3D printing, or additive manufacturing, has transformed medical device design with its capacity to create highly customized, precise, and complex products. This technology, now deeply embedded in academic curricula and increasingly affordable due to declining costs, has made remarkable strides over the past decade, offering new ways to tackle healthcare challenges.
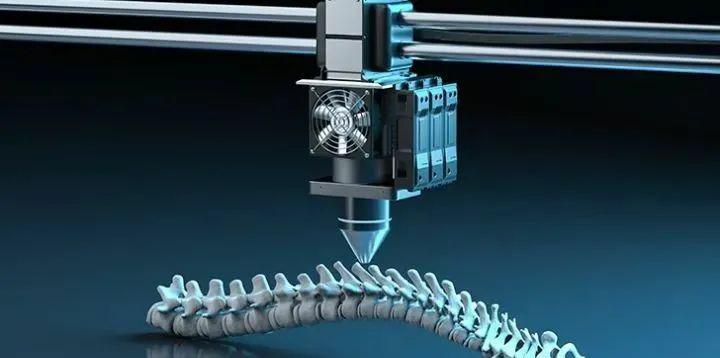
3D PRINGTING MEDICAL
What Is 3D Printing and How Does It Work?
3D printing is a process that constructs three-dimensional objects layer by layer, following a preset digital design. This technology can produce objects in intricate geometries previously impossible to manufacture. The digital model is typically created using computer-aided design (CAD) software or sourced from patient imaging data such as MRI or CT scans. Materials used include plastics, metals, ceramics, and composites. The production process is computer-controlled, resulting in a highly efficient, accurate, and customizable manufacturing method.
Benefits of 3D Printing in Medical Device Design
Customization:
3D printing allows for seamless customization of implants, prostheses, and surgical guides to align precisely with the patient’s unique anatomy. CAD models can be derived from imaging data like CT scans to create devices perfectly tailored to the patient. This ability to customize products reduces complications, improves patient outcomes, and enhances patient comfort.
Speed:
The technology accelerates the design iteration process, enabling rapid changes and adjustments without requiring additional equipment or specialized tooling. This speed benefits the development of prototypes and offers investors an early preview of the final product.
Reduced Risk:
The rapid prototyping ability of 3D printing allows designers to identify and rectify potential issues early, reducing risks and minimizing unknowns. Frequent iterations enable earlier testing and validation, ensuring a more refined design and production process.
Applications of 3D Printing in Medical Devices
Custom Implants and Prosthetics:
Traditionally manufactured prostheses and implants often require significant adjustments to fit the patient’s anatomy. 3D printing resolves this by creating devices precisely tailored to the patient, improving comfort, reducing risks, and minimizing healthcare costs associated with corrective procedures.
Anatomical Models:
Accurate 3D-printed anatomical models enable surgeons to practice and refine their approach before performing surgery, reducing surgical errors and improving patient outcomes. Additionally, these models help medical students and junior doctors grasp complex anatomical structures more easily.
Surgical Instruments:
Cutting and drilling guides ensure precision during surgical procedures. By using 3D printing to customize these tools, surgeries become more accurate and minimally invasive, leading to quicker recovery times and lower complication rates.
Human Tissue Repair 3D printing technology plays a significant role in reconstructing damaged human tissue. It can rapidly produce bio-sealed, highly transparent surfaces that closely mimic the natural tissue structure. These materials have excellent biocompatibility, providing a suitable environment for cells to grow and form three-dimensional structures. This capability allows researchers to test tissue viability in human models before transplanting the new tissue back into patients. Such advancements pave the way for more efficient and successful tissue repair procedures, reducing the risk of rejection and improving patient recovery.
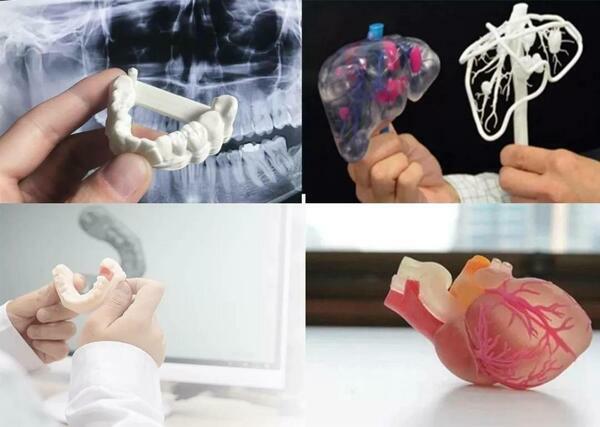
Challenges of 3D Printing in Medical Device Design
Cleaning and Sterilization:
The intricate structures created through additive manufacturing can be difficult to clean and sterilize thoroughly. Regulatory bodies like the FDA require stringent validation to ensure the complete removal of any residual materials before a device can be approved for clinical use.
Cost:
While the cost of prototyping has decreased, specific materials, particularly metals, remain relatively expensive. This challenge is compounded for biomedical applications requiring high-quality or specialty materials.
Future Growth Opportunities in Medical 3D Printing
Personalized Medicine:
3D-printed drugs can be custom-manufactured in specific dosages tailored to individual patients. This innovation reduces waste, speeds up clinical trials, and opens doors to faster, more affordable drug development.
Bioprinting:
Bioprinting, a technique involving the layer-by-layer deposition of bio-ink (living cells), aims to create artificial tissues, skin grafts, and even organs for transplantation. Though still in experimental phases, advancements in bioprinting could one day eliminate the need for donated organs and reduce the risk of rejection.
Medical Devices:
Beyond prototyping, 3D printing is being used to produce components for end-use medical devices, such as inhalers, injectors, and surgical tool trays. The technology also helps produce bespoke tools and molds for traditional manufacturing processes, further enhancing efficiency.

Conclusion
3D printing is reshaping the medical device industry by offering unprecedented levels of customization, speed, and risk mitigation. Despite challenges in cleaning, sterilization, and costs, the potential to create complex, patient-specific products is revolutionizing the field. As the technology continues to evolve and overcome existing limitations, 3D printing in medical devices will become increasingly indispensable, offering new hope and solutions for healthcare providers and patients alike.
More Resources:
Titanium – Source: Wikipedia
Titanium 3d Printing– Source: JHMIM