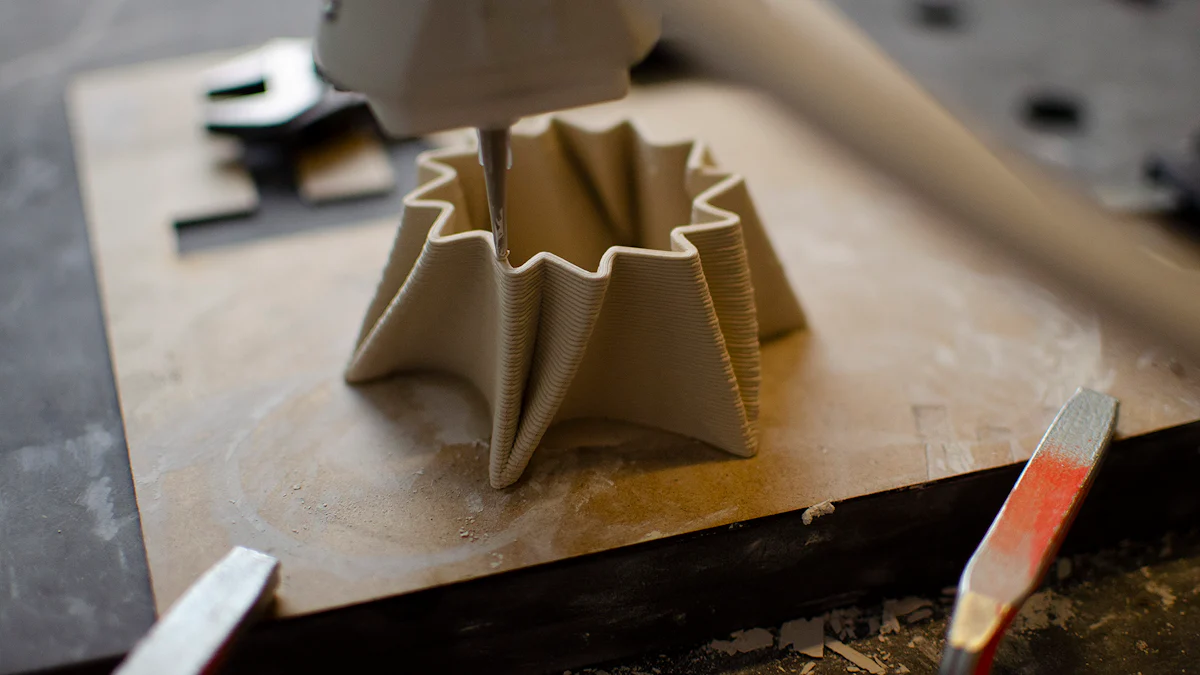
Overview of DMLS
In my experience, Direct Metal Laser Sintering (DMLS) stands out as a revolutionary additive manufacturing technique. This process uses a high-power laser to melt and fuse metallic powders into solid, three-dimensional parts. Unlike traditional methods, DMLS allows for the creation of complex geometries that machining cannot achieve. The technology eliminates the need for physical molds, offering precision and high-resolution results. I find it fascinating how DMLS can produce parts with excellent surface quality and near-wrought mechanical properties.
Steps Involved in DMLS
The DMLS process involves several key steps:
- Preparation: I start by preparing a digital CAD file that outlines the design of the part. This file guides the laser during the printing process.
- Layering: A thin layer of titanium powder spreads over the build area. The laser then traces the predefined path of the object’s cross-section, selectively melting the powder.
- Sintering: The laser fuses the titanium particles together and to the layer below, creating a solid structure. This step requires careful control of the energy input to avoid defects like warping.
- Repetition: The machine spreads another layer of powder, and the process repeats. Layer by layer, the part takes shape.
- Post-Processing: Once the printing completes, I often use conventional polishing techniques or precision turning to finish the part. This step ensures the final product meets the desired specifications.
Through these steps, DMLS offers the flexibility to produce metal parts that traditional manufacturing cannot. The ability to work with a wide variety of metal powders, including super alloys, makes DMLS an invaluable tool in industries like aerospace, automotive, and medical applications.
Key Cost Factors in Sintered Titanium 3D Printing
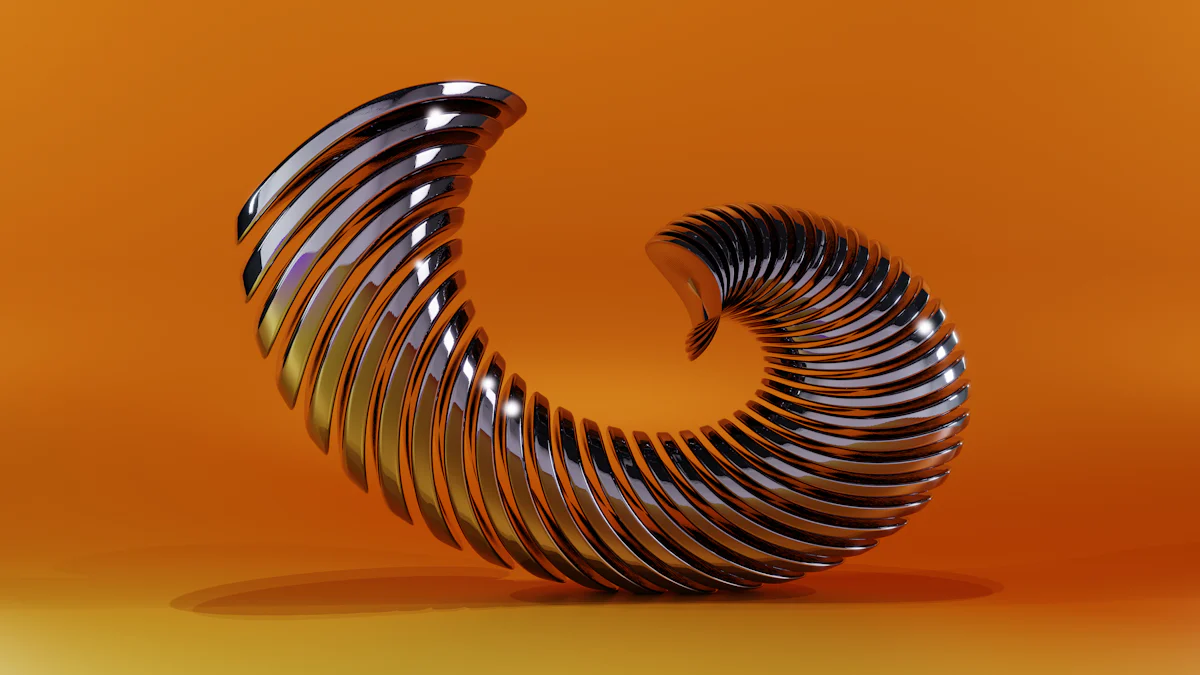
Understanding the sintered titanium 3D printing cost involves examining several key factors. Each element contributes significantly to the overall expense, and recognizing these can help in making informed decisions.
Material Costs
The cost of materials plays a crucial role in determining the sintered titanium 3D printing cost. Titanium powders, essential for the DMLS process, are notably expensive. Prices typically range from $350 to $550 per kilogram. This high cost stems from the quality and purity required for effective sintering. In comparison, other 3D printing materials, such as FDM filaments, are more affordable, ranging from $50 to $150 per kilogram. However, the unique properties of titanium, including its strength-to-weight ratio and corrosion resistance, justify the higher price. When planning a project, I always consider the material costs as a primary factor.
Machine Time
Machine time significantly impacts the sintered titanium 3D printing cost. The DMLS process requires precise control and extended periods to complete complex builds. For small and simple parts, costs can start from $50 to $500. Larger or more intricate designs can escalate to $10,000. The machine’s operational time directly correlates with the complexity and size of the part. I find that optimizing the design for efficiency can reduce machine time, thereby lowering costs. This aspect is crucial when budgeting for a project.
Post-Processing Costs
Post-processing is another vital component of the sintered titanium 3D printing cost. After printing, parts often require additional work to meet specific standards. This includes polishing, heat treatment, or precision machining. These steps ensure the final product achieves the desired mechanical properties and surface finish. The labor and equipment involved in post-processing can add substantial costs. In my experience, planning for these expenses early in the project helps avoid unexpected financial burdens.
By understanding these key cost factors, I can better manage the sintered titanium 3D printing cost. Each element, from material selection to machine time and post-processing, plays a pivotal role in the overall expense. Recognizing these aspects allows for more strategic decision-making and potential cost savings.
Comparing Costs with Traditional Manufacturing
Cost Comparison
When I compare the costs of sintered titanium 3D printing with traditional manufacturing, several factors come into play. 3D printing often presents lower upfront costs, especially for small-scale production or prototyping. This is because it eliminates the need for expensive tooling and molds. In contrast, traditional manufacturing methods like injection molding or CNC machining require significant initial investments. These costs can be prohibitive for low-volume production.
However, as production volume increases, traditional manufacturing becomes more cost-effective. The cost per unit decreases due to economies of scale. For mass production, traditional methods generally offer a more time-efficient solution. They can produce large quantities of parts quickly once the setup is complete. In my experience, this makes traditional manufacturing more suitable for high-volume production runs.
Potential Cost Savings
Despite the higher sintered titanium 3D printing cost, potential savings exist. 3D printing excels in low-volume production, custom parts, and prototypes. It offers significant time and cost savings by eliminating the need for tooling changes and setup time. This flexibility allows for rapid iteration and customization, which traditional methods cannot match.
Moreover, 3D printing can replace complex workflows associated with conventional manufacturing. This leads to substantial time savings. I find that the ability to produce intricate designs without additional costs is a major advantage. The reduced buy-to-fly ratio in aerospace applications, for example, highlights the potential for cost savings. By minimizing material waste, 3D printing can offer a clear cost profit over traditional methods.
In conclusion, understanding the sintered titanium 3D printing cost involves recognizing key factors like material expenses, machine time, and post-processing. To optimize costs, I recommend focusing on design efficiency, such as hollowing models and minimizing support structures. Adjusting printer settings can also reduce material usage and wear. Despite higher initial costs, 3D printing offers advantages over traditional methods, including flexibility and reduced waste. By considering these aspects, I ensure my projects remain innovative and budget-conscious.
FAQ
Can titanium 3D printing be used for mass production?
Titanium 3D printing shines in industries like aerospace and healthcare. However, it presents challenges for mass production due to substantial initial costs. Industrial-grade DMLS systems often carry six or seven-figure price tags. The production of titanium powder, crucial for 3D printing, involves high costs. This is because it requires high purity and fine particle consistency. These processes are energy-intensive and technologically demanding. Additionally, the environmental impact of titanium extraction and processing adds to the cost. Extensive safety and regulatory compliance are necessary.
What are the main challenges in 3D printing with titanium?
3D printing with titanium involves several challenges. Material manufacturers create titanium powders specifically for 3D printing. These metal powders are engineered for uniform particle size and shape. This improves flowability and packing density in the print bed. As a result, prints become smoother and more detailed. The mechanical properties also strengthen by reducing inclusions and porosity. Despite these advancements, achieving consistent quality remains a challenge. The high cost of materials and equipment further complicates the process.
How does the cost of titanium 3D printing compare to other materials?
Titanium 3D printing generally incurs higher costs compared to other materials. Titanium powders range from $350 to $550 per kilogram. In contrast, materials like stainless steel are more affordable. Some services charge around $150 per pound for stainless steel. The high cost of titanium stems from its unique properties. These include a high strength-to-weight ratio and excellent corrosion resistance. While more expensive, titanium offers advantages that justify the cost in specific applications.
What factors influence the cost of titanium 3D printing?
Several factors influence the cost of titanium 3D printing. Material costs play a significant role. Titanium powders are expensive due to their quality and purity requirements. Machine time also impacts costs. The DMLS process requires precise control and extended periods for complex builds. Post-processing adds to the expense. Parts often need additional work to meet specific standards. This includes polishing, heat treatment, or precision machining. Each factor contributes to the overall cost, making it essential to consider them when budgeting for a project.
Are there any cost-saving strategies for titanium 3D printing?
Yes, there are strategies to save costs in titanium 3D printing. I recommend focusing on design efficiency. This includes hollowing models and minimizing support structures. Adjusting printer settings can also reduce material usage and wear. Additionally, optimizing the design for efficiency can lower machine time. By implementing these strategies, I can achieve potential cost savings while maintaining quality.