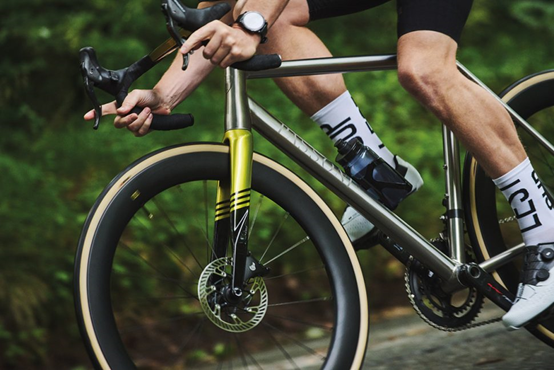
1. Characteristics of Titanium
Elegant Simplicity
Our frames’ elegant lines highlight the natural beauty of titanium. The lightly brushed and polished titanium emits a soft, unique luster. We choose not to paint the frames because the timeless allure of titanium needs no embellishment. Its bare beauty is irresistible and impossible to ignore.
Strong and Flexible
Perfect riding depends on balancing lateral stiffness for power transmission and vertical compliance to absorb road feedback. Titanium’s unparalleled strength-to-weight ratio ensures rigidity while providing enough flex to make you feel like you’re floating.
Resilient Durability
Titanium remains unyielding under pressure. Its exceptional fatigue life and impact resistance, coupled with a natural titanium dioxide coating, ensure it can withstand the harshest conditions. It will never rust, rot, or corrode.
Lightweight and Strong
The lightweight nature of titanium does not compromise its strength. It offers high performance without adding weight, making it an ideal choice for applications demanding durability and maneuverability.
Environmentally Friendly
Titanium is abundant and recyclable, making it an eco-friendly choice. Its long lifespan reduces the need for frequent replacements, contributing to sustainability.

2. Comparison with Traditional Materials
Comparison with Steel
Steel is one of the traditional materials for bicycle frames, known for its high strength and durability. However, steel is quite heavy, making it more demanding to ride. Additionally, steel is prone to rust and requires regular maintenance.
Comparison with Aluminum
Aluminum alloy is also a common bicycle material. Aluminum is lightweight, approximately 30% lighter than steel, and has good corrosion resistance. However, aluminum has a shorter fatigue life and is more prone to cracking over prolonged use. Additionally, aluminum’s higher rigidity can make the ride feel harsher compared to the comfort offered by titanium alloy.
Comparison with Carbon Fiber
Carbon fiber is a newer bicycle material that is extremely lightweight and offers high strength and rigidity. However, its high cost makes it unsuitable for the general public, being more appropriate for competitive racing bicycles.
Comparison Table
Comparison Item | Titanium Alloy | Steel | Aluminum | Carbon Fiber |
Weight | Density of about 4.5 g/cm³, about 50% lighter than steel | Density of about 7.8 g/cm³, heavier | Density of about 2.7 g/cm³, about 30% lighter than steel | Extremely lightweight, suitable for high-performance and racing bicycles |
Corrosion Resistance | Does not rust, no need for paint protection | Prone to rust, requires regular maintenance and paint protection | Good corrosion resistance, does not easily rust | Does not rust but requires a protective coating |
Strength and Durability | High strength and good fatigue resistance, can withstand repeated stress | High strength and durability, good fatigue resistance | High strength, but shorter fatigue life, prone to cracking after prolonged use | High stiffness-to-weight ratio, provides efficient power transfer but is prone to damage |
Comfort | Good elasticity and shock absorption, provides a comfortable riding experience | Good elasticity, provides a comfortable riding experience | Higher rigidity, feels harder while riding, not as comfortable as titanium alloy | High rigidity, provides efficient power transfer but less comfort |
Price | High extraction and processing costs, expensive | Relatively low cost, suitable for mass production | Lower cost, suitable for mass production | Very expensive, especially in the high-end market |
Processing Difficulty | Welding and processing require special techniques and equipment, difficult | Easy to repair, can be fixed by welding and other methods | Relatively easy to process but has a shorter fatigue life | Complex processing, highly formable, but difficult to repair once damaged |
Environmental Impact | Recyclable, environmentally friendly | Recyclable, environmentally friendly | Recyclable, environmentally friendly | Limited recyclability, not as environmentally friendly as metal materials |
Specific data examples:
- Titanium alloy: Density approximately 4.5 g/cm³, tensile strength approximately 900 MPa, elastic modulus approximately 110 GPa.
- Steel: Density approximately 7.8 g/cm³, tensile strength approximately 400-550 MPa, elastic modulus approximately 210 GPa.
- Aluminum: Density approximately 2.7 g/cm³, tensile strength approximately 300-400 MPa, elastic modulus approximately 70 GPa.
- Carbon fiber: Density approximately 1.6 g/cm³, tensile strength approximately 3500 MPa, elastic modulus approximately 230 GPa.
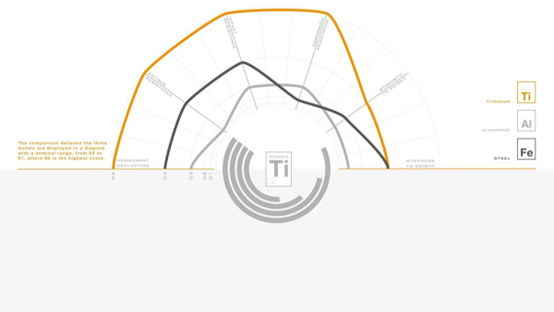
In summary, titanium alloy frames have significant advantages in durability, comfort, and corrosion resistance. However, their high cost and processing difficulty make them a choice for the high-end market. In contrast, steel and aluminum frames are more advantageous in terms of price and processing but lack in weight and durability. Carbon fiber frames excel in weight and performance, but their high cost and vulnerability limit their widespread use.
3.Which titanium materials can be used for bicycle components
Titanium materials have been widely used in high-end bicycle components due to their excellent performance, but not all types are suitable for bicycle manufacturing. The most commonly used are pure TA1, Ti-3Al-2.5V alloy, and Ti-6Al-4V alloy. The former has good machinability and weldability, while the latter is known for its high strength and lightweight.
Titanium Material and its Performance Parameters
Material Type | Primary Components | Density (g/cm³) | Tensile Strength (MPa) | Yield Strength (MPa) | Elastic Modulus (GPa) | Main Applications |
TC4 (Ti-6Al-4V) | Titanium, Aluminum, Vanadium | 4.43 | 895-930 | 825-860 | 110 | Frame, handlebar, seat post, screws |
TA1 (Pure Titanium) | Titanium | 4.51 | 240-370 | 170-240 | 105 | Frame, screws |
TC2 (Ti-3Al-2.5V) | Titanium, Aluminum, Vanadium | 4.48 | 620-700 | 483-620 | 105 | Frame, handlebar, seat post |
Performance characteristics of titanium materials
- TC4 (Ti-6Al-4V)
- Density: 4.43 g/cm³
- Tensile Strength: 895-930 MPa
- Yield Strength: 825-860 MPa
- Elastic Modulus: 110 GPa
- Applications: Widely used in components such as frames, handlebars, seat posts, and screws due to its high strength and good corrosion resistance.
- TA1 (Pure Titanium)
- Density: 4.51 g/cm³
- Tensile Strength: 240-370 MPa
- Yield Strength: 170-240 MPa
- Elastic Modulus: 105 GPa
- Applications: Mainly used in frames and screws due to its good biocompatibility and corrosion resistance.
- TC2 (Ti-3Al-2.5V)
- Density: 4.48 g/cm³
- Tensile Strength: 620-700 MPa
- Yield Strength: 483-620 MPa
- Elastic Modulus: 105 GPa
- Applications: Commonly used in frames, handlebars, and seat posts due to its good machinability and moderate strength.
TC4, TA1, and TC2 are common types of titanium materials, each with different performance characteristics suitable for various bicycle components.
4.Which high-performance bicycle components use titanium alloy?
With the development of titanium alloy technology, an increasing number of bicycle components are starting to use titanium alloy materials. In addition to traditional frames and forks, many high-end bicycles are incorporating titanium alloys for components such as stems, seat posts, pedals, chains, screws, and more. The use of these components not only significantly reduces the weight of the bicycle but also enhances overall durability and comfort.
5. Comparison between Traditional Machining Methods and New Metal 3D Printing Technology
Processing method | Process description | Advantages | Disadvantages |
Precision Casting | Through investment casting technology, the titanium alloy is melted and poured into a mold to form. | Suitable for mass production and relatively low cost. | The process is complex, the production cycle is long, and the part accuracy and surface quality are limited. |
CNC machining | uses computer numerical control machine tools to perform precision cutting and machining of titanium alloys. | High precision, high quality, suitable for the manufacture of complex parts. | The processing time is long, the material is wasted, and the cost is high. |
Wire cutting | Uses electric spark wire cutting technology to cut and shape titanium alloy. | Suitable for precision processing of high-hardness materials. | The processing speed is slow and suitable for small batch production. |
Welding | Titanium alloy parts are joined together by welding techniques such as tungsten inert gas welding (TIG). | Suitable for assembly of complex structures. | Welding residual stress may cause deformation and fatigue failure of parts. |
Surface treatment | Titanium alloy parts are subjected to surface treatment such as anodizing and electroplating to improve corrosion resistance and aesthetics. | This improves the durability and appearance quality of the parts. | This increases manufacturing costs and process complexity. |
3D printing technology | Process description | Advantages | Disadvantages |
Laser melting (SLM) | Uses a high-energy laser beam to melt titanium alloy powder layer by layer and solidify it into shape. | High precision, strong ability to form complex structures, and high material utilization. | The equipment cost is high, suitable for small batch production and customized products. |
Electron beam melting (EBM) | Uses an electron beam to melt titanium alloy powder layer by layer and solidify it into shape. | Suitable for the manufacture of large-size parts with fast molding speed. | The equipment cost is high and the operating environment requirements are strict. |
6. Using 3D printing technology to manufacture titanium components for high-performance bicycles has several key advantages:
- Lightweight: 3D printing technology can create extremely lightweight titanium components, which is crucial for high-performance bicycles. Titanium itself has a high strength-to-weight ratio, and through 3D printing technology, designs can be further optimized to reduce unnecessary material usage, thus reducing weight. For example, the full titanium alloy frame manufactured by Angel Cycle Works using 3D printing technology is 400 grams lighter than previous versions.
- High Strength: Titanium alloys like TC4 (Ti-6Al-4V) have extremely high strength and durability, making them suitable for manufacturing bicycle components that need to withstand high stress. 3D printing technology can precisely control the material’s microstructure, ensuring that the printed titanium components have excellent mechanical properties.
- Complex Designs: 3D printing technology allows for the manufacturing of complex geometries and internal structures, which are difficult to achieve with traditional manufacturing methods. For example, 3D printing can create internal channels, hollow or lattice-filled components to reduce weight while maintaining strength. This design freedom allows bicycle components to achieve lightweight and efficient aerodynamic performance while maintaining strength.
- Reduced Material Waste: 3D printing is an additive manufacturing technology that uses only the amount of material needed to manufacture the part, reducing waste of raw materials. Compared to traditional subtractive manufacturing (such as CNC machining), 3D printing is more environmentally friendly and cost-effective.
- Personalized Customization: 3D printing technology can be used to customize components according to the specific needs of customers, creating unique bicycle components. This is particularly important for the high-end market and professional athletes who need to customize components according to their personal riding styles and requirements.
- Shortened Design Cycle: 3D printing technology can quickly manufacture prototypes and final products, shortening the product development cycle. This is an important advantage for bicycle manufacturers who need to quickly respond to market demands and iterate on products.
- Reduced Welding Stress: Titanium components manufactured using 3D printing technology can avoid welding residual stress caused by complex structure welding, reducing the risk of deformation and fatigue failure, thereby improving the overall quality and reliability of components.
- Cost Reduction: The biggest difficulty in traditional titanium alloy processing lies in welding, which requires very skilled welders. Otherwise, the firmness of the welding will affect the safety of the whole vehicle, so the wages of workers are particularly high. 3D printing solves this problem very well, greatly reducing manufacturing costs.
7.Surface Treatment of Titanium Alloy Parts
There are various surface treatment methods for titanium alloy parts, aimed at improving their corrosion resistance, wear resistance, anti-fretting wear resistance, and high-temperature oxidation resistance. Here are several common surface treatment methods for titanium alloys and their detailed explanations:
- Electroplating Electroplating is the process of depositing a layer of metal, such as nickel, hard chromium, or silver, on the surface of titanium alloy to improve its conductivity, solderability, and wear resistance. Since there is a dense oxide film on the surface of titanium alloy, pretreatment must be carried out before electroplating to remove this oxide film.
- Anodizing Anodizing is the process of forming an oxide film on the surface of titanium alloy through electrochemical reactions. This method can significantly improve the corrosion resistance and wear resistance of titanium alloys and can achieve different coloring effects by adjusting the electrolyte composition and voltage.
- Coating Technology Coating technologies include thermal spraying, PVD (Physical Vapor Deposition), CVD (Chemical Vapor Deposition), etc., which form coatings such as TiO, TiN, and TiC on the surface of titanium alloys, significantly improving their wear resistance and corrosion resistance.
- Surface Oxidation Treatment Surface oxidation treatment involves generating an oxide film on the surface of titanium alloy through chemical or electrochemical methods to enhance its wear resistance and biocompatibility. This method is commonly used in the surface treatment of biomedical titanium alloys.
- Chemical Plating Chemical plating is the process of depositing a metal coating, such as nickel or copper, on the surface of titanium alloy through chemical reactions to improve its corrosion resistance and conductivity. This method does not require electricity and is suitable for parts with complex shapes.
- Sandblasting Sandblasting involves removing oxide layers and contaminants from the surface of titanium alloys by high-pressure abrasive blasting, increasing surface roughness and improving the adhesion of subsequent coatings or electroplating.
- Chemical Polishing Chemical polishing achieves flat polishing by the oxidation-reduction reaction of metals in a chemical medium, improving surface smoothness and aesthetics.
- Laser Etching Laser etching uses a high-energy laser beam to etch fine patterns or structures on the surface of titanium alloys, commonly used for decorative and functional surface treatments.
In conclusion, there are various surface treatment methods for titanium alloy parts, each with its unique advantages and applications. By selecting the appropriate surface treatment method, the performance of titanium alloy parts can be significantly improved to meet the requirements of different application fields.
8. Titanium Parts Manufactured by JH TI
At JH TI, we have successfully manufactured a variety of titanium alloy parts including frames, rear parts, cranks, guide wheels, stems, and seats. We welcome inquiries for these and other titanium components. Here is a list of some of the titanium alloy parts we manufacture:
- Frames
- Rear parts
- Cranks
- Guide wheels
- Stems
- Seats
Feel free to contact us for inquiries and quotes on these titanium parts and more.
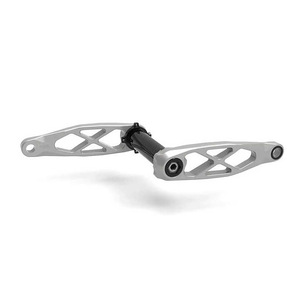
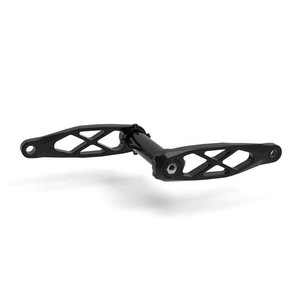

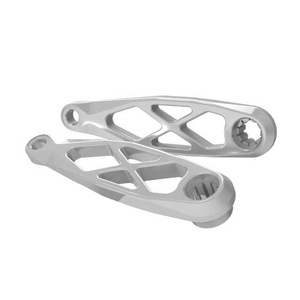
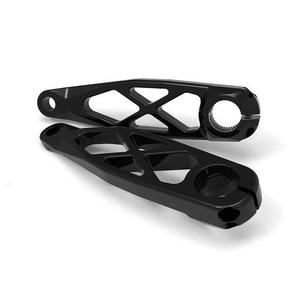
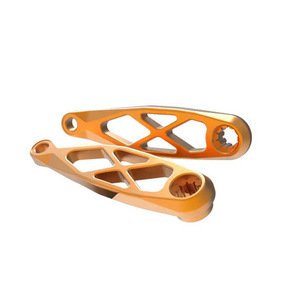
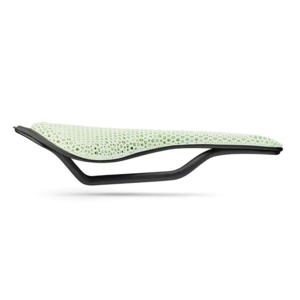
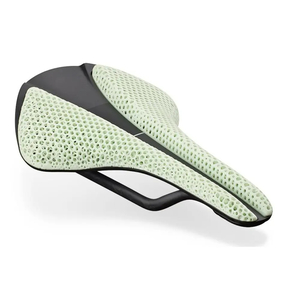
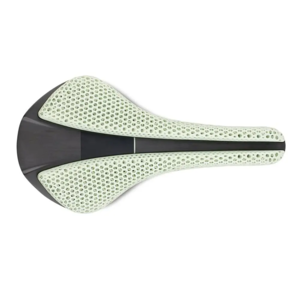
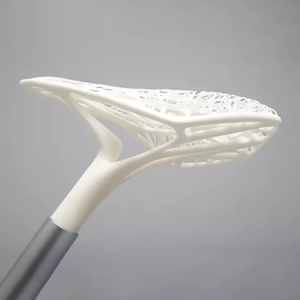
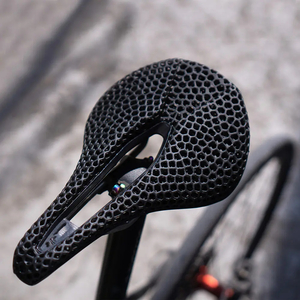
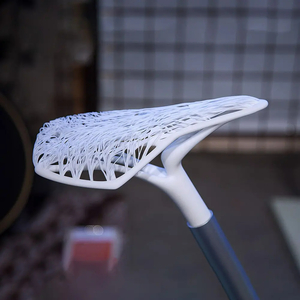