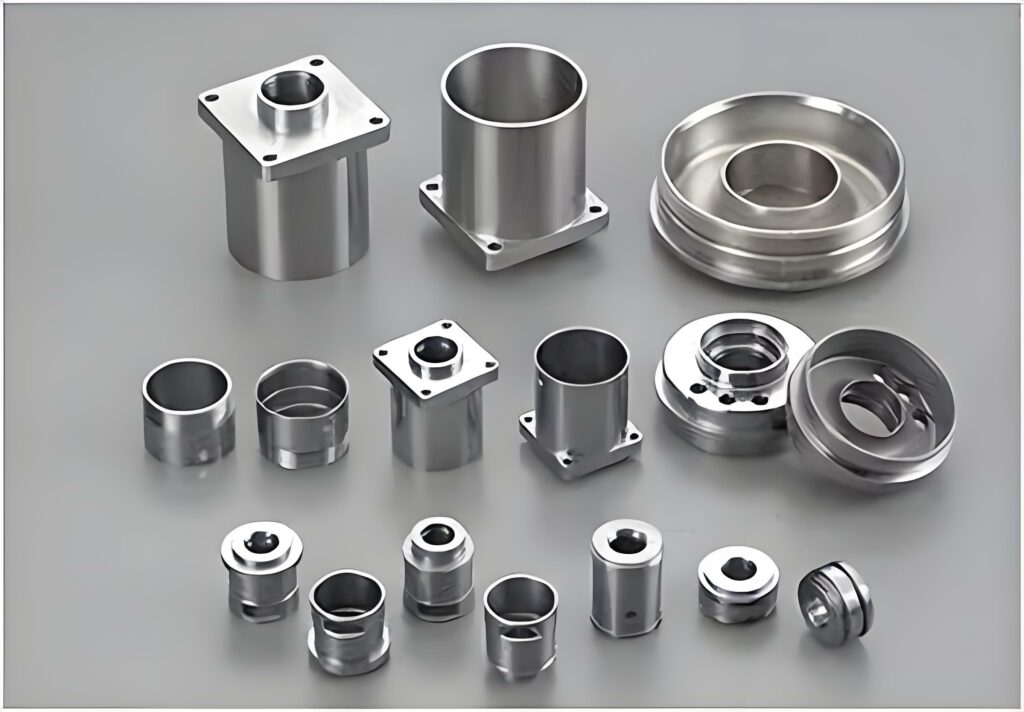
Titanium stands as a pivotal material in modern industries due to its exceptional properties. Its high strength-to-weight ratio and corrosion resistance make it indispensable in sectors like aerospace, medical, and automotive. The aerospace industry, in particular, relies heavily on titanium for components such as aircraft seats, shafts, and turbine parts. Understanding the challenges of titanium machining becomes crucial as its applications expand. Mastering these challenges ensures efficient production and technological advancement, highlighting the importance of this remarkable metal in today’s world.
Understanding the Challenges of Titanium Machining
Properties of Titanium
Titanium’s unique properties make it a sought-after material in various industries. Its high strength-to-weight ratio stands out as one of its most significant attributes. This property allows titanium to provide exceptional strength without adding unnecessary weight, making it ideal for aerospace and automotive applications. Engineers often choose titanium for components that require both durability and lightness.
Another remarkable property is its corrosion resistance. Titanium naturally forms a protective oxide layer, which shields it from environmental factors that cause corrosion. This makes it an excellent choice for medical implants and marine applications, where exposure to harsh conditions is common. The ability to withstand corrosion extends the lifespan of titanium components, reducing maintenance costs and enhancing reliability.
Common Machining Issues
Despite its advantageous properties, titanium presents several challenges during machining. One of the primary issues is tool wear and tear. Titanium’s hardness and strength can quickly degrade cutting tools, leading to frequent replacements and increased costs. The material’s toughness requires specialized tools that can withstand the stress of machining without losing their edge.
Another significant challenge is heat generation. Titanium’s low thermal conductivity means that heat accumulates at the cutting area during machining. This heat can cause tools to wear out faster and may even lead to tool failure. Effective heat management becomes crucial to prevent these issues. According to research, Swiss lathes have proven effective in managing heat during titanium machining, offering a potential solution to this problem.
Physical Phenomena in Titanium Machining
Heat Dissipation Challenges
Low Thermal Conductivity
Titanium’s low thermal conductivity poses significant challenges in machining. This property means that heat generated during the cutting process does not dissipate quickly. Instead, it accumulates at the cutting site. As a result, the temperature rises rapidly, which can lead to tool wear and potential damage to the workpiece. The slow heat flow through titanium exacerbates these issues, making effective heat management crucial in titanium machining.
Impact on Tool Life
The heat generated during titanium machining directly impacts tool life. High temperatures can degrade cutting tools, leading to frequent replacements and increased operational costs. Tools may lose their sharpness quickly, reducing their effectiveness and precision. This degradation affects the surface integrity of titanium parts, potentially compromising their geometric accuracy. Therefore, managing heat effectively becomes essential to prolong tool life and maintain the quality of machined components.
Work Hardening
Definition and Effects
Work hardening refers to the process where a material becomes harder and stronger as it is deformed. In titanium machining, this phenomenon occurs when the metal’s surface undergoes repeated stress and strain. The high temperatures generated during cutting can exacerbate work hardening, leading to increased hardness and strength of the titanium surface. This change in material properties can complicate the machining process, as it requires more force to cut through the hardened areas.
Implications for Machining
Work hardening presents several implications for titanium machining. As the material hardens, cutting tools must exert greater force to penetrate the surface. This increased force can lead to higher tool wear and potential tool failure. Additionally, work hardening can reduce the fatigue strength of titanium components, affecting their long-term performance and reliability. Machinists must carefully manage cutting parameters to minimize work hardening and ensure the production of high-quality titanium parts.
Scientific Research Findings:
- Studies on Heat Dissipation and Work Hardening in Titanium Machining highlight that titanium’s low thermal conductivity and tendency to work harden complicate machining operations. These factors contribute to tool wear and potential distortion of the workpiece.
- The high temperatures generated during cutting can damage the surface integrity of titanium alloy parts, leading to reduced geometric accuracy and work hardening, which lowers their fatigue strength.
Technological Solutions for Titanium Machining
In the realm of titanium machining, technological advancements play a crucial role in overcoming the inherent challenges. These solutions not only enhance efficiency but also improve the quality of the machined components.
Advanced Cutting Tools
Selecting the right cutting tools is vital for successful titanium machining. The use of coated carbide tools has become a standard practice. These tools feature coatings such as Titanium Nitride (TiN), Titanium Carbonitride (TiCN), and Aluminum Titanium Nitride (AlTiN). These coatings significantly enhance wear resistance and reduce friction, allowing the tools to withstand the high temperatures and pressures typical in titanium machining. By minimizing tool wear, these coatings extend the lifespan of the cutting tools, leading to cost savings and improved productivity.
High-speed steel tools also find their place in titanium machining. Although not as durable as carbide tools, they offer flexibility in certain applications. High-speed steel tools can be effective when machining titanium at lower speeds, providing a balance between performance and cost. The choice between carbide and high-speed steel depends on the specific requirements of the machining operation, including the desired surface finish and production volume.
Cooling Techniques
Effective cooling techniques are essential in managing the heat generated during titanium machining. Cryogenic cooling represents a cutting-edge solution. This technique involves using liquid nitrogen to cool the cutting area, drastically reducing the temperature. Cryogenic cooling not only prolongs tool life but also improves the surface finish of the machined parts. The rapid cooling prevents the workpiece from reaching temperatures that could cause distortion or work hardening.
Another innovative approach is the use of high-pressure coolant systems. These systems deliver coolant at high pressures directly to the cutting zone. The intense coolant flow effectively removes heat and chips from the cutting area, reducing tool wear and enhancing machining precision. High-pressure coolant systems are particularly beneficial in operations involving deep cuts or complex geometries, where heat management becomes critical.
“By integrating technological solutions and adopting appropriate tool structures and strategies, precision machining of titanium alloys can be significantly improved, resulting in high-quality components, extended tool life, and overall process efficiency.”
These technological solutions underscore the importance of adapting to the unique demands of titanium machining. By leveraging advanced cutting tools and innovative cooling techniques, manufacturers can achieve superior results, ensuring that titanium continues to be a valuable material across various industries.
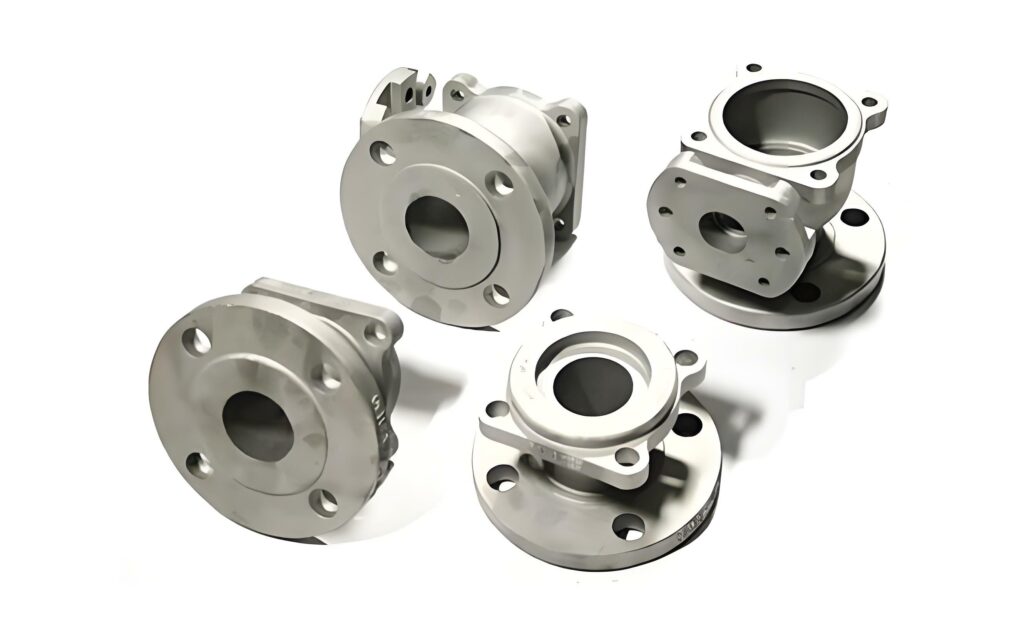
Tool Structures and Machining Strategies
In the realm of titanium machining, the structure of tools and the strategies employed play a pivotal role in achieving precision and efficiency. Understanding these elements can significantly enhance the machining process, ensuring high-quality outcomes.
Tool Geometry
The geometry of cutting tools directly influences the effectiveness of titanium machining. Engineers must carefully consider the design to optimize performance.
Optimal Cutting Angles
Selecting the right cutting angles is crucial for successful titanium machining. The high strength and low thermal conductivity of titanium necessitate specific angles to minimize tool wear and enhance cutting efficiency. A sharper angle can reduce the cutting force required, thereby decreasing the stress on the tool. This adjustment helps in managing the heat generated during the process, which is vital given titanium’s tendency to retain heat.
Chip Breaker Design
Chip breaker design is another critical aspect of tool geometry. Titanium’s ‘gummy’ nature often results in long, continuous chips that can wrap around the tool, causing damage and inefficiency. A well-designed chip breaker can fragment these chips into smaller pieces, preventing them from interfering with the machining process. This design not only improves the safety and cleanliness of the operation but also extends the life of the cutting tool by reducing the risk of chip-induced wear.
Machining Parameters
Beyond tool geometry, the parameters set during titanium machining significantly impact the process’s success. These parameters must be meticulously controlled to accommodate titanium’s unique properties.
Speed and Feed Rates
Controlling speed and feed rates is essential in titanium machining. High-speed machining can lead to excessive heat generation, which may cause tool wear and affect the quality of the machined surface. Therefore, operators often use lower speeds to manage heat effectively. However, this must be balanced with feed rates to maintain productivity. An optimal combination of speed and feed rates ensures efficient material removal while preserving tool integrity.
Depth of Cut
The depth of cut is another parameter that requires careful consideration. A deeper cut increases the contact area between the tool and the titanium, which can lead to higher temperatures and increased tool wear. Conversely, a shallow cut may prolong machining time and reduce efficiency. Finding the right balance is crucial. Operators must adjust the depth of cut based on the specific requirements of the task and the characteristics of the titanium alloy being machined.
“Precision machining of titanium alloys demands a comprehensive understanding of tool structures and machining strategies. By optimizing tool geometry and carefully controlling machining parameters, manufacturers can overcome the challenges posed by titanium’s unique properties.”
Case Studies and Industry Examples
Aerospace Industry
Application of Titanium Components
The aerospace industry heavily relies on titanium machining due to the metal’s exceptional properties. Engineers use titanium to manufacture critical components such as aircraft frames, engine parts, and landing gear. These components benefit from titanium’s high strength-to-weight ratio, which enhances fuel efficiency and performance. Additionally, titanium’s corrosion resistance ensures longevity and reliability in harsh environments. The demand for lightweight yet durable materials makes titanium an ideal choice for aerospace applications.
Machining Innovations
Innovations in titanium machining have significantly advanced the aerospace sector. Manufacturers have developed specialized cutting tools and techniques to address the challenges posed by titanium’s hardness and low thermal conductivity. For instance, the use of coated carbide tools has become prevalent. These tools withstand high temperatures and reduce tool wear, improving machining efficiency. Moreover, high-pressure coolant systems effectively manage heat during machining, preventing tool degradation and ensuring precision. These innovations have enabled the production of high-quality titanium components, meeting the stringent requirements of the aerospace industry.
Medical Device Manufacturing
Precision Requirements
In the medical field, titanium machining plays a crucial role in producing implants and devices. Titanium’s biocompatibility makes it suitable for medical applications, including joint replacements and dental implants. Precision is paramount in this industry, as components must meet exact specifications to ensure patient safety and comfort. CNC machining technology allows manufacturers to achieve the necessary precision, producing intricate designs with tight tolerances. This precision ensures that medical devices function correctly and integrate seamlessly with the human body.
Overcoming Machining Challenges
Medical device manufacturers face unique challenges in titanium machining. The need for precision and the complexity of designs require advanced machining techniques. Cryogenic cooling has emerged as a solution to manage heat and maintain tool integrity. By using liquid nitrogen, manufacturers can cool the cutting area rapidly, reducing the risk of work hardening and distortion. Additionally, the development of high-speed steel tools provides flexibility in machining operations, allowing for adjustments based on specific requirements. These advancements have enabled the production of reliable and effective medical devices, enhancing patient outcomes.
“The integration of innovative machining techniques and technologies has revolutionized the production of titanium components in both aerospace and medical industries, ensuring high-quality outcomes and advancing technological capabilities.”
Titanium machining presents unique challenges due to the metal’s properties, such as its high strength and low thermal conductivity. These challenges require innovative solutions. Manufacturers have developed advanced cutting tools and cooling techniques to address these issues. Continued research and innovation remain crucial for improving titanium machining processes. As industries demand more efficient production, understanding the design for manufacturability becomes essential. Simplifying complex geometries and incorporating features that ease machining operations can lead to better quality parts. The future of titanium machining looks promising with ongoing advancements in technology and strategies.