1. An overview of MIM technology and titanium alloy properties
MIM is a new kind of powder metallurgy near-net forming technique that blends conventional powder metallurgy procedures with contemporary plastic injection molding technology. The manufacture of intricate and very precise parts is possible with MIM technology. With mold design and adjustment, MIM technology can flexibly produce parts of different shapes and specifications, resulting in customized production that is appropriate for the efficient production of small and complex internal structural parts. It also has lower costs and higher production efficiency than traditional manufacturing methods—all while minimizing material waste and improving resource utilization efficiency.

Ti-MIM Products
2.Benefits and Difficulties

Characteristics of Titanium Powder for Metal Injection Molding
Titanium alloys’ exceptional strength-to-weight ratio, corrosion resistance, and biocompatibility have led to an increase in their application in the production of high-performance components. The MIM method effectively produces intricately formed, highly precise titanium alloy components, satisfying the demands of several industries for high-performance parts. High surface activity and ease of sintering and densification are key characteristics of titanium alloy powders, which are essential for enhancing the mechanical qualities of MIM products.
The ability to mass-produce intricately shaped metal parts with excellent material utilization and minimal waste is an advantage of MIM technology. The development of MIM titanium technology does face certain obstacles, though, including the high cost of low-oxygen spherical titanium alloy powders, a lack of supply, inconsistent feed preparation, product cracking and deformation during degreasing, and shrinkage control during sintering. Process parameter optimization and material improvement are required to address these issues.
3. Fields for applications
01/Aerospace
Titanium alloys’ high specific strength and resistance to corrosion make them useful in the aircraft industry. Complex and lightweight titanium alloy components, including connections, structural brackets, and engine blades for airplanes, can be produced using MIM technique. In addition to being lightweight, these components have superior mechanical qualities and fatigue resistance, which significantly raises the aircraft’s overall performance and safety.

Titanium alloy turbine engine blades
02/Medical Equipment
Titanium alloys are perfect for making medical devices because of their high corrosion resistance and biocompatibility. Complexly shaped titanium alloy medical items, including dental implants, orthopedic joint components, tweezers, surgical knife handles, and scissors, can be manufactured using MIM technology. The titanium alloy’s elastic modulus is especially near to that of human bones (10~30) GPa. The components may not only blend in well with human tissues after they are implanted, but they also have long-lasting superior mechanical qualities and resistance to corrosion. At the moment, it is the most remarkable biomaterial.

Titanium dental implants

TiMIM’s Ti-6Al-4V commercial permanent implant (port system) is used as a medication delivery tool to treat cancer.
03/Expensive Manufacturing
Automotive turbocharger parts, internal combustion engine, and gas turbine rotating and vibrating parts are just a few examples of the high-end manufacturing (precision instruments, automotive sector, etc.) applications for MIM steel alloy technology. In addition to their exceptional performance, these parts can greatly lower manufacturing costs and increase production efficiency. The titanium alloy Ti-6Al-2Sn-4Zn-2Mo is used in the United States to make automobile intake and exhaust valves. This alloy not only makes the vehicle lighter, but it also boosts the vehicle’s speed and valve life.
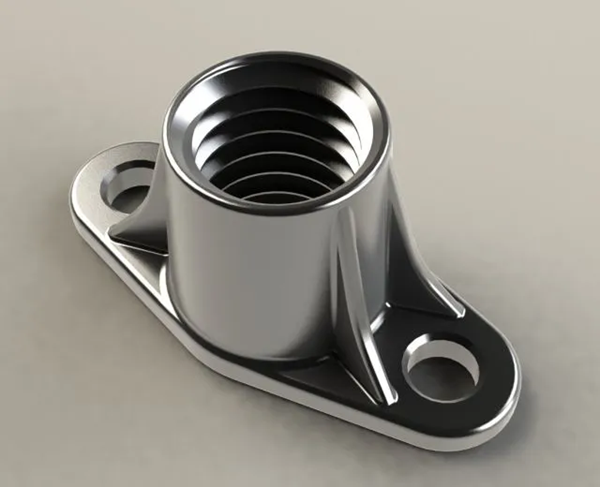
Titanium metal injection molding automotive parts

Parts for folding bicycle frames made of titanium alloy
4. Electronics for Consumers
The electrical 3C sector has made extensive use of titanium alloy injection molding. Since 2010, Apple has been utilizing MIM components and has consistently broadened and spearheaded the use of MIM. Chinese MIM businesses have become leaders in the consumer electronics industry thanks to the successful use of MIM components in mobile phones, including buttons, camera rings, card trays, power interface parts, and more. The fundamental components of consumer electronics like smartphones and smart wearables will advance in sophistication and complexity as they get lighter and thinner. In light of this, MIM technology’s potential applications will get more varied.
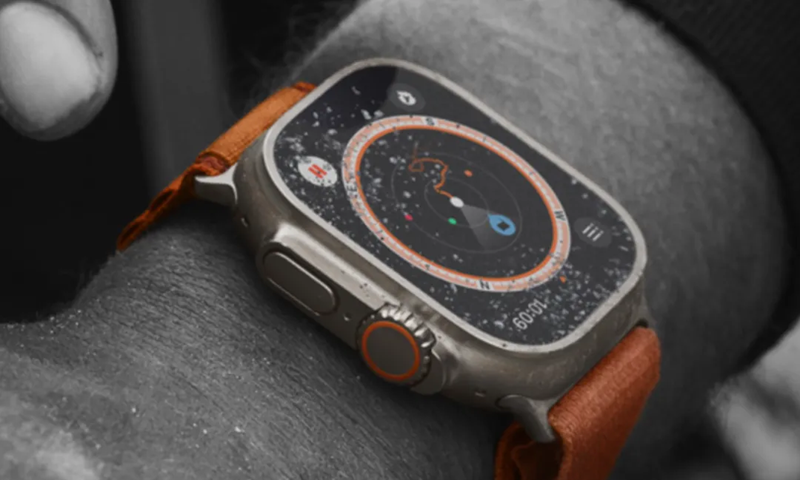
Smart watch with a titanium alloy frame
4. Future Development Trends
With the development of science and technology, MIM titanium alloy technology will continue to improve, such as: developing new high-performance titanium alloy powder materials and new titanium-based composite materials; improving the uniformity and stability of feeding; optimizing the degreasing and sintering process to reduce the deformation and cracking of products; applying advanced computer simulation technology to accurately control the shrinkage and dimensional accuracy of products. These technical improvements will further improve the performance and quality of titanium alloy MIM products and broaden their application areas. At the same time, with the development of personalized and intelligent manufacturing, titanium alloy MIM technology will also usher in new opportunities: by combining 3D printing technology with MIM technology, personalized titanium alloy parts can be quickly manufactured to meet the special needs of different customers; by introducing intelligent manufacturing technology, the automation and intelligence of the MIM production process can be realized, and production efficiency and product quality can be improved. In the future, green manufacturing will become an important trend of future development. Titanium alloy MIM technology should focus on environmental protection and sustainable development, such as developing non-toxic and harmless binders, reducing the emission of harmful gases during degreasing and sintering, and realizing the recycling of waste titanium alloy products. These measures will help promote the green development of titanium alloy MIM technology and achieve a win-win situation of economic and environmental benefits.
In conclusion
The technique for injection molding titanium alloy is advancing quickly in a number of industries that produce high-performance parts. Through ongoing advancements in process optimization, green manufacturing, and technical innovation, it can satisfy the market’s need for affordable parts with intricate, high-quality shapes. The prospects for titanium alloy MIM technology will expand with the creation of new materials and the use of digital intelligent manufacturing, opening up greater development space and application options across several industries.