Introduction
Titanium alloys have revolutionized modern manufacturing, offering exceptional properties that make them indispensable in various high-tech industries. Among these, Ti-6Al-4V stands out due to its unique combination of strength, lightness, and corrosion resistance. This article delves into the specifics of Ti-6Al-4V, exploring its properties, applications, and the transformative role of customized OEM 3D printing in its utilization.
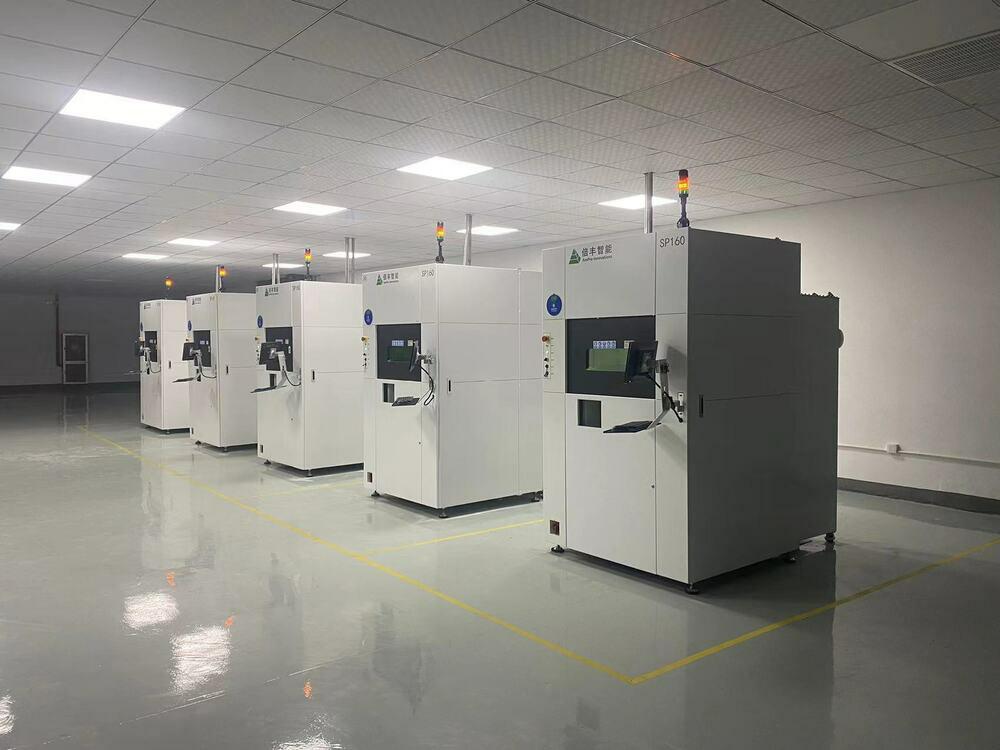
Understanding Titanium Alloy Ti-6Al-4V
Composition and Properties of Ti-6Al-4V
Chemical Composition
Ti-6Al-4V, also known as Grade 5 titanium, is an alpha-beta alloy primarily composed of titanium (approximately 90%), aluminum (6%), and vanadium (4%). The aluminum acts as a strength enhancer while stabilizing the alpha phase, whereas vanadium stabilizes the beta phase, thus contributing to the alloy’s robustness and thermal stability. This balanced composition results in a material that can withstand extreme conditions while maintaining its structural integrity.
Mechanical Properties
Ti-6Al-4V is celebrated for its high strength-to-weight ratio, making it ideal for applications requiring lightweight yet strong materials. It boasts excellent corrosion resistance, particularly against chloride-induced stress corrosion cracking, which is crucial for marine and chemical processing environments. Furthermore, its biocompatibility makes it suitable for medical implants. The alloy can endure high temperatures (up to 400°C) and has impressive fatigue resistance, making it a preferred choice in demanding industries like aerospace and automotive.
Comparison with Other Titanium Alloys
When compared to other titanium alloys, Ti-6Al-4V demonstrates superior mechanical properties and versatility. For instance, while Ti-3Al-2.5V offers good weldability and is often used in aircraft hydraulic systems, it lacks the same high-temperature performance and strength as Ti-6Al-4V. Conversely, Ti-6Al-2Sn-4Zr-2Mo, used in gas turbine engines, provides excellent high-temperature performance but at a higher cost and with reduced ductility. Therefore, Ti-6Al-4V is often the go-to alloy for applications requiring a balance of strength, weight, and performance.
Applications of Ti-6Al-4V
Aerospace and Defense
In the aerospace and defense sectors, Ti-6Al-4V is extensively used for critical components such as jet engine parts, airframe structures, and fasteners. Its ability to maintain strength at high temperatures and resist corrosion in harsh environments ensures reliability and safety. For example, turbine blades made from Ti-6Al-4V benefit from reduced weight, leading to improved fuel efficiency and performance.
Medical and Dental
The biocompatibility and strength of Ti-6Al-4V make it ideal for medical and dental applications. It is used in joint replacements, bone screws, and dental implants, where it promotes osseointegration, leading to better patient outcomes. The alloy’s non-toxic and non-reactive nature ensures it does not adversely affect the body, which is paramount for long-term implant success.
Automotive and Motorsports
Ti-6Al-4V is also a favorite in the automotive and motorsports industries, where performance and weight reduction are critical. Components such as connecting rods, valves, and suspension parts benefit from the alloy’s lightweight and high-strength properties. In motorsports, where every gram counts, Ti-6Al-4V contributes to superior vehicle dynamics and speed.
The Role of 3D Printing in Customizing Ti-6Al-4V Parts
Advantages of 3D Printing for Titanium Alloys
Design Flexibility
3D printing, or additive manufacturing, allows for unprecedented design flexibility. Complex geometries that are impossible or cost-prohibitive with traditional manufacturing methods can be easily achieved. This capability reduces material waste and production costs, enabling the creation of lightweight structures with optimized strength and functionality.
Speed and Efficiency
3D printing significantly accelerates the production process. Rapid prototyping allows for quicker iteration cycles, reducing the time from design to final product. This efficiency is particularly beneficial for custom OEM parts, where small batch production and specific modifications are often required.
Enhanced Performance
Additive manufacturing enables the creation of parts with enhanced performance characteristics. For Ti-6Al-4V, this means leveraging its mechanical properties to produce parts that are not only lighter but also stronger and more resilient. Optimized designs can enhance thermal performance, reduce fatigue, and improve overall part longevity.
Customized OEM Solutions
Tailored to Specific Requirements
Customized OEM 3D printing allows manufacturers to meet unique specifications and tolerances that standard manufacturing processes cannot. This customization is crucial in industries such as aerospace and medical, where precision and reliability are non-negotiable.
Collaboration with OEMs
Successful OEM collaborations often involve close partnerships, where both parties work together to achieve the desired outcomes. This collaborative approach ensures that the final product meets all technical and performance requirements. Case studies, such as the development of custom aerospace components or medical devices, highlight the effectiveness of such partnerships.
Quality Control and Certification
Quality control is paramount in 3D printing, particularly for critical applications. Rigorous testing and certification processes ensure that each part meets industry standards and regulations. Certifications such as ISO 13485 for medical devices and AS9100 for aerospace components provide assurance of quality and reliability.

Challenges and Future Trends in Ti-6Al-4V 3D Printing
Overcoming Technical Challenges
Printability Issues
While Ti-6Al-4V is well-suited for 3D printing, it presents specific challenges, such as residual stresses and warping. Advances in printing technology and process optimization, including controlled cooling rates and support structure design, are helping to mitigate these issues, ensuring higher quality prints.
Post-Processing Requirements
Post-processing is crucial for achieving the desired properties and surface finish in 3D printed Ti-6Al-4V parts. Techniques such as heat treatment, machining, and surface finishing enhance the mechanical properties and appearance of the final product. These steps are essential to meet the stringent requirements of aerospace and medical applications.
Future Trends and Innovations
Advancements in 3D Printing Technology
The future of 3D printing for Ti-6Al-4V looks promising with ongoing advancements in technology. Emerging techniques like electron beam melting (EBM) and laser powder bed fusion (LPBF) are improving print quality, speed, and efficiency. These innovations are set to expand the capabilities and applications of titanium 3D printing.
Market Growth and Opportunities
The market for titanium 3D printing is projected to grow significantly, driven by increasing demand from aerospace, medical, and automotive sectors. Businesses that invest in this technology can capitalize on the growing need for high-performance, customized components. The potential for innovation and competitive advantage makes this an exciting area for investment.
Sustainability and Environmental Impact
Sustainability is becoming a critical focus in manufacturing. 3D printing contributes to sustainability by reducing material waste and energy consumption compared to traditional manufacturing methods. The ability to produce lightweight components also contributes to energy efficiency in applications such as aerospace and automotive, further reducing the environmental footprint.

Conclusion
Ti-6Al-4V’s exceptional properties and versatility make it a cornerstone in modern manufacturing. The integration of 3D printing technology enhances its potential, enabling customized OEM solutions that meet specific industry requirements. As technology advances and market demand grows, the future of Ti-6Al-4V 3D printing looks bright, promising continued innovation and sustainability in various high-tech industries.
Resource
Ti-6Al-4V—— Wikipedia
Ti-6Al-4V 3D printing——JHMIM China