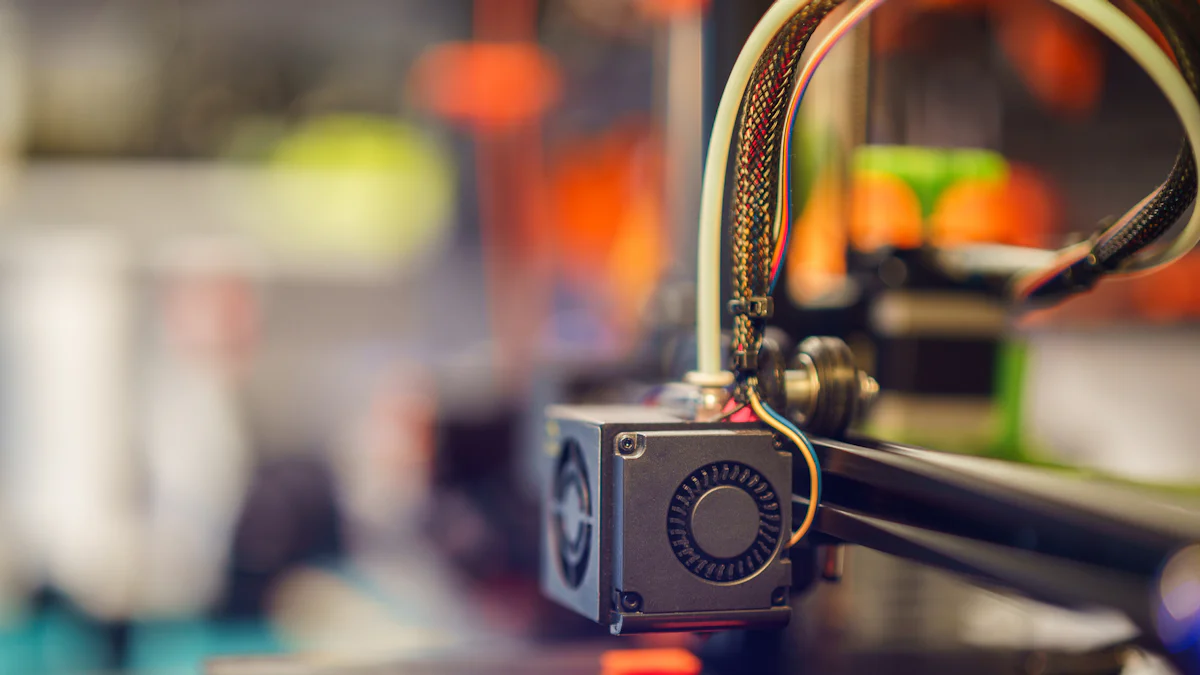
Regarding strength in 3D printing, titanium is the top contender, making it clear which 3D printing material is the strongest. You’ll find it unmatched in durability and toughness, especially when processed through advanced techniques like DMLS, SLM, or EBM. Its ability to handle extreme conditions makes it a favorite for demanding applications. Other materials like carbon fiber composites, polycarbonate, and nylon also bring impressive strength to the table. Each offers unique benefits depending on your needs. The strength of these materials depends on factors like tensile strength, impact resistance, and how well they perform in different environments.
What Makes a 3D Printing Material Strong?
When you’re choosing a 3D printing material, strength is often a top priority. But what exactly makes a material strong? Let’s break it down into key factors and explore how material composition plays a role.
Key Factors Influencing Material Strength
Tensile Strength and Durability
Tensile strength measures how much force a material can handle before it breaks. Materials with high tensile strength, like titanium or polycarbonate, can withstand heavy loads without cracking or deforming.
Impact Resistance and Flexibility
Impact resistance determines how well a material absorbs sudden shocks or forces. For example, polycarbonate excels in this area, making it ideal for parts exposed to frequent impacts. Flexibility also matters. Materials like nylon combine flexibility with strength, allowing them to bend without breaking. This balance is crucial for applications like hinges or gears, where movement is constant.
Heat and Chemical Resistance
Some materials lose their strength when exposed to high temperatures or harsh chemicals. Heat-resistant options like PEEK or PEI maintain their integrity in extreme conditions. Chemical resistance is equally important for parts used in industrial or medical environments. Choosing a material with these properties ensures your printed parts perform reliably, even in challenging settings.
The Role of Material Composition
Pure Thermoplastics vs. Composites
However, composites take things to the next level. By combining a base material with reinforcements, 3D Printing Materials deliver superior strength and performance.
Additives and Reinforcements (e.g., carbon fiber, glass fiber)
Additives and reinforcements enhance the properties of base materials. Carbon fiber or glass fiber can significantly boost tensile strength, impact resistance, and heat tolerance. These additives create materials that are not only stronger but also lighter. If you’re wondering which 3D printing material is the strongest for your project, composites with these reinforcements often top the list.
Top Strongest 3D Printing Materials
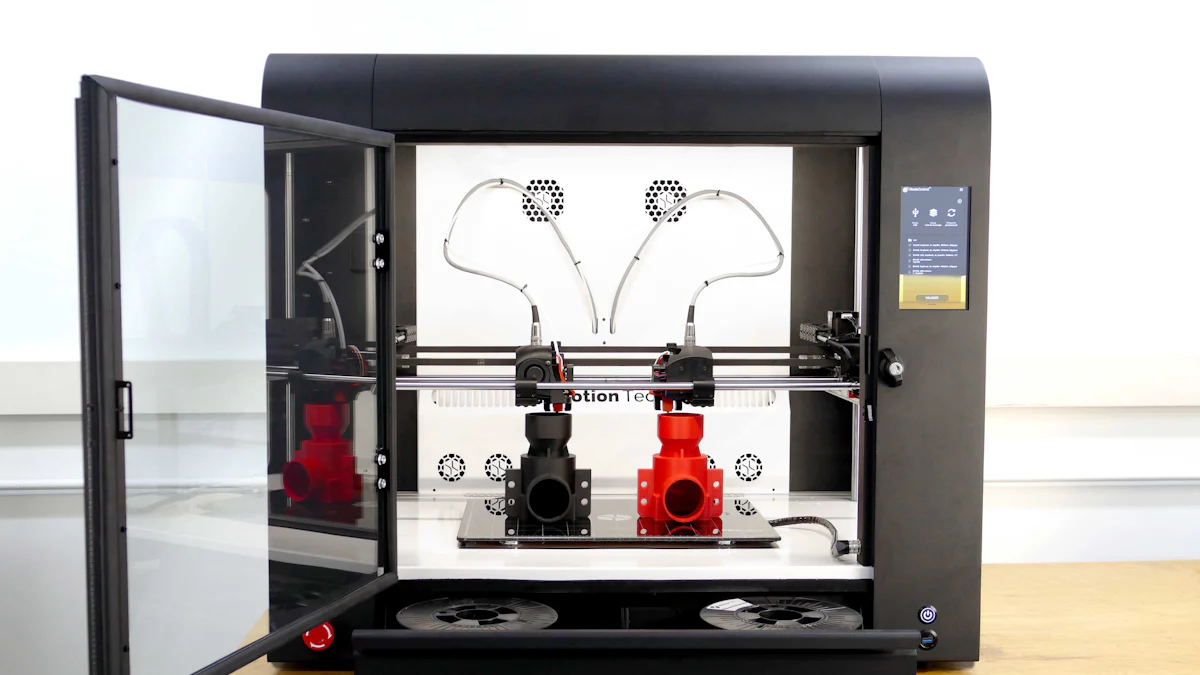
When you’re looking for the strongest materials in 3D printing, a few options stand out. Each material offers unique properties that make it suitable for specific applications. Let’s dive into the top contenders and see what makes them exceptional.
Titanium
Properties: Exceptional strength, lightweight, and corrosion resistance
Titanium is often considered the gold standard for strength in 3D printing. Its exceptional strength-to-weight ratio makes it a favorite for projects requiring durability without adding unnecessary weight. Titanium resists corrosion, even in harsh environments, which ensures long-lasting performance. It also handles extreme temperatures with ease, maintaining its structural integrity under stress.
Applications: Aerospace, medical implants, and high-performance engineering
You’ll find titanium widely used in industries where reliability is critical. In aerospace, it’s perfect for creating lightweight yet strong components. Medical implants benefit from titanium’s biocompatibility, ensuring safety and durability inside the human body. Engineers rely on it for high-performance parts that need to withstand heavy loads or extreme conditions.
Carbon Fiber Composites
Properties: High strength-to-weight ratio, rigidity, and heat resistance
Carbon fiber composites combine strength and lightness like no other material. These composites feature a high strength-to-weight ratio, making them ideal for applications where weight reduction is key. They also offer excellent rigidity, ensuring parts remain stable under pressure. Their heat resistance adds another layer of reliability, especially in demanding environments.
Applications: Aerospace, automotive, and industrial tooling
In aerospace and automotive industries, carbon fiber composites shine. They help reduce weight in vehicles and aircraft without compromising strength. Industrial tooling also benefits from their rigidity and durability, ensuring tools last longer and perform better. If you need a material that balances strength and efficiency, carbon fiber composites are a solid choice.
Polycarbonate (PC)
Properties: High impact resistance, transparency, and heat resistance
Polycarbonate stands out for its impressive impact resistance. It can absorb shocks and handle rough use without cracking or breaking. Its transparency makes it a versatile option for applications requiring clear or see-through parts. Additionally, polycarbonate resists heat, making it suitable for environments where temperature fluctuations occur.
Applications: Functional prototypes, mechanical parts, and enclosures
Polycarbonate works well for functional prototypes that need to endure testing and adjustments. Mechanical parts made from this material can handle wear and tear, ensuring reliability over time. Enclosures benefit from its strength and transparency, offering protection while maintaining visibility. If you’re searching for a material that combines toughness with versatility, polycarbonate delivers.
Nylon (Polyamide)
Nylon, also known as polyamide, stands out for its unique combination of durability, flexibility, and chemical resistance. You’ll notice its ability to handle wear and tear, making it a reliable choice for parts that face constant movement or friction. Nylon’s flexibility allows it to bend without breaking, which is essential for applications requiring repeated motion. Its chemical resistance ensures it performs well in environments exposed to oils, greases, or other harsh substances.
When you’re working on projects like gears or hinges, nylon becomes an excellent option. Gears made from nylon can endure continuous rotation and pressure without losing their shape or strength. Hinges benefit from its flexibility, allowing smooth movement over time. For wear-resistant parts, nylon’s durability ensures they last longer, even under challenging conditions. If you need a material that balances strength with adaptability, nylon delivers exceptional results.
PEEK and PEI (Ultem)
PEEK and PEI, often referred to as Ultem, are high-performance materials that excel in demanding environments. These materials offer unmatched high-temperature resistance, maintaining their strength and stability even under extreme heat. You’ll also appreciate their chemical stability, which protects them from degradation when exposed to aggressive chemicals. Their mechanical strength ensures they can handle heavy loads and stress without compromising performance.
In high-performance engineering, PEEK and PEI shine as top choices. They’re commonly used in industries where reliability is critical. Medical devices benefit from their biocompatibility and resistance to sterilization processes. Electronics manufacturers rely on these materials for components that must withstand heat and maintain precision. Whether you’re designing for aerospace, healthcare, or advanced engineering, PEEK and PEI provide the strength and resilience you need.
Testing and Comparing Material Strength
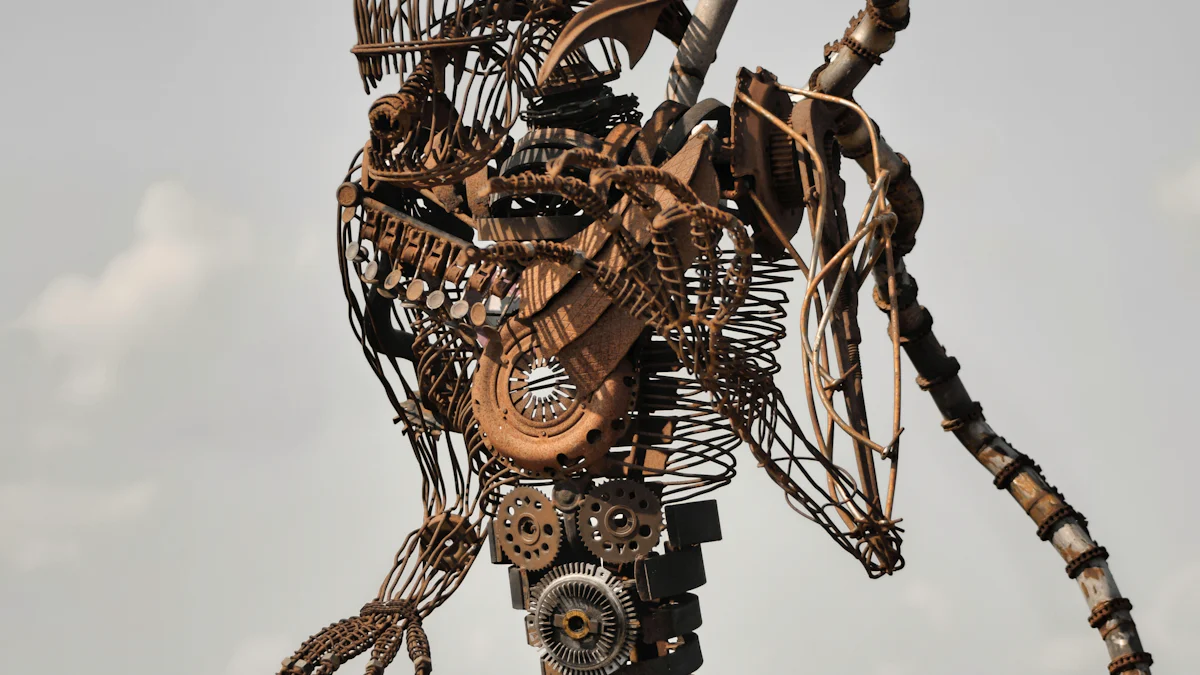
When it comes to understanding the strength of 3D printing materials, testing plays a crucial role. You can’t just rely on claims or assumptions; you need measurable data to make informed decisions. Let’s explore how material strength is tested and compare some of the strongest options available.
How Material Strength is Measured
Testing methods help you evaluate how well a material performs under different conditions. These tests focus on specific properties like tensile strength, impact resistance, and heat deflection.
Tensile Strength Testing
Tensile strength testing measures how much force a material can handle before it breaks. In this test, a sample is stretched until it snaps. The results show the maximum load the material can bear. For example, titanium excels in tensile strength, making it ideal for heavy-duty applications. If your project involves structural components, this test gives you a clear idea of which material can handle the stress.
Impact Resistance Testing
Impact resistance testing evaluates how well a material absorbs sudden shocks or impacts. A weighted object strikes the material, and the test measures its ability to resist cracking or breaking. Polycarbonate often shines in this area due to its toughness. If you’re designing parts that face frequent collisions or drops, this test helps you choose a material that won’t fail under pressure.
Heat Deflection Testing
Heat deflection testing determines how a material performs under high temperatures. The test involves applying heat and pressure to see when the material starts to deform. Materials like PEEK and PEI maintain their shape and strength even in extreme heat. If your project involves high-temperature environments, this test ensures your material won’t lose its integrity.
Examples of Strength Comparisons
Comparing materials side by side helps you understand their strengths and weaknesses. Let’s look at some common comparisons to see how different materials stack up.
Titanium vs. Carbon Fiber Composites
Titanium offers unmatched tensile strength and durability. It resists corrosion and handles extreme conditions with ease. On the other hand, carbon fiber composites provide a high strength-to-weight ratio. They’re lighter than titanium but still incredibly strong. If weight reduction is a priority, carbon fiber composites might be the better choice. However, for applications requiring maximum toughness, titanium takes the lead.
Polycarbonate vs. Nylon
Polycarbonate stands out for its impact resistance and transparency. It’s perfect for parts that need to endure rough handling. Nylon, however, combines flexibility with durability. It bends without breaking, making it ideal for moving parts like hinges or gears. If your project involves constant motion, nylon’s adaptability makes it a strong contender. For static parts exposed to impacts, polycarbonate might be the better option.
PEEK vs. Standard PLA or ABS
PEEK outperforms standard PLA and ABS in almost every category. It resists high temperatures, harsh chemicals, and heavy loads. PLA and ABS, while easier to print, lack the advanced properties of PEEK. If your project demands high performance in challenging environments, PEEK is the clear winner. For simpler applications, PLA or ABS might suffice, but they can’t match PEEK’s strength and resilience.
How to Choose the Right Material for Your Needs
Selecting the right 3D printing material can feel overwhelming with so many options available. To make the best choice, you need to evaluate your project’s specific requirements and balance those needs with practical considerations. Let’s break it down step by step.
Assessing Your Application Requirements
Understanding your project’s demands is the first step in choosing the right material. Every application has unique needs, and identifying them helps narrow down your options.
Functional Needs: Strength, Flexibility, or Heat Resistance
Does it need to support heavy loads without breaking? If so, materials like titanium or carbon fiber composites might be your best bet.
Environmental Factors: Temperature, Humidity, or Chemical Exposure
Consider the environment where the part will be used. Will it face extreme heat or fluctuating temperatures? Heat-resistant materials like polycarbonate or PEEK can handle these conditions. If the part will be exposed to moisture or chemicals, nylon or PEEK provide excellent resistance. Ignoring environmental factors can lead to material failure, so it’s crucial to choose a material that can withstand the conditions it will face.
Balancing Strength with Other Factors
While strength is important, other factors like cost, availability, and ease of use also play a role in your decision. Balancing these considerations ensures you get the best results without unnecessary complications.
Cost and Availability
Some of the strongest materials, like titanium or PEEK, come with a higher price tag. If your budget is tight, you might need to explore more affordable options like polycarbonate or nylon. Availability also matters. Certain materials may not be readily accessible, especially if they require specialized printers or suppliers. Weighing cost and availability against your project’s needs helps you make a practical choice.
Printer Compatibility and Ease of Use
Not all materials work with every 3D printer. High-performance materials like PEEK often require advanced printers capable of handling high temperatures. On the other hand, materials like polycarbonate or nylon are more printer-friendly and easier to work with. If you’re new to 3D printing, starting with a material that’s easier to print can save you time and frustration. Always check your printer’s specifications before committing to a material.
By carefully assessing your application requirements and balancing them with practical considerations, you can confidently choose the right material for your project. Whether you need maximum strength, flexibility, or heat resistance, there’s a material out there that fits your needs perfectly.
Your choice should depend on your project’s requirements, environmental conditions, and budget.
FAQ
What is the strongest 3D printing material available?
Titanium takes the crown as the strongest 3D printing material. Its exceptional strength-to-weight ratio, corrosion resistance, and durability make it ideal for demanding applications like aerospace and medical implants. If you need unmatched toughness, titanium is your go-to choice.
Are carbon fiber composites stronger than titanium?
Carbon fiber composites offer a high strength-to-weight ratio and excellent rigidity, but they don’t surpass titanium in overall strength. Titanium excels in tensile strength and durability, while carbon fiber composites shine in lightweight applications. Your choice depends on whether weight reduction or maximum toughness is more important for your project.
Can I use polycarbonate for high-impact applications?
Yes, polycarbonate is an excellent choice for high-impact applications. It absorbs shocks and resists cracking, making it perfect for parts exposed to frequent collisions or rough handling. If you need a material that combines toughness with versatility, polycarbonate delivers.
Is nylon a good option for flexible parts?
Absolutely! Nylon offers a unique combination of flexibility and strength. It bends without breaking, making it ideal for moving parts like hinges or gears. If your project involves repeated motion or friction, nylon provides reliable performance.
How does PEEK compare to standard materials like PLA or ABS?
PEEK outperforms PLA and ABS in almost every way. It resists high temperatures, harsh chemicals, and heavy loads, making it suitable for advanced engineering and industrial applications. PLA and ABS are easier to print but lack the durability and strength of PEEK. For high-performance needs, PEEK is the superior choice.
What factors should I consider when choosing a 3D printing material?
You should focus on your project’s functional needs, environmental conditions, and budget. Ask yourself if the part requires strength, flexibility, or heat resistance. Consider the environment, such as exposure to heat, humidity, or chemicals. Balancing these factors ensures you pick the right material for your specific application.
Do stronger materials require special 3D printers?
Yes, some strong materials like PEEK or titanium need advanced 3D printers. These printers handle high temperatures and specialized processes. Materials like polycarbonate or nylon are more printer-friendly and work with standard FDM printers. Always check your printer’s specifications before selecting a material.
Are composites better than pure thermoplastics?
Composites often outperform pure thermoplastics in strength and durability. Additives like carbon fiber or glass fiber enhance the base material’s properties, creating stronger and lighter options. If your project demands high performance, composites are usually the better choice.
How can I test the strength of my 3D-printed parts?
You can test strength through methods like tensile strength testing, impact resistance testing, and heat deflection testing. These tests measure how much force, shock, or heat a material can handle before failing. Testing helps you ensure your parts meet the required performance standards.
Is cost a major factor when choosing strong materials?
Cost plays a significant role, especially for high-performance materials like titanium or PEEK. These materials are more expensive but offer unmatched strength and durability. If you’re on a budget, options like polycarbonate or nylon provide a balance of strength and affordability. Always weigh cost against your project’s requirements.